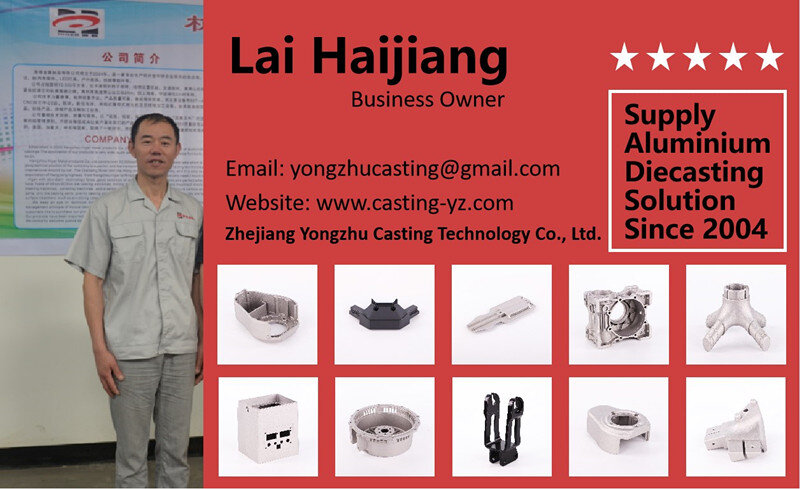
In the realm of manufacturing and design, precision is paramount. Two critical techniques that significantly impact the aesthetics, functionality, and manufacturability of parts are chamfering and filleting.
This comprehensive guide delves into the nuances of chamfer vs fillet, offering detailed insights to empower designers and engineers in making informed decisions for their projects.
What is a Chamfer?
A chamfer is a transitional edge between two faces of an object. It is typically a symmetrical sloping surface at a 45-degree angle, used to remove sharp edges, facilitate assembly, or for aesthetic purposes. Chamfers are prevalent in both mechanical and architectural design, serving as a pragmatic solution for stress concentration reduction and improving parts’ longevity.
Understanding Fillets
Contrastingly, a fillet is a rounding of an interior or exterior corner of a part design. Fillets are used to smooth out sharp corners and edges to increase the strength of a component by reducing stress concentration. In the context of aerodynamics, fillets help in reducing drag, making them essential in automotive and aerospace design.
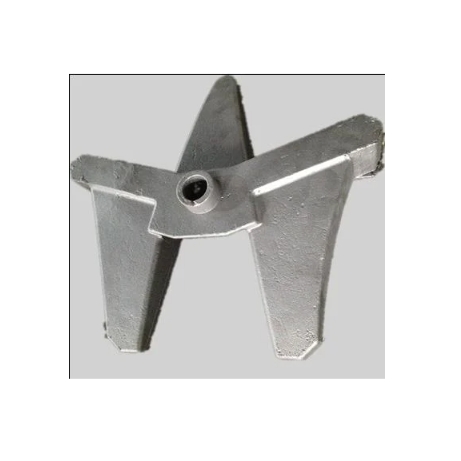
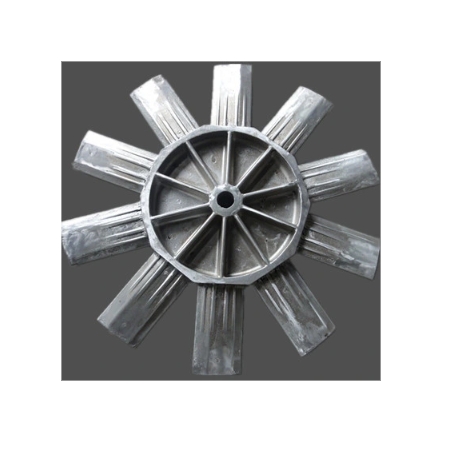
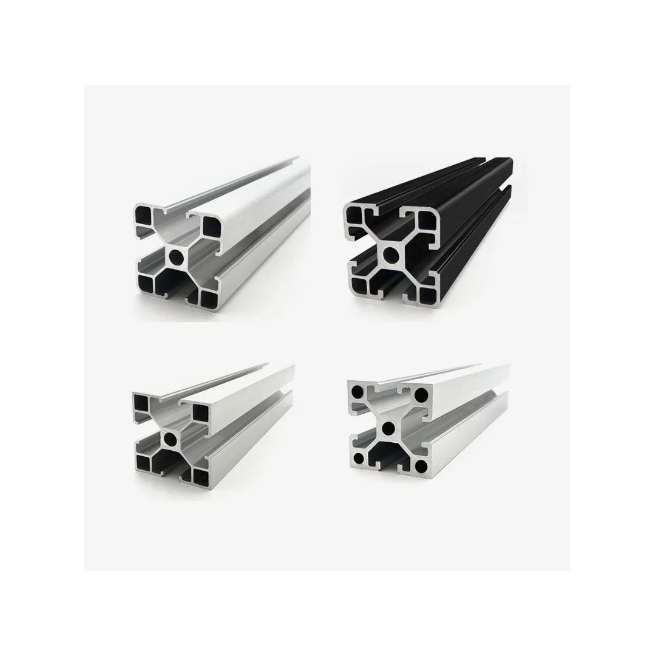
Chamfer vs Fillet: Key Differences and Applications
The choice between chamfer and fillet often depends on the specific requirements of a project, including aesthetic preferences, manufacturing techniques, and functionality needs.
- Aesthetic Appeal: Chamfers often provide a sleek, angular appearance, while fillets offer a smooth, rounded look. The choice between the two can significantly influence the final product’s visual appeal.
- Manufacturing Considerations: Chamfers are generally easier and less costly to produce than fillets, especially in metal machining processes. Fillets may require more sophisticated tooling, particularly for large radii.
- Stress Distribution: Fillets are superior in reducing stress concentration in high-stress areas, making them ideal for components subjected to fatigue or high loads.
- Assembly Ease: Chamfers aid in the assembly process, especially for parts that need to be fitted together, by guiding the components into place.
When to Use Chamfer
- Assembly and Installation: Chamfers are the go-to choice for facilitating easier assembly and installation, particularly for parts that require precise alignment.
- Cost-Sensitive Projects: Due to their simpler manufacturing process, chamfers are preferred for projects where cost reduction is a priority.
- Edge Clearance: In cases where it is necessary to ensure clearance between edges for operational or safety reasons, chamfers provide an effective solution.
When to Use Fillet
- High-Stress Applications: For components that will undergo significant stress or fatigue, fillets are indispensable for their ability to distribute stress more evenly.
- Aerodynamic Efficiency: In the aerospace and automotive industries, the smooth transition provided by fillets can significantly reduce drag, enhancing performance.
- Aesthetic Smoothness: For designs where a smooth, flowing appearance is desired, fillets offer an aesthetic advantage over chamfers.
Conclusion
The decision between using a chamfer or fillet in design projects is nuanced, influenced by factors such as aesthetic preferences, manufacturing capabilities, and functional requirements.
Drop me an email with your ideas, and I’ll get back to you swiftly!