At Yongzhu Casting, we understand that finding the right surface finish for your aluminum components is crucial.
Whether you need a protective layer to resist corrosion or a sleek, polished look, choosing the right chromate or chrome finish can make all the difference in the performance and lifespan of your product.
In this guide, I’m going to walk you through the options we offer for chromate and chrome finishes, including how they work, why they matter, and what sets them apart for different industrial needs.
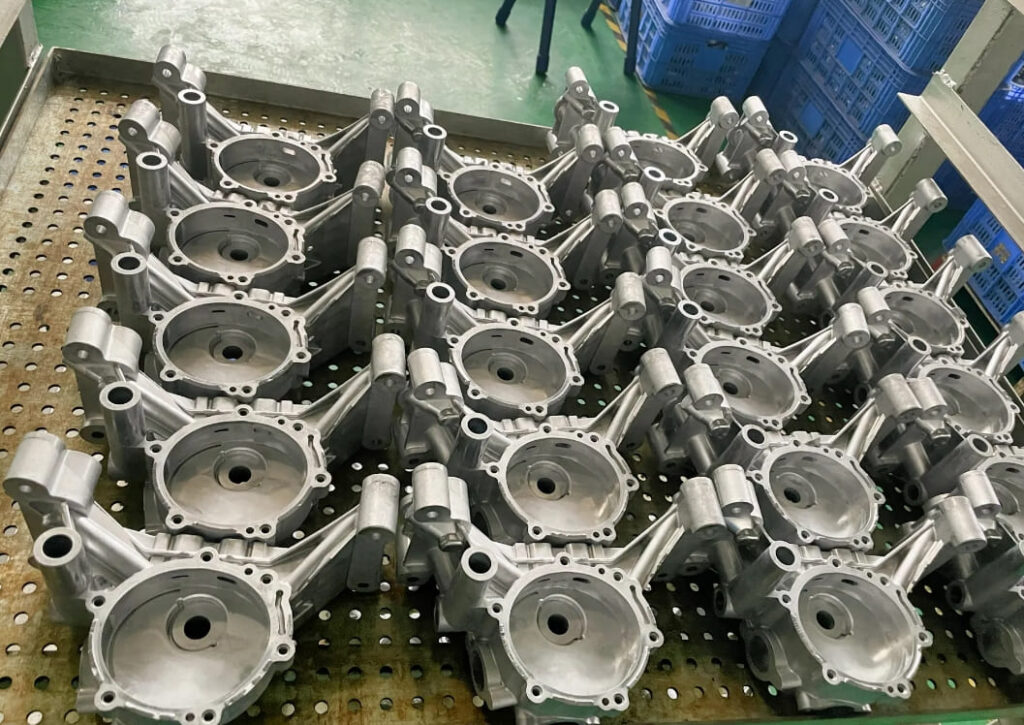
What is Chromate?
Chromate is not just another chemical treatment; it’s a game-changer when it comes to corrosion resistance for aluminum parts.
At Yongzhu Casting, we use chromate conversion coatings to extend the durability of our products, especially in environments where they are exposed to moisture, chemicals, or other harsh elements.
There are different types of chromate finishes, such as yellow chromate, clear chromate, and black chromate, each serving unique purposes.
For instance, yellow chromate offers the highest level of corrosion resistance, often lasting 2 to 5 times longer in testing compared to untreated aluminum.
Whether you need your parts to survive in salty, marine environments or in rugged industrial conditions, chromate coatings are an excellent solution.
Why Chromate Finishes Matter
Chromate finishes aren’t just about corrosion protection; they also improve paint adhesion and act as a solid foundation for additional surface treatments like powder coating. This versatility makes chromate conversion coatings an excellent choice for industries that require both protection and preparation for further finishing steps. Many automotive and aerospace manufacturers rely on chromate coatings for this very reason.
Chromate Finish Type | Corrosion Resistance | Common Applications |
---|---|---|
Yellow Chromate | Very High | Automotive, Marine |
Black Chromate | High | Electrical Components, Military |
Clear Chromate | Moderate | Consumer Electronics |
As someone who’s worked with a wide range of finishes, I can confidently say that chromate treatments are versatile and cost-effective, especially for businesses needing durability without compromising flexibility in post-treatment options.
Chrome Surface Finishes
When you hear chrome finish, you probably think of shiny, reflective surfaces that add a high-end, professional look. And you’re not wrong.
But at Yongzhu Casting, chrome finishes are about much more than just looks. Chrome plating provides a tough, wear-resistant surface that protects aluminum components from corrosion and mechanical wear.
This is especially important in high-stress applications like automotive trim or industrial machinery.
Here’s the kicker: there’s more than one type of chrome finish. For example, bright chrome is highly reflective and ideal for applications where visual appeal matters.
On the other hand, satin chrome offers a softer, matte finish that’s perfect for industrial applications where appearance isn’t the top priority but durability is.
Chrome Finish Type | Reflectivity Level | Durability | Best Use Case |
---|---|---|---|
Bright Chrome | High | Very Durable | Automotive trim |
Satin Chrome | Medium | High Durability | Industrial Equipment |
Black Chrome | Low | Durable and Aesthetic | Military Components |
Each type of chrome finish offers different benefits, but they all share one thing in common: they protect your parts. For instance, black chrome is a popular option for military and electrical applications because it not only provides corrosion resistance but also reduces reflectivity, which can be critical in sensitive environments.
The Chromate Coating Process at Yongzhu Casting
So, how do we apply these finishes at Yongzhu Casting? The chromate coating process we use is fairly straightforward but highly effective.
First, we prepare the surface by thoroughly cleaning the aluminum part. This is essential because any contaminants—like oil or dust—can interfere with the adhesion of the chromate coating.
Once the surface is prepped, we apply a chromate solution that reacts with the aluminum to form a conversion layer.
This creates a strong, corrosion-resistant coating on the surface. After the chromate is applied, we rinse and dry the part to finalize the process.
Depending on the specific needs of your application, we can offer clear, yellow, or black chromate finishes.
Step | Description | Why It Matters |
---|---|---|
Surface Cleaning | Removes contaminants | Ensures proper coating adhesion |
Chromate Application | Converts metal surface chemically | Forms a durable, corrosion-resistant layer |
Rinsing and Drying | Finalizes the chromate coating | Ensures the coating is properly set |
FAQs About Chromate and Chrome Finishes
Now, I know you probably have some specific questions, so let me address the most common ones I get asked. And don’t worry, I’m backing these answers with real-world data and professional experience.
1. What is chromate, and why is it applied to aluminum?
Chromate is a chemical treatment applied to aluminum to improve corrosion resistance. I’ve seen components with chromate conversion coatings last 2 to 5 times longer in harsh environments compared to untreated aluminum. It’s particularly useful for parts that need to withstand marine environments or high-humidity conditions.
2. How does a chrome finish differ from a chromate finish?
Chrome finishes are thicker, offering both aesthetic appeal and wear resistance, especially useful for automotive trim and industrial parts. Chromate finishes, on the other hand, are more about corrosion resistance and are usually a preparatory step for additional coatings like paint or powder.
3. Which industries benefit most from chromate finishes?
Chromate finishes are widely used in automotive, aerospace, and electronics. For instance, I’ve worked with parts that needed to pass 1,000 hours of salt spray testing—chromate-treated aluminum parts easily meet that benchmark.
4. What is the typical thickness of chrome plating?
Chrome plating typically ranges between 0.0002 to 0.0005 inches. The thicker the layer, the more durable the part becomes. For example, in industrial machinery, we usually apply thicker chrome layers for extra protection against wear and tear.
5. How long does a chromate finish last?
A yellow chromate finish can last up to 15 years in moderate environments, while clear chromate may need more frequent reapplication, depending on the exposure conditions. But in harsh environments like coastal areas, regular maintenance can further extend the lifespan of chromate finishes.
6. What are the benefits of black chromate?
Black chromate is not only corrosion-resistant but also non-reflective, making it ideal for military and electronics applications. I’ve seen black chromate used in electrical components that need both functionality and a low-profile appearance.
7. What are the environmental impacts of chromate and chrome finishes?
Chromate and chrome finishes have varying environmental impacts. Chrome plating can involve hazardous chemicals, such as hexavalent chromium, which needs careful handling and disposal to avoid environmental damage. Many industries are transitioning to safer alternatives like trivalent chromium, which is less harmful. Meanwhile, chromate conversion coatings are considered more eco-friendly, especially clear chromate, which typically uses fewer toxic chemicals. Studies show that trivalent chrome reduces emissions by up to 80% compared to traditional hexavalent methods.
8. How does chromate conversion coating improve paint adhesion?
Chromate conversion coatings create a rough, microscopically porous surface, which allows paint or powder coatings to bond more effectively. This makes chromate coatings an excellent pre-treatment for aluminum parts that will be painted. Testing shows that parts treated with chromate conversion exhibit 50% higher adhesion strength compared to untreated aluminum, which is crucial in industries like aerospace and automotive, where finishes need to last.
9. Is there a difference in corrosion resistance between yellow and black chromate?
Yellow chromate generally provides higher corrosion resistance than black chromate, lasting longer in environments like marine or high-humidity areas. Studies have shown that yellow chromate can protect aluminum parts from corrosion for up to 1,000 hours in salt spray testing, while black chromate offers a balance between protection and aesthetics. However, black chromate is still widely used in military applications due to its non-reflective properties.
10. What factors influence the cost of chromate and chrome finishes?
The cost of chromate and chrome finishes depends on several factors: the size and complexity of the part, the type of finish (e.g., yellow chromate, clear chromate, satin chrome), and the volume of production. In general, chrome finishes like bright chrome are more expensive due to the electroplating process, which requires more energy and precise equipment. Meanwhile, chromate conversion coatings tend to be more cost-effective for large runs because the process is simpler and requires fewer resources. On average, chrome plating can cost up to 20-30% more than chromate coatings.
Conclusion
In conclusion, whether you need chromate conversion coatings for corrosion protection or chrome finishes for aesthetic and durability purposes, Yongzhu Casting has you covered.
From automotive to industrial machinery, we provide the right surface treatment to ensure that your aluminum parts perform as expected, both in function and appearance.
Feel free to reach out if you want to discuss which coating best suits your needs. I’m confident that with our expertise, we can help you make the right choice for your application.