A380 aluminum alloy is one of the most commonly used materials in die casting due to its excellent balance of properties and cost-effectiveness.
Die casting involves injecting molten metal into a mold cavity under high pressure. The A380 alloy is particularly favored for its high fluidity, pressure tightness, and resistance to hot cracking.
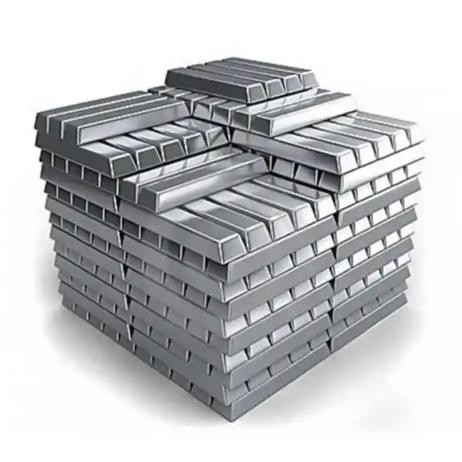
Benefits of A380 Aluminum Alloy
Superior Mechanical Properties
A380 aluminum alloy offers excellent mechanical properties, including high tensile strength, corrosion resistance, and thermal conductivity.
These characteristics make it suitable for manufacturing a wide range of components in the automotive, aerospace, and electronics industries.
Cost Efficiency
The A380 alloy is relatively inexpensive compared to other die casting materials, making it an economical choice for mass production.
Its high fluidity reduces the need for complex tooling and minimizes wastage, further lowering production costs.

Versatility in Application
A380 aluminum alloy is highly versatile, allowing for the creation of complex and intricate shapes with tight tolerances.
This versatility makes it ideal for producing components such as engine blocks, gearboxes, and electronic housings.
Detailed Steps in the A380 Die Casting Process
1. Preparation of the Die
The die is the mold used to shape the molten metal. It consists of two halves: the cover die and the ejector die. Proper preparation of the die is crucial for ensuring the quality and precision of the final cast.
This involves cleaning, preheating, and coating the die with a lubricant to facilitate the flow of the molten metal and prevent sticking.
2. Melting and Injection of A380 Alloy
The A380 alloy is melted in a furnace at a temperature of approximately 610°C to 650°C. Once the metal reaches the desired molten state, it is injected into the die cavity under high pressure, typically ranging from 1,500 to 25,000 psi.
This high-pressure injection ensures that the molten metal fills the entire mold cavity and captures fine details.



3. Solidification and Cooling
After injection, the molten metal begins to solidify and cool within the die. Cooling rates can be controlled to influence the microstructure and mechanical properties of the final cast.
Rapid cooling usually results in finer grain structures, enhancing the strength and durability of the component.
4. Ejection of the Casting
Once the metal has solidified, the die is opened, and the casting is ejected using ejector pins. Care must be taken during ejection to avoid damaging the casting.
The die is then prepared for the next cycle, and the process is repeated.
5. Trimming and Finishing
The cast component often has excess material, known as flash, which needs to be trimmed. This is done using trimming dies or manual methods.
Post-processing operations such as machining, heat treatment, and surface finishing are performed to achieve the desired specifications and enhance the component’s properties.
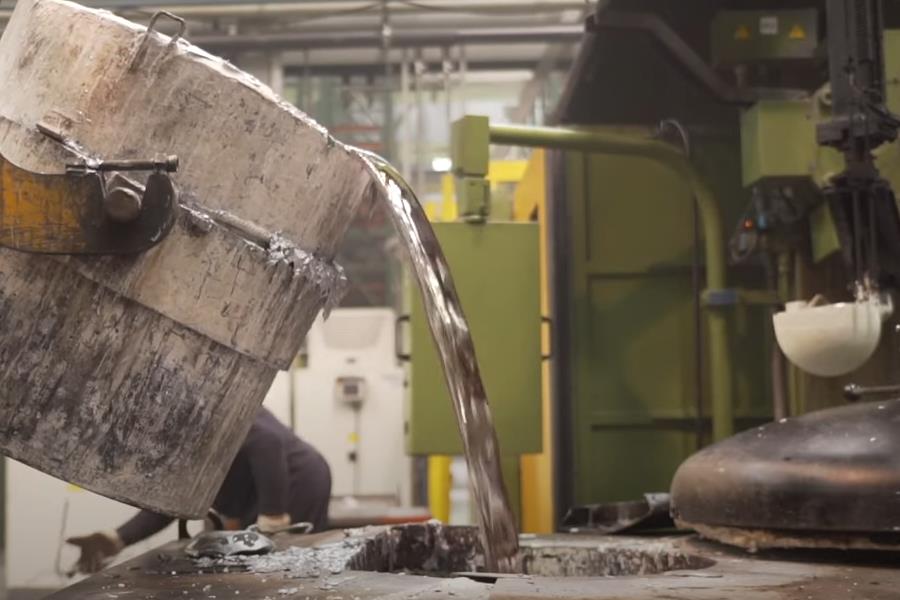
Quality Control in A380 Die Casting
Inspection and Testing
Quality control is a critical aspect of the die casting process. Components are inspected for defects such as porosity, cracks, and dimensional inaccuracies.
Non-destructive testing methods, including X-ray inspection and ultrasonic testing, are used to ensure the integrity of the castings.
Process Optimization
Continuous monitoring and optimization of the die casting process are essential for maintaining high quality. This includes adjusting parameters such as injection speed, pressure, and die temperature to achieve optimal results.
Advanced technologies like computer simulation and process automation are increasingly used to enhance precision and efficiency.

Applications of A380 Die Cast Components
Automotive Industry
In the automotive sector, A380 die cast components are widely used due to their lightweight and high-strength properties. Common applications include engine blocks, transmission housings, and structural parts.
Aerospace Industry
The aerospace industry benefits from A380 aluminum alloy’s excellent strength-to-weight ratio. It is used in the production of aircraft components such as brackets, housings, and connectors, contributing to fuel efficiency and performance.
Electronics Industry
A380 die castings are also prevalent in the electronics industry, where they are used to manufacture heat sinks, housings, and connectors. The alloy’s thermal conductivity and corrosion resistance make it ideal for these applications.



Contact us today to discuss your project needs and receive a quote, you can trust us to deliver exceptional castings that meet your requirements.