Both powder coating and anodizing are finishing techniques that create durable, corrosion-resistant coatings on products.
Knowing the distinctions between these two methods can guide your choice for aluminum products. This allows you to consider the benefits of each process against your specific needs.
This guide provides insight into the features, differences, and uses of each, as well as where you can obtain these services.

What is Aluminum Powder Coating?
The process of aluminum powder coating involves applying a dry powder to an aluminum part. First, the powder is electrostatically charged, and then the part is heated to create a long-lasting coating.
This finishing technique forms a smooth layer that can conceal flaws and offers a wide variety of color choices.
Powder coating provides a protective layer that is resistant to corrosion and UV damage. The strength and longevity of the coating depend on the conditions the aluminum product is exposed to.
Key Advantages of Powder Coating
These are some attributes that make powder coating a preferred option when choosing between powder coating and anodizing.
Aspect | Key Points | Applications | Benefits |
---|---|---|---|
Cost-Effective | Less expensive than anodizing; suitable for high-volume production. | Manufacturing | Lower production costs; easy storage. |
Consistent Appearance | Covers flaws; ensures uniform finish and color consistency. | Aesthetic industries | Eliminates color variations; hides imperfections. |
Chemical Resistance | Protects against gasoline, cleansers, oils, and other chemicals. | Industrial | Long-lasting part durability. |
Impact Resistance | Creates robust products resistant to impacts and scratches. | Mechanical applications | Preserves quality and appearance. |
Corrosion Resistance | Offers protection against moisture and chemicals. | Outdoor applications | Prevents corrosion and damage. |
Versatile Application | Suitable for a range of aluminum parts due to heat resistance. | Various industries | Widely applicable across sectors. |
Heat Resistance | Shields parts in high-temperature environments. | Automotive and grilling | Maintains integrity in harsh conditions. |
Aluminum Anodizing Process
Anodizing is the process of forming a protective oxide layer on the surface of aluminum through an electrolytic method. This technique can also be applied to coat aluminum alloys.
In this process, the aluminum serves as the anode, while liquid coatings function as the cathode.
After the process is complete, the paint becomes fully integrated with the aluminum part. As a result, the coating is permanently bonded and won’t chip away like traditional paint.
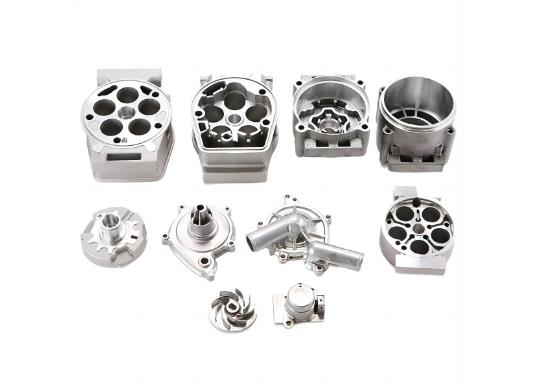
Anodizing Features
Here is a table summarizing the key aspects of anodizing in terms of corrosion resistance, consistent coating, exceptional durability, and eco-friendliness:
Aspect | Key Points | Benefits |
---|---|---|
Corrosion Resistance | Anodizing strengthens metal resistance due to a fully bonded protective coat. | Guards against wear, tear, and scratches, ideal for various applications. |
Consistent Coating | Submerging aluminum in the anodizing bath creates a uniform, smooth finish. | Provides even coverage of all surfaces and intricate areas. |
Exceptional Durability | Anodizing forms a permanent bond between aluminum and the paint. | Long-lasting durability with various color options. |
Eco-Friendly | Reusable electrolyte bath and no VOC emissions. | Sustainable process with minimal environmental impact. |
Powder Coating vs Anodizing: Which is Superior?
When choosing between powder coating and anodizing, consider the following factors to determine the best finishing method for your needs:
Aspect | Key Points | Benefits |
---|---|---|
Environmental Friendliness | Both processes produce minimal waste and are non-toxic and chemically stable. | Eco-friendly options with minimal impact. |
Cost | Powder coating is generally less expensive than anodizing, making it ideal for large-scale production. | Lower production costs; efficient for mass production. |
Variety | Powder coating offers a wider range of color options, while anodizing keeps the aluminum surface visible for intricate designs. | Enhanced design options and visual appeal. |
Superior Powder Coating Services by Yongzhu Metal
Yongzhu Metal excels in both functional and aesthetic surface finishes, serving as a trusted B2B partner worldwide.
If you desire a long-lasting finish on your aluminum components or castings, Yongzhu Metal is a top choice.

Leveraging advanced technology, they offer finishes with various textures, tones, and gloss levels.
In addition to powder coating and anodizing, they provide additional services such as liquid painting, chromate conversion, laser carving, and more.
Another advantage of choosing Yongzhu Metal for powder coating is their rigorous quality inspections throughout the production process.
The company also ensures that all finished parts comply with REACH and ROHS standards. Drop me an email with your ideas, and I’ll get back to you swiftly!