Shot lube stains are surface discolorations found on die-casting parts due to mold release solutions or lubricating oils. These stains often appear dark or grey, whether or not they’re easily visible. Plunger lubricants and die oils are heavily used during the withdrawal process.
It’s important to distinguish shot lube stains from blackening issues in casting alloys. While shot lube stains are a subset of blackening, they should not be treated as identical. Lubricants play a significant role in causing this particular defect.
This article briefly explores the sources, effects, and preventive measures for shot lube stains in castings during production.
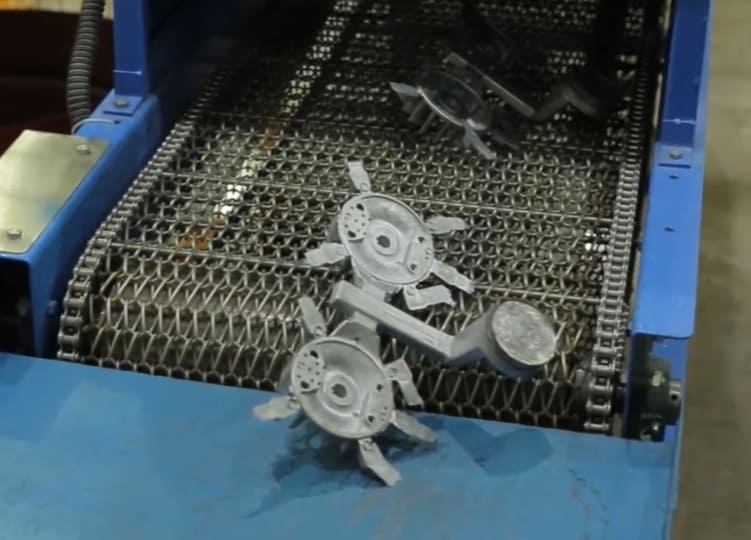
Causes of Shot Lube Stains in Casting:
- Excessive Amount: Applying too much lubricant, whether intentionally or accidentally, is rare in modern casting production. However, damaged mold sections may necessitate additional oils to fill gaps, leading to stains.
- Extreme Concentration: Some oils are highly concentrated, often requiring dilution with water or other oils. Direct application of these concentrated lubricants can easily cause stains on surfaces.
- Faulty Processing: Compromised or incorrect setup adjustments can result in the injection of too much or too little lubricant into the molded alloys/metals. While small amounts may not cause stains, excessive amounts can lead to the defect.
- Improper Lubricant: Different alloys require specific lubricating oils for casting, and changes in compositions may necessitate adjustments in the amount applied. Any deviation from the optimal parameters can result in surface staining.
- Defective Lubricant: Lubricants may contain impurities, alterations, or defects, which can compromise their effectiveness. Using such oils may fail to provide adequate lubrication and instead result in defects such as black spots in die casting.
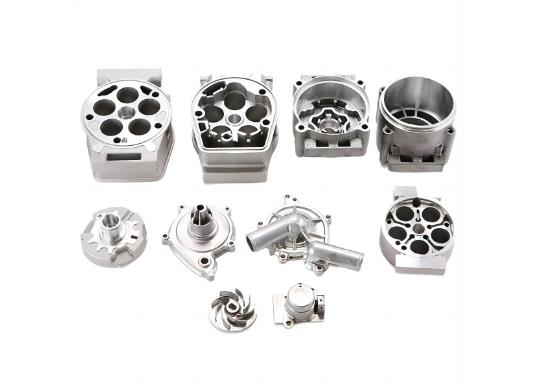
Die-casting stains primarily impact the overall appearance. Even if the defect seems minor or requires close inspection, favorable conditions can exacerbate the issue.
Over time, parts intended for architectural purposes can become devalued and lose their functionality.
Preventing Lube Stains in Die Casting:
- Proper Lubricant Application: Apply the chosen lubricant appropriately to avoid stained castings. Address any irregularities or damages in the mold/die to prevent excessive demand.
- Selecting the Right Lubricant: Choose the most suitable lubricant to ensure proper shaping of the molten metal/alloy. Any alterations or differences in liquid composition require a review of lubrication type, amount, and concentration.
- Optimal Die Casting Setup: Ensure a perfect setup to minimize staining issues. Pay attention to the design, parameters, and effectiveness of machinery to accurately inject lubricants.
- Contamination Prevention: Avoid any impurities or contaminants in the liquid stream to maintain lubricant efficiency. Contamination should be prevented in the casting process, regardless of the alloys/metals used.
- Validity and Purity of Lubricant: Avoid using old or uncertain lubricants for high-quality die casts. Even permissible ones that are considerably older may cause issues due to modern machining practices.
Die-casting lubricants play a crucial role in the manufacturing process. Improper, erroneous, or unacceptable usage can result in both visible and invisible stains, with the possibility of future expansion.Drop me an email with your ideas, and I’ll get back to you swiftly!