Hot plating is a specialized technique that applies a metal coating to a base material by immersing it in a molten metal bath.
This process is critical for enhancing the durability, conductivity, and resistance of various components, including those used in medical humidifiers.
By creating a robust and uniform bond, hot plating significantly extends the lifespan and functionality of components, making it a preferred choice in industries where performance and precision are paramount.
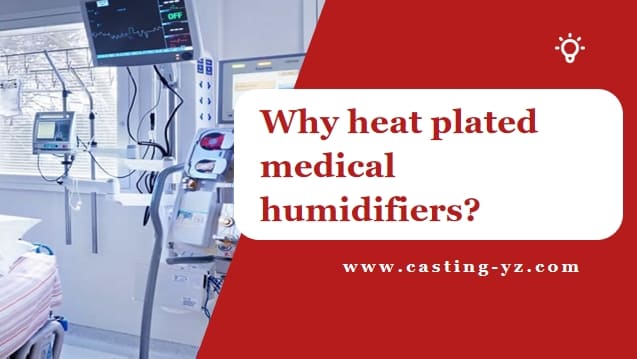
Why Hot Plating Matters in Medical Applications
Hot plating provides several advantages that make it indispensable for medical devices:
- It improves wear resistance, preventing damage from continuous use.
- It enhances corrosion resistance, crucial for humidifiers operating in moist environments.
- A smoother surface finish ensures easier cleaning and sterilization.
- For electrically active parts, hot plating increases conductivity, boosting efficiency.
Medical humidifiers, vital for patient care, rely on precision-manufactured components. Hot plating enhances these parts’ durability, ensuring consistent performance even in demanding settings.
The Hot Plating Process Explained
Hot plating involves several meticulous steps to ensure high-quality results:
- Surface Preparation
The base metal, often aluminum or stainless steel, is thoroughly cleaned to remove impurities. Proper cleaning ensures better adhesion of the plating material. - Material Selection
Molten metal baths may include zinc for corrosion resistance, nickel for hardness, or copper for conductivity. The choice depends on the component’s intended application. - Immersion
The component is dipped into the molten metal bath. Precise timing and temperature control are essential to achieve a uniform coating. - Cooling
After plating, the component is carefully cooled, solidifying the coating and ensuring it adheres properly. - Inspection and Finishing
Each part undergoes rigorous quality checks. Any necessary post-treatment, such as polishing or additional coatings, is applied to enhance the surface finish.
Searching for High-Quality for Cast Aluminum Parts?
You’ve come to the right place! Yongzhu Casting is a certified die casting manufacturer with over 20 years of expertise in the industry.
We have successfully completed numerous die casting projects for Aluminum casting parts, particularly in your industry.

Zhejiang Yongzhu Casting Technology Co., Ltd.
Location: Zhejiang, Shaoxing
Company type: Manufacturing
Year Founded: 2004
Main Products: Aluminium die casting, Mold Making, Die Casting, Sand Casting, Gravity Casting
Leading Chinese producer Yongzhu Casting is formerly known as Hangzhou Higer Metal Products Co., Ltd., was established in 2004.
With 20 years of experience in the industry, we are a specialized manufacturer in Aluminum casting and Machining.
Our products are widely used in various applications such as Automotive, Energy, Lighting, Medical, Home Furnishings, Machinery & Equipment etc. Below is one of our products.
It’s worth mentioning that the evolution of rapid logistics has transformed how industries approach purchasing. Aluminum casting orders can now be sourced from overseas suppliers efficiently.
For instance, working with YONGZHU CASTING, you can inquire, order, and even find better value than your local options—all while maintaining assured quality.
Design Review & DFM Support
Our professionals will evaluate your designs and provide suggestions for cost savings. Additionally, we offer Design for Manufacturing (DFM) assistance and conduct mold flow analyses to facilitate efficient production.
State-of-the-Art Manufacturing Equipment
Our facility is equipped with advanced hot-chamber and cold-chamber die casting machinery for aluminum and zinc production.
We also utilize high-precision CNC machines in a temperature-controlled workshop, featuring 3-Axis, 4-Axis and 5-Axis setups to manage any project you have.
Rigorous Quality Control Measures
Our dedicated quality control team ensures that all parts meet the highest standards of quality and consistency. We employ high-accuracy measurement instruments, including CMM, spectrometers, and X-ray detectors.
Comprehensive Surface Treatment Options
We provide a variety of surface finishing techniques for your precision die casting components. Our in-house services include cleaning, polishing, anodizing, shot blasting, and painting.
Flexible Project Acceptance
While larger manufacturers often shy away from low-volume projects, and smaller ones may struggle with quality, Yongzhu Casting stands apart. We prioritize customer satisfaction and willingly accept high-mix, low-volume projects like yours.

Key Materials for Hot Plating in Medical Devices
Material | Advantages | Applications |
---|---|---|
Zinc | Affordable, excellent corrosion resistance | External humidifier components |
Nickel | Hard, durable, superior resistance | Internal mechanisms |
Copper | High conductivity, efficient heat transfer | Electrical heating elements |
Stainless Steel | Strong, rust-resistant | Structural parts |
Chrome | Aesthetic, smooth finish | Visible parts in premium devices |
Additional Features for Medical Humidifiers
Medical humidifiers benefit from advanced features enabled by hot plating:
- Thermostat Control: Precisely regulates temperature for consistent steam production.
- Anti-Spill Design: Reduces risks associated with water overflow.
- Antimicrobial Coatings: Enhances hygiene and reduces contamination risks.
These features, combined with hot plating’s benefits, make humidifiers more efficient and reliable for medical use.
Applications of Hot Plating Beyond Medical Devices
Hot plating is not limited to medical applications. Its versatility spans various industries:
- Electronics: Improves conductivity in connectors and circuit boards.
- Automotive: Enhances durability in engine components and heat exchangers.
- Aerospace: Provides corrosion resistance for aircraft parts exposed to extreme conditions.
- Industrial Equipment: Strengthens tools and machinery components for longer service life.
FAQs
1. What is hot plating, and why is it essential?
Hot plating involves coating components with a molten metal layer, enhancing durability and performance.
2. What materials are used for hot plating in medical devices?
Zinc, nickel, copper, and chrome are commonly used for their corrosion resistance and conductivity.
3. Can hot plating improve electrical conductivity?
Yes, metals like copper significantly enhance electrical conductivity in components.
4. Why is nickel commonly used in hot plating?
Nickel provides exceptional corrosion resistance and hardness, making it ideal for critical applications.
5. What are the advantages of hot plating over other surface treatments?
Hot plating offers better adhesion, longer-lasting durability, and improved electrical properties compared to paint or anodizing.
6. Is hot plating suitable for all metals?
It works best with aluminum, stainless steel, and copper-based alloys due to their compatibility with molten metal baths.
7. How does hot plating enhance medical humidifiers?
It improves heat distribution, corrosion resistance, and overall reliability of key components.
8. What safety measures are required in the hot plating process?
Proper ventilation, protective equipment, and adherence to environmental regulations are essential for safe operations.
9. How does hot plating compare to powder coating?
Hot plating forms a bonded metallic layer, while powder coating provides a durable surface finish.
10. What makes Yongzhu Casting a trusted partner for hot plating?
Our advanced technology, experienced team, and commitment to quality ensure optimal results for every project.
Conclusion
Hot plating has emerged as a critical process for ensuring the durability, functionality, and safety of components in various industries, especially in medical devices like humidifiers.
By enhancing wear resistance, improving surface quality, and boosting conductivity, it addresses the key challenges of modern manufacturing.
At Yongzhu Casting, we specialize in providing high-quality hot plating services tailored to meet specific project requirements.
Our expertise ensures reliable, long-lasting components for medical, industrial, and other applications. Contact us today to explore how our solutions can support your manufacturing goals.