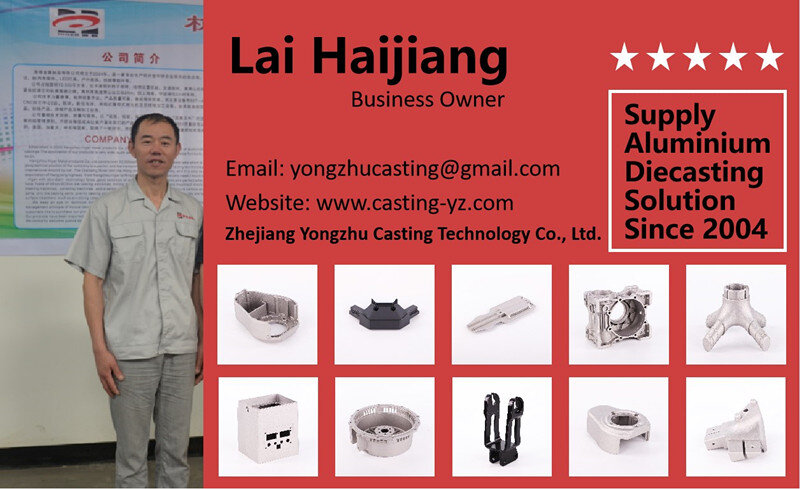
Die casting is a highly efficient and versatile manufacturing process that allows for the production of complex metal parts with high precision and smooth finishes.
At the core of achieving high-quality die casting results are the gate and overflow systems, which play critical roles in material flow and quality control. This article delves into the intricacies of these systems, providing essential insights for optimizing your die casting projects.
Understanding Die Casting Gates
Types of Gates in Die Casting
Gates in die casting serve as the entry points for molten metal to flow into the mold cavity. The design and placement of gates significantly influence the quality and integrity of the casted part.
- Direct Gates: The simplest form, allowing molten metal direct entry into the cavity, suitable for simple, thick parts.
- Fan Gates: Spread the material over a wider area to reduce turbulence and promote uniform filling.
- Tab Gates: Minimize the impact on the part by connecting the gate to a tab that can be easily removed.
- Sprue Gates: Ideal for cylindrical or round parts, providing a direct flow path that minimizes turbulence.
Optimizing Gate Design
The key to optimizing gate design lies in ensuring a smooth, turbulence-free flow of molten metal, which reduces porosity and enhances the mechanical properties of the cast part. Factors to consider include gate location, size, and shape, which should be tailored to the specific part geometry and material.
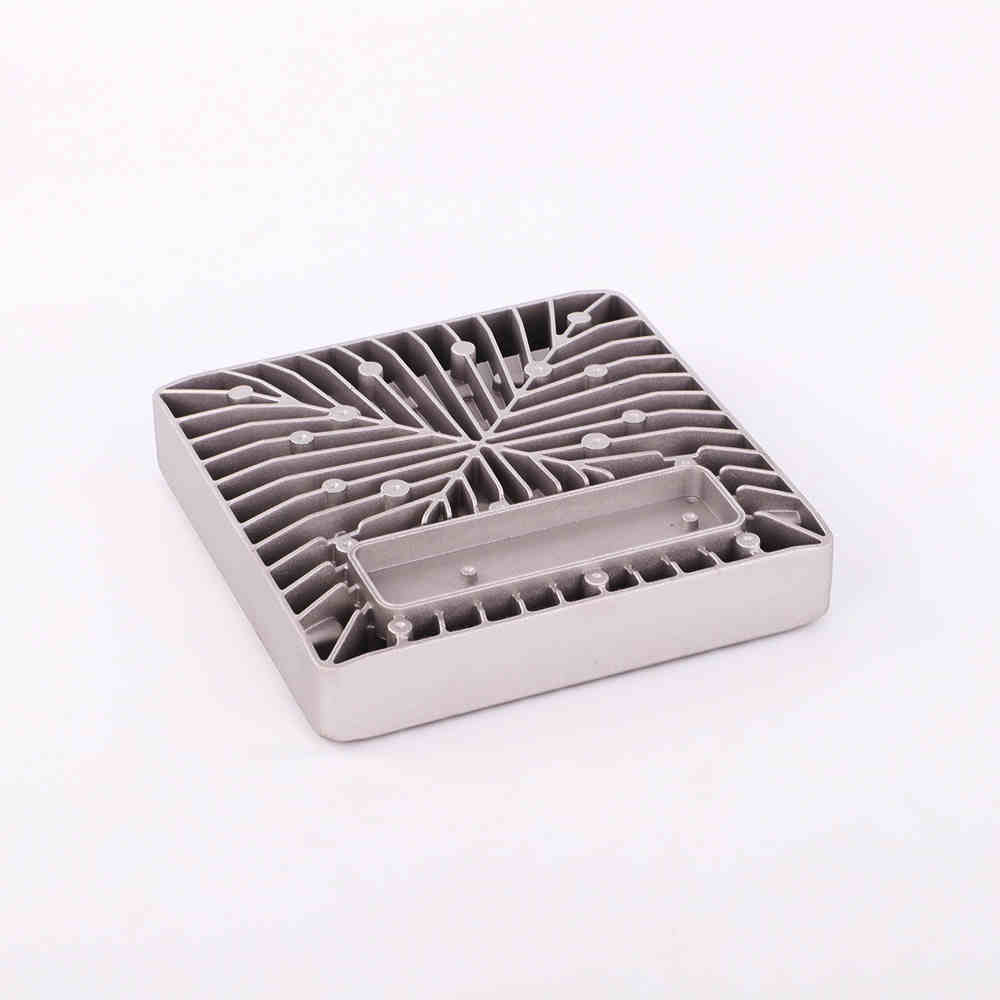
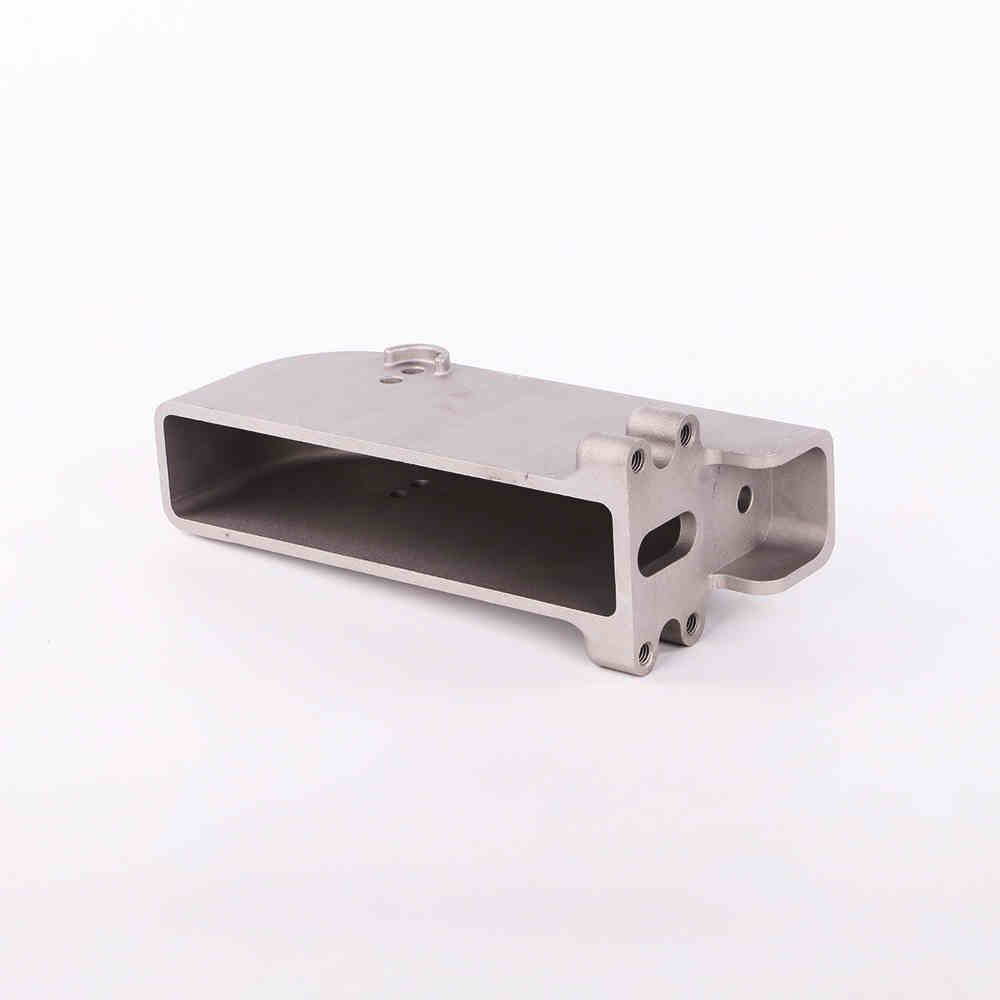
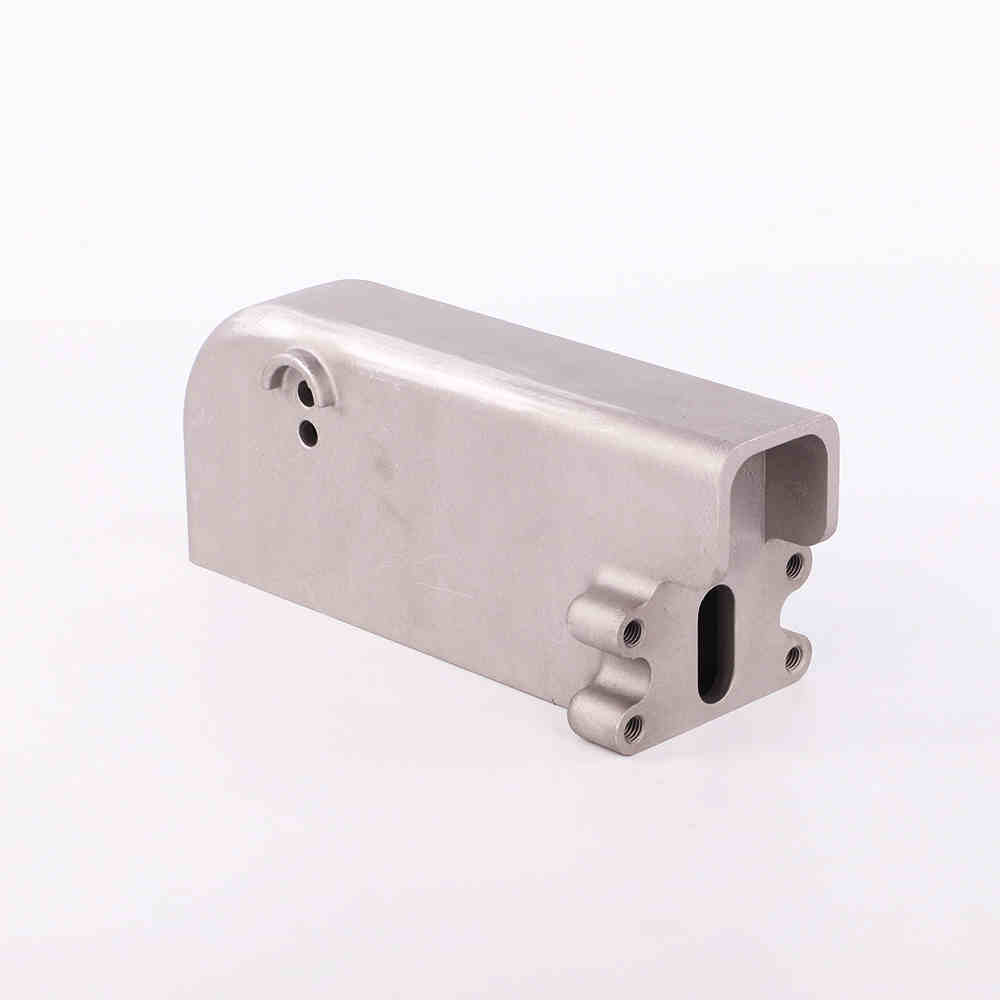
Navigating Overflow Systems in Die Casting
Purpose of Overflow Systems
Overflow systems are crucial for capturing excess molten metal and facilitating the escape of gases and trapped air from the mold cavity. This not only prevents defects but also contributes to a higher quality surface finish.
Strategic Placement of Overflows
Overflows should be placed at the highest points and near the end of the fill where air and gases are likely to be trapped. Their design should ensure that they fill after the main cavity, acting as a secondary route for excess material.
Integrating Gate and Overflow Systems for Optimal Results
The synergy between gate and overflow systems is vital for achieving optimal die casting results. A well-designed gate system ensures uniform fill and minimal turbulence, while strategically placed overflows prevent defects and enhance surface quality.
Best Practices for Gate and Overflow Design
- Simulate Flow Patterns: Use simulation software to predict flow patterns and identify potential issues before production.
- Test and Iterate: Prototype with different gate and overflow designs to find the optimal configuration for your specific part.
- Material Consideration: Adjust gate and overflow designs based on the material properties, as different metals behave differently under pressure and temperature.
Advanced Techniques in Gate and Overflow Optimization
Leveraging advanced techniques such as 3D printing for mold design can greatly enhance the flexibility and precision of gate and overflow systems. Additionally, real-time monitoring of the casting process allows for adjustments on-the-fly, ensuring consistent quality across production runs.
Conclusion
Mastering the design and integration of gate and overflow systems is crucial for maximizing the quality and efficiency of die casting operations.
By understanding and applying the principles outlined in this guide, manufacturers can significantly improve their die casting outcomes, leading to stronger, more reliable, and higher-quality metal parts.
Embracing innovation and continuous improvement in these areas will position companies at the forefront of the die casting industry, ensuring competitive advantage and customer satisfaction.
Drop me an email with your ideas, and I’ll get back to you swiftly!