Introduction
In the realm of manufacturing, the high-pressure die casting process stands as a cornerstone for producing intricate components with precision and efficiency.
At Yongzhu, we specialize in optimizing process parameters for high-pressure die casting, ensuring superior results and maximum productivity.
In this comprehensive guide, we explore the profound impact of process parameters on die casting outcomes, offering invaluable insights and expert strategies to enhance your manufacturing processes.
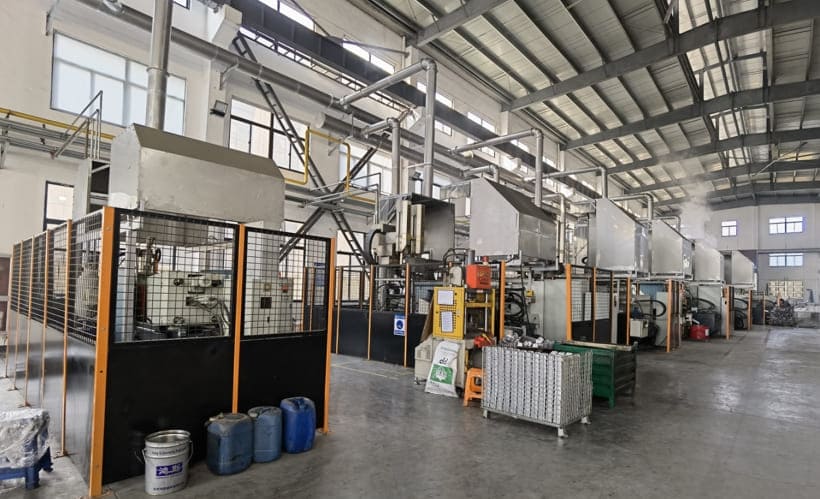
Understanding High-Pressure Die Casting
High-pressure die casting is a versatile manufacturing technique that involves injecting molten metal into a steel mold cavity under high pressure.
This process enables the production of intricate and high-precision components with minimal post-processing requirements. It finds widespread applications across various industries, including automotive, aerospace, and consumer electronics.
The Influence of Process Parameters
The success of high-pressure die casting hinges on the careful control and optimization of various process parameters, including:
Injection Pressure | Determines the force applied to the molten metal during injection, impacting mold filling and part quality. |
Injection Speed | Regulates the rate at which molten metal is injected into the die cavity, affecting filling time and material distribution. |
Metal Temperature | Controls the temperature of the molten metal prior to injection, influencing flow behavior, solidification, and part properties. |
Die Temperature | Maintains the temperature of the die cavity, affecting metal solidification, cycle times, and part quality. |
Cooling Rate | Determines the rate at which the cast part cools and solidifies, impacting dimensional stability and mechanical properties. |

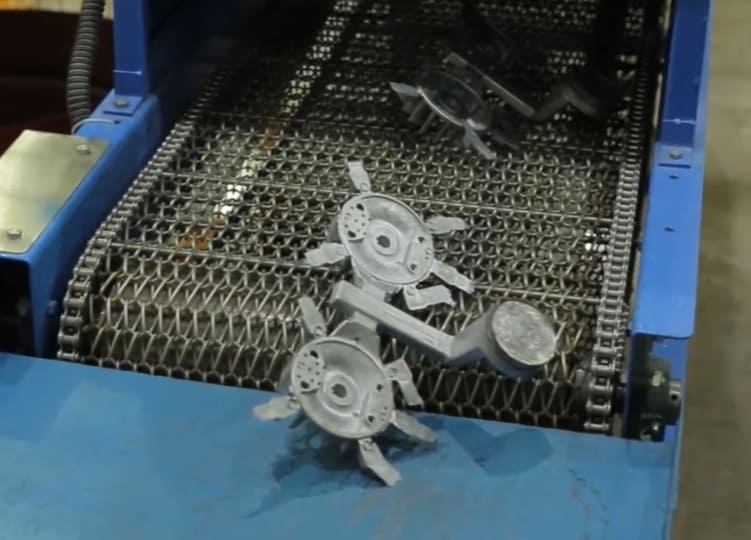

Strategies for Optimizing Process Parameters
1. Robust Design of Experiments (DOE)
- Utilize DOE methodologies to systematically analyze the effects of process parameters on die casting outcomes.
- Conduct factorial experiments to identify optimal parameter settings and their interactions, minimizing defects and enhancing part quality.
2. Advanced Simulation and Modeling
- Leverage computational fluid dynamics (CFD) simulations to visualize and analyze the flow behavior of molten metal during injection.
- Use finite element analysis (FEA) to predict temperature distribution, stress levels, and distortion in the cast part, optimizing die and process design.
3. Real-Time Monitoring and Control
- Implement sensors and monitoring systems to collect data on key process parameters in real time.
- Utilize feedback control mechanisms to adjust process settings dynamically, maintaining consistency and quality throughout production runs.
Benefits of Optimized Process Parameters
Benefit | Description |
---|---|
Improved Quality | Optimizing process parameters leads to reduced porosity, shrinkage defects, and dimensional variations, resulting in superior part quality. |
Enhanced Productivity | Fine-tuning parameters such as injection speed and cooling rate minimizes cycle times, increasing throughput and efficiency. |
Cost Savings | By minimizing scrap and rework, optimized process parameters reduce material waste and production costs. |
Greater Design Freedom | With precise control over process parameters, designers can explore complex geometries and innovative designs with confidence. |
Conclusion
Optimizing process parameters is crucial for achieving superior results in high-pressure die casting.
By understanding the profound influence of parameters such as injection pressure, speed, and temperature, Yongzhu empowers you to enhance your manufacturing processes and unlock new levels of efficiency and quality.
Partner with us to harness the full potential of high-pressure die casting for your component manufacturing needs. Drop me an email with your ideas, and I’ll get back to you swiftly!