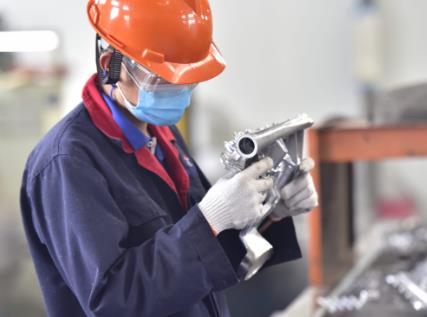
Introduction: The Significance of Aluminum in Manufacturing
Aluminum, a key player in modern manufacturing, is prized for its lightweight yet robust nature. Two primary methods of aluminum manipulation – casting and forging – offer distinct benefits, tailored for specific industry needs.
Cast Aluminum: Process and Advantages
The Casting Technique
Casting involves pouring molten aluminum into molds to achieve complex shapes and designs, solidifying as it cools.
Key Benefits of Cast Aluminum
- Design Versatility: Allows for intricate and detailed designs.
- Economical for Large Productions: Ideal for creating complex parts at scale.
- Balanced Durability and Lightness: Offers a good mix of strength and lightweight properties.
Applications of Cast Aluminum
- Automotive components
- Aerospace parts
- Artistic and decorative items
Forged Aluminum: Strength and Application
The Forging Process
Forging aluminum involves compressing the metal under high pressure, enhancing its density and strength, suitable for demanding applications.
Advantages of Forged Aluminum
- Enhanced Strength: Exhibits superior durability and wear resistance.
- Optimized for High-Stress Use: Ideal for parts requiring high strength-to-weight ratios.
- Tailored Customization: Suited for specific needs, though less versatile in design than casting.
Use-Cases for Forged Aluminum
- Performance-driven automotive parts
- Aircraft and aerospace components
- Heavy-duty industrial machinery
Comparative Insights: Cast vs. Forged Aluminum
Strength and Longevity
- Forged aluminum typically offers greater strength and endurance, ideal for high-pressure environments.
- Cast aluminum, while robust, may have vulnerabilities like porosity that impact its strength.
Design Flexibility and Complexity
- Casting excels in producing detailed and complex geometries.
- Forging, though less flexible in design, ensures uniformity in simpler shapes.
Cost Implications and Production Efficiency
- Casting is more cost-effective for intricate designs and large batches.
- Forging, though potentially pricier, provides unparalleled strength for specialized applications.
Conclusion: Making the Informed Choice
The decision between cast and forged aluminum hinges on project-specific requirements. Recognizing the strengths and limitations of each method is essential for achieving the best balance of performance and cost-effectiveness.