Introduction
Aluminum die casting is an essential process in manufacturing, widely used across various industries such as automotive, aerospace, electronics, and telecommunications.
Its ability to produce complex, high-precision parts with durability and lightweight properties makes it a top choice for manufacturers.
The die-casting process can be costly due to several factors, such as materials, tooling, and production setup.
This article will dive into why die casting is expensive, what contributes to the costs, and—most importantly—strategies to help reduce these expenses.
Whether you’re a buyer or manufacturer, these insights will help you make informed decisions while maintaining high-quality standards in your production.
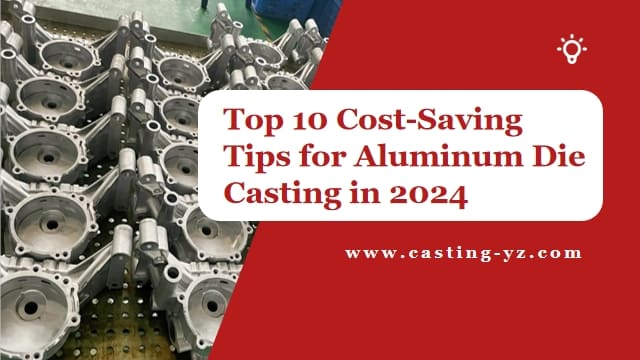
What is Aluminum Die Casting?
Die casting is a process that uses high pressure to force molten metal into a steel mold cavity, creating a solid, detailed part as the metal cools and solidifies.
Aluminum die casting specifically is popular for producing lightweight yet durable components, and the process stands out for its speed and precision compared to other casting methods.
Die casting’s advanced machinery, precision requirements, and intricate mold designs contribute to its high costs.
Why is Die Casting Expensive?
To understand why die casting can be costly, let’s examine key factors and opportunities to optimize each one.
1. Material Costs
- Aluminum is the primary material for die casting due to its lightweight and corrosion-resistant properties. Aluminum is costly, with prices around $3000 per ton. Additionally, die casting requires specialized melting furnaces for aluminum, which can cost around $2500 on average. These material and equipment expenses contribute significantly to overall production costs.
- Optimization Tip: Reduce Wall Thickness: If feasible, design parts with thinner walls. Thinner walls reduce material usage, lowering costs. Additionally, consider optimizing channel systems in the mold to ensure that material flow is efficient, as this can also help save material while achieving uniform fills.
2. Production Costs
- Production costs in die casting are driven by the type of machinery used, hourly rates, and cycle times. Die casting machines are categorized by tonnage, with larger machines capable of higher clamping forces typically used for larger parts or materials requiring high pressure. A basic cold chamber die casting machine can range from $20,000 to $100,000, depending on size and quality.
- Optimization Tip: Choose the Right Die Casting Machine: For example, use a cold chamber machine for metals with high melting points like aluminum. While cold chamber machines may be pricier upfront, their ability to handle high melting points makes them ideal for aluminum, potentially saving on repairs and production delays in the long run. Additionally, optimizing cycle times by shortening cooling and ejection times can reduce production costs.
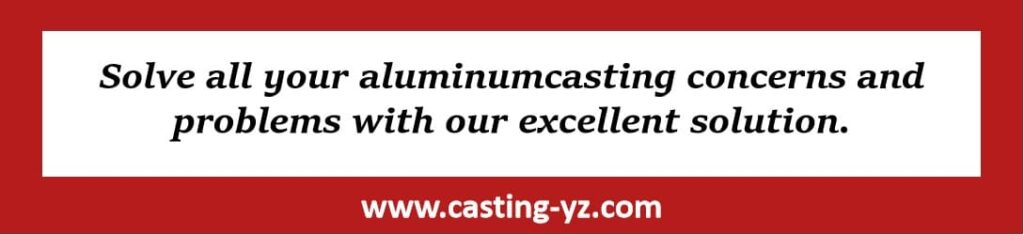
3. Mold Costs
- Mold design and production are some of the highest costs in die casting, especially for complex parts requiring precise, high-quality molds. Complex molds demand high-grade tooling materials, such as H13 steel, and advanced manufacturing techniques like CNC machining, which can cost from $11,000 to as much as $150,000 for industrial molds.
- Optimization Tip: Reuse and Modify Existing Molds: Where possible, use modular molds or incorporate cores to produce variations of similar parts. This way, molds can be reused or adjusted rather than completely redesigned, resulting in significant savings.
4. Tooling Costs
- Tooling in die casting includes not only the mold but also auxiliary equipment like CNC machines, tumbling machines, and deburring equipment. Tooling costs are generally influenced by the quality of the tools and their longevity.
- Optimization Tip: Invest in High-Quality Tooling for Durability: High-quality tools may have a higher initial cost but typically result in lower long-term expenses due to fewer replacements and repairs. Regular maintenance schedules also extend the life of tools, reducing tooling expenses over time.
5. Labor and Utility Expenses
- Operating die casting machinery is energy-intensive, with average machines consuming approximately 455 KJ per hour. Alongside energy costs, labor rates contribute to total production expenses, especially when additional processes like polishing, coating, and quality inspections are needed.
- Optimization Tip: Automate Processes Where Possible: Automating repetitive tasks, such as part ejection and inspection, reduces manual labor costs. Automation also speeds up production, ensuring consistent quality and reducing the potential for human error. Furthermore, using energy-efficient machinery or recycling excess materials where possible can help cut utility costs.
6. Performance Specifications and Design Complexity
- Designing die-cast parts with complex geometries often requires additional features, such as gussets and ribs, to meet strength and performance requirements. These added elements drive up costs in both tooling and production.
- Optimization Tip: Simplify Design Without Compromising Quality: Simplifying part geometry helps reduce mold complexity, saving on tooling costs. Additionally, by using mold flow analysis software, manufacturers can simulate the metal flow, cooling, and solidification process, allowing for a more efficient mold design that meets specifications without unnecessary complexity.
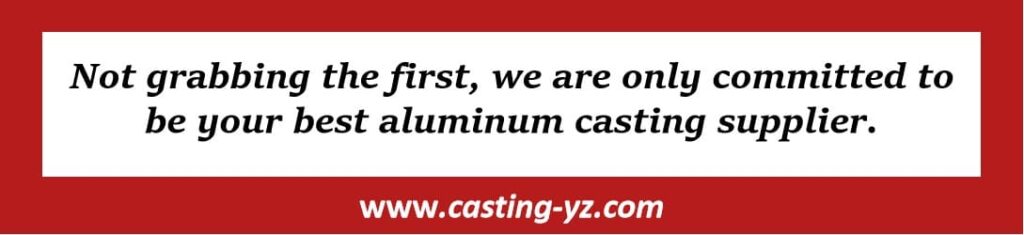
7. Secondary Processes and Finishing
- Post-casting processes, including trimming, deburring, polishing, and surface treatments like powder coating or anodizing, add to production costs. These steps are necessary for achieving high-quality finishes and meeting product specifications.
- Optimization Tip: Minimize Secondary Processes Through Design: By designing for fewer post-casting processes, manufacturers can save time and labor costs. For example, if the casting process can achieve a smooth enough surface finish, additional polishing or coating may not be required. Integrating finishing into the casting process directly can help reduce secondary processing costs.
8. Mold Flow Analysis and Simulation
- Mold flow analysis is crucial for efficient mold design, but it adds to the initial production cost. This process allows engineers to identify potential issues, optimize the mold structure, and reduce waste.
- Optimization Tip: Conduct Mold Flow Analysis: While it may be an upfront expense, mold flow analysis can prevent costly issues down the line. By simulating the die casting process and identifying potential defects before production, manufacturers save on material and rework costs.
9. Selecting the Right Supplier
- Sourcing aluminum die casting from suppliers with limited capabilities can lead to higher costs due to longer lead times, quality issues, or limited service options. The best suppliers often provide comprehensive services, including mold creation, die casting, and post-casting processes.
- Optimization Tip: Choose a Supplier Who Specializes in Your Needs: Look for suppliers with the necessary experience, equipment, and capacity to meet your production needs. Getting quotes from multiple suppliers and comparing their offerings can help ensure you get the best value.
10. Volume and Production Scale
- Die casting typically benefits from economies of scale, where larger production runs result in lower per-part costs. However, producing on a small scale can make die casting appear costly, as tooling and setup costs are distributed across fewer units.
- Optimization Tip: Plan for High-Volume Production: If possible, plan production in high volumes to spread out the initial tooling and setup costs. For smaller runs, consider alternative manufacturing methods or look for ways to adapt existing molds for similar parts, maximizing efficiency.
Searching for High-Quality for Cast Aluminum Parts?
You’ve come to the right place! Yongzhu Casting is a certified die casting manufacturer with over 20 years of expertise in the industry.
We have successfully completed numerous die casting projects for Aluminum casting parts, particularly in your industry.
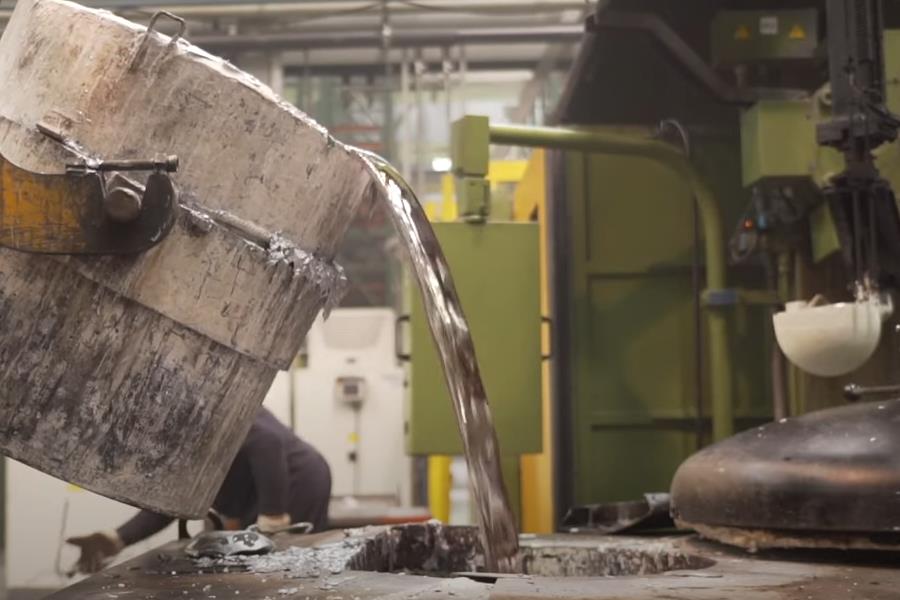
Zhejiang Yongzhu Casting Technology Co., Ltd.
Location: Zhejiang, Shaoxing
Company type: Manufacturing
Year Founded: 2004
Main Products: Aluminium die casting, Mold Making, Die Casting, Sand Casting, Gravity Casting
Leading Chinese producer Yongzhu Casting is formerly known as Hangzhou Higer Metal Products Co., Ltd., was established in 2004.
With 20 years of experience in the industry, we are a specialized manufacturer in Aluminum casting and Machining.
Our products are widely used in various applications such as Automotive, Energy, Lighting, Medical, Home Furnishings, Machinery & Equipment etc. Below is one of our products.
It’s worth mentioning that the evolution of rapid logistics has transformed how industries approach purchasing. Aluminum casting orders can now be sourced from overseas suppliers efficiently.
For instance, working with YONGZHU CASTING, you can inquire, order, and even find better value than your local options—all while maintaining assured quality.
Design Review & DFM Support
Our professionals will evaluate your designs and provide suggestions for cost savings. Additionally, we offer Design for Manufacturing (DFM) assistance and conduct mold flow analyses to facilitate efficient production.
State-of-the-Art Manufacturing Equipment
Our facility is equipped with advanced hot-chamber and cold-chamber die casting machinery for aluminum and zinc production.
We also utilize high-precision CNC machines in a temperature-controlled workshop, featuring 3-Axis, 4-Axis and 5-Axis setups to manage any project you have.
Rigorous Quality Control Measures
Our dedicated quality control team ensures that all parts meet the highest standards of quality and consistency. We employ high-accuracy measurement instruments, including CMM, spectrometers, and X-ray detectors.
Comprehensive Surface Treatment Options
We provide a variety of surface finishing techniques for your precision die casting components. Our in-house services include cleaning, polishing, anodizing, shot blasting, and painting.
Flexible Project Acceptance
While larger manufacturers often shy away from low-volume projects, and smaller ones may struggle with quality, Yongzhu Casting stands apart. We prioritize customer satisfaction and willingly accept high-mix, low-volume projects like yours.

Tips to Lower Die Casting Costs in 2024
1. Optimize Mold Design
By focusing on mold design optimization, manufacturers can reduce costs while improving efficiency.
CAD and CAE simulation software enables virtual testing and analysis, allowing engineers to identify potential flaws and optimize mold designs before production.
This step significantly cuts down on trial-and-error testing, leading to savings on both time and materials.
2. Use Core Inserts for Standardized Parts
If parts have standard design elements that can be used across multiple products, consider using core inserts. This approach reduces the need for unique molds for each product.
Modular cores allow for flexibility, meaning that slight changes to parts don’t require creating an entirely new mold.
3. Reuse Existing Molds
When molds reach their end life, reusing parts of older molds can lead to savings.
Keeping a durable mold frame allows for replacement of only the core elements, reducing expenses related to full mold replacements.
4. Control Material and Wall Thickness
Choosing thinner walls where feasible can reduce the volume of material needed and lower costs.
Although thicker sections might sometimes be necessary for structural reasons, using reinforced design features such as ribs or gussets can achieve strength without added material.
5. Evaluate Supplier’s Equipment and Capacity
Choose suppliers who have the right equipment for your specific requirements.
Small suppliers are suitable for low-volume or high-precision orders, while larger companies with automated systems and high-capacity machines are ideal for bulk orders with rigorous timelines.
Choosing the Right Aluminum Die Casting Supplier
Finding a reliable aluminum die casting supplier is key to balancing cost and quality. Here are some considerations:
- Evaluate Production Capabilities
Suppliers with modern equipment, including CNC machines and automated casting systems, are better equipped to deliver high-quality products at scale. Ensure that the supplier’s equipment matches your requirements, particularly if you need high-precision parts. - Check Quality Standards and Certifications
A supplier with ISO 9001 and IATF 16949 certifications, among others, shows commitment to quality and regulatory compliance. These certifications indicate stringent quality control measures, which is crucial for industries like automotive and aerospace. - Consider Geographical Proximity and Logistics
Local suppliers or those with robust logistics networks can help reduce transportation costs and ensure timely delivery. Overseas suppliers may offer competitive pricing, but factors like shipping fees and import tariffs can add to the overall cost. - Communication and Service
An effective supplier relationship is built on clear communication. Choose a supplier that understands your specifications and is responsive to adjustments. A good partnership can lead to smoother transactions and consistent quality.
Conclusion
The die-casting process, while invaluable for producing high-quality, complex parts, can be expensive due to material, tooling, and production costs. From optimizing mold design and reducing material usage to carefully selecting suppliers, each step offers opportunities for savings.
Choosing the right supplier further enhances cost-effectiveness by ensuring quality and efficiency in every production run.
Whether you’re in need of small, high-precision parts or large, high-volume orders, understanding and applying these insights will help you achieve the best balance of cost and quality in aluminum die casting.
Unimaginable advances in logistics have transformed how industries make purchases.
Aluminum casting orders can now be sourced internationally with ease, especially from YONGZHU CASTING, where you can inquire and place orders confidently—often at a better value than local suppliers, with quality equally assured.