Aluminum die casting, a precision manufacturing process, produces high-quality, lightweight, and durable components by injecting molten aluminum into molds under high pressure.
With diverse applications in industries such as automotive, aerospace, electronics, and medical, achieving the optimal surface finish is critical to meeting performance and aesthetic standards.
This guide outlines key surface finishing options, industry-specific requirements, and how Yongzhu Casting can support your surface finish selection process.
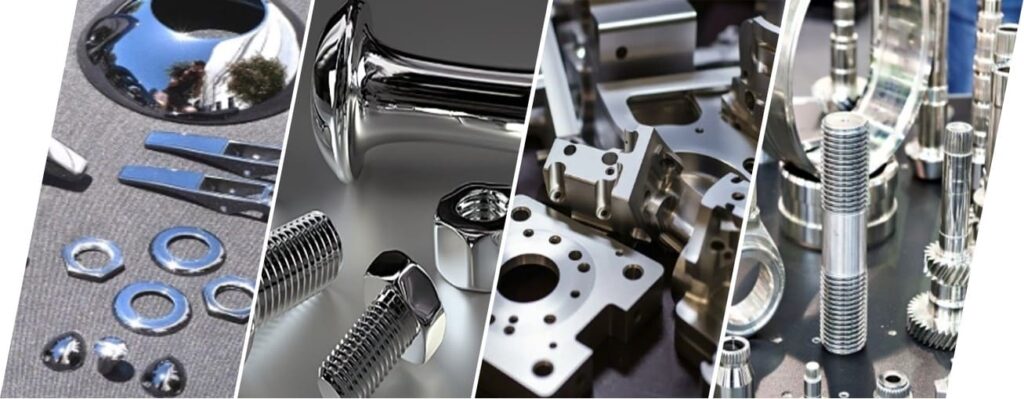
Factors to Consider for Optimal Surface Finish in Aluminum Die Casting
When choosing a surface finish, various factors must align with industry-specific requirements. Here are essential considerations to enhance the die-cast component’s performance and appearance:
- Aesthetic Needs: Many industries require specific textures or colors to complement the final product’s appearance.
- Durability and Corrosion Resistance: Industries like automotive and aerospace demand finishes with high corrosion resistance, while medical and electronics often require surfaces free of imperfections for functional purposes.
- Thermal and Electrical Conductivity: These properties are essential for electronics and automotive sectors, where parts like heat sinks need to dissipate heat efficiently.
- Target Budget: Costs can vary significantly with each surface finish option. It’s essential to balance budget constraints with desired finish quality.
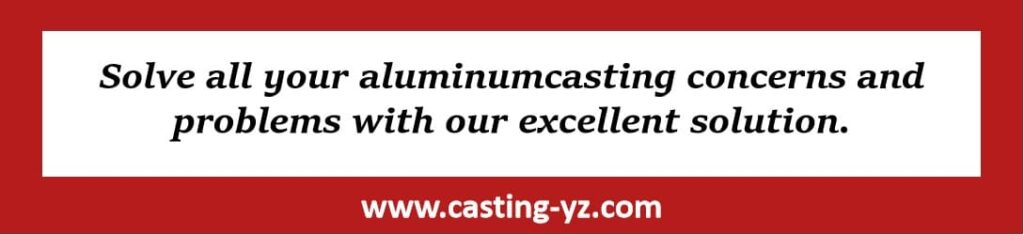
Industry-Specific Requirements in Surface Finishing
Different industries have unique needs for aluminum die-cast parts, and surface finishing often plays a key role in achieving their standards. Here’s a breakdown of requirements across major sectors:
- Automotive Industry: With over 60% of die-cast aluminum used in automotive manufacturing, finishes must provide corrosion resistance, durability, and thermal conductivity. For instance, aluminum parts used in vehicle exteriors benefit from powder coatings for durability, while interior components may require anodizing for aesthetic appeal.
- Aerospace Sector: Die-cast parts in aerospace must withstand high temperatures and resist corrosion in extreme environments. Processes like anodizing provide an extra layer of corrosion protection, while mechanical finishes, such as shot blasting, prepare the surface for final coatings, enhancing durability and reducing weight.
- Medical Devices: In the medical field, precision and cleanliness are paramount. Surfaces must be non-porous, corrosion-resistant, and easy to sterilize. Electroless nickel plating is a popular finish for medical tools, offering a smooth, matte surface that resists wear and maintains biocompatibility.
- Electronics Industry: Electronics manufacturers prioritize conductive finishes, such as copper tin plating, for effective heat dissipation and electromagnetic interference (EMI) shielding. These finishes improve device reliability by regulating temperatures and reducing signal interference.
Available Surface Finish Options for Die Cast Aluminum
Yongzhu Casting offers various surface finishes to cater to your industry’s specific requirements. Here’s a closer look at the most common options:
- Mechanical Finishes
- Shot Blasting: Removes flash, evens out surfaces, and improves coating adhesion. Ideal for non-cosmetic, functional parts.
- Ball Burnishing: Achieves a smooth, shiny surface ideal for highly cosmetic parts in automotive interiors or consumer electronics.
- Chemical Conversion Coatings
- Trivalent Clear Chromate: Enhances corrosion resistance and adhesion for additional coatings. Suitable for moderate exposure applications.
- Yellow Chromate: Provides higher corrosion resistance with a unique, golden finish, though it is not RoHS-compliant.
- Anodizing: Adds corrosion protection and non-conductivity, especially useful for parts in aerospace or electronic enclosures requiring insulating properties.
- Final Coatings
- E-Coat: A high-gloss, black coating with excellent corrosion resistance, often used for parts requiring a durable, cosmetic finish.
- Powder Coating: Available in a wide variety of colors and textures, powder coating is a durable option for automotive parts and outdoor applications.
- Electroless Nickel: Provides excellent wear resistance and EMI shielding, ideal for medical devices and electronic components requiring conductivity and protection.
In-Depth Analysis of Finishing Processes
For customers seeking detailed insights into the pros and cons of each finish, here’s an overview of cost and performance across various methods:
- Shot Blasting: Low cost, functional, and durable, yet not ideal for high-cosmetic applications ($0.08/part).
- Ceramic Media: Provides smoothness and is versatile across alloys ($0.12/part).
- Trivalent Clear Chromate: Low-cost, medium corrosion resistance, with minimal added thickness ($0.44/part).
- Powder Coating: High durability, excellent color customization, but requires precision in application to avoid uneven thickness ($0.80/part).
- Electroless Nickel: High wear resistance, good for tight tolerance parts, although slightly more expensive ($0.82/part).
Design Tips for Optimal Surface Finish in Die Casting
Integrating surface finish requirements in the design phase ensures the best results for your application. Here are some considerations to keep in mind:
- Masking and Rack Points: Plan for areas that should remain uncoated or have tight tolerances.
- Tall Exposed Features: Address potential issues with powder coating on high-profile features by adjusting design or rack positioning.
- Texture in Molds: Pre-designed textures in the die mold can save time by eliminating extra finishing steps, particularly useful for parts with consistent texture needs.
How Yongzhu Casting Can Support Your Surface Finish Needs
With extensive experience across various industries, Yongzhu Casting leverages advanced simulation tools like MagnaSoft to ensure optimal flow and quality in the die casting process.
Our in-house experts guide you through selecting the best surface finish for your application, from high-durability powder coatings for automotive applications to corrosion-resistant anodizing for aerospace components.
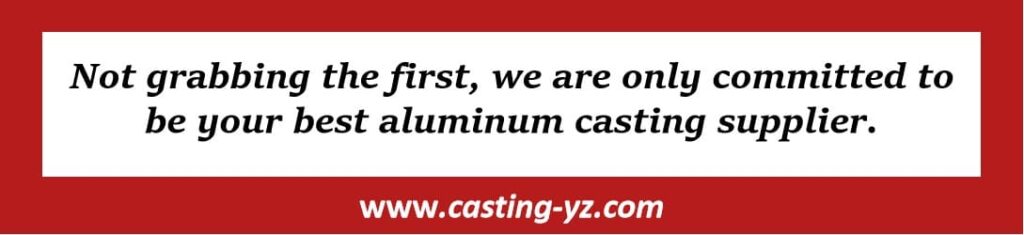
Conclusion
Surface finish selection is integral to maximizing the durability, appearance, and functionality of die-cast aluminum parts.
With a comprehensive range of mechanical, chemical, and final coating options, Yongzhu Casting tailors solutions for every industry, ensuring your die-cast components meet rigorous standards and project goals.
Visit our website to learn more or consult our experts on finding the perfect finish for your casting needs.