In the manufacturing industry, particularly when working with metals, the distinction between tapped and threaded holes is critical for engineers and designers.
Understanding these two types of holes ensures that components are securely fastened and optimized for long-term durability.
This article delves into the differences between tapped holes and threaded holes, offering insights into their respective advantages, applications, and the techniques for creating each type.
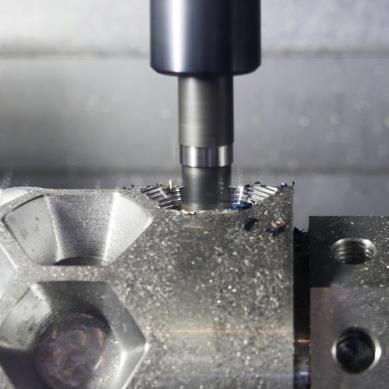
What Are Tapped Holes?
A tapped hole is a pre-drilled hole into which threads are cut using a tapping tool.
These holes are designed to accept a screw or bolt, allowing the fastener to grip securely into the material.
Tapping processes are employed in various industries including automotive, aerospace, and heavy machinery, where high-strength connections are crucial.
Key Benefits of Tapped Holes
- Precision and Consistency: Tapped holes provide uniform threads that ensure consistent engagement with screws or bolts. This is vital for ensuring the strength of the connection, especially in high-load applications.
- Strength: Since the threads are directly cut into the material, tapped holes tend to offer higher strength than using threaded inserts.
- Material Versatility: Tapped holes can be applied to a wide range of materials, including metals, plastics, and composites.
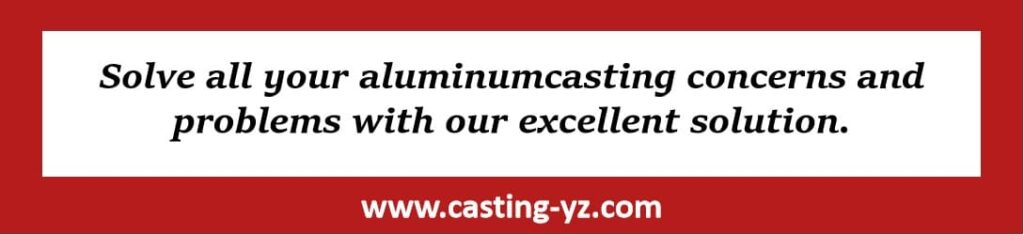
What Are Threaded Holes?
Threaded holes, also referred to as internally threaded holes, are created either by tapping (manually or through machine processes) or by using self-tapping screws, which cut their own threads as they are driven into the material.
The purpose of a threaded hole is to allow the insertion of fasteners like bolts, screws, or studs with matching thread profiles.
Types of Threaded Holes
- Pre-Tapped Holes: These are holes that are drilled and then tapped manually or through an automatic process to create the internal threads.
- Self-Tapped Holes: Created when self-tapping screws cut their own threads as they are driven into the material, eliminating the need for a pre-tapped hole.
- Threaded Inserts: For materials prone to wear or with poor thread strength, threaded inserts can be placed in drilled holes to provide a durable threaded connection.
Searching for High-Quality for Cast Aluminum Parts?
You’ve come to the right place! Yongzhu Casting is a certified die casting manufacturer with over 20 years of expertise in the industry.
We have successfully completed numerous die casting projects for Aluminum casting parts, particularly in your industry.
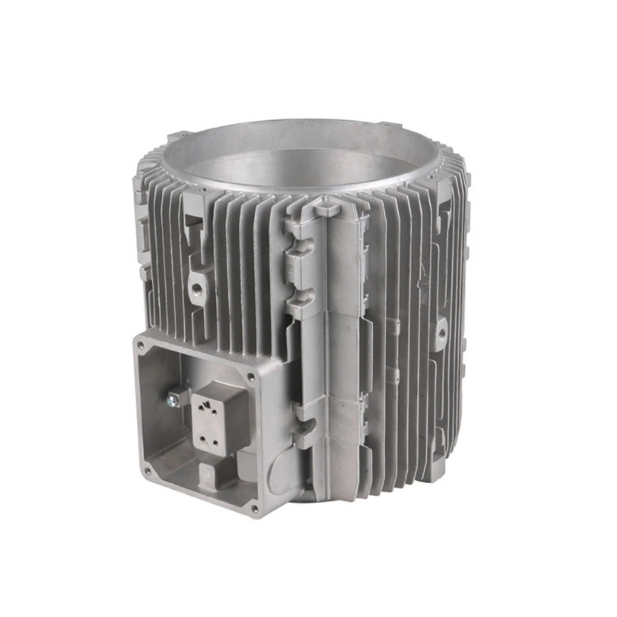
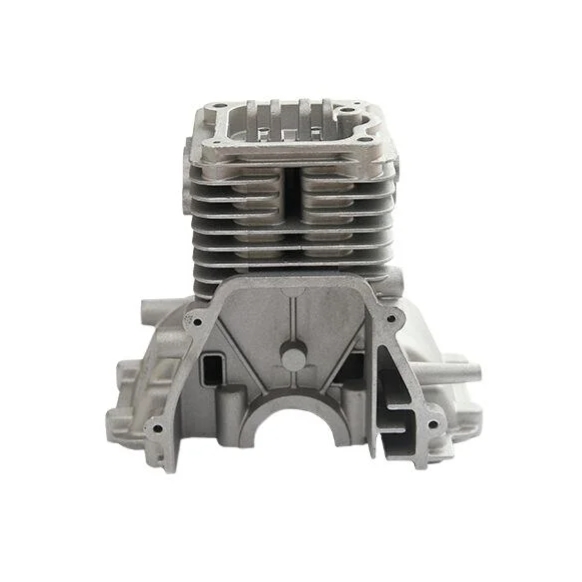
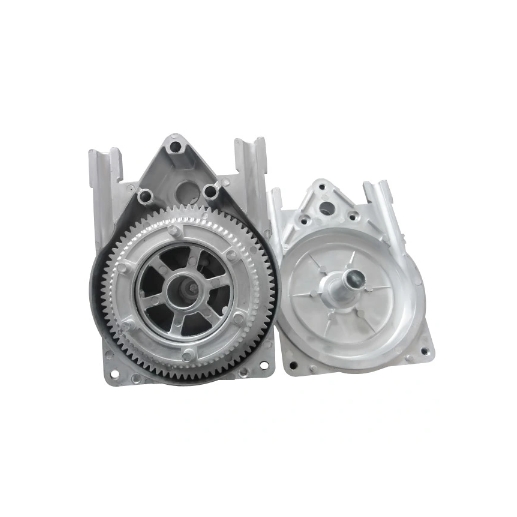
Design Review & DFM Support
Our professionals will evaluate your designs and provide suggestions for cost savings.
Additionally, we offer Design for Manufacturing (DFM) assistance and conduct mold flow analyses to facilitate efficient production.
State-of-the-Art Manufacturing Equipment
Our facility is equipped with advanced hot-chamber and cold-chamber die casting machinery for aluminum and zinc production.
We also utilize high-precision CNC machines in a temperature-controlled workshop, featuring 3-Axis, 4-Axis, 5-Axis, and 7-Axis setups to manage any project you have.
Rigorous Quality Control Measures
Our dedicated quality control team ensures that all parts meet the highest standards of quality and consistency.
We employ high-accuracy measurement instruments, including CMM, spectrometers, and X-ray detectors.
Comprehensive Surface Treatment Options
We provide a variety of surface finishing techniques for your precision die casting components. Our in-house services include cleaning, polishing, anodizing, shot blasting, and painting.
Flexible Project Acceptance
While larger manufacturers often shy away from low-volume projects, and smaller ones may struggle with quality, Yongzhu Casting stands apart.
We prioritize customer satisfaction and willingly accept high-mix, low-volume projects like yours.
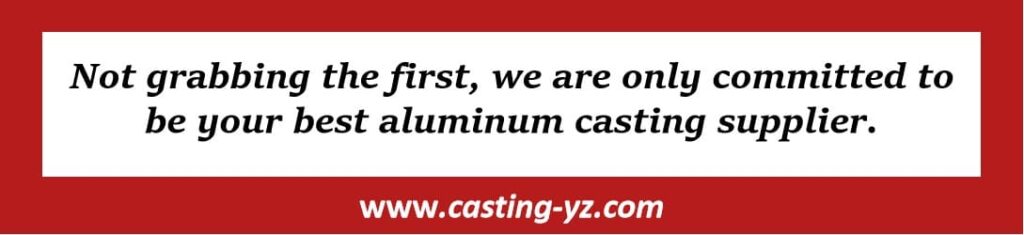
Tapped Holes vs Threaded Holes: Detailed Comparison
1. Strength and Durability
- Tapped Holes: Tapped holes typically provide more strength in materials with good machinability, like metals, because the threads are cut into the material itself. This makes them ideal for applications where high-strength fastening is required.
- Threaded Holes: Threaded holes, especially those created with self-tapping screws, are more commonly used in softer materials, like plastics or woods. While they may not offer the same strength as tapped holes in metal, they are more efficient for lightweight or non-structural applications.
2. Ease of Creation
- Tapped Holes: Creating tapped holes requires precision machinery or manual tapping tools, which makes the process more labor-intensive. For mass production, CNC machines are often employed to tap holes with high precision.
- Threaded Holes: Self-tapping screws simplify the process by creating their own threads during installation, which can save time in assembly.
3. Applications
- Tapped Holes: Used in situations where precise and high-strength connections are required. Common in automotive engine blocks, heavy-duty machine components, and critical aerospace parts.
- Threaded Holes: These are typically found in applications involving softer materials, like plastic enclosures, where the strength of tapped threads would be unnecessary.
4. Cost Efficiency
- Tapped Holes: Due to the precision needed for tapping, this process tends to be more expensive, especially in high-volume production.
- Threaded Holes: The ability to use self-tapping screws or threaded inserts reduces labor costs and time, making threaded holes a more cost-effective solution for lightweight or non-critical components.
5. Installation Speed
- Tapped Holes: Installation can be slower due to the requirement for precision tapping.
- Threaded Holes: Faster assembly since self-tapping screws create threads in a single operation.
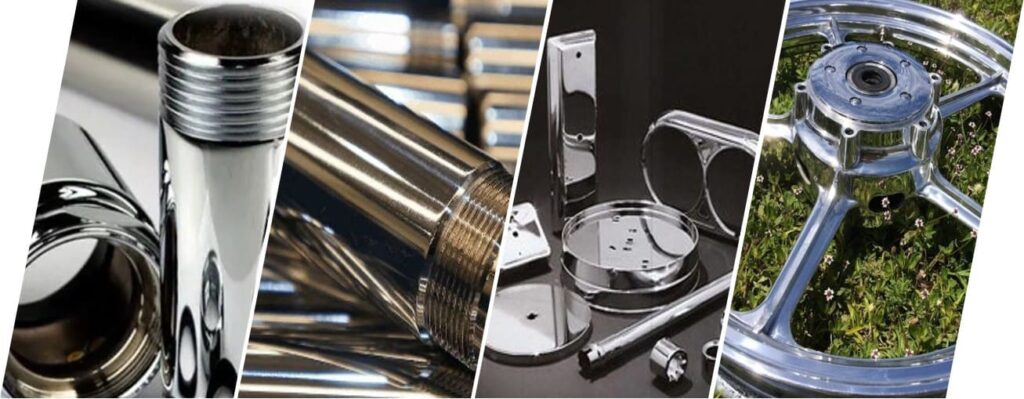
Best Practices for Creating Tapped and Threaded Holes
- Material Selection: Tapping is more effective in metals, while self-tapping screws work best in softer materials like plastics.
- Correct Thread Size: Ensure that the screw or bolt used matches the hole’s thread size to prevent stripping or damaging the material.
- Lubrication: When tapping holes, especially in hard metals, lubrication can reduce wear on the cutting tool and increase the longevity of the threads.
- Depth Control: For both tapped and threaded holes, controlling the depth of the hole is critical to avoid over-tapping or damaging the material.
Advantages of Using Threaded Inserts
Threaded inserts offer a hybrid solution between tapped and threaded holes.
These inserts are placed into drilled holes to provide durable threads, especially in materials that are prone to stripping, such as plastics or thin metals.
Common applications include electronics enclosures, automotive dashboards, and aerospace components.
Benefits of Threaded Inserts
- Enhanced Durability: Provides stronger threads in materials that otherwise might not hold up under high stress.
- Repairability: Damaged threads can easily be replaced by removing the old insert and installing a new one, saving costs on parts replacement.
- Corrosion Resistance: Inserts made from materials like stainless steel or brass resist corrosion better than the host material.
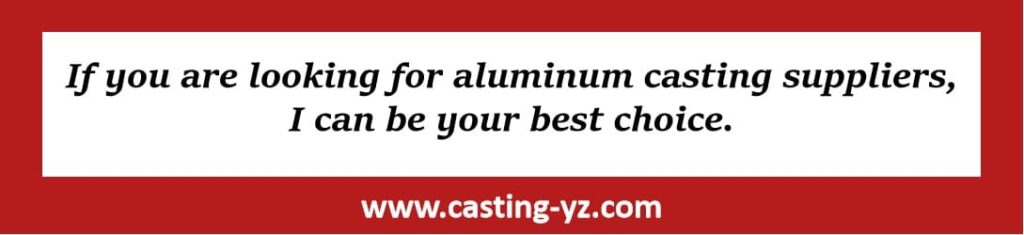
Conclusion
The decision between using tapped holes or threaded holes depends largely on the application and the material being used.
Tapped holes offer superior strength in metals, while threaded holes provide speed and cost-efficiency in non-critical applications, particularly with softer materials.
Knowing the benefits of both types of holes helps manufacturers make the right decision for their products, ensuring the longevity and reliability of their fastened connections.
By choosing the right type of hole and threading technique, you can optimize your assembly process and ensure the long-term reliability of your components.
FAQs
What is the difference between a tapped hole and a threaded hole?
Tapped holes are pre-drilled with threads cut into them, while threaded holes can be made using self-tapping screws or pre-tapped.
When should I use a tapped hole instead of a threaded hole?
Use tapped holes in metals where high strength and precision are required, such as in machinery or automotive parts.

What materials are best suited for tapped holes?
Tapped holes work best in metals like aluminum, steel, and brass, but can also be applied to some harder plastics.
Can self-tapping screws be used in tapped holes?
No, self-tapping screws are designed to create their own threads in soft materials and are not meant for pre-tapped holes.
What tools are needed to create tapped holes?
Tapping requires a drill for the hole and a tapping tool to cut the threads, or automated CNC machinery for mass production.
Are threaded inserts the same as tapped holes?
No, threaded inserts are used in softer materials or worn-out holes to add durable threads, whereas tapped holes cut threads directly into the material.
How do I prevent thread stripping in tapped holes?
Proper lubrication during the tapping process, correct thread size, and ensuring the hole depth is sufficient can help prevent thread stripping.
What is the advantage of using threaded inserts?
Threaded inserts provide stronger threads in weak materials and can easily be replaced if damaged.
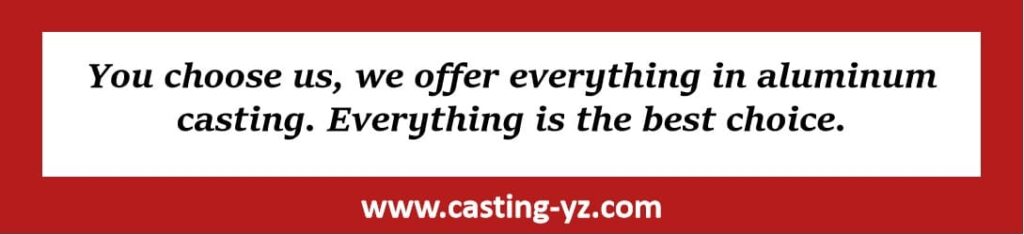
Can tapped holes be repaired?
Yes, if a tapped hole’s threads are damaged, threaded inserts can be used to repair and restore the hole’s functionality.
Are tapped holes more expensive to produce than threaded holes?
Yes, tapped holes require more precision and tooling, making them more expensive to produce, especially in high-volume applications.
What industries commonly use tapped holes?
Tapped holes are widely used in automotive, aerospace, heavy machinery, and manufacturing sectors where strong, precise fastenings are necessary.
Can tapped holes be created in plastics?
Yes, tapped holes can be created in some harder plastics, but they are more commonly used in metals.
Do tapped holes require lubrication?
Lubrication is often recommended when tapping metal to reduce tool wear and ensure clean, precise threads.
What are self-tapping screws used for?
Self-tapping screws are used to create threads in softer materials like plastics, woods, or sheet metals without the need for pre-drilling.
How deep should a tapped hole be?
The depth of a tapped hole should be at least 1.5 times the diameter of the screw or bolt to ensure a secure hold.