Introduction
In the realm of aluminum die casting, achieving optimal wall thickness is crucial for ensuring structural integrity, performance, and cost-efficiency of the final parts.
At Yongzhu, we excel in optimizing wall thickness in aluminum die casting parts. In this guide, we delve into the intricacies of wall thickness optimization, offering insights and strategies to help you achieve superior results in your die casting projects.
Wall Thickness: The Key Consideration
Wall thickness refers to the distance between the inner and outer surfaces of a die-cast part. It plays a critical role in determining the mechanical properties, dimensional stability, and overall quality of the component.
Insufficient wall thickness can result in porosity, shrinkage defects, and reduced strength, while excessive thickness may lead to increased material usage, longer cycle times, and unnecessary weight.


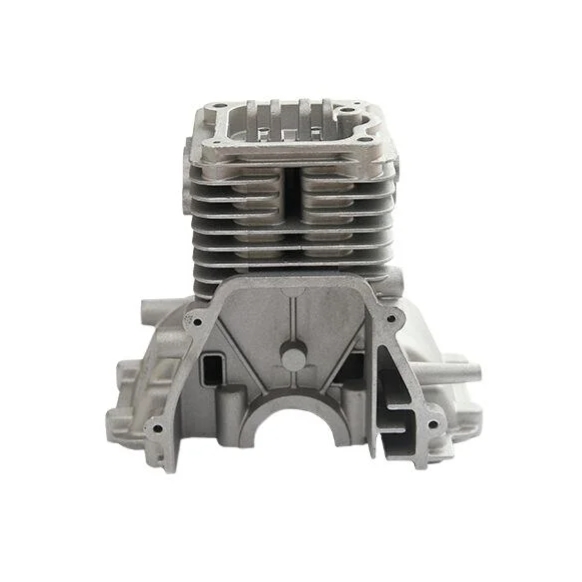
Factors Influencing Wall Thickness
Several factors influence the determination of optimal wall thickness in aluminum die casting parts:
- Part Design: The complexity and geometry of the part significantly impact the required wall thickness.
- Material Properties: The choice of aluminum alloy and its mechanical properties influence the minimum viable wall thickness.
- Die Casting Process Parameters: Variables such as injection pressure, temperature, and cooling rate affect the flow behavior and solidification of the molten metal, thereby influencing wall thickness uniformity.
- Functional Requirements: The intended application and performance specifications of the part dictate the necessary wall thickness to meet functional demands.
Strategies for Maximizing Wall Thickness
Topic | Description 1 | Description 2 | Description 3 |
---|---|---|---|
Design Optimization | Employing fillets and ribs strategically can enhance structural integrity while minimizing material usage. | Utilize simulation software to analyze flow behavior and identify areas of potential thinning or thickening. | Implementing draft angles and uniform wall thicknesses facilitates mold filling and ejection, reducing the risk of defects. |
Material Selection | Choose aluminum alloys with superior fluidity and solidification characteristics to achieve uniform wall thickness. | Consider the alloy’s thermal conductivity and shrinkage behavior to mitigate the risk of warpage and distortion. | |
Process Control | Fine-tune process parameters such as melt temperature, injection speed, and die temperature to ensure consistent wall thickness throughout the part. | Implement advanced monitoring and control systems to detect deviations and optimize process stability. |
Benefits of Optimized Wall Thickness
- Enhanced Structural Integrity: By maximizing wall thickness, die-cast parts exhibit improved strength, rigidity, and durability.
- Cost Savings: Efficient material utilization and reduced cycle times lead to cost savings in production.
- Consistent Quality: Uniform wall thickness minimizes the occurrence of defects and ensures dimensional accuracy and repeatability.
- Design Flexibility: Optimized wall thickness allows for greater design freedom and facilitates the integration of features and functionalities.
Conclusion
Achieving optimal wall thickness in aluminum die casting is essential for producing high-quality parts that meet performance requirements and cost targets.
By leveraging advanced design techniques, materials expertise, and process control strategies, Yongzhu empowers you to maximize wall thickness in aluminum die casting parts. Partner with us to unlock the full potential of your die casting projects.
Drop me an email with your ideas, and I’ll get back to you swiftly!