Aluminum Die Casting for EVs
Aluminum die casting is a popular manufacturing process in the automotive industry, especially for electric vehicles (EVs).
This process involves forcing molten aluminum into a mold cavity under high pressure to create complex and precise parts.
Key Considerations for Custom Aluminum Die Casting
Material Selection
Selecting the right aluminum alloy is crucial for achieving the desired properties in die-cast parts.
Factors such as strength, thermal conductivity, corrosion resistance, and machinability must be considered. Commonly used alloys include A360, A380, and ADC12.
Comparison of A360, A380, and ADC12 Alloys
Alloy | Properties | Applications |
---|---|---|
A360 | High corrosion resistance Good mechanical properties Excellent fluidity for filling complex molds | Automotive components Housings for electronic equipment |
A380 | Good balance of casting properties High mechanical strength Good thermal conductivity Dimensional stability Resistance to cracking under thermal stress | Engine blocks Gearbox cases Structural automotive parts |
ADC12 | Similar to A380 Excellent castability High corrosion resistance Good mechanical properties Good thermal conductivity | Automotive parts Electrical equipment Industrial applications with complex geometries and high precision |
Design Complexity
Custom aluminum die casting allows for the production of intricate designs with tight tolerances. This involves considering factors such as wall thickness, draft angles, and rib placement.
Tooling and Mold Design
High-quality tooling and mold design are essential for producing consistent and precise parts. The mold must withstand high pressures and temperatures without deforming.
Proper cooling channels and venting systems are also critical to ensure uniform solidification and reduce defects.
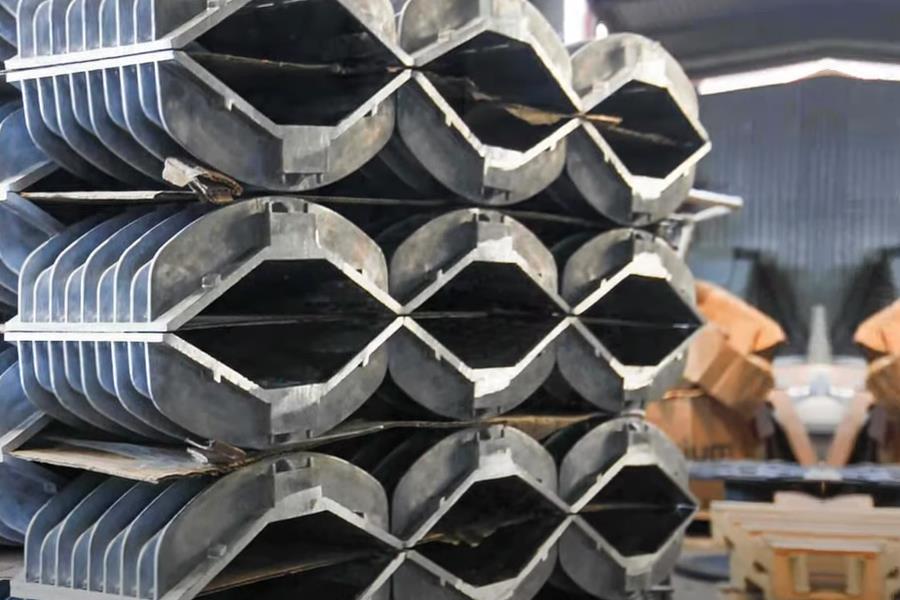
Production Volume
The production volume plays a significant role in determining the cost-effectiveness of custom aluminum die casting.
While the initial investment in tooling can be high, large production runs can significantly reduce the per-unit cost.
Surface Finishing
Surface finishing is an important consideration for die-cast parts, especially for aesthetic and functional purposes.
Various finishing techniques, such as powder coating, anodizing, and painting, can be applied to enhance the appearance and protect the parts from environmental factors.
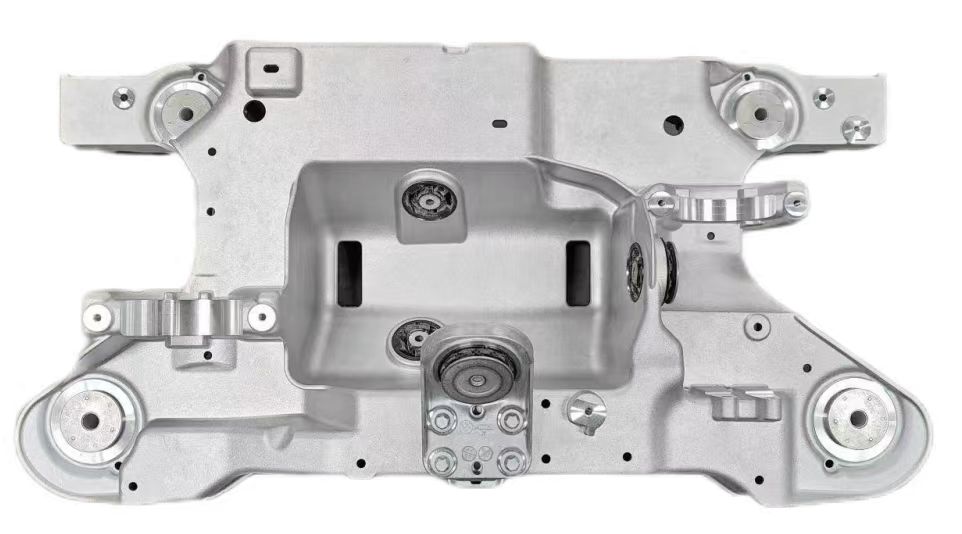
Advantages of Custom Aluminum Die Casting for EVs
Lightweight Properties
Aluminum is known for its lightweight nature, which is crucial for EVs to improve energy efficiency and extend battery life.
Reducing the vehicle’s weight directly contributes to better performance and longer driving ranges.
High Strength and Durability
Despite its lightweight properties, aluminum die-cast parts offer excellent strength and durability. This ensures the structural integrity of critical components in electric vehicles, enhancing safety and reliability.
Thermal Conductivity
Aluminum’s superior thermal conductivity helps dissipate heat generated by electronic components and batteries in EVs.
Efficient heat management is essential for maintaining optimal performance and preventing overheating.
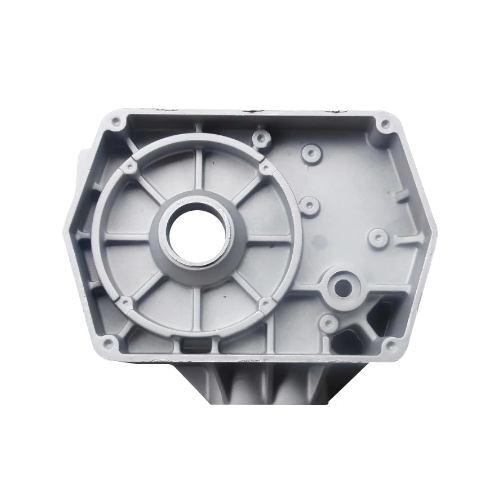


Corrosion Resistance
Aluminum naturally forms a protective oxide layer, making it highly resistant to corrosion.
This property is particularly advantageous for EV components exposed to harsh environmental conditions, such as road salt and moisture.
Cost-Effectiveness
Custom aluminum die casting can be highly cost-effective, especially for large production volumes.
The ability to produce complex parts with minimal machining reduces production costs and time, making it an economical choice for manufacturers.

Applications of Custom Aluminum Die Casting in EVs
Battery Housings
Aluminum die-cast battery housings provide robust protection for battery packs while offering excellent thermal management.
The lightweight nature of aluminum also contributes to reducing the overall weight of the vehicle.
Motor Housings
Motor housings made from aluminum die casting ensure optimal heat dissipation and structural integrity. This enhances the performance and longevity of electric motors in EVs.
Inverter and Controller Enclosures
Inverters and controllers are critical components in EVs, requiring effective thermal management and protection from environmental factors.
Custom aluminum die-cast enclosures meet these requirements, ensuring reliable operation.
Contact us today to discuss your project needs and receive a quote, you can trust us to deliver exceptional castings that meet your requirements.