Burrs are flaws that can be unattractive and can significantly decrease the part’s safety and effectiveness. If you frequently purchase parts, you may have encountered unwanted burrs on components.
What Is Deburring?
Deburring is a process used to remove unwanted burrs from metal products.
It serves as a secondary machining technique designed to improve the final appearance of a part by eliminating excess pieces and raised edges of the material.
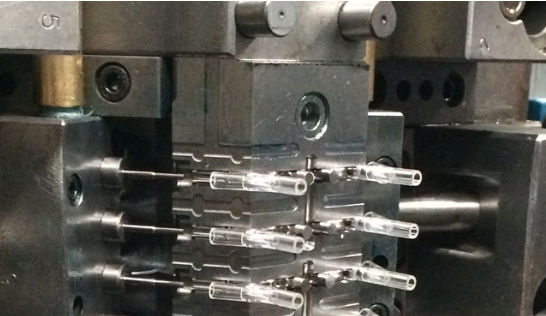
Burrs can form due to piercing, cutting, compressing, or bending materials. The deburring process utilizes machines that remove burrs through thermal, electrochemical, or mechanical methods.
Deburring incurs costs, typically ranging from 10% to 25% of the manufacturing cost, depending on the application.
Although this can be a substantial expense, it does not significantly increase the intrinsic value of a part.
Sources of Burrs
Burrs can commonly arise during various machining processes and may emerge at different stages of the manufacturing process, including:
- Forming
- Stamping
- Engraving
- Turning
- Drilling
- Plasma cutting
- Sintering
- Casting
- Grinding
- Laser cutting
- Drilling
Categories of Burrs
When burrs form during machining, they manifest in various shapes and forms, categorizing them into different types.
Here’s a table summarizing the types of burrs and their key features:
Type | Description | Removal Methods |
---|---|---|
Rollover Burrs | Small pieces of metal protruding, creating rounded edges. | Proper tools and methods |
Poisson Burrs | Excess material accumulates and spreads sideways, creating a rough edge. | Easily removed with deburring tools |
Breakout Burrs | Material tears or fractures at the cutting tool’s exit point. | Mix of techniques and tools |
Tear Burrs | Uneven, jagged edge from material tearing during cutting. | Aggressive deburring tools |
Oxide Burrs | Raised edge from heat causing metal to oxidize during cutting. | Chemical and mechanical processes |
Micro-burrs | Tiny, often invisible burrs causing functional issues if not removed. | Precision tools and polishing |
Significance of Deburring
Parts with burrs present defects that can compromise the durability, safety, and overall performance of the component. These are some quality issues caused by burrs:
- Reduced fracture resistance
- Damage to fasteners
- Material failure and cracks
- Lubrication challenges
- Increased surface wear
- Lower safety levels
- Decreased corrosion resistance
Deburring removes these imperfections, resulting in a more functional, aesthetically pleasing, and safer part.
This process also minimizes the need for additional grinding and sanding. When done effectively, deburring lowers material usage and boosts productivity.
Deburring is often part of the surface finishing process, which may include additional steps such as edge breaking, descaling, graining, and deslagging.

Burrs can create safety risks as sharp edges may cut through electrical wires and pressurized lines. Additionally, individuals handling such parts may face harm.
In machining, finishing can account for up to 35% of labor expenses. Since finishing is part of quality assurance, deburring parts ensures higher quality outcomes for your customers.
Deburring Media
A variety of abrasive media are commonly used in deburring, including organic compounds, ceramics, plastics, and steel.
These materials come in different sizes and shapes and are used to cut, scratch, and keep parts from sticking together.
Here’s a table summarizing different types of deburring media and their key features:
Media Type | Description | Key Features |
---|---|---|
Ceramic Media | Suitable for deburring plastics and metals. Offers a range of finishes at various speeds. | Ideal for hard metals due to hardness |
Plastic Media | Designed for specific applications. Low density makes them suitable for general-purpose deburring. | Effective with ferrous and non-ferrous metals |
Synthetic Media | Contains up to 70% abrasives like emery, silicon carbide, and alumina. | Mixes with soft material that erodes, leaving abrasives to deburr surfaces |
Steel Media | Best for light deburring tasks. More costly but favored for cleanliness and lower attrition rate. | |
Organic Media | Examples include corn cob and walnut shells. Absorb oil and water, useful for drying applications. |
Various Deburring Methods
Different methods of deburring are chosen based on factors such as part geometry, cost, production volume, the location of burrs, and material.
Traditional methods include manual and mechanical deburring. Thermal and electrochemical deburring are designed for specific use cases.
Hand Deburring
This method utilizes handheld or mechanized tools such as grinders, sanders, and files. It focuses on specific areas, avoiding impact on other parts of the component.
Though time-consuming, it is often used in small machine shops and requires skilled craftsmanship for optimal results.
Machine Deburring
Here’s a table summarizing different mechanical deburring techniques and their key features:
Technique | Description | Key Features |
---|---|---|
Grinding | Removes burrs using various grinding tools and techniques. | Offers a high-quality finish with minimal effort |
Sanding | Utilizes abrasives such as zirconia, silicon carbide, and aluminum oxide. | Available in forms like discs, wheels, belts, sheets |
Vibratory | Uses vibrating machines and abrasive media for deburring. | Effective for complex parts or mass production |
Tumbling | Employs a container with liquids and abrasives. | Removes burrs without scratching the part; provides excellent surface finish |
Rolling | Achieves high-quality finishes with minimal effort. | Cost-effective, similar to hand deburring but suitable for mass production |
Punching Deburring
This method uses punching machines to remove burrs. Multiple types of dies are required for punch mold work.
Punching offers higher productivity and efficiency compared to hand deburring but requires specialized tools and is unsuitable for complex shapes.
Internal Hole Deburring
This approach applies when the inside of a hole needs deburring. Various tools such as cutting tools are used. The tool enters the hole and removes burrs without causing damage or scratches.
Brushing
Special brushes are used to clean the surface, similar to deburring with sandpaper. As the brush is mounted on a machine tool, the process is more straightforward and efficient.
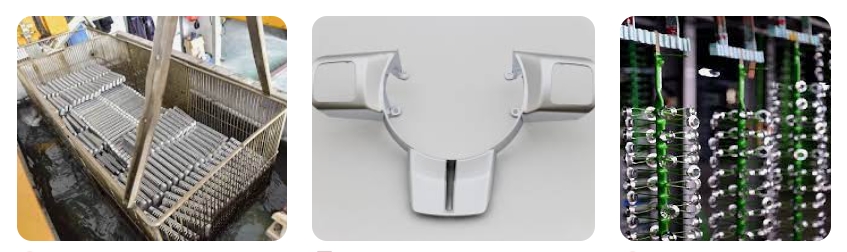
Electrochemical Deburring
Also known as electropolishing, this method is ideal for removing burrs from hard-to-reach areas. It works opposite to plating by removing material instead of adding it.
Combustion Deburring
In this method, burrs are removed by burning the material in a controlled combustion chamber. This technique suits mass production because it is quick and can deburr multiple parts simultaneously.
Water Pressure Deburring
This method uses pressurized water to remove debris and burrs from a part. Water pressure is managed to prevent damage to the part. But it is not suitable for removing larger burrs, as it may harm the part.
Drop me an email with your ideas, and I’ll get back to you swiftly!