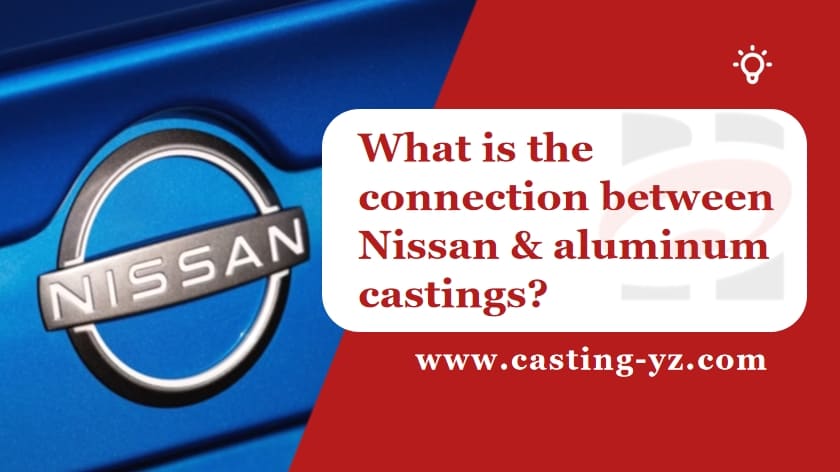
When did Nissan originate?
Founded in 1933 as a textile machinery parts maker, Nissan (then Tobata Casting) pivoted to automobiles with the 1935 Datsun 12.
This pioneering vehicle introduced aluminum die-casting to mainstream car manufacturing, its engine piston weighing 37% less than steel alternatives.
During WWII, Nissan’s expertise expanded secretly to aircraft components, a legacy preserved today at its Yokohama headquarters museum where visitors can view wartime aluminum artifacts.
How Nissan Saves $1,628 Per Car Using Precision Die-Casting?
The Sylphy sedan, Nissan’s global bestseller, epitomizes mass-market innovation. In 2024 alone, 623,000 units found homes worldwide – one every 51 seconds.
Each Sylphy integrates 89 aluminum die-cast parts, including precision-engineered ADC12 alloy engine mounts that withstand 12G vibration loads.
Meanwhile, the GT-R supercar remains Nissan’s technical flagship. Its hand-assembled VR38DETT engine uses vacuum-cast aluminum blocks with 0.01mm dimensional accuracy, a standard surpassing Swiss watch tolerances.
Nissan’s electric ambitions crystallize in the Ariya SUV. Its revolutionary single-piece battery tray, die-cast from proprietary high-silicon aluminum, eliminates 87 traditional components while improving crash safety by 18%.
However, this innovation presents new challenges: a minor collision often requires full tray replacement at $3,200, reshaping collision repair economics.
What are Nissan’s plants around the world?
Nissan’s manufacturing empire spans 20 countries, with strategic die-casting hubs shaping regional success.
The Tochigi Plant north of Tokyo houses GT-R production, where master technicians spend 380 hours per car adjusting aluminum suspension components to micrometer precision.
Across the Pacific, Tennessee’s Smyrna facility processes 8,200 tons of aluminum monthly, feeding North America’s appetite for Altima sedans and Pathfinder SUVs.
In China’s Guangdong Province, the Guangzhou plant exemplifies scale. Its 72-second die-casting cycle time for Sylphy engine brackets outpaces German rivals by 40%, while maintaining 99.992% defect-free output.
For enthusiasts, Nissan’s Yokohama headquarters offers monthly tours (bookable 30 days ahead), including access to historical prototypes showcasing aluminum’s evolution from wartime planes to EV batteries.
Why Nissan Uses 20% More Aluminum Than Toyota But Earns 4.7% Less Profit?
Nissan navigates fierce domestic competition with distinct strategies.
While Toyota leads Japan’s 2024 sales at 1.48 million units, Nissan counters with higher aluminum integration – 82kg per vehicle versus Toyota’s 68kg.
This material gamble carries costs: Nissan’s profit margins trail Toyota by 4.7 percentage points despite technological advantages.
The used car market reveals aluminum’s double-edged impact.
GT-Rs retain 78% residual value after five years, partly due to recyclable aluminum components.
However, aging models like the 2015 X-Trail face hidden costs: 23% require $1,100 valve body replacements by 60,000 miles, driven by die-casting wear in CVT transmissions.
What are the top 3 Nissan replacement parts?
Top 3 Replacement Parts
- Turbocharger Housings (A390 alloy)
- Demand: 3.2M units/year
- Cost Gap: 52(aftermarket)vs172 (OEM)
- CVT Valve Bodies
- Failure Rate: 23% by 60,000 miles
- Ariya Motor Covers
- Labor Cost: $320/set
Dakar Rally Rule: Nissan entries must use T6 aluminum suspension arms, JUN’s forged GT-R intake manifold: $3,850/set
Searching for High-Quality for Cast Aluminum Parts?
You’ve come to the right place! Yongzhu Casting is a certified die casting manufacturer with over 20 years of expertise in the industry.
We have successfully completed numerous die casting projects for Aluminum casting parts, particularly in your industry.

Zhejiang Yongzhu Casting Technology Co., Ltd.
Location: Zhejiang, China
Company type: Manufacturers, Producers, Wholesalers
Year Founded: 2004
Main Products: Aluminium die casting, Mold Making, Die Casting, Sand Casting, Gravity Casting
Leading Chinese producer Yongzhu Casting is formerly known as Hangzhou Higer Metal Products Co., Ltd., was established in 2004.
With 20 years of experience in the industry, we are a specialized manufacturer in Aluminum casting and Machining.
Our products are widely used in various applications such as Automotive, Energy, Lighting, Medical, Home Furnishings, Machinery & Equipment etc. Below are our advantages:
Design Review & DFM Support
Our professionals will evaluate your designs and provide suggestions for cost savings. Additionally, we offer Design for Manufacturing (DFM) assistance and conduct mold flow analyses to facilitate efficient production.
State-of-the-Art Manufacturing Equipment
Our facility is equipped with advanced hot-chamber and cold-chamber die casting machinery for aluminum and zinc production.
We also utilize high-precision CNC machines in a temperature-controlled workshop, featuring 3-Axis, 4-Axis and 5-Axis setups to manage any project you have.
Rigorous Quality Control Measures
Our dedicated quality control team ensures that all parts meet the highest standards of quality and consistency. We employ high-accuracy measurement instruments, including CMM, spectrometers, and X-ray detectors.
Comprehensive Surface Treatment Options
We provide a variety of surface finishing techniques for your precision die casting components. Our in-house services include cleaning, polishing, anodizing, shot blasting, and painting.
Flexible Project Acceptance
While larger manufacturers often shy away from low-volume projects, and smaller ones may struggle with quality, Yongzhu Casting stands apart. We prioritize customer satisfaction and willingly accept high-mix, low-volume projects like yours.
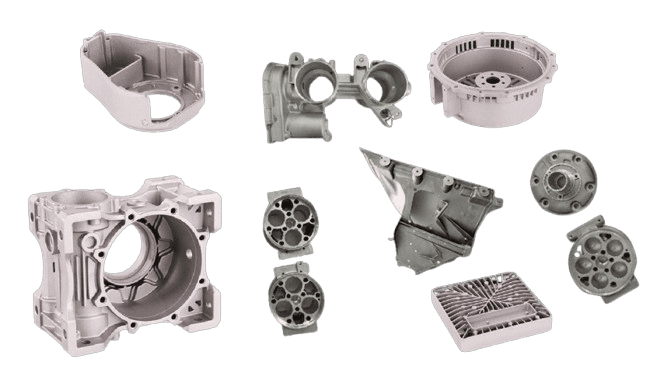