Break Out is a critical failure primarily associated with the continuous casting of alloys, especially steel. It occurs when the slab shell fails to solidify adequately, leading to ruptures, leaks, or breaks that allow molten metal to escape.
Continuous casting is a specialized die-cast process that aims to achieve uniform metal grain structures.
In this process, molten metal or alloy is poured into a mold, rapidly cooled before solidification, allowing the alloy or metal to take its final shape without interruptions.
Breakouts in continuous casting machines pose significant risks for manufacturers.
This concise yet informative article examines the sources, types, effects, and preventive strategies for managing breakouts.
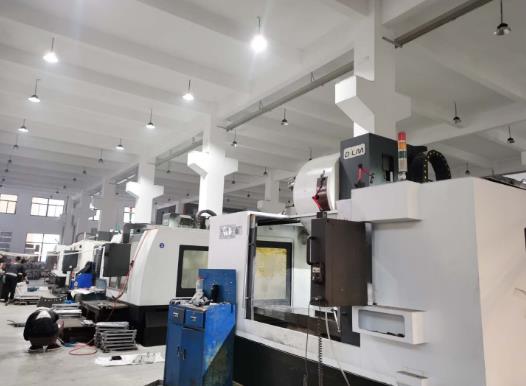
Causes of Breakout in Die Casting
There isn’t a single root cause for breakouts; rather, various mechanical factors contribute to the issue, such as:
Issue | Cause | Key Concern |
---|---|---|
Inadequate Pouring Control | Ineffective initial pouring of molten metal/alloy | Open pouring breakouts |
Insufficient Shell Wall Thickness | Thin walls can’t support liquid column | Disrupts heat transfer and leads to leakage |
Cast Shell Damage | Physical imperfections or excessive pouring turbulence | Interferes with casting solidification |
Contaminants | Presence of foreign materials like slags | Weakens shell wall, causing leakage or bleeding |
Corner Defects | Seams, scratches, or recessed pads in corners | Hinders smooth cast removal, leading to suspension breakouts |
Major Exterior Faults | Corner cracks, surface detachment, longitudinal cracks | Cause breakouts at the mold exits |
Shell-Mold Adhesion | Shell adheres to mold surface | Ruptures machine’s meniscus, allowing escape of molten metal |
Speed Issues | Fast operations and slow cooling rates | Leads to breakouts at break-off points |
Types of Breakout in Die Casting
As previously mentioned, different causes lead to various types of breakouts in die-cast parts. The most notable types include:
Type | Cause | Key Feature |
---|---|---|
Open Pouring Breakout | Errors in equipment, process, or handling | Temperature imbalance causes insufficient solidification |
Pouring Breakout | Mold can’t withstand static pressure of molten metal | Results in possible rupture |
Bonded Breakout | Fluctuations in molding levels and lubrication loss | Most common breakout with V-shaped rupture at exits |
Suspension Breakout | Blocked withdrawal of die-cast part from the mold | Corner seam measuring >0.35mm without replacement |
Slag Entrapment Breakout | Errors in handling, preparation, pouring, and solidification | Traps slag within molten alloys, causing blank-type breakouts |
Consequences of Breakout
Visible die-casting breakouts present significant threats to operation and safety. Key effects include:Here is the information presented in a table format, summarizing the key points:
Aspect | Key Points |
---|---|
Hot Molten Metals Risk | Serious safety risks exist due to the presence of hot molten metals in the process. |
Defects Impact Costs | Addressing defects raises production and operational costs, as they are challenging to repair. |
Avoiding Breakouts in Die Casting
Breakouts can disrupt the entire casting system, so taking comprehensive preventative measures is essential.
The following precautions can help maximize processing accuracy and eliminate the defect.
- Consistent Metal Quality: Ensuring optimal metal/alloy quality at all stages is crucial. Even small variations may require excessive corrections in processes.
- Consistent Temperatures: Uniform temperatures in the pouring platform and during pouring are important. However, the molten metal/alloy stream should remain slightly overheated.
- Controlled Pulling Speed: Adjusting temperatures and pulling speeds can stabilize the process and prevent breakouts.
- Manage Slag Pool Thickness: Keeping the slag pool below 10mm can help prevent breakouts. The blank shell requires consistent lubrication without solid attachments.
- Monitor Water Flow: Checking water pressure before pouring can detect potential blockages for smooth flow. Verify the water quality for casting.
- Repair Corner Seams: Filling corner seams at plate joints with lime or plaster reduces the likelihood of breakouts. The permissible fillet radius should be no more than 0.2mm.
- Adjust Machinery: Carefully adjusting the necessary parameters provides control over equipment. Calculated and coordinated adjustments are always recommended.
- Select Appropriate Mold Powder: Choose mold powder that aligns with the alloy’s chemical composition. Also, confirm the powder’s validity period.
Complex mechanical adjustments during the die-casting process can lead to breakouts.
Given how challenging they are to address, we should taking preventive measures from the outset is the most practical approach.
Drop me an email with your ideas, and I’ll get back to you swiftly!