Aluminum is a versatile metal used across industries for its lightweight, durability, and corrosion resistance.
To enhance its appearance, durability, or corrosion resistance, various types of finishes are applied to aluminum parts.
At Yongzhu Casting, we offer a range of aluminum finishes to meet the specific needs of industries like automotive, aerospace, electronics, and architecture.
This article will cover the top six aluminum finishes available at Yongzhu Casting, their benefits, and the applications where each finish excels.
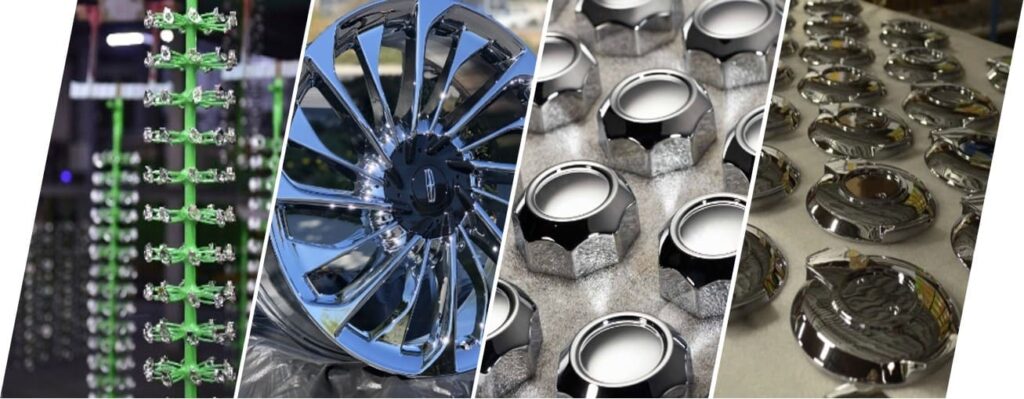
Anodizing
Anodizing is a widely used finishing process that enhances aluminum’s natural oxide layer.
By applying an electrical current in an acid solution, anodizing creates a thick, controlled oxide layer that improves corrosion resistance, wear resistance, and aesthetic appearance.
Anodized aluminum can be dyed in various colors for decorative applications.
Key Benefits of Anodizing
- Enhanced Corrosion Resistance: Anodizing significantly improves the natural corrosion resistance of aluminum, making it ideal for outdoor applications or environments exposed to moisture and chemicals.
- Durability: Anodized coatings have hardness levels up to 500 HV, improving the wear resistance of aluminum surfaces.
- Aesthetic Flexibility: The anodized surface can be dyed in a variety of colors, providing both protection and customization for applications like electronics and architecture.
Benefit | How It Helps | Application Examples |
---|---|---|
Corrosion Resistance | Protects aluminum from harsh environments. | Outdoor structures, marine components. |
Durability | Increases surface hardness, reducing wear. | Automotive parts, machinery. |
Aesthetic Flexibility | Allows for customized color finishes. | Electronics, consumer goods. |
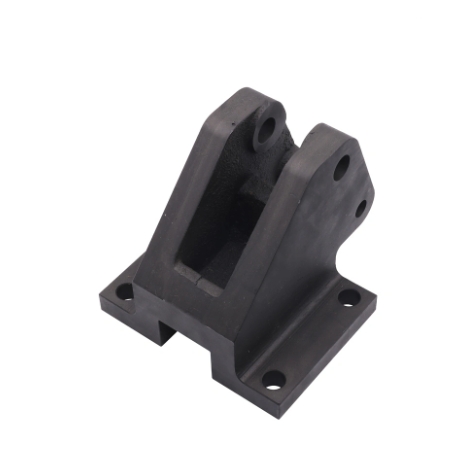

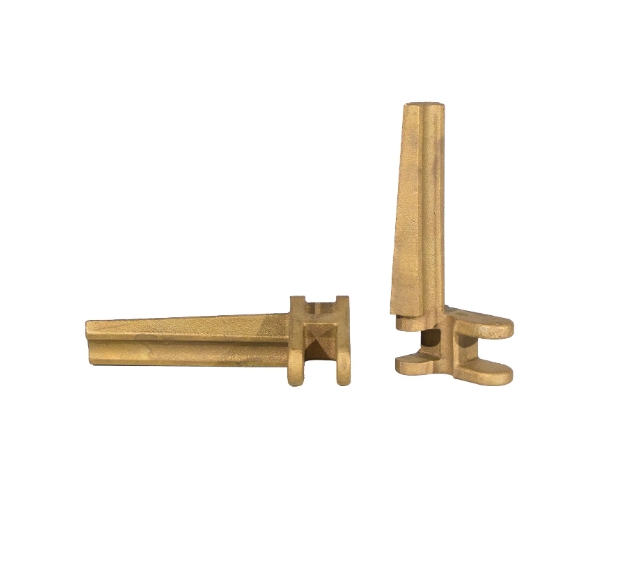
Powder Coating
Powder coating is a dry finishing process where electrostatically charged powder is sprayed onto the aluminum surface.
The coated part is then heated, causing the powder to melt and form a smooth, durable coating. Powder coating provides excellent corrosion protection, impact resistance, and a wide range of color options.
Key Benefits of Powder Coating
- Excellent Protection: Powder coating creates a strong barrier against corrosion, scratches, and wear. It’s often used for outdoor furniture, appliances, and automotive parts exposed to harsh conditions.
- Aesthetic Appeal: Powder coatings offer smooth, even coverage, enhancing both the appearance and durability of aluminum.
- Environmentally Friendly: Unlike traditional painting, powder coating produces minimal waste and contains no volatile organic compounds (VOCs), making it a more eco-friendly choice.
Benefit | How It Helps | Application Examples |
---|---|---|
Corrosion Protection | Provides a robust shield against moisture and wear. | Outdoor furniture, automotive components. |
Durable Finish | Withstands impact, chipping, and fading. | Industrial machinery, appliance surfaces. |
Eco-Friendly | Produces no VOC emissions, reducing environmental impact. | Architectural products, electronics. |
Brushed Finish
A brushed finish is created by using an abrasive belt or wheel to give the aluminum surface a fine linear texture.
This process enhances the visual appeal of the aluminum, giving it a satin-like appearance. Brushed aluminum is commonly used in products where aesthetics are important, such as appliances, electronics, and architectural panels.
Key Benefits of a Brushed Finish
- Sleek Aesthetic: The brushed finish gives aluminum a sophisticated look, ideal for high-end products like consumer electronics and kitchen appliances.
- Fingerprint Resistance: The texture of brushed aluminum helps minimize the appearance of fingerprints and smudges, keeping the surface looking clean for longer.
- Customizable: The depth and direction of the brushing can be customized based on design requirements.
Benefit | How It Helps | Application Examples |
---|---|---|
Aesthetic Appeal | Adds a high-end, modern look to products. | Electronics, kitchen appliances. |
Fingerprint Resistance | Minimizes visible smudges and fingerprints. | Consumer electronics, furniture. |
Customizable Texture | Brushing can be adjusted for different visual effects. | Architectural panels, decorative fixtures. |
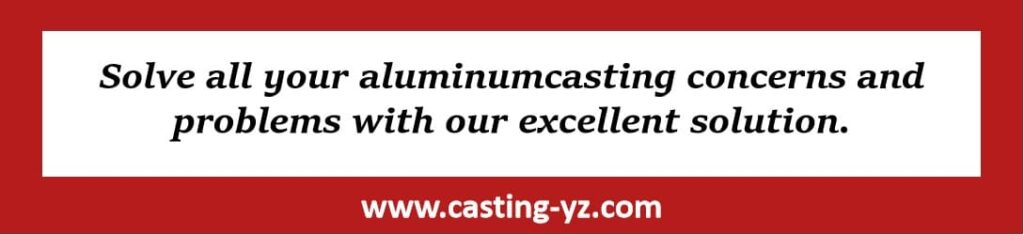
Electropolishing
Electropolishing is a finishing process that uses an electrochemical reaction to remove material from the aluminum surface, creating a smooth and highly reflective finish.
It’s often used for medical devices, food processing equipment, and pharmaceutical machinery, where cleanliness and a smooth surface are critical.
Key Benefits of Electropolishing
- Smooth Surface: Electropolishing removes surface imperfections, leaving behind a mirror-like finish that improves both appearance and functionality.
- Corrosion Resistance: The process enhances the natural oxide layer of aluminum, improving its corrosion resistance.
- Easy Cleaning: The smooth surface makes electropolished aluminum easier to clean, an important feature for medical and food industry applications.
Benefit | How It Helps | Application Examples |
---|---|---|
Smooth Finish | Removes surface imperfections, creating a reflective surface. | Medical devices, food processing equipment. |
Enhanced Cleanability | Makes aluminum easier to sanitize and maintain. | Pharmaceutical machinery, lab equipment. |
Corrosion Resistance | Boosts the natural resistance of aluminum to environmental wear. | Sanitary applications, marine components. |
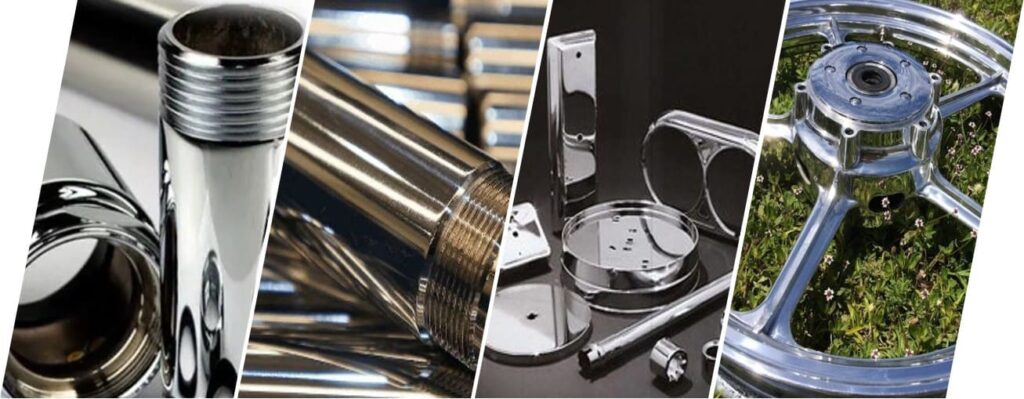
Painting
Painting is a traditional method for finishing aluminum that allows for a wide range of colors and finishes. While not as durable as powder coating or anodizing, painted aluminum is often used for decorative applications where aesthetic appeal is a priority.
Paint finishes can also provide a layer of protection against corrosion, although they may require more maintenance over time.
Key Benefits of Painting
- Color Variety: Painting allows for the application of virtually any color, making it ideal for architectural or artistic aluminum applications.
- Custom Finishes: Paint can provide various finishes such as gloss, matte, or satin, depending on the design requirements.
- Cost-Effective: Painting is often more cost-effective than powder coating for small-scale projects.
Benefit | How It Helps | Application Examples |
---|---|---|
Color Variety | Allows for a wide range of colors and finishes. | Decorative panels, signage. |
Custom Finishes | Provides flexibility in choosing gloss, matte, or satin finishes. | Artistic projects, furniture. |
Cost-Effective | More economical for small-scale projects. | Residential aluminum components. |
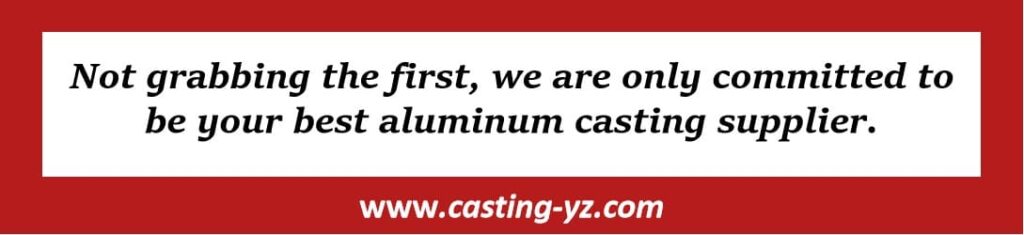
Mechanical Polishing
Mechanical polishing involves the use of abrasives to create a smooth, shiny surface on aluminum.
This process is commonly used to refine the surface finish and prepare aluminum for further treatments like anodizing or electroplating. Polished aluminum is widely used in automotive and architectural applications.
Key Benefits of Mechanical Polishing
- High-Gloss Finish: Mechanical polishing gives aluminum a bright, reflective finish that enhances its aesthetic appeal.
- Surface Preparation: Polished aluminum is often used as a base for further surface treatments, ensuring better adhesion and a superior finish.
- Improved Durability: The smoother surface achieved through polishing can reduce the buildup of dirt and debris, making the part easier to clean and maintain.
Benefit | How It Helps | Application Examples |
---|---|---|
High-Gloss Finish | Produces a bright, reflective surface for a premium look. | Automotive trim, architectural elements. |
Prepares for Treatments | Creates an ideal base for further finishing processes. | Components that will be anodized or electroplated. |
Easier to Clean | Reduces dirt and debris buildup for easier maintenance. | High-touch surfaces, consumer goods. |
Searching for High-Quality for Cast Aluminum Parts?
You’ve come to the right place! Yongzhu Casting is a certified die casting manufacturer with over 20 years of expertise in the industry.
We have successfully completed numerous die casting projects for Aluminum casting parts, particularly in your industry.
Design Review & DFM Support
Our professionals will evaluate your designs and provide suggestions for cost savings. Additionally, we offer Design for Manufacturing (DFM) assistance and conduct mold flow analyses to facilitate efficient production.
State-of-the-Art Manufacturing Equipment
Our facility is equipped with advanced hot-chamber and cold-chamber die casting machinery for aluminum and zinc production. We also utilize high-precision CNC machines in a temperature-controlled workshop, featuring 3-Axis, 4-Axis, 5-Axis, and 7-Axis setups to manage any project you have.

Rigorous Quality Control Measures
Our dedicated quality control team ensures that all parts meet the highest standards of quality and consistency. We employ high-accuracy measurement instruments, including CMM, spectrometers, and X-ray detectors.
Comprehensive Surface Treatment Options
We provide a variety of surface finishing techniques for your precision die casting components. Our in-house services include cleaning, polishing, anodizing, shot blasting, and painting.
Flexible Project Acceptance
While larger manufacturers often shy away from low-volume projects, and smaller ones may struggle with quality, Yongzhu Casting stands apart. We prioritize customer satisfaction and willingly accept high-mix, low-volume projects like yours.