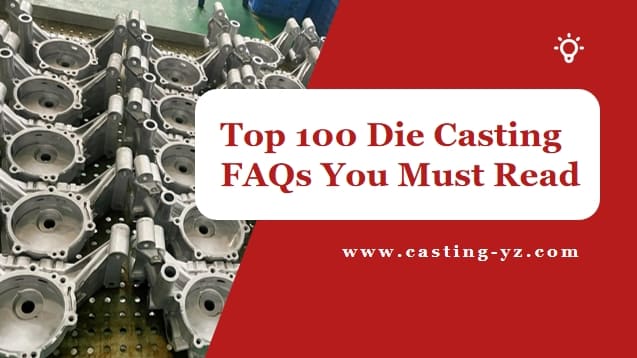
What is die used for casting?
A die is a reusable metal mold used in the high-pressure die casting process. It is designed to shape molten metal into a precise form.
What are the two types of die casting?
There are two primary types of die casting:
- Hot-chamber die casting: The molten metal is kept in a chamber, and a plunger forces it into the die cavity.
- Cold-chamber die casting: Molten metal is transferred from a separate furnace into the machine before being injected into the die.
Why is it called die casting?
“Die casting” refers to the process where molten metal is injected under high pressure into a reusable metal mold, or “die,” to create precise parts.
What is the difference between die casting and normal casting?
Die casting is a high-pressure process using reusable molds, resulting in precise, fast production. Traditional casting (like sand casting) uses gravity and disposable molds, leading to slower, less accurate results.
Feature | Die Casting | Normal Casting (e.g., Sand Casting) |
---|---|---|
Mold | Reusable die | Disposable sand mold |
Process | High-pressure | Gravity flow |
Production speed | Faster | Slower |
Accuracy | High | Lower |
Surface finish | Smoother | Rougher |
Is die casting good or bad?
Die casting is a highly effective method for mass production of precision parts. It excels in producing parts with consistent quality, but may not be ideal for small batches due to high initial costs for die creation.
Is die casting expensive?
Yes, die casting can be expensive, especially for small production runs. The cost is largely driven by the initial investment in tooling, machinery, and die creation.
What are the disadvantages of die casting?
The main drawbacks include:
- High initial costs for tooling and die creation.
- Limited design flexibility for intricate or complex parts.
- It is not suitable for very high-melting-point metals like steel or titanium.
What is most widely used for die casting?
Aluminum is the most widely used metal in die casting, known for its good castability, strength-to-weight ratio, corrosion resistance, and recyclability.
What is the easiest metal to cast with?
Zinc and pewter are considered the easiest metals to cast due to their low melting points and good fluidity.
Metal | Melting Point | Advantages for Casting |
---|---|---|
Zinc | 425°C (797°F) | Lower temperature, good flowability |
Pewter | 230°C (446°F) | Very low melting point, easy to work with |
What metal is not used in die casting?
Metals with very high melting points, like iron, steel, tungsten, and molybdenum, are not typically used in die casting due to their inability to withstand the high pressures and temperatures involved.
Metal Category | Reason for Exclusion |
---|---|
Iron & Steel | High melting point, difficult to cast |
Tungsten & Molybdenum | Extremely high melting points |
Highly Reactive Metals | Safety hazards (e.g., oxidation) |
What does diecast mean?
As a noun, “diecast” refers to products made through the die casting process, such as miniature models. As a verb, it refers to the manufacturing process where molten metal is injected under high pressure into a die to form parts.
What products are produced by die casting?
Die casting is used to manufacture a wide variety of products, including:
- Automotive parts: Engine blocks, transmission components, wheels.
- Consumer electronics: Housings for smartphones, laptops, and game consoles.
- Toys & sporting goods: Die-cast models like cars, trucks, and figurines.
What products are made by high-pressure die casting?
High-pressure die casting produces parts for:
- Automotive Industry: Engine blocks, cylinder heads, and gearboxes.
- Aerospace: Lightweight components for aircraft.
- Electrical & Electronics: Housings for devices and connectors.
What is a casting die machine?
A casting die machine is a specialized piece of equipment used in the die casting process to inject molten metal into the die cavity under high pressure to form parts.
What are the two types of die casting machines?
- Hot-Chamber Die Casting Machine: Used for metals with low melting points, such as zinc.
- Cold-Chamber Die Casting Machine: Used for metals with higher melting points, such as aluminum and copper alloys.
How much does a casting die mold cost?
The cost of a die can vary depending on its complexity:
- Simple die: $2,000 – $50,000
- Moderately complex die: $50,000 – $100,000+
- Highly complex die: Over $100,000
Is die casting cheaper than machining?
Die casting is typically more cost-effective than machining for high-volume production because it involves faster processing and lower unit costs after the initial investment in die creation.
Feature | Die Casting | Machining |
---|---|---|
Upfront cost | High | Low |
Cost per unit | Low (high volume) | High |
Production speed | Fast | Slower |
Design flexibility | Limited | More flexible |
What is the structure of die casting?
The die casting process involves several key components:
- Die (Mold): Shapes the molten metal into the desired form.
- Sprue: Channel through which molten metal enters the die.
- Runners: Distribute the metal within the die.
- Ejector pins: Push the solidified part from the die.
What are the different types of die casting processes?
There are several variations of die casting, including:
- Cold Chamber Die Casting: Metal is melted in a separate furnace and injected into the mold.
- Hot Chamber Die Casting: The metal is melted within the machine and directly injected.
- Vacuum Die Casting: A vacuum is created before the metal is injected to reduce porosity and enhance the quality of parts.
What are the advantages of using aluminum in die casting?
Aluminum offers a number of advantages for die casting, including:
- Lightweight and durable.
- Excellent strength-to-weight ratio.
- Corrosion-resistant.
- Easily recyclable.
- Good thermal and electrical conductivity.
Can other metals besides aluminum, zinc, and magnesium be die-cast?
Yes, but with limitations. Metals like iron, steel, and copper alloys require special equipment due to their higher melting points. Reactive metals pose safety challenges in the casting process.
What are some factors affecting the surface finish of die-cast parts?
Factors include:
- Die temperature: Affects metal flow and surface smoothness.
- Injection pressure: Higher pressures improve surface quality.
- Material choice: Different metals have varying finish characteristics.
- Post-processing treatments: Polishing, plating, and coatings enhance surface quality.
What is the difference between die casting and investment casting?
Die Casting:
- Utilizes reusable metal molds (dies) and injects molten metal under high pressure.
- Ideal for mass production of small to medium-sized parts.
- Offers high dimensional accuracy, smoother surfaces, and faster production rates.
Investment Casting:
- Involves creating a wax model, coating it with a ceramic shell, and then melting the wax away.
- Suitable for parts with complex geometries and intricate details.
- Typically used for low to medium-volume production of precision components, often in industries like aerospace and medical devices.
Key Differences:
Feature | Die Casting | Investment Casting |
---|---|---|
Mold Type | Reusable metal die | Ceramic mold |
Production Speed | Faster (mass production) | Slower (precision parts) |
Part Complexity | Less complex shapes | More intricate designs |
Materials | Limited to lower melting point metals (Al, Zn, Mg) | Suitable for high melting point metals (steel, titanium) |
Surface Finish | Smooth, minimal post-processing | High surface finish, may require minimal post-processing |
What are some common defects in die casting?
Common defects in die casting include:
- Porosity – Small voids inside the part, often caused by trapped air or gases during the injection process. This can be reduced by optimizing the venting system and using vacuum die casting.
- Cold shuts – Occur when two flows of molten metal do not fuse correctly, often due to inadequate temperature control or insufficient injection speed.
- Flash – Excess metal that leaks out between the die halves, typically caused by misalignment or excessive injection pressure.
- Warping – Deformation of the part after cooling, often due to uneven cooling rates or part geometry.
- Inclusion – Foreign materials, like oxides or debris, that get trapped in the casting, typically due to poor material handling or improper die maintenance.
Each defect can usually be minimized or corrected through better process control, improved die design, or the use of higher-quality materials.
What metals are commonly used in die casting?
- Aluminum – Lightweight, corrosion-resistant, and strong, making it ideal for automotive, aerospace, and electronics industries.
- Zinc – Low melting point, excellent fluidity, and good surface finish, widely used in consumer electronics and automotive applications.
- Magnesium – Lightweight and strong, suitable for aerospace and automotive parts requiring reduced weight.
- Copper – Used for parts requiring high thermal and electrical conductivity.
- Lead – Rarely used today due to environmental concerns, but once popular for its ease of casting.
- Tin – Primarily used for small parts or for making alloys with other metals.
Each metal is selected based on its specific properties such as melting point, strength, and suitability for the final product.
How can die casting be optimized for better part quality?
To optimize die casting for better part quality, consider the following:
- Die Design – A well-designed die with proper venting, gating, and runner systems can significantly improve the flow of molten metal and reduce defects.
- Material Selection – Choosing the right material with optimal melting point and fluidity for the part design ensures better casting quality.
- Injection Pressure and Speed – Proper control of injection pressure and speed ensures uniform filling of the die and prevents defects like cold shuts or porosity.
- Die Temperature Control – Maintaining a consistent die temperature is critical to ensure uniform solidification and avoid warping.
- Post-Processing – Techniques such as heat treatment, surface polishing, or machining can be applied to improve mechanical properties and surface finish.
Can die casting be used for parts with complex geometries?
Yes, die casting can be used for parts with relatively complex geometries, but there are some limitations. Parts with undercuts, deep cavities, or intricate designs may require special die modifications, such as side cores or collapsible cores, to allow for proper ejection of the part.
For extremely complex parts, other manufacturing methods, like investment casting or 3D printing, might be more suitable. However, die casting is an excellent choice for parts that require high precision and surface finish, provided the design constraints are well-understood.
What industries benefit the most from die casting?
Die casting is widely used in many industries due to its ability to produce high-precision, mass-produced parts. Some of the major industries include:
- Automotive – Engine blocks, wheels, transmission parts, and other lightweight, high-strength components.
- Aerospace – Components like structural parts, engine components, and housings that require strength and lightweight properties.
- Electronics – Housings for smartphones, laptops, and other consumer electronic devices.
- Medical – Precision parts for medical devices such as implants, surgical tools, and housings for medical equipment.
- Consumer Goods – Products like hardware, toys, and sporting goods.
- Industrial Equipment – Components for machinery, hydraulics, and other heavy-duty applications.
What is the difference between cold chamber and hot chamber die casting?
Cold Chamber Die Casting:
- Used for metals with higher melting points, such as aluminum, magnesium, and copper alloys.
- The metal is melted in a separate furnace and then ladled into the injection chamber.
- Suitable for parts requiring high-strength and resistance to corrosion.
Hot Chamber Die Casting:
- Used for metals with lower melting points, such as zinc, lead, and tin alloys.
- The injection system is directly connected to the molten metal, reducing the need for ladling.
- Offers faster cycle times and is ideal for high-volume production of smaller parts.
Comparison:
Feature | Cold Chamber | Hot Chamber |
---|---|---|
Suitable Metals | Aluminum, Magnesium, Copper | Zinc, Lead, Tin |
Injection System | Separate furnace, ladling | Direct injection from furnace |
Cycle Time | Slower | Faster |
Strength of Parts | Higher strength | Moderate strength |
Part Size | Larger parts | Smaller parts |
How does die casting contribute to sustainability in manufacturing?
Die casting contributes to sustainability in several ways:
- Material Efficiency – The precision of die casting reduces material waste, with parts being nearly net shape, requiring minimal finishing.
- Energy Efficiency – The use of hot chamber die casting (for low melting point metals like zinc) allows faster production times, reducing energy consumption.
- Recycling – Die-cast metals like aluminum and zinc are 100% recyclable, reducing the need for virgin raw materials and minimizing environmental impact.
- Reduced Waste – Due to the high precision of die casting, there is minimal scrap or waste generated in the production process.
- Lightweight Parts – In industries like automotive, die casting helps produce lightweight components that improve fuel efficiency and reduce carbon footprints.
These factors make die casting a highly sustainable manufacturing method, particularly for industries focused on reducing environmental impacts.
What is the significance of die casting in the automotive industry?
Die casting plays a critical role in the automotive industry due to its ability to produce lightweight, strong, and durable parts that meet the high demands of the sector. Key advantages include:
- Lightweight Parts – Components like engine blocks, wheels, and transmission parts are made using die casting, contributing to fuel efficiency and overall vehicle performance.
- High Precision – Die casting produces parts with tight tolerances and consistent quality, ensuring optimal performance and safety.
- Cost Efficiency – Die casting allows for high-volume production with low unit costs, making it ideal for automotive manufacturers who require large quantities of parts.
- Durability – Parts produced by die casting are strong and resistant to wear, corrosion, and high temperatures, essential for automotive applications.
- Complex Geometries – Die casting enables the production of intricate, complex parts, which are often required for automotive designs and functions.
Examples of automotive parts made with die casting include engine blocks, transmission housings, and wheel rims.
What is the role of die casting in the electronics industry?
In the electronics industry, die casting is used to manufacture components that require precision, strength, and excellent thermal properties. Die-cast parts are used in products like:
- Casings and Housings – For smartphones, laptops, tablets, and other electronic devices, die-cast metals like aluminum are commonly used for their durability and lightweight properties.
- Heat Sinks – Die casting is used to create heat sinks for computers, LED lighting, and power supply units, where efficient heat dissipation is crucial.
- Connectors and Switches – Die casting helps produce high-precision electrical connectors and switches, which are key components in electronic devices.
- Radiators – In some electronic equipment, die-cast parts are used as heat exchangers or radiators due to their excellent thermal conductivity.
The primary benefits of die casting in electronics are cost-effectiveness, high precision, and the ability to create complex shapes that improve performance and aesthetics.
What is the lifespan of a die casting die?
The lifespan of a die casting die can vary significantly based on factors such as the material used, the complexity of the part, and the production volume. On average:
- Aluminum Die Castings – Die life can range from 100,000 to 500,000 shots, depending on the alloy used and maintenance practices.
- Zinc Die Castings – Dies typically last longer than those used for aluminum, often between 200,000 to 1 million shots.
- Magnesium Die Castings – Dies for magnesium alloys tend to have a shorter lifespan, often in the range of 50,000 to 200,000 shots.
To extend die life, proper maintenance, cooling, and lubrication systems are essential, along with ensuring that the die is designed to withstand the specific stress and temperature conditions of the casting process.
Can die casting be used for thin-walled parts?
Yes, die casting is highly effective for producing thin-walled parts, especially for materials like aluminum and zinc alloys. Thin-walled components are commonly used in industries like automotive, electronics, and consumer products due to their lightweight nature.
Key Considerations for Thin-Walled Die Casting:
- Material Selection – Choosing the right material with good fluidity and low shrinkage is essential for casting thin walls.
- Injection Pressure – Higher injection pressures are often needed to ensure the molten metal fills the die and forms uniform walls.
- Wall Thickness – While thin walls can be cast, there is a practical limit based on the material and design. Typically, walls range from 1 mm to 3 mm, though some die castings can achieve even thinner walls with advanced techniques.
- Die Design – A well-designed die with optimized gating and venting systems ensures that molten metal flows smoothly, preventing defects like cold shuts or incomplete filling.
Thin-walled die casting is commonly used for applications like mobile phone casings, automotive brackets, and lightweight housing for electronic components.
What are the main benefits of using aluminum for die casting?
Aluminum is one of the most popular materials used in die casting due to its numerous advantages:
- Lightweight – Aluminum is significantly lighter than other metals, making it ideal for applications where weight is a concern, such as in automotive and aerospace industries.
- Corrosion Resistance – Aluminum naturally forms a protective oxide layer, making it highly resistant to corrosion, which is crucial for outdoor and marine applications.
- Good Thermal Conductivity – Aluminum is an excellent conductor of heat, making it ideal for heat sink and heat exchanger applications in electronics and automotive industries.
- Strength-to-Weight Ratio – Aluminum die castings have a high strength-to-weight ratio, providing strong and durable parts without added weight.
- Recyclability – Aluminum is highly recyclable, making it an environmentally friendly option that can be reused without losing its properties.
These properties make aluminum a versatile material for producing high-performance, lightweight parts with excellent durability and heat resistance.
Can die casting be used for both small and large parts?
Yes, die casting is a versatile process that can be used to produce both small and large parts, though the method of casting and tooling may differ.
- Small Parts: Die casting is highly effective for small parts like electronic housings, automotive components, and consumer goods, offering high precision and low-cost mass production.
- Large Parts: Larger die castings, such as engine blocks or large structural parts, are also achievable. However, larger parts may require more robust tooling, longer cycle times, and potentially a different approach to maintain quality and precision.
The key is ensuring the appropriate material, die design, and process parameters are chosen for the size of the part being produced.
What is the typical cycle time for die casting?
The cycle time in die casting refers to the time it takes to complete one full cycle of the die casting process, from injection to part ejection. Typical cycle times are:
- Zinc Die Casting: 10-30 seconds per cycle
- Aluminum Die Casting: 30-60 seconds per cycle
- Magnesium Die Casting: 30-60 seconds per cycle
The cycle time can vary depending on the complexity and size of the part, the material being cast, and the specific machine used. The speed of the cycle is a key factor in determining the overall production efficiency and cost.
How do die casting parts compare to sand cast parts?
Die Casting vs. Sand Casting:
- Precision: Die casting offers much higher precision and tighter tolerances, producing parts that require minimal post-processing. Sand casting is less precise, often resulting in rougher surfaces and greater variation in dimensions.
- Production Speed: Die casting is faster, with cycle times measured in seconds or minutes, while sand casting can take hours or even days for a single part to be made.
- Material Selection: Die casting is often used for metals like aluminum, zinc, and magnesium, while sand casting is typically used for metals such as iron and steel.
- Cost: Die casting is more cost-effective for high-volume production, but initial tooling costs can be higher compared to sand casting, which is more cost-effective for low-volume, custom, or prototype parts.
Die casting is better suited for high-precision, high-volume applications, while sand casting is preferred for larger, more complex parts with lower production runs.
How does die casting compare to injection molding?
Die Casting vs. Injection Molding:
- Material: Die casting is primarily used for metals, such as aluminum, zinc, and magnesium, while injection molding is typically used for plastics and polymers.
- Precision: Die casting offers excellent precision for metal parts, while injection molding provides high precision for plastic parts but may not achieve the same level of detail with metals.
- Production Speed: Both processes are suitable for high-volume production, but injection molding tends to have faster cycle times for plastic parts compared to die casting for metal parts.
- Cost: Injection molding has lower initial tooling costs for plastic components, while die casting requires more expensive tooling due to the higher pressures involved in metal casting.
Overall, die casting is ideal for producing complex metal parts, while injection molding is better suited for plastic components.
Can die casting be used for producing prototypes?
Yes, die casting can be used for producing prototypes, especially when high precision, durability, and functionality are required. Prototypes made using die casting can help manufacturers test the design, functionality, and performance of a part before committing to full-scale production.
- Benefits: Die-cast prototypes offer real-world material properties and dimensional accuracy, making them more useful for testing than other rapid prototyping methods like 3D printing.
- Challenges: The initial tooling costs for die casting are higher than those for methods like 3D printing, but this can be justified if the parts are likely to be produced in high volumes once the design is finalized.
How does the gating system affect the die casting process?
The gating system is a critical component of the die casting process as it controls the flow of molten metal into the die. It directly influences the quality of the casting, and improper gating can lead to defects like incomplete filling, air pockets, or uneven cooling.
Key Factors:
- Gating Design – The placement, size, and shape of the gates affect how the molten metal flows and fills the die.
- Venting – Proper venting is essential to allow air and gases to escape during the injection process, preventing air entrapment.
- Type of Gate – There are different types of gates (e.g., direct, overflow, or side gates), and each type can have an impact on the final part quality.
Proper gating system design is essential for optimizing material flow, reducing defects, and improving cycle times.
What is the difference between die casting and forging?
Die Casting vs. Forging:
- Material: Die casting is used for metals like aluminum, zinc, and magnesium, while forging is typically used for stronger metals like steel and titanium.
- Manufacturing Process: Die casting involves injecting molten metal into a mold under pressure, whereas forging involves shaping metal by applying compressive forces.
- Strength: Forged parts typically have better mechanical properties, including higher strength and resistance to wear. Die-cast parts, while durable, are generally not as strong as forged parts.
- Cost: Die casting is more cost-effective for high-volume production, whereas forging may require more intensive labor and equipment but is better suited for heavy-duty, high-strength parts.
Die casting is preferred for complex, lightweight parts, while forging is ideal for high-strength applications.
What are the key challenges in die casting production?
- Defects: Issues like cold shuts, porosity, and flash can occur, requiring skilled operators and optimal machine settings to minimize defects.
- Tooling Costs: Die casting requires expensive molds and tooling, which can make initial production costs high, especially for low-volume runs.
- Material Selection: Choosing the right alloy for the application is critical, as different materials offer different mechanical properties, corrosion resistance, and thermal conductivity.
- Part Complexity: While die casting allows for complex shapes, overly intricate parts can lead to difficulties in filling the die properly, resulting in defects.
Managing these challenges requires expertise in die design, material selection, and process optimization.
Can die casting be used for producing high-strength parts?
Yes, die casting can produce high-strength parts, especially when using high-performance alloys like aluminum, magnesium, and zinc. The strength of a die-cast part depends on several factors:
- Alloy Selection – The right alloy can significantly enhance the strength of the part. For example, high-strength aluminum alloys (like 383 and 380 series) are commonly used in die casting for automotive and aerospace applications.
- Die Design – Proper die design, including uniform wall thickness and optimized gating, ensures that the metal fills the mold correctly and reduces the risk of defects that can weaken the part.
- Heat Treatment – Post-casting heat treatment processes can further improve the mechanical properties of die-cast parts, such as strength and hardness.
While die casting is ideal for high-volume production of complex parts, it can also meet the demands of applications requiring high strength and durability.
How do temperature and cooling rates affect die casting?
Temperature and cooling rates are critical factors in the die casting process:
- Pouring Temperature – The temperature of the molten metal affects its viscosity and flow characteristics. Too high a temperature can cause oxidation, while too low a temperature may lead to incomplete filling.
- Cooling Rate – The cooling rate of the metal during solidification affects its microstructure and mechanical properties. Faster cooling typically results in finer grain structures, which can enhance strength and fatigue resistance.
- Die Temperature – The temperature of the die affects the solidification rate and the final properties of the part. A properly controlled die temperature helps reduce defects like warping or cracking.
Proper temperature and cooling control are essential for producing high-quality die-cast parts.
How does die casting impact the automotive industry’s manufacturing process?
Die casting is widely used in the automotive industry due to its ability to produce complex, lightweight, and durable parts. The process helps automotive manufacturers achieve:
- Lightweight Components – Die casting produces parts that are lighter without compromising strength, which is essential for improving fuel efficiency and reducing carbon emissions.
- High Precision – The precision of die casting ensures that automotive components meet stringent safety and performance standards.
- Cost-Effective High-Volume Production – Die casting enables high-volume production of consistent, high-quality parts at relatively low cost, making it ideal for the mass production of automotive parts like engine blocks, transmission housings, and structural components.
- Material Efficiency – The precision of die casting allows manufacturers to minimize material waste, which is critical for reducing overall production costs.
How does die casting affect the overall cost of production?
Die casting can significantly impact the overall cost of production, especially in high-volume manufacturing, due to several factors:
- Tooling Costs: The initial cost of the molds or dies used in die casting is higher than other methods, such as sand casting or injection molding. Tooling costs can range from several thousand to tens of thousands of dollars depending on the complexity of the part and the material being used.
- Cycle Time: Die casting has relatively short cycle times, often ranging from 20 seconds to a few minutes, which can lead to high-volume production with lower per-unit costs.
- Material Waste: Die casting is a highly efficient process with minimal material waste, as excess material can be recycled and reused, reducing overall material costs.
- Labor Costs: While initial tooling costs are high, the automated nature of die casting reduces the need for manual labor, making it more cost-effective for high-volume runs.
Ultimately, die casting offers cost advantages in high-volume production, though the initial tooling investment is a key consideration.
How can die casting reduce material waste?
Die casting is known for its material efficiency because it involves injecting molten metal into precisely designed molds. The key ways in which die casting reduces material waste are:
- Precision Molding: The molds used in die casting are highly precise, resulting in parts with minimal excess material. Parts are created with near-net shape accuracy, meaning little to no material is wasted during the casting process.
- Recycling of Sprues and Gates: Any excess material, such as sprues and gates, that are not part of the final product can be melted down and reused in future runs, further reducing material waste.
- High Yield: Die casting can achieve high yield rates, especially with metals like aluminum and zinc, leading to fewer rejected parts and less wasted material.
As a result, die casting is more material-efficient compared to many other manufacturing processes, contributing to overall cost savings and environmental benefits.
What types of metals are used in die casting?
Die casting is typically used with metals that have low melting points and good fluidity. The most common metals used are:
- Aluminum: The most widely used material for die casting, aluminum is lightweight, corrosion-resistant, and has excellent thermal conductivity, making it suitable for automotive, aerospace, and electronics industries.
- Zinc: Zinc die casting is popular for producing small, intricate parts with high strength and excellent corrosion resistance. Zinc alloys are often used in the production of hardware, electronics, and consumer goods.
- Magnesium: Magnesium alloys are used in die casting for applications requiring lightweight materials with good strength-to-weight ratios, such as automotive and aerospace parts.
- Copper Alloys: Copper alloys, including bronze, are also used for die casting, though less frequently. These alloys provide good strength, corrosion resistance, and conductivity.
Each material has unique properties that make it suitable for different applications, and the choice of metal depends on the part’s intended use and performance requirements.
What are the common defects in die casting, and how can they be prevented?
Common defects in die casting include:
- Porosity: Small holes or voids in the casting caused by trapped air or gases. To prevent porosity, it’s important to design proper vents in the die, control the metal temperature, and optimize the gating system.
- Cold Shut: Occurs when molten metal flows together but doesn’t fuse properly, leading to weak spots. This can be prevented by adjusting pouring temperature, gating design, and ensuring proper mold filling.
- Flash: Excess material that escapes the die during injection. Flash can be minimized by ensuring correct clamping force and maintaining precise die alignment.
- Warpage: Distortion caused by uneven cooling or material shrinkage. To prevent warpage, controlling cooling rates and ensuring uniform wall thickness in the design can help.
- Inclusion: Contaminants or impurities trapped in the casting. Maintaining a clean molten metal bath and using high-quality materials can reduce the risk of inclusions.
Proper die design, process control, and regular maintenance of equipment can greatly reduce the occurrence of defects in die-cast parts.
How does die casting compare to machining in terms of efficiency?
Die casting and machining are both common manufacturing methods, but they have different efficiencies depending on the application:
- Die Casting: Die casting is highly efficient for producing large quantities of parts with complex shapes. Once the initial tooling is completed, the process is quick, with fast cycle times, making it ideal for high-volume production. It reduces material waste and minimizes the need for post-processing.
- Machining: Machining, on the other hand, involves removing material from a larger piece using tools like drills, lathes, or mills. While it can produce high-precision parts, it is typically slower and more expensive, especially for large quantities. It also results in more material waste.
In high-volume production, die casting is usually more efficient than machining due to lower cycle times, reduced material waste, and less post-processing required.
What is the typical lead time for die casting production?
The lead time for die casting production varies depending on factors such as part complexity, material selection, and tooling requirements. Generally, the process can be broken down into:
- Tooling Time: The initial design and manufacturing of the die or mold can take 4-8 weeks, depending on the complexity of the part and the material being used.
- Production Time: Once tooling is complete, the actual die casting production cycle is relatively quick, typically taking between 1-4 weeks for production runs, depending on the order quantity and part complexity.
- Delivery Time: Additional time is required for shipping and distribution, which can range from a few days to a couple of weeks, depending on the location and logistics.
For high-volume production, the overall lead time can be relatively short, but the tooling phase is the most time-consuming part.
How do you select the right die casting supplier?
Selecting the right die casting supplier involves evaluating several key factors:
- Expertise and Experience: Look for a supplier with a proven track record in die casting for your specific industry. An experienced supplier will have the knowledge to handle complex designs and offer insights into material selection, tooling, and process optimization.
- Quality Control: Ensure the supplier follows strict quality control measures, including certification to industry standards (e.g., ISO 9001) and the use of advanced quality testing tools (e.g., X-ray, CMM inspection).
- Capacity: Consider the supplier’s capacity to handle your volume requirements. This includes machine capabilities, workforce availability, and lead time flexibility.
- Cost: While price is important, it should not be the only deciding factor. Choose a supplier that offers the best balance of cost, quality, and service.
- Customer Support: A good supplier should offer excellent customer service, including clear communication, troubleshooting assistance, and technical support during the design and production phases.
Choosing a supplier with a balance of expertise, quality, and reliability will help ensure the success of your die casting project.
Searching for High-Quality for Cast Aluminum Parts?
You’ve come to the right place! Yongzhu Casting is a certified die casting manufacturer with over 20 years of expertise in the industry.
We have successfully completed numerous die casting projects for Aluminum casting parts, particularly in your industry.
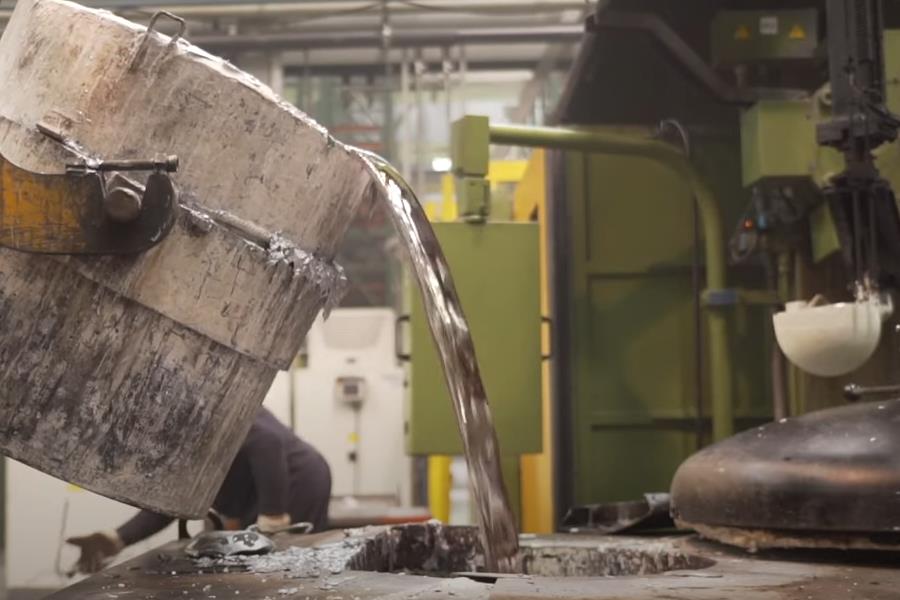
Zhejiang Yongzhu Casting Technology Co., Ltd.
Location: Zhejiang, Shaoxing
Company type: Manufacturing
Year Founded: 2004
Main Products: Aluminium die casting, Mold Making, Die Casting, Sand Casting, Gravity Casting
Leading Chinese producer Yongzhu Casting is formerly known as Hangzhou Higer Metal Products Co., Ltd., was established in 2004.
With 20 years of experience in the industry, we are a specialized manufacturer in Aluminum casting and Machining.
Our products are widely used in various applications such as Automotive, Energy, Lighting, Medical, Home Furnishings, Machinery & Equipment etc. Below is one of our products.
It’s worth mentioning that the evolution of rapid logistics has transformed how industries approach purchasing. Aluminum casting orders can now be sourced from overseas suppliers efficiently.
For instance, working with YONGZHU CASTING, you can inquire, order, and even find better value than your local options—all while maintaining assured quality.
Design Review & DFM Support
Our professionals will evaluate your designs and provide suggestions for cost savings. Additionally, we offer Design for Manufacturing (DFM) assistance and conduct mold flow analyses to facilitate efficient production.
State-of-the-Art Manufacturing Equipment
Our facility is equipped with advanced hot-chamber and cold-chamber die casting machinery for aluminum and zinc production.
We also utilize high-precision CNC machines in a temperature-controlled workshop, featuring 3-Axis, 4-Axis and 5-Axis setups to manage any project you have.
Rigorous Quality Control Measures
Our dedicated quality control team ensures that all parts meet the highest standards of quality and consistency. We employ high-accuracy measurement instruments, including CMM, spectrometers, and X-ray detectors.
Comprehensive Surface Treatment Options
We provide a variety of surface finishing techniques for your precision die casting components. Our in-house services include cleaning, polishing, anodizing, shot blasting, and painting.
Flexible Project Acceptance
While larger manufacturers often shy away from low-volume projects, and smaller ones may struggle with quality, Yongzhu Casting stands apart. We prioritize customer satisfaction and willingly accept high-mix, low-volume projects like yours.

What industries benefit most from die casting?
Die casting is used in a wide range of industries due to its ability to produce durable, high-precision parts. Key industries that benefit from die casting include:
- Automotive: Die casting is widely used to produce lightweight, durable parts for vehicles, such as engine blocks, transmission housings, and wheels.
- Aerospace: The aerospace industry uses die casting for parts requiring high strength-to-weight ratios, such as aircraft components, engine parts, and structural elements.
- Electronics: Die casting is commonly used for enclosures, heat sinks, and other components for consumer electronics, providing both strength and efficient heat dissipation.
- Medical: Medical devices, including housings for diagnostic equipment and surgical instruments, often use die-cast metal parts due to their durability and precision.
- Industrial Machinery: Die casting is used to produce complex parts for industrial machines, including housing, brackets, and structural components that require strength and resistance to wear.
How can die casting improve product performance?
Die casting can improve product performance in various ways:
- Enhanced Durability: The high precision of die casting results in parts with superior mechanical properties, such as strength and wear resistance, which improves product longevity and performance.
- Weight Reduction: By using lightweight metals like aluminum and magnesium, die casting helps reduce the weight of products, improving energy efficiency and performance in applications like automotive and aerospace.
- Heat Dissipation: Die-cast parts, especially those made from metals with high thermal conductivity, such as aluminum, help improve heat dissipation, making them ideal for electronics and other high-heat applications.
- Complex Geometry: Die casting can produce parts with intricate shapes that enhance functionality, such as complex internal cooling channels, which are crucial for improving the performance of machinery and electronics.
By leveraging the benefits of die casting, manufacturers can create products that offer enhanced performance, durability, and efficiency.
What is the impact of die casting on part design?
Die casting offers several advantages when it comes to part design, but there are also some limitations to be aware of:
- Design Flexibility: Die casting allows for complex geometries that might be difficult or expensive to achieve with other manufacturing processes, such as internal cavities, thin walls, and intricate details.
- Dimensional Precision: Die casting produces parts with high dimensional accuracy, often within tolerances of ±0.1 mm, which reduces the need for additional machining and post-processing.
- Material Efficiency: The near-net shape achieved by die casting minimizes material waste and reduces the need for further shaping or trimming.
- Design Constraints: Although die casting can produce complex shapes, parts with very deep sections or undercuts may require special tooling or may be more challenging to cast. It’s important to design with draft angles and considerations for mold release.
Overall, die casting can enable innovative designs while ensuring efficiency, but it’s essential to work closely with the foundry to optimize the design for the process.
What is the difference between hot chamber and cold chamber die casting?
Hot chamber and cold chamber die casting are two different methods of injecting molten metal into molds, each with its own advantages and limitations:
- Hot Chamber Die Casting:
- Process: The metal is injected directly from the furnace into the die through a chamber that is kept at a high temperature.
- Metals Used: Hot chamber die casting is typically used for metals with low melting points, such as zinc, lead, and tin.
- Advantages: Faster cycle times, lower initial investment, and more cost-effective for high-volume production.
- Limitations: The process is limited to low-melting-point metals since the machinery needs to remain molten at high temperatures.
- Cold Chamber Die Casting:
- Process: The molten metal is poured manually or automatically into a cold chamber before being injected into the die.
- Metals Used: Cold chamber die casting is used for metals with higher melting points, such as aluminum, magnesium, and copper alloys.
- Advantages: More versatile, as it can handle a wider range of metals.
- Limitations: Slower cycle times and higher operational costs due to the need for additional equipment to handle the high temperatures.
The choice between the two depends on the material being used and the desired production speed.
Can die casting be used for producing large parts?
Yes, die casting can be used to produce large parts, although there are certain limitations to consider:
- Size Limitations: Die casting is generally more suited for smaller to medium-sized parts due to the size constraints of the die and the need for precise control over the molten metal. For very large parts, the mold design and machinery must be appropriately scaled.
- Material Selection: Larger parts require materials with good flow characteristics to fill the die efficiently. Aluminum and zinc alloys are often used for larger die-cast parts.
- Cost: As the size of the part increases, so do tooling costs. The cost per part may also rise due to the longer cycle times and greater material usage required for large parts.
Die casting can be an effective process for producing large, high-precision parts in industries like automotive, aerospace, and industrial machinery, though considerations for part size and material are crucial.
What role does die casting play in the automotive industry?
Die casting plays a significant role in the automotive industry due to its ability to produce lightweight, durable, and high-precision components. Common applications include:
- Engine Components: Die-cast parts such as engine blocks, cylinder heads, and transmission housings are lightweight and strong, contributing to overall vehicle performance and fuel efficiency.
- Structural Parts: Die-casting is used for producing structural components like cross members, brackets, and mounts that require both strength and precision.
- Interior and Exterior Components: Die casting is used for producing trim pieces, door handles, and other components that require aesthetic and functional properties.
- Electric Vehicles (EVs): The automotive industry’s push toward electric vehicles has led to the increased use of die casting, especially for lightweight battery enclosures and complex heat sinks for electric motors.
Die casting helps reduce the weight of automotive components, improve fuel efficiency, and increase the durability of parts.
How does die casting contribute to the design of heat exchangers?
Die casting contributes to the design and manufacturing of heat exchangers by enabling the production of complex, high-performance components. Benefits include:
- Complex Geometries: Die casting can produce heat exchangers with intricate internal channels and cooling fins, which are difficult to achieve with other manufacturing methods.
- Material Efficiency: The precision of die casting minimizes material waste, and the metal used in die-cast heat exchangers can be recycled, reducing environmental impact.
- Thermal Conductivity: Die-cast materials like aluminum and copper alloys offer excellent thermal conductivity, making them ideal for efficient heat transfer in heat exchangers.
- Strength and Durability: Die-cast heat exchangers are strong, lightweight, and resistant to corrosion, which is essential for their longevity and reliability in HVAC, automotive, and industrial applications.
Overall, die casting enables the efficient production of high-performance heat exchangers with superior thermal properties and design flexibility.
What are the advantages of die casting over other casting methods?
Die casting offers several key advantages over other casting methods, making it a preferred choice for many high-precision applications:
- High Precision: Die casting produces parts with tight tolerances, often within ±0.1 mm, reducing the need for secondary machining processes.
- Faster Cycle Times: Die casting has short cycle times compared to other casting methods like sand casting or permanent mold casting, enabling high-volume production.
- Superior Surface Finish: Die-cast parts typically have a smooth surface finish that requires minimal post-processing, which is ideal for parts that need aesthetic appeal.
- Minimal Waste: Unlike sand casting, which can result in significant material waste, die casting uses minimal material, with excess material being recycled for future use.
- Complex Geometries: Die casting can produce parts with complex shapes and features, such as undercuts, thin walls, and intricate internal channels, that are difficult or expensive to achieve with other methods.
These advantages make die casting a highly efficient and cost-effective solution for producing parts with high precision and volume.
How does die casting affect the environmental impact of manufacturing?
Die casting has several environmental benefits that help reduce its overall impact on manufacturing:
- Material Recycling: Many metals used in die casting, such as aluminum, zinc, and magnesium, are highly recyclable. The process generates minimal waste, and excess material can be melted and reused, significantly reducing the need for new raw materials.
- Reduced Energy Consumption: Die casting is an energy-efficient process compared to other metalworking techniques. With shorter cycle times and precise material use, energy consumption is typically lower.
- Lower Emissions: The efficiency of die casting helps minimize greenhouse gas emissions, as the process reduces material waste and energy usage, contributing to a lower carbon footprint.
- Less Polluting Waste: The waste generated during die casting is primarily scrap metal, which can be easily recycled, unlike some other processes that produce hazardous waste.
By focusing on efficiency, material recycling, and lower emissions, die casting is a more sustainable option in the manufacturing sector.
What factors influence the cost of die casting production?
Several factors influence the cost of die casting production, and understanding these can help in estimating project costs:
- Tooling and Mold Design: The design and complexity of the die or mold play a significant role in initial costs. More intricate designs or larger molds require more time and investment.
- Material Choice: The type of metal used for die casting (e.g., aluminum, zinc, magnesium) impacts the overall cost. Aluminum is typically more expensive than zinc, for example.
- Production Volume: Higher production volumes generally lower the cost per unit due to economies of scale, while lower volumes result in higher per-unit costs.
- Cycle Time: Shorter cycle times lead to faster production rates and can reduce overall costs. Longer cycle times increase labor and energy consumption.
- Part Complexity: More complex parts require specialized tooling and processing, increasing the cost. Simpler parts may have lower tooling and cycle costs.
What are the limitations of die casting?
While die casting offers numerous advantages, it also has some limitations:
- High Initial Tooling Costs: The cost of producing the die or mold is high, making die casting more suitable for high-volume production runs.
- Part Size Limitations: Die casting is generally better suited for small to medium-sized parts. Large parts may require larger and more expensive molds.
- Material Restrictions: Die casting is typically limited to metals with lower melting points, such as aluminum, zinc, and magnesium. It is not suitable for high-melting-point materials like steel.
- Post-Processing: Some parts may require additional finishing, such as machining, painting, or coating, to meet specific requirements.
Despite these limitations, die casting remains a highly efficient and cost-effective process for many applications.
How do die casting alloys compare to traditional casting alloys?
Die casting alloys offer several benefits compared to traditional casting alloys:
- Improved Fluidity: Die casting alloys, such as aluminum and zinc, have better fluidity, allowing them to fill intricate molds more easily, resulting in higher precision and fewer defects.
- Superior Strength: Die casting alloys are often stronger and more durable than traditional alloys, making them suitable for high-stress applications.
- Better Surface Finish: Die casting alloys typically produce smoother surfaces, reducing the need for post-casting finishing processes.
- Higher Density: Die-cast alloys tend to have a higher density, which improves their strength and heat resistance compared to traditional casting alloys.
These properties make die casting alloys ideal for producing lightweight, durable, and precise parts with complex geometries.
How do you determine the best material for a die-cast part?
Selecting the best material for a die-cast part depends on several factors:
- Mechanical Properties: Consider the strength, hardness, and durability required for the part’s intended use. For example, aluminum is often chosen for parts that need to be lightweight but strong.
- Thermal Properties: If the part will be exposed to high temperatures, such as engine components, materials with good heat resistance, such as aluminum or magnesium, may be preferred.
- Corrosion Resistance: In environments where corrosion is a concern, such as automotive or marine applications, materials like aluminum and zinc are often chosen for their resistance to oxidation.
- Cost Considerations: Material cost plays a role in selecting the best option. While aluminum and magnesium alloys may be ideal in terms of performance, they can be more expensive than zinc or lead alloys.
- Environmental Considerations: Sustainability and recyclability may also influence material selection, as metals like aluminum are highly recyclable, reducing environmental impact.
How does die casting compare to sand casting in terms of precision?
Die casting typically offers much higher precision than sand casting. Here’s a comparison:
- Dimensional Accuracy: Die casting can achieve tolerances as tight as ±0.1 mm, while sand casting typically has tolerances around ±0.5 mm to ±1.0 mm.
- Surface Finish: Die casting provides a smooth surface finish, often requiring no additional machining, while sand casting typically has a rougher surface that requires additional post-processing.
- Cycle Time: Die casting has much faster cycle times, typically around 30-60 seconds per cycle, while sand casting requires longer cycle times due to the need for mold cooling and curing.
Overall, die casting is a more precise and efficient method for high-volume production, while sand casting is better suited for larger, less intricate parts.
What are the common defects in die casting and how can they be avoided?
Common die casting defects include:
- Porosity: Small voids or bubbles in the cast material, often caused by trapped air or gas during the casting process. To avoid porosity, it’s important to maintain proper venting, use vacuum-assisted die casting, and control the cooling rate.
- Cold Shut: This occurs when molten metal fails to fill the die cavity completely, resulting in a weak spot. It can be avoided by improving the metal flow, increasing the pressure, or adjusting the gating system.
- Flash: Excess metal that leaks out of the die cavity, often due to excessive pressure or poor mold alignment. Flash can be minimized by improving die maintenance and ensuring precise mold alignment.
- Misruns: Incomplete filling of the mold, typically due to insufficient injection pressure or improper metal temperature. Maintaining optimal metal temperature and injection speed can help avoid misruns.
Proper die design, regular maintenance, and optimized process control are essential to minimizing defects.
What is the role of the die in die casting?
The die plays a critical role in the die casting process, acting as the mold into which molten metal is injected. Here are its functions:
- Shape and Design: The die determines the final shape, size, and surface finish of the cast part. Its design must account for the flow of molten metal, cooling, and ejection.
- Material Selection: The die must be made from materials that can withstand the high temperatures and pressures of the casting process. Tool steels or heat-treated alloys are commonly used.
- Cycle Efficiency: The die is designed to minimize cycle time and maximize production efficiency. Proper die cooling and ejection mechanisms reduce the overall cycle time and improve part consistency.
The die is key to ensuring precision and high-quality parts, making its design and maintenance critical to a successful die casting process.
How does die casting improve part durability?
Die casting improves the durability of parts in several ways:
- Strong and Dense Material: Die-cast parts are produced under high pressure, which compacts the material and creates a dense, strong structure. This helps parts resist wear and impact.
- Alloy Properties: Die-casting alloys like aluminum, zinc, and magnesium offer superior mechanical properties such as high strength-to-weight ratios, corrosion resistance, and high thermal conductivity.
- Consistency: The precision of die casting ensures uniform material distribution, reducing the risk of weak spots in the part, which could otherwise lead to early failure.
As a result, die-cast parts are typically more durable than parts produced by other casting methods.
Can die casting be used for electrical components?
Yes, die casting is frequently used for producing electrical components. Common applications include:
- Electrical Enclosures: Die-cast aluminum and zinc are often used for electrical housings because they offer high strength, excellent corrosion resistance, and the ability to shield electrical equipment from electromagnetic interference (EMI).
- Connectors: Die-casting produces precise electrical connectors, ensuring reliable conductivity and durability.
- Heat Sinks: Die-cast parts are used for heat sinks due to their excellent thermal conductivity, especially in aluminum and copper alloys.
The combination of high precision, material properties, and efficient production makes die casting an ideal choice for electrical components.
What is the difference between die casting and injection molding?
While both die casting and injection molding involve injecting molten material into a mold, there are key differences:
- Material: Die casting is typically used for metals like aluminum, zinc, and magnesium, while injection molding is used for plastics.
- Pressure and Temperature: Die casting requires high pressure and high temperatures to melt and inject metals, while injection molding uses lower pressure and temperature for melting plastics.
- Cycle Time: Die casting typically has shorter cycle times for smaller parts, while injection molding may have longer cycles depending on the material and part complexity.
- Strength and Durability: Die-cast parts are stronger and more durable than injection-molded plastic parts, making them suitable for load-bearing applications.
Die casting is preferred for metal parts requiring high strength and precision, while injection molding is ideal for high-volume plastic parts.
What are the benefits of using aluminum in die casting?
Aluminum is one of the most popular metals used in die casting due to its numerous advantages:
- Lightweight: Aluminum has a low density, making it ideal for applications where weight reduction is important, such as automotive and aerospace industries.
- Strength-to-Weight Ratio: Despite being lightweight, aluminum offers a high strength-to-weight ratio, providing durability while keeping the overall weight low.
- Corrosion Resistance: Aluminum naturally forms a protective oxide layer, making it highly resistant to corrosion and ideal for outdoor and marine applications.
- Thermal Conductivity: Aluminum is an excellent conductor of heat, making it suitable for heat exchange and cooling applications.
- Recyclability: Aluminum is 100% recyclable, reducing the environmental impact and supporting sustainability.
These properties make aluminum an excellent choice for a wide range of die-cast parts, from automotive to electronics.
How do you optimize die casting for high-volume production?
To optimize die casting for high-volume production, consider the following:
- Tooling Design: Use high-quality, durable molds that can withstand high-pressure injections and high temperatures without wear. Optimizing the mold design for efficient metal flow reduces cycle times and costs.
- Automation: Implement automated systems for metal pouring, die ejection, and part inspection to reduce labor costs and increase consistency.
- Material Efficiency: Use die-cast alloys that have good fluidity and low shrinkage rates, minimizing material waste and reducing the need for secondary operations.
- Cycle Time Optimization: Fine-tune parameters such as injection speed, pressure, and cooling time to reduce cycle time while maintaining part quality.
- Quality Control: Integrate in-line inspection systems to ensure that each part meets quality standards, reducing the risk of defects and rework.
By optimizing these factors, die casting can be made more cost-effective for high-volume production.
What are the challenges of die casting in the aerospace industry?
The aerospace industry presents unique challenges for die casting, including:
- Material Requirements: Aerospace parts require materials that can withstand extreme temperatures, pressures, and stresses. Die casting alloys like aluminum and magnesium are commonly used, but special alloys may be needed for specific applications.
- Precision and Tolerances: The need for high precision in aerospace components is critical, and even minor defects can compromise safety. Achieving tight tolerances requires advanced die casting techniques and stringent quality control.
- Lightweight: Reducing weight while maintaining strength is a key challenge in aerospace manufacturing. Die casting offers solutions by producing lightweight yet strong parts, but careful material selection and design optimization are crucial.
- Regulatory Compliance: Aerospace components must meet strict regulatory standards for safety and performance, which adds complexity to the die casting process.
Despite these challenges, die casting remains a valuable method for producing high-precision, lightweight parts for the aerospace industry.
How does die casting support sustainability in manufacturing?
Die casting contributes to sustainability in several ways:
- Material Recycling: Metals like aluminum, zinc, and magnesium used in die casting can be recycled, reducing the need for new raw materials and conserving natural resources.
- Energy Efficiency: Die casting has shorter cycle times compared to other metalworking processes, leading to lower energy consumption per part.
- Reduced Material Waste: The precision of die casting ensures minimal waste, as excess metal can be reused and scrap can be melted down for future use.
- Durability: Die-cast parts are strong and durable, leading to longer product lifespans, which reduces the need for replacements and contributes to the overall sustainability of products.
By improving efficiency and reducing waste, die casting can be a more sustainable manufacturing process.
Can die casting be used for medical device manufacturing?
Yes, die casting is used in the manufacturing of medical devices, particularly for components that require high precision, strength, and durability. Common applications include:
- Surgical Instruments: Die-cast components are used in surgical tools that require high precision and strength.
- Medical Enclosures: Die casting is used to produce durable enclosures for medical devices such as diagnostic machines, sensors, and pacemakers.
- Precision Parts: Die-cast parts such as valves, handles, and housings are commonly used in medical devices for their durability, precision, and corrosion resistance.
The high quality and precision of die casting make it an ideal choice for medical device manufacturing, where safety and performance are critical.
How does die casting contribute to the automotive industry’s lightweighting goals?
Die casting significantly contributes to the automotive industry’s lightweighting efforts:
- Material Choice: Aluminum and magnesium alloys, commonly used in die casting, are much lighter than steel, which reduces the overall weight of automotive components.
- Structural Efficiency: Die casting enables the creation of complex, high-strength parts with minimal material usage, helping to reduce vehicle weight without compromising safety or performance.
- Fuel Efficiency: By reducing the weight of key automotive components, such as engine blocks, transmission cases, and body panels, die-cast parts contribute to improved fuel efficiency and lower CO2 emissions.
For example, switching from a steel to an aluminum die-cast component can reduce weight by up to 50%, leading to more fuel-efficient vehicles.
How does die casting help with complex part geometries?
Die casting allows for the production of highly complex geometries that are difficult or impossible to achieve with other methods:
- Design Flexibility: Die casting molds can accommodate intricate designs, such as thin walls, internal cavities, and fine details, which can eliminate the need for additional machining.
- Reduced Secondary Operations: Complex geometries can often be cast without the need for additional processing, such as milling or drilling, reducing production time and cost.
- Precision: The high-pressure injection process ensures that molten metal fills every corner of the mold, creating parts with precise dimensions and intricate features.
This capability is essential in industries such as automotive, aerospace, and electronics, where high precision and complex shapes are often required.
How does die casting improve the overall cost-effectiveness of manufacturing?
Die casting offers several advantages that help improve cost-effectiveness:
- High Production Speed: The die casting process is capable of producing large quantities of parts quickly, reducing the cost per part in high-volume runs.
- Minimal Waste: The precise control over material flow ensures minimal waste, reducing material costs and improving yield.
- Reduced Labor Costs: The automation of die casting processes, including metal injection, cooling, and ejection, reduces the need for manual labor, driving down overall production costs.
- Less Post-Processing: Due to the high accuracy of die casting, many parts require little or no additional finishing, reducing post-processing costs.
Overall, die casting is a highly cost-effective method for manufacturing precision parts in high volumes.
What are the key factors affecting the lifespan of a die casting mold?
The lifespan of a die casting mold depends on several factors:
- Material Selection: Molds made from high-quality, heat-treated steel or alloys last longer than those made from lower-grade materials. Tool steels like H13 or A2 are common for high-performance molds.
- Temperature and Pressure: High temperatures and injection pressures can lead to mold wear over time. Optimizing the cooling rate and injection process can help prolong the mold’s life.
- Maintenance: Regular maintenance, including cleaning, polishing, and checking for wear, helps extend the life of the mold.
- Design: The design of the mold, including proper venting and cooling channels, can impact how well the mold handles thermal stresses and pressure, affecting its lifespan.
Typical mold life for die casting can range from 100,000 to 1 million cycles, depending on the factors above.
How does die casting contribute to reduced material waste in manufacturing?
Die casting significantly reduces material waste compared to other manufacturing methods:
- Near-Net Shape: The high precision of die casting ensures that parts are produced close to their final shape, minimizing the need for extensive machining, which reduces material loss.
- Recyclable Materials: Metal scrap generated during the die casting process, including sprue, runners, and gates, can be recycled and reused in the next production cycle, reducing overall waste.
- Efficient Material Usage: Die casting uses a fixed amount of material for each part, and due to the precision of the process, very little excess material is generated.
By reducing waste, die casting not only helps cut costs but also contributes to more sustainable manufacturing.
Can die casting be used for high-temperature applications?
Yes, die casting can be used for high-temperature applications, depending on the material:
- Material Selection: Certain die-casting alloys, such as aluminum, zinc, and magnesium, have good thermal resistance, while others, like copper and brass alloys, can withstand even higher temperatures.
- Heat Treatment: Parts cast from heat-resistant alloys can undergo heat treatments to further enhance their thermal stability, making them suitable for high-temperature environments.
- Applications: Die-cast parts used in high-temperature applications include engine components, turbine blades, heat exchangers, and industrial machinery.
By selecting the appropriate alloy and incorporating heat treatment processes, die-cast parts can be used reliably in high-temperature settings.
How can die casting improve the performance of automotive engine components?
Die casting enhances the performance of automotive engine components by offering:
- Improved Strength-to-Weight Ratio: Aluminum and magnesium die-cast engine components are lighter than their steel counterparts while maintaining or even improving strength, which helps reduce the overall vehicle weight and improve fuel efficiency.
- Precision: Die casting allows for highly precise, complex engine parts with minimal variation, ensuring reliable performance in high-stress environments.
- Heat Resistance: Certain die-cast alloys, particularly aluminum, are designed to withstand high operating temperatures, which is crucial for engine parts that are exposed to extreme heat.
- Corrosion Resistance: Aluminum’s natural resistance to corrosion enhances the longevity and performance of engine components.
These benefits make die casting a favored method for producing components like engine blocks, cylinder heads, and transmission housings.
How can die casting be used for electronic components?
Die casting is commonly used to manufacture electronic components for several reasons:
- Precision: Die-cast parts can be produced with tight tolerances and complex geometries, which is crucial for electronic components like connectors, housings, and heat sinks.
- Thermal Management: Materials like aluminum, often used in die casting, have excellent thermal conductivity, which is critical for managing the heat generated by electronic devices.
- Shielding: Die-cast metals, such as zinc and aluminum, can provide electromagnetic interference (EMI) shielding, which is important for many electronic applications, such as computer components and communication devices.
- Durability: Die-cast components are strong, lightweight, and resistant to corrosion, making them ideal for use in electronics that need to withstand environmental factors.
Die casting ensures the high quality and durability required for electronic components, including housings, connectors, and enclosures.
What role does die casting play in the renewable energy industry?
Die casting is an essential part of the renewable energy industry by enabling the production of high-performance parts used in renewable energy systems:
- Wind Turbine Components: Die-cast aluminum parts are used in wind turbines for components like housings, gearboxes, and connectors, helping to reduce weight and improve efficiency.
- Solar Energy Systems: Die casting is used to produce lightweight, durable parts for solar panels, inverters, and mounting systems, ensuring optimal performance in harsh environmental conditions.
- Energy Storage: Die-cast parts are used in energy storage systems, such as batteries and power inverters, where strength, durability, and heat resistance are crucial.
- Corrosion Resistance: The corrosion-resistant properties of aluminum and zinc alloys make die-cast parts ideal for use in outdoor renewable energy applications.
By enabling the production of durable, lightweight, and efficient components, die casting plays a significant role in the renewable energy industry.
How do different die casting alloys impact product quality?
The choice of die casting alloy has a significant impact on the product’s overall quality:
- Aluminum Alloys: Aluminum is lightweight, corrosion-resistant, and has good thermal and electrical conductivity, making it ideal for automotive, aerospace, and electronics applications.
- Zinc Alloys: Zinc offers superior strength, durability, and excellent casting flow properties, ideal for precise, high-volume parts like gears, locks, and connectors.
- Magnesium Alloys: Magnesium alloys are the lightest of all die-casting metals and are used in automotive and aerospace applications where weight reduction is crucial.
- Copper Alloys: Copper die castings provide excellent thermal and electrical conductivity, making them ideal for use in electrical components and heat exchangers.
Each alloy has unique properties that make it suited to specific applications, affecting factors like strength, durability, corrosion resistance, and heat conductivity.
What is the role of die casting in reducing production time and cost?
Die casting offers several benefits that reduce production time and cost:
- High-Speed Production: Die casting can produce parts quickly, especially in high-volume production runs, due to the rapid injection of molten metal into the mold.
- Minimal Post-Processing: Parts produced through die casting often require little to no post-processing, such as machining or polishing, because they are already close to the desired final shape.
- Reduced Material Waste: Die casting is highly efficient in terms of material usage, as there is minimal scrap generated during the process. Materials such as zinc and aluminum can be recycled within the same production cycle.
- Automation: The die casting process can be automated, which reduces labor costs and increases production consistency.
These advantages significantly cut down the time and cost involved in producing high-quality parts.
How does die casting impact the surface finish of parts?
The surface finish of die-cast parts is influenced by several factors:
- Mold Quality: A high-quality mold with a smooth surface will produce parts with a better finish. Molds are often polished to reduce surface imperfections.
- Alloy Selection: The choice of material impacts the surface finish. For instance, aluminum provides a smoother finish than magnesium, while zinc alloys are typically smoother and require less post-processing.
- Injection Pressure: High injection pressures result in a finer, smoother finish because they force the molten metal to fill every detail of the mold, minimizing surface defects.
- Cooling Rate: Faster cooling times can reduce the likelihood of shrinkage marks, resulting in a better surface finish.
In general, die-cast parts can have excellent surface finishes that require minimal post-processing, making the process highly efficient for high-quality products.
How does die casting compare to injection molding in terms of material options?
Die casting and injection molding both have their advantages in terms of material options:
- Die Casting: Typically used with metals such as aluminum, zinc, magnesium, and copper alloys. These metals offer strength, durability, and resistance to high temperatures, making die casting ideal for industries like automotive and aerospace.
- Injection Molding: Generally used with plastics, including thermoplastics and thermosets, which are lightweight and have good insulation properties but lack the strength and heat resistance of metals.
- Material Limitations: Die casting allows for the production of parts that require higher strength and heat resistance, whereas injection molding is better suited for products requiring flexibility, electrical insulation, or lightweight properties.
Thus, die casting is more suitable for applications requiring strong, durable, and heat-resistant materials, while injection molding is ideal for plastic parts with specific performance requirements.
What are the key advantages of die casting for the aerospace industry?
Die casting offers several advantages to the aerospace industry:
- Lightweight Components: Aluminum and magnesium die castings reduce the overall weight of aircraft, improving fuel efficiency and performance.
- Precision and Complexity: Die casting allows for the creation of complex parts with high precision, which is crucial for aerospace components like brackets, housings, and engine parts.
- Corrosion Resistance: Die-cast aluminum and magnesium parts are resistant to corrosion, making them ideal for the harsh conditions found in aerospace applications.
- High Strength-to-Weight Ratio: Die-cast components can withstand high stress and pressure without adding excessive weight to the aircraft, which is vital for both structural and non-structural parts.
These advantages make die casting an ideal manufacturing process for producing critical aerospace parts.
How does die casting help in producing parts with thin walls?
Die casting is particularly well-suited for producing parts with thin walls:
- High Pressure: The high pressure used in die casting forces molten metal into intricate, detailed molds, allowing for the creation of thin-walled parts with precision.
- Material Flow: The process ensures that the molten material flows evenly throughout the mold, filling thin sections without leaving voids or defects.
- Alloy Selection: Certain alloys, such as aluminum and zinc, have excellent fluidity, which allows them to fill thin sections of the mold with ease.
- Reduced Material Use: Thin-walled parts reduce material usage, making the process more cost-effective and environmentally friendly.
This ability to produce thin-walled parts is particularly useful in industries such as automotive and electronics, where lightweight and efficient designs are crucial.
What types of finishes can be achieved with die-cast parts?
Die-cast parts can be finished in various ways to achieve different surface qualities:
- Polished: Die-cast parts can be polished to a mirror-like finish, which is particularly useful for aesthetic applications or parts that require high precision and smooth surfaces.
- Painted or Powder Coated: Parts can be painted or powder-coated for additional protection, aesthetics, or to achieve specific colors.
- Anodized: Aluminum die-cast parts can undergo anodization, which enhances corrosion resistance while providing a durable and attractive finish.
- Shot Blasting: Shot blasting can be used to create a matte or textured finish on die-cast parts, commonly used in industrial applications.
These finishes allow manufacturers to tailor the final appearance and functionality of parts to specific requirements.
What are the environmental benefits of die casting?
Die casting offers several environmental benefits:
- Material Recycling: The metals used in die casting, such as aluminum, zinc, and magnesium, are highly recyclable. Scrap from the die casting process can be reused in subsequent cycles, reducing the need for virgin materials.
- Energy Efficiency: Die casting processes, especially when using efficient machines, consume less energy compared to traditional casting methods.
- Reduced Waste: The precision of die casting reduces material waste. Parts are produced close to their final shape, requiring minimal machining and thus reducing scrap.
- Long-Lasting Components: The durability and strength of die-cast parts ensure that products have a long lifecycle, contributing to reduced waste in the long term.
As a result, die casting is considered an environmentally friendly manufacturing process due to its energy efficiency, material reuse, and waste reduction.
How can die casting improve product strength and durability?
Die casting improves product strength and durability through:
- High-Pressure Injection: The molten metal is injected at high pressures into the mold, ensuring that the metal fills every crevice and solidifies with minimal air pockets, resulting in a strong, dense part.
- Alloy Selection: The choice of alloy plays a critical role in the strength and durability of die-cast products. For example, aluminum alloys offer a good balance of strength, lightweight, and corrosion resistance, while zinc alloys provide high strength and hardness.
- Controlled Cooling: The rapid cooling of the molten metal ensures that the parts retain their shape and strength once solidified, reducing the likelihood of defects like warping or cracking.
- Reduced Porosity: The high pressure and fast cooling rates reduce porosity in die-cast parts, leading to stronger, more durable components.
These factors result in highly durable parts that can withstand mechanical stresses, thermal cycling, and environmental factors.
Can die casting be used for prototypes or low-volume production?
Yes, die casting can be used for both prototypes and low-volume production:
- Prototyping: Die casting allows for the production of high-quality prototype parts that closely resemble the final design, enabling manufacturers to test fit, function, and form before scaling to mass production.
- Low-Volume Production: Although die casting is typically used for high-volume runs, it is also suitable for low-volume production when molds are designed for multiple uses. This can help reduce the cost per part in low-volume manufacturing.
- Rapid Turnaround: With advancements in 3D printing and rapid prototyping, the lead time for creating die-casting molds has decreased, making the process viable for prototype and short-run production.
Die casting is versatile enough to accommodate both large-scale and small-scale production needs, making it a valuable option for manufacturers at all stages of product development.
How does die casting affect the dimensional accuracy of parts?
Die casting offers high levels of dimensional accuracy, making it suitable for applications where precision is critical:
- High Injection Pressure: The high pressure used in the die casting process ensures that molten metal fills the mold completely, producing parts with tight tolerances and consistent dimensions.
- Mold Precision: The molds used in die casting are made to precise specifications, which ensures that parts maintain their accuracy throughout production.
- Low Shrinkage: Compared to other casting methods, die casting has low shrinkage rates, which helps maintain the shape and dimensions of the part as it cools.
- Repeatability: Die casting is highly repeatable, making it ideal for large-volume production where consistent dimensional accuracy is required.
This precision ensures that die-cast parts meet the stringent requirements of industries such as automotive, aerospace, and electronics.
What is the typical cycle time for die casting?
The cycle time for die casting varies depending on factors such as the complexity of the part and the material used:
- Simple Parts: For simple components, cycle times can range from 15 to 60 seconds, as the injection and cooling processes are faster for parts with less complexity.
- Complex Parts: More intricate components, especially those with thin walls or large surface areas, may have cycle times of up to 2-3 minutes due to the need for longer cooling times.
- Material Influence: The type of material also influences cycle time. Aluminum and zinc alloys generally cool faster than magnesium alloys, which can extend cycle times.
- Automation: Automation in die casting can further reduce cycle times by streamlining the loading, injection, and cooling processes.
Overall, the cycle time for die casting is relatively short compared to other manufacturing methods, allowing for high-volume production in a short period.
How does die casting contribute to cost savings in manufacturing?
Die casting can significantly reduce manufacturing costs:
- Reduced Waste: The high precision of die casting minimizes material waste. Parts are produced to near-final shapes, reducing the need for extensive post-processing or machining.
- High Production Speed: The speed at which die casting operates, particularly in high-volume runs, allows manufacturers to produce large quantities of parts in a short time, lowering the cost per part.
- Tool Longevity: High-quality molds used in die casting can last for thousands of cycles, spreading the initial tooling cost over a large number of parts.
- Reduced Labor Costs: The automation potential in die casting reduces labor requirements compared to more labor-intensive manufacturing methods.
These factors combine to make die casting a cost-effective solution for producing high-quality parts in large volumes.
How does die casting compare to sand casting in terms of material properties?
Die casting and sand casting are both metal casting methods, but they differ in the material properties they produce:
- Die Casting: Die casting produces parts with high density, fine grain structures, and superior mechanical properties due to the high pressure and rapid cooling. This makes die-cast parts stronger, with a more consistent surface finish.
- Sand Casting: Sand casting results in coarser grain structures, which can result in weaker mechanical properties compared to die casting. It also requires more post-processing to achieve a smoother finish.
- Material Efficiency: Die casting has better material efficiency, as there is less waste, while sand casting often requires more material due to the less precise mold.
- Tolerances: Die casting offers better dimensional accuracy and tighter tolerances than sand casting, which makes it ideal for parts requiring high precision.
While both methods are used for metal casting, die casting provides superior material properties, precision, and surface finish.
What industries benefit most from die casting?
Several industries rely on die casting for its ability to produce high-quality, cost-effective parts:
- Automotive: Die casting is widely used in the automotive industry for producing engine components, transmission parts, wheels, and housings, where high strength and lightweight properties are essential.
- Aerospace: Aerospace companies use die casting for parts that require precision and high strength, such as brackets, housings, and structural components.
- Electronics: The electronics industry uses die casting to manufacture heat sinks, casings, and connectors, where thermal conductivity and electrical conductivity are crucial.
- Medical: Die casting is also used to produce medical devices and equipment parts that require durability, precision, and sterilizability.
- Consumer Goods: Die-cast components are found in products like household appliances, power tools, and outdoor equipment due to their strength and functionality.
These industries benefit from die casting’s ability to produce complex, durable parts quickly and cost-effectively.
What is the difference between cold chamber and hot chamber die casting?
Cold chamber and hot chamber die casting are two different types of die casting processes, each suited for different applications:
- Cold Chamber Die Casting: In this process, molten metal is ladled into the chamber manually before being injected into the mold. It is typically used for metals with higher melting points, such as aluminum and magnesium.
- Pros: Suitable for high-melting-point metals; allows for precise control of injection.
- Cons: Slower than hot chamber die casting due to the manual feeding of molten metal.
- Hot Chamber Die Casting: In this process, the injection mechanism is submerged in the molten metal, allowing for continuous injection. It is typically used for metals with lower melting points, such as zinc and lead.
- Pros: Faster production rates; ideal for low-melting-point metals.
- Cons: Not suitable for high-melting-point alloys due to the risk of damage to the machine.
The key difference lies in the method of introducing molten metal into the chamber and the types of metals that can be used.
How can die casting improve part strength without increasing weight?
Die casting allows for the production of strong, lightweight parts through several methods:
- Material Selection: Lightweight alloys such as aluminum and magnesium provide excellent strength-to-weight ratios while maintaining durability.
- Thin-Walled Design: Die casting enables the creation of parts with thin walls, reducing weight without sacrificing strength.
- Hollow Structures: Parts can be designed with internal cavities or hollow sections, further reducing weight while maintaining structural integrity.
- Grain Structure: The rapid cooling of molten metal in the die results in a fine-grain structure, which increases the strength of the part without adding excess material.
These methods allow manufacturers to create strong parts that are both lightweight and durable, making die casting ideal for industries such as automotive and aerospace.
What is the role of venting in the die casting process?
Venting is a crucial step in the die casting process that ensures the smooth flow of molten metal into the mold and prevents defects:
- Air Expulsion: Vents allow trapped air or gas to escape from the mold during the injection process, preventing air pockets, gas porosity, or surface defects.
- Improved Mold Fill: Proper venting ensures that the molten metal fills the mold completely without causing air voids, leading to better part quality.
- Reduced Defects: Without proper venting, die-cast parts can suffer from issues like porosity, surface imperfections, or incomplete filling of the mold.
- Optimizing Efficiency: Effective venting also reduces the chances of material waste and helps maintain the mold’s integrity during production.
Proper venting is essential for achieving high-quality die-cast parts that meet dimensional and mechanical specifications.
How does die casting contribute to product design flexibility?
Die casting offers significant flexibility in product design:
- Complex Geometries: Die casting allows for the production of intricate and complex shapes that would be difficult or costly to achieve with other manufacturing processes, such as machining.
- Customization: Designers can tailor die-cast parts to meet specific functional and aesthetic requirements, including the integration of features like threads, inserts, and textured surfaces.
- Thin Walls: Die casting allows for the creation of thin-walled parts, reducing material usage while still achieving the necessary strength and durability.
- Variety of Materials: Die casting supports a wide range of metals, including aluminum, zinc, and magnesium, offering flexibility in selecting the best material for the desired properties.
This flexibility makes die casting an ideal choice for industries that require both functional and design flexibility in their parts.
How does die casting help with reducing production time in large-volume manufacturing?
Die casting significantly reduces production time for large-volume manufacturing:
- Fast Cycle Times: Die casting processes have fast cycle times, especially for high-volume runs, allowing manufacturers to produce large quantities of parts quickly.
- Automation: The process can be fully automated, speeding up production while ensuring consistent quality and reducing labor costs.
- Reduced Post-Processing: Die-cast parts typically require minimal post-processing, which further shortens production time.
- High-Precision Molds: Die casting uses precise molds, reducing the need for additional machining or adjustments during production.
These factors enable manufacturers to meet high-demand production schedules while maintaining cost efficiency and quality.