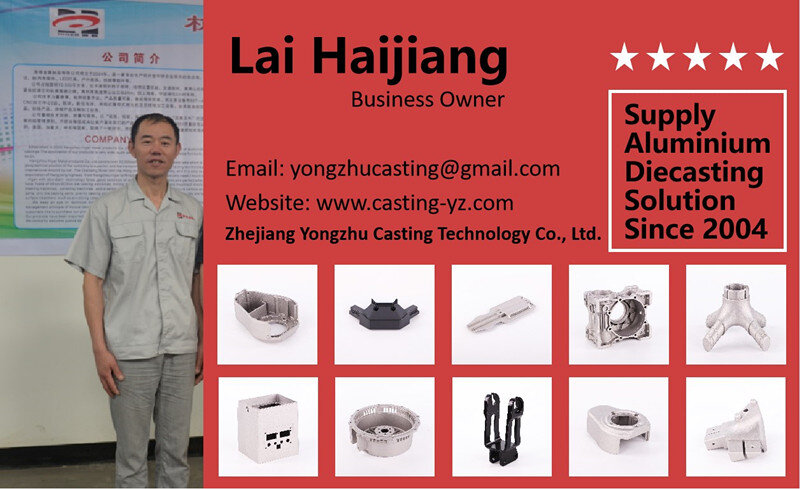
Introduction
In metal fabrication processes such as welding and cutting, drag marks can occur, leading to aesthetic defects and compromised structural integrity. Understanding the causes, prevention methods, and remediation techniques for drag marks is essential for maintaining high-quality metal components.
This comprehensive guide explores the phenomenon of drag marks in metal fabrication, offering insights into their origins and effective mitigation strategies.
Causes of Drag Marks
Drag marks, also known as trailing marks or weld drag, can result from various factors, including:
- Improper Torch Angle: Holding the welding torch at an incorrect angle can cause the molten metal to drag along the surface, leaving behind undesirable marks.
- Excessive Travel Speed: Moving the welding torch too quickly across the workpiece can lead to insufficient fusion and pronounced drag marks.
- Inadequate Shielding Gas Coverage: Insufficient shielding gas coverage can expose the molten weld pool to atmospheric contamination, resulting in irregularities and drag marks.
- Dirty or Contaminated Workpiece: Surface contaminants such as oil, grease, or rust can interfere with the welding process, causing irregular bead formation and drag marks.
- Incorrect Torch Settings: Improper adjustments of welding parameters such as voltage, current, and wire feed speed can exacerbate drag mark formation.
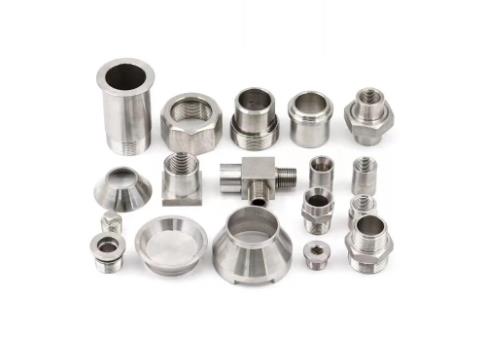
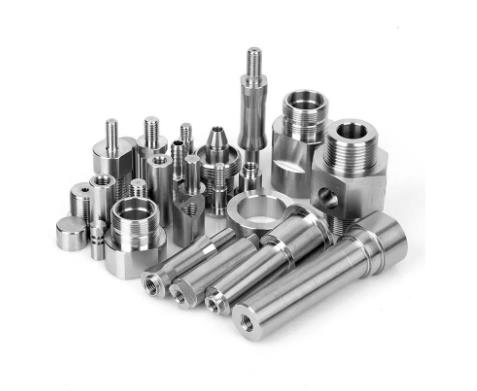
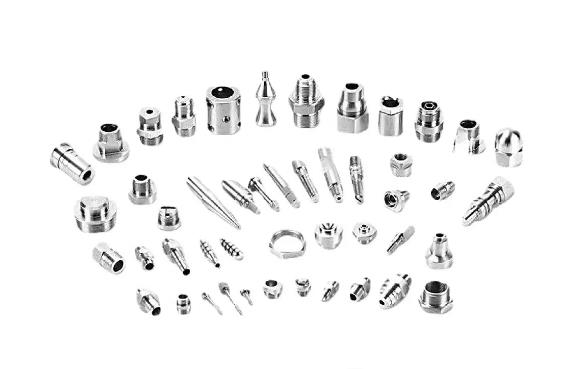
Prevention Methods
To prevent drag marks and ensure high-quality welds, consider the following preventive measures:
- Proper Torch Angle: Maintain a consistent torch angle relative to the workpiece surface, typically between 5 to 15 degrees, to minimize drag and achieve smooth weld beads.
- Optimized Travel Speed: Adjust the welding travel speed to achieve adequate fusion and penetration without excessive dragging or undercutting.
- Optimal Shielding Gas Flow: Ensure sufficient shielding gas flow rate and distribution to provide adequate protection for the weld pool and prevent atmospheric contamination.
- Surface Preparation: Thoroughly clean and degrease the workpiece surface before welding to remove any contaminants that could contribute to drag marks.
- Regular Equipment Maintenance: Periodically inspect and maintain welding equipment, including torches, regulators, and gas hoses, to ensure optimal performance and minimize defects.
Remediation Techniques
In cases where drag marks have already occurred, the following techniques can help remediate the defects:
- Grinding and Polishing: Use grinding and polishing tools to remove surface irregularities and blend the affected areas seamlessly with the surrounding metal.
- Re-welding: If the drag marks are extensive or affect the structural integrity of the weld, consider re-welding the affected areas using proper techniques and parameters to achieve satisfactory results.
- Filler Metal Addition: Apply additional filler metal to fill in any gaps or voids caused by drag marks, ensuring adequate fusion and strength of the weld joint.
Conclusion
Drag marks in metal fabrication processes can detract from the quality and appearance of welded components. By understanding the causes of drag marks and implementing preventive measures, manufacturers can minimize defects and achieve superior weld quality.
In cases where drag marks occur, timely remediation techniques can restore the integrity and aesthetics of the fabricated metal parts.
Drop me an email with your ideas, and I’ll get back to you swiftly!