Aluminum is widely used in various industries due to its excellent natural surface quality. Specific applications require additional surface finishing to enhance aesthetics, improve surface structure, increase corrosion resistance, and enhance electrical insulation.
Below, we examine six top aluminum finishing techniques, detailing their processes, benefits, and applications.
Anodizing
Anodizing is an electrochemical process that significantly improves the durability and wear resistance of aluminum by forming a thick oxide layer.
Feature | Description |
---|---|
Process | Immersing aluminum in an electrolytic bath where an electric current triggers oxidation. |
Benefits | -Excellent abrasion and corrosion resistance -Improved aesthetics -Functional surfaces -Enhanced electrical properties |

Powder Coating
The process involves coating the metal with thermoplastic or thermoset powders, resulting in a smooth, durable finish.
Aspect | Details |
---|---|
Durability | Powder coating offers superior durability, making aluminum surfaces resistant to wear and tear. |
Abrasion Resistance | The process enhances the metal’s ability to withstand scratches and abrasions. |
Visual Appeal | Available in a variety of finishes and colors, powder coating improves the aesthetics of aluminum products. |
Maintenance | Requires minimal maintenance due to its long-lasting protective layer. |
Process | Involves applying thermoplastic or thermoset powders to aluminum, followed by curing. |
Alodining (Passivation)
Alodining, also known as chem film, is a chemical process that forms a protective layer on aluminum. By reacting chromium salts and acid with aqueous solutions, a durable, adhesive coating is created.
This finish is common in aerospace, military, and electrical industries for its corrosion resistance, although it offers limited abrasion resistance and a less decorative finish.
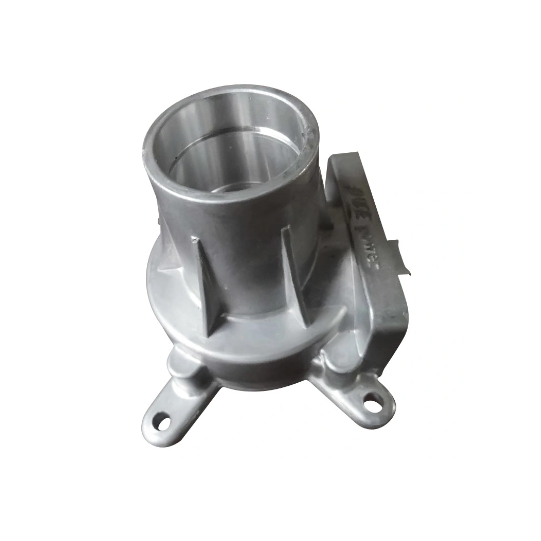
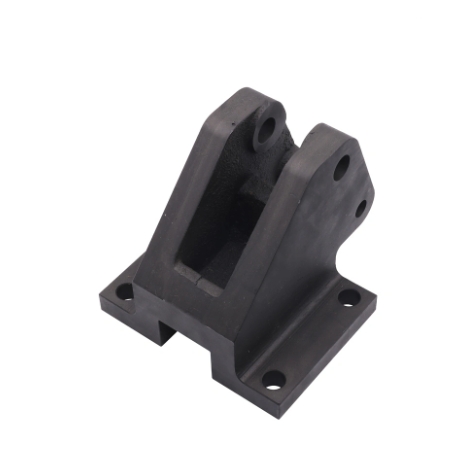
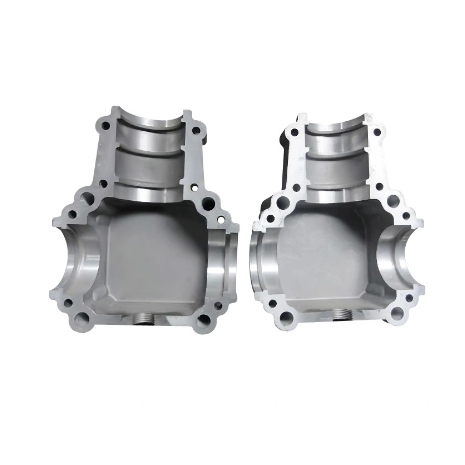
Liquid Paint
Liquid painting provides a versatile and accessible finishing option for aluminum, offering a wide range of compositions and colors, including polyester, silicone, acrylics, and PVDF.
Despite its benefits, such as ease of application and variety, liquid painting can produce more waste and may contain volatile organic compounds (VOCs).
PVDF coatings are particularly advantageous for their lightweight, chemical resistance, and non-reactive properties, making them ideal for the chemical processing industry.
Mechanical Finishing
Mechanical finishing processes like grinding, buffing, blasting, polishing, tumbling, and vibratory finishing can achieve various aluminum finishes. These methods enhance surface appearance, remove imperfections, and prepare the metal for further processing.
Each technique offers unique benefits, such as grinding for flat surfaces, buffing for removing emery marks, blasting for debris removal, and polishing for a reflective finish.

E-Coating
E-Coating, or electrostatic coating, uses charged paint particles to create a uniform, thin coating on aluminum parts. This cost-effective and efficient method involves two main types: Anodic and Cathodic E-Coating.
Conclusion
Selecting the right aluminum finishing method depends on factors such as available machinery, budget, environmental considerations, safety measures, and required skill levels.
Each finishing technique offers distinct advantages, from enhancing aesthetic appeal to improving surface properties and durability.
Contact us today to discuss your project needs and receive a quote, you can trust us to deliver exceptional castings that meet your requirements.