Investment casting, also known as lost-wax casting, is a manufacturing process that has been utilized for thousands of years.
This method is highly regarded for producing high-precision, complex metal components with excellent surface finishes and minimal material waste.
We specialize in investment casting to meet the growing demands of various industries, ensuring that every part meets the highest standards in terms of quality, durability, and dimensional accuracy.
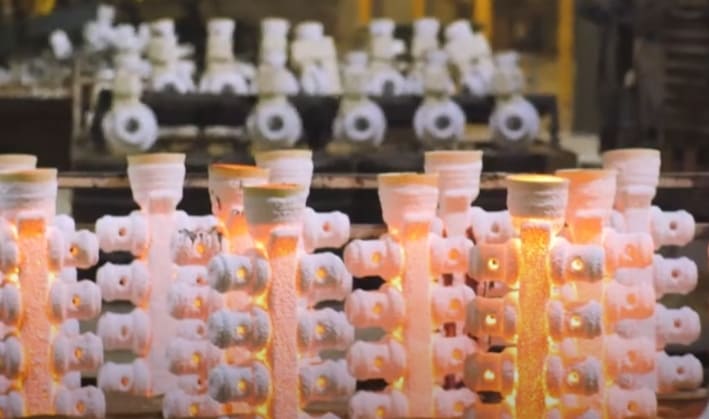
What is Investment Casting?
Investment casting is a precision metal casting process in which a wax model is coated with a refractory ceramic material.
Once the ceramic hardens, the wax is melted and drained away, leaving a hollow mold. Molten metal is poured into the mold, forming a cast part when the metal cools and solidifies.
This process is particularly useful for creating intricate designs and ensuring that the final product meets tight tolerances without the need for extensive machining or finishing.
Why Precision Casting is Also Known as Investment Casting or Lost-Wax Casting
The term “Precision Casting” is commonly used interchangeably with “Investment Casting” and “Lost-Wax Casting” due to the precision and accuracy inherent in this manufacturing process. Here’s why:
- Precision Casting: This name highlights the process’s ability to produce highly detailed and complex parts with tight tolerances. The term emphasizes the accuracy and fine detail achievable, making it ideal for industries where precision is crucial.
- Investment Casting: The process is called investment casting because the wax model is “invested” or surrounded by a ceramic shell. This term focuses on the technique of creating a ceramic mold around the wax pattern, which is then used to cast the final metal part.
- Lost-Wax Casting: This name refers to the removal or “loss” of the wax during the casting process. The wax is melted and drained after the ceramic mold hardens, leaving a cavity for molten metal. This term highlights the historical and foundational method behind the process, which has been in use for thousands of years.
These three terms are used interchangeably because they all refer to different aspects of the same process: the precision of the final product, the investment of the wax model in ceramic, and the removal of the wax.
The result is highly accurate, durable components, which are used in industries where detail and exactness are vital.
Benefits of Investment Casting
Benefit | Description |
---|---|
Precision and Accuracy | Investment casting delivers complex shapes with tight tolerances, making it ideal for intricate components. |
Excellent Surface Finish | The process allows for smooth, high-quality surface finishes, reducing post-production finishing work. |
Material Efficiency | Little material is wasted in investment casting, which reduces costs and environmental impact. |
Wide Material Variety | Investment casting supports a range of metals and alloys, including stainless steel, aluminum, and titanium. |
Cost-Effectiveness | Especially for small to medium production runs, the process provides a cost-effective solution. |
Materials Used in Investment Casting
The investment casting process is compatible with a wide variety of metals and alloys, providing flexibility for different applications. Common materials include:
- Stainless Steel: Corrosion-resistant and ideal for high-strength applications.
- Carbon Steel: Frequently used for durable components in mechanical systems.
- Aluminum: Lightweight and corrosion-resistant, suitable for aerospace and automotive industries.
- Brass and Bronze: Used for applications requiring wear resistance and low friction.
- Titanium: Known for its excellent strength-to-weight ratio and corrosion resistance, frequently used in aerospace and medical industries.
Industries That Rely on Investment Casting
Investment casting has proven itself indispensable across various industries due to its precision and versatility. Some key sectors include:
- Aerospace – Used for producing engine components, brackets, and structural parts.
- Automotive – Investment casting is favored for gear components, turbochargers, and other precision parts.
- Medical Devices – Produces highly accurate parts used in surgical instruments and medical implants.
- Energy – Essential in the production of turbine blades, valves, and other components in energy sectors.
- Defense and Military – Used in the manufacture of weaponry, missiles, and high-performance equipment.
Investment Casting Process
- Wax Pattern Creation: Wax models of the final component are created using a die or mold.
- Shell Building: The wax model is dipped in ceramic slurry to build a hard outer shell.
- Wax Removal: The hardened shell is heated to melt and remove the wax, leaving an empty mold.
- Metal Pouring: Molten metal is poured into the ceramic mold, filling the void left by the wax.
- Cooling and Solidification: The metal cools, solidifying into the shape of the final component.
- Shell Removal: The ceramic mold is broken away to reveal the cast metal part.
- Finishing Process: Any necessary finishing work, such as machining or surface treatment, is carried out to meet final specifications.
Comparison: Investment Casting vs. Other Casting Methods
Feature | Investment Casting | Sand Casting | Die Casting |
---|---|---|---|
Precision | High precision with complex geometries | Lower precision, suitable for larger parts | Medium precision for large volume production |
Surface Finish | Smooth, fine finish | Rough, requiring additional machining | Smooth, but tooling wear affects quality over time |
Material Wastage | Minimal waste | More material waste | Low waste, but high initial cost |
Part Size | Small to medium-sized parts | Best for large, bulky components | Medium-sized parts in high volumes |
Tooling Costs | Moderate tooling costs | Low tooling costs | High tooling costs |
FAQs on Investment Casting
1. What is investment casting used for?
Investment casting is used to produce precision metal components that require intricate designs, such as turbine blades, engine parts, and medical devices.
2. What materials can be used in investment casting?
A wide range of metals, including stainless steel, carbon steel, aluminum, and titanium, are commonly used in investment casting, allowing for flexibility in applications.
3. How accurate is investment casting?
Investment casting offers high dimensional accuracy, typically achieving tolerances within ±0.005 inches, making it ideal for complex, precise parts.
4. Is investment casting expensive?
While the initial tooling costs can be higher compared to other methods, investment casting becomes cost-effective in medium-volume production due to reduced material waste and minimal finishing requirements.
5. What are the advantages of investment casting over sand casting?
Investment casting provides better surface finish, higher precision, and the ability to create more complex shapes than sand casting, though it is more suited for smaller components.
6. How does the surface finish in investment casting compare to die casting?
Investment casting typically provides a smoother surface finish than die casting, particularly for complex or intricate parts, reducing the need for post-production machining.
7. How long does the investment casting process take?
The timeline varies depending on part complexity and production volume, but the process can take several days from pattern creation to final finishing.
8. What is the maximum size of parts that can be produced using investment casting?
Investment casting is generally suitable for small to medium-sized components, though larger parts can be cast with more complex arrangements.
9. What are the environmental benefits of investment casting?
The process generates less material waste, making it more environmentally friendly. Additionally, many of the materials used can be recycled.
10. How does investment casting improve product consistency?
Due to the high precision and repeatability of the process, investment casting produces highly consistent parts, especially important for critical applications like aerospace and medical devices.