Cold shuts in die casting are surface flaws marked by discontinuities. They appear as irregular, sunken, and almost straight lines that can be narrow and small, sometimes with broken junctions or edges.
Cold lap point is another term for this defect, especially in pressure die casting. A thin, fine foliation cleavage on the surface signifies its presence.
These linear cracks tend to appear far from the gate, particularly in aluminum die-casting alloys. Parts with cold shuts are often rejected due to their reduced usability.
This article briefly outlines the causes, effects, and solutions for this surface casting defect.

Causes of Die-Casting Cold Shuts:
The primary cause of cold shuts is the premature solidification of molten metals or alloys during the casting process. However, several factors can lead to this issue:
- Low Temperature: When the mold or molten alloy/metal is too cool, it can disrupt the surface and cause defects.
- Insufficient Fluidity: A lack of proper fluidity in the molten liquid prevents a smooth combination, resulting in surface cracks.
- Poor Fusion: When the liquid metal/alloy fills separate runners, it disrupts the uniform flow, impeding proper mold fusion.
- Design Flaws: Incorrect, poor, or faulty gate designs can interfere with the flow of liquid, causing cold shuts in distant areas.
- Processing Challenges: Inadequate exhaust, slow filling speeds, and prolonged filling times can result in problematic flow combinations.
- Internal Pressure: Little to no gas permeability can lead to a buildup of pressure, slowing down or impeding the flow of molten metals.
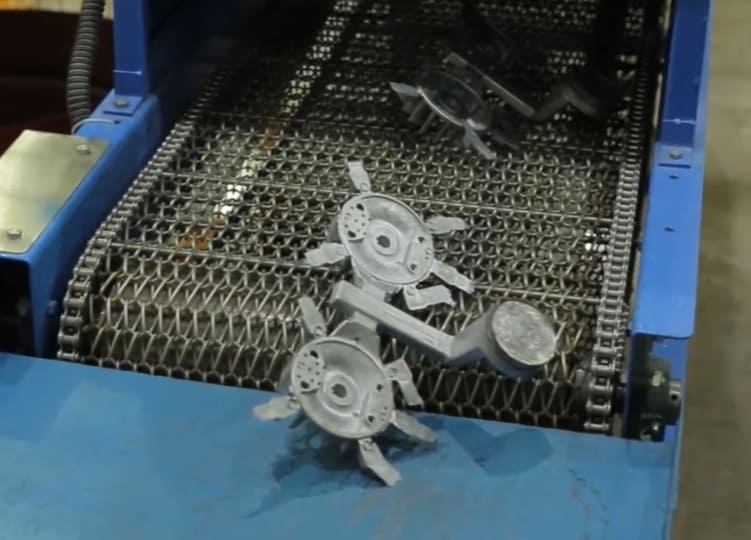
Consequences of Cold Shuts in Casting
Cold shuts typically occur as surface-level defects with notable depth, but they can also form slightly beneath the surface.
Since these defects often appear thin or fine, they may be overlooked intentionally. However, this can be dangerous as the defect can worsen over time.
As cold shuts develop, they can lead to significant structural failure. A well-known example is the Liberty Bell crack in 1846, which began as a hairline fracture and expanded into a more noticeable crack.
Additionally, addressing or repairing cold shuts in die-casting can be challenging.
Preventing Cold Shuts in Die-Casting
To prevent cold shut defects in die-casting, consider the following measures:
Aspect | Key Points |
---|---|
Raise Temperatures | Maintain appropriate mold and metal temperatures to avoid premature solidification. |
Optimal Chemical Composition | Achieve the right balance of alloy composition to boost fluidity and ensure smooth flow. |
Enhanced Casting System | Optimize filling specifications, gating systems, and exhaust parameters for consistent flow. |
Improved Overflow Conditions | Refine overflow setups and stream pathways for better casting results. |
Boost Pressure and Speed | Increase gate and injection speeds, and apply additional pressure to expel impurities and speed up molten streams. |
Drop me an email with your ideas, and I’ll get back to you swiftly!