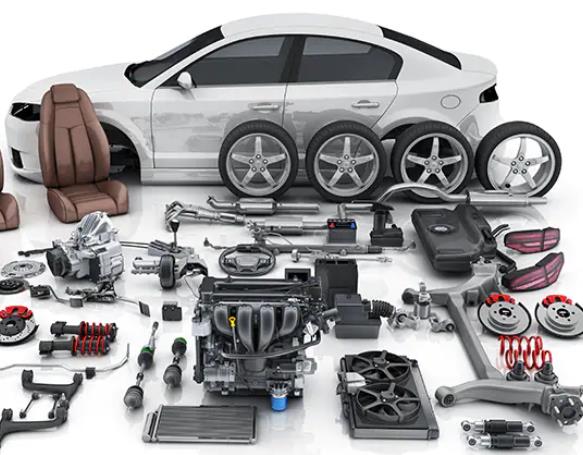
The aluminum die casting process, a cornerstone in modern manufacturing, offers unparalleled versatility in crafting detailed and intricate components. This exploration delves into the nuances of aluminum die casting, encapsulating its foundational principles and diverse applications.
It highlights the expertise of Yongzhu Casting, a prominent figure in the aluminum die casting domain, rooted in Zhejiang, China, since 2004.
Demystifying Aluminum Die Casting
What is Aluminum Die Casting?
Aluminum die casting stands as a pivotal metal casting method, involving the high-pressure injection of molten aluminum into a meticulously designed mold cavity.
This technique yields precision parts characterized by exceptional surface finish, accuracy, and intricate detailing. Its adaptability across various sectors underscores its significance in manufacturing a multitude of components.
Yongzhu Casting’s Expertise
Since 2004, Yongzhu Casting has cemented its reputation in the aluminum die casting industry. Our facility in Zhejiang, China, is dedicated to crafting superior aluminum die cast parts, tailoring our solutions to the eclectic needs of our clientele.
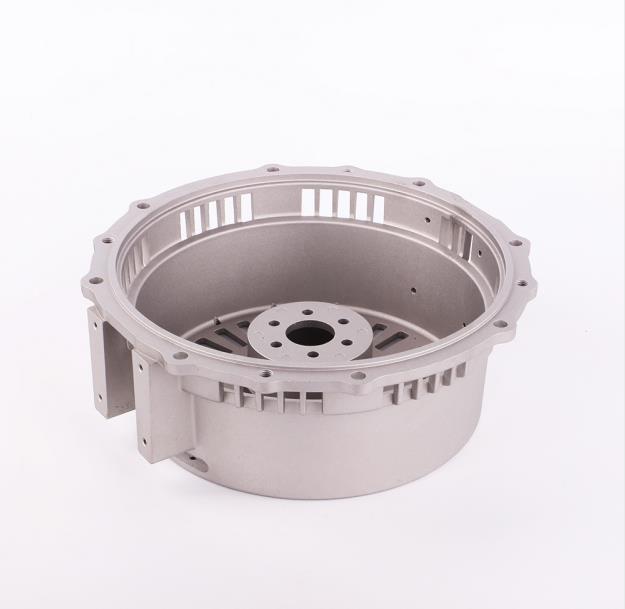
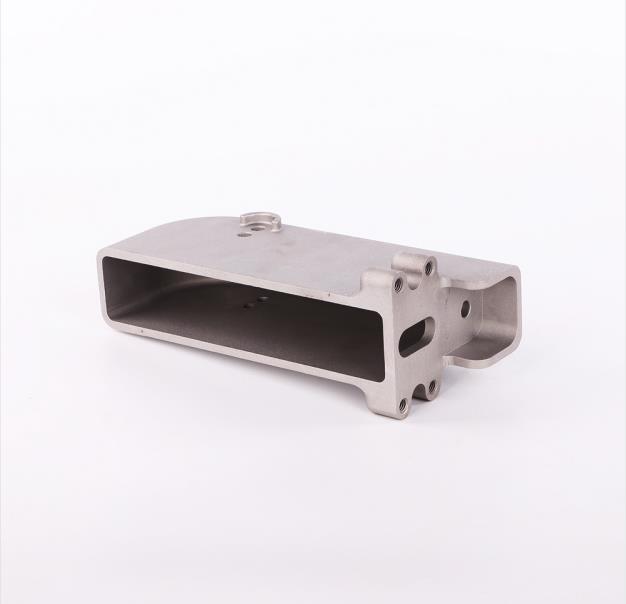

The Aluminum Die Casting Process Unfolded
Mold Design and Preparation
The journey begins with crafting the mold, a steel construct comprising two segments: the cavity and the core. Precision in mold design is vital to ensure the dimensional accuracy of the final product.
Melting and Injection
Aluminum is melted and then propelled into the mold cavity under high pressure. This step is crucial for capturing the intricate details of the mold design.
Rapid Cooling and Solidification
Following injection, rapid cooling within the mold facilitates the aluminum’s transformation into a solid state, a critical phase for attaining the desired physical and dimensional attributes.
Ejection and Finishing
Post-solidification, the mold halves part, revealing the formed aluminum piece. This stage demands meticulous handling to maintain the integrity of the part.
Exploring the Benefits of Aluminum Die Casting
Precision and Intricacy
Aluminum die casting is lauded for its capability to reliably produce parts with complex geometries and fine details, meeting stringent tolerance requirements.
Material Advantages
The process leverages aluminum’s inherent strengths: a high strength-to-weight ratio, corrosion resistance, and efficient thermal conductivity, broadening its applicability across various fields.
Cost-Effectiveness
Aluminum die casting’s rapid production rate renders it a cost-efficient solution for both large-scale and smaller production needs, minimizing the necessity for additional machining.
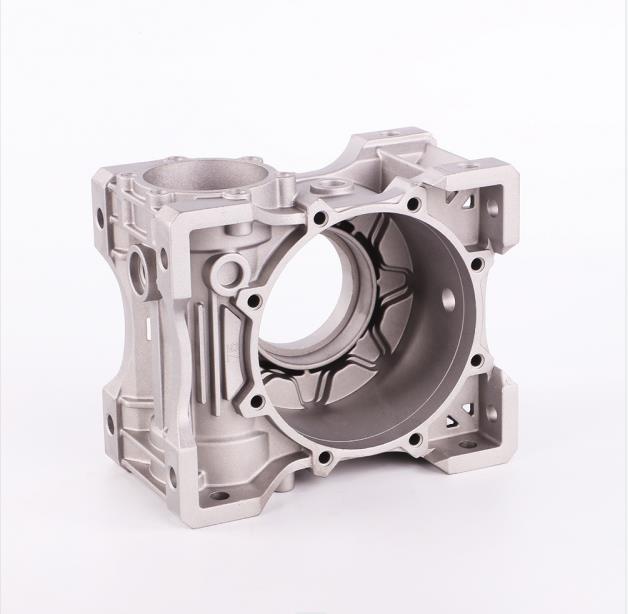

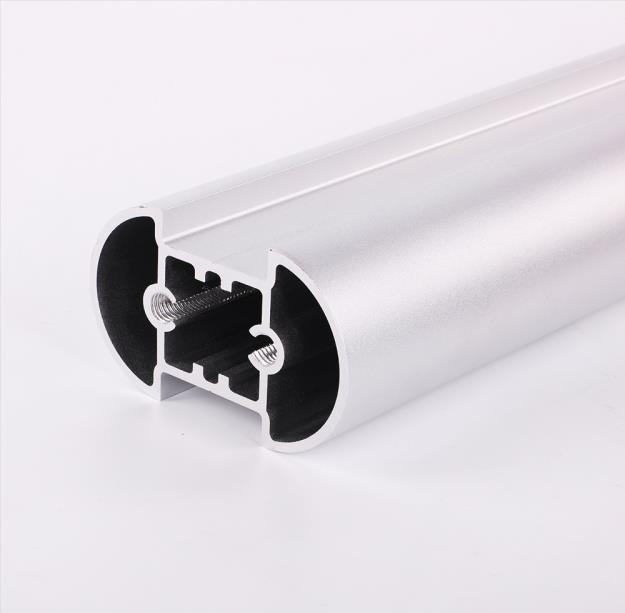
Wide-Ranging Applications of Aluminum Die Casting
Automotive Innovations
In the automotive realm, aluminum die casting is instrumental in fabricating engine parts, transmission components, and structural elements, benefiting from aluminum’s lightweight and robust nature.
Electronics and Home Appliances
This process is pivotal in creating components like heat sinks and casings in electronics and appliances, where effective heat management is essential.
Industrial Machinery
For industrial equipment, aluminum die casting is integral in producing precise and durable components such as pumps, valves, and various machinery parts.
Conclusion
Aluminum die casting emerges as a versatile and effective technique for manufacturing high-quality, detailed, and precise parts.
At Yongzhu Casting, our longstanding expertise as an aluminum die casting provider since 2004 positions us as a go-to partner for diverse industry requirements. Engage with us to explore how our aluminum die casting capabilities can elevate your project’s success.