Introduction
In the evolving world of manufacturing, selecting the right aluminum casting method is crucial for ensuring quality, efficiency, and cost-effectiveness.
This guide provides a detailed comparison of the most common methods used in aluminum casting, including the latest updates for 2024.
Overview of Aluminum Casting Methods
Aluminum casting is a versatile manufacturing process used to create intricate components with complex geometries. The primary methods include:
- Sand Casting
- Die Casting
- Investment Casting
- Permanent Mold Casting
- Centrifugal Casting
Each method has its unique advantages and is suited for different applications based on factors such as production volume, complexity, and material properties.
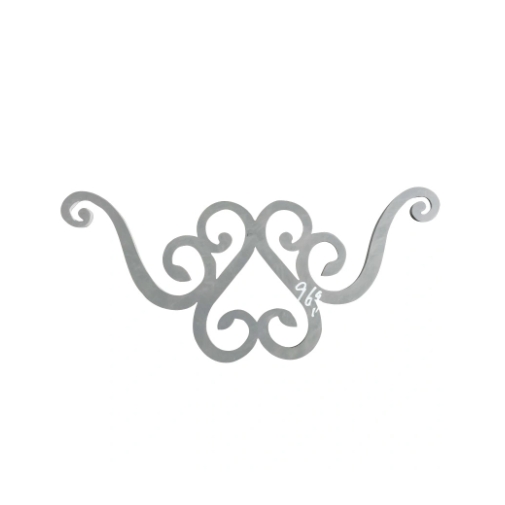
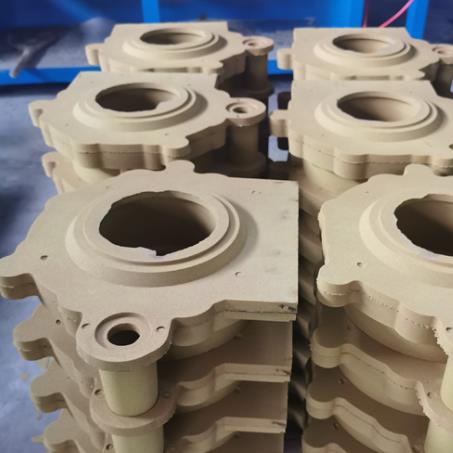
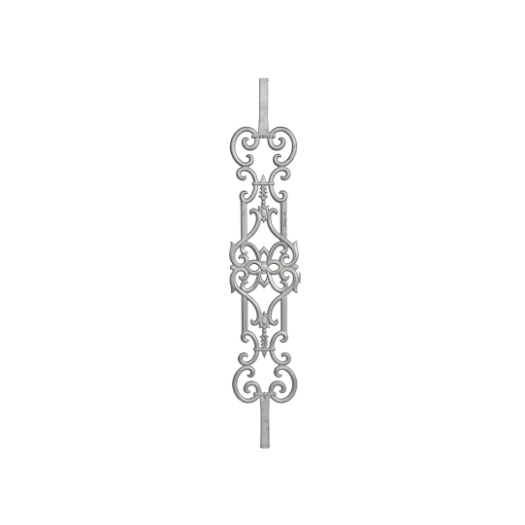
Sand Casting
Sand casting involves creating a mold from sand, into which molten aluminum is poured. The mold is destroyed to retrieve the casting, making it a one-time-use process.
Advantages | Disadvantages |
Versatility: Suitable for a wide range of sizes and complex geometries. Cost-Effective: Ideal for low to medium production volumes. Material Flexibility: Works well with various aluminum alloys. | Surface Finish: Typically rough, requiring post-processing. Tolerance Levels: Lower precision compared to other method |
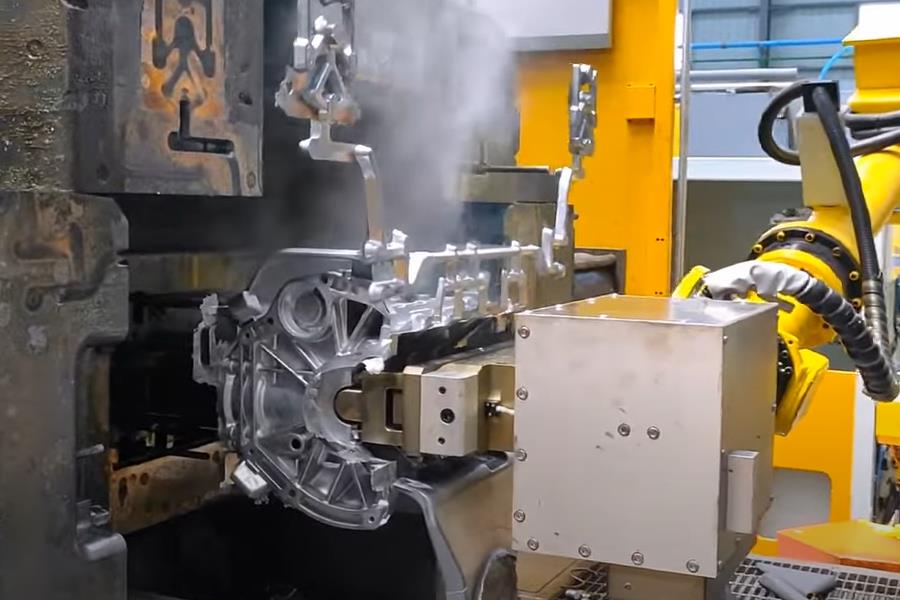
Die Casting
Die casting involves forcing molten aluminum into a steel mold under high pressure. The mold is reusable, allowing for high production efficiency.
Advantages | Disadvantages |
High Precision: Tight tolerances and smooth surface finishes. Efficiency: Suitable for high-volume production with minimal waste. Durability: Long mold life due to the steel construction. | Cost: High initial tooling costs. Material Limitations: Best suited for alloys with low melting points. |
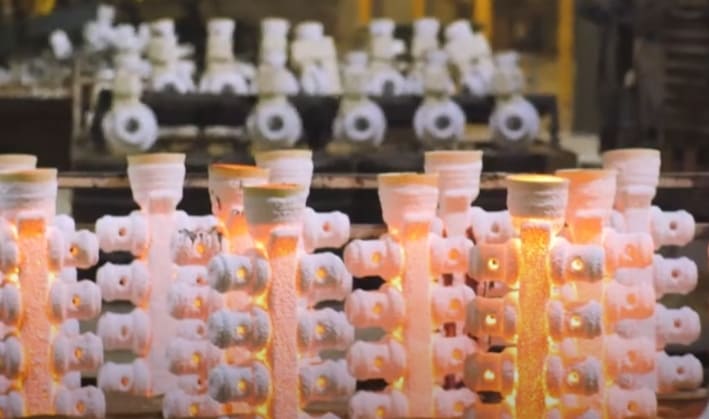
Investment Casting
Investment casting uses a wax pattern surrounded by a ceramic shell. Once the wax is melted out, molten aluminum is poured into the cavity.
Advantages | Disadvantages |
Complexity: Capable of producing highly intricate designs. Surface Finish: Superior finish with minimal machining required. Dimensional Accuracy: High precision for complex parts. | Cost: Higher per-piece cost due to the labor-intensive process. Size Limitations: Generally used for smaller parts. |
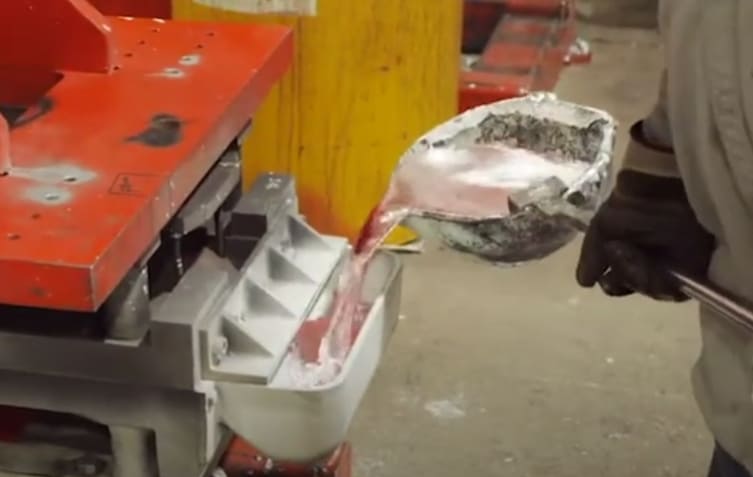
Permanent Mold Casting
Permanent mold casting involves pouring molten aluminum into a reusable mold made of metal. Gravity or low pressure fills the mold.
Advantages | Disadvantages |
Consistency: Produces parts with uniform properties. Surface Quality: Better finish compared to sand casting. Production Rate: Faster than sand casting with moderate tooling costs. | Design Restrictions: Limited to simpler shapes. Initial Costs: Higher than sand casting due to mold fabrication. |
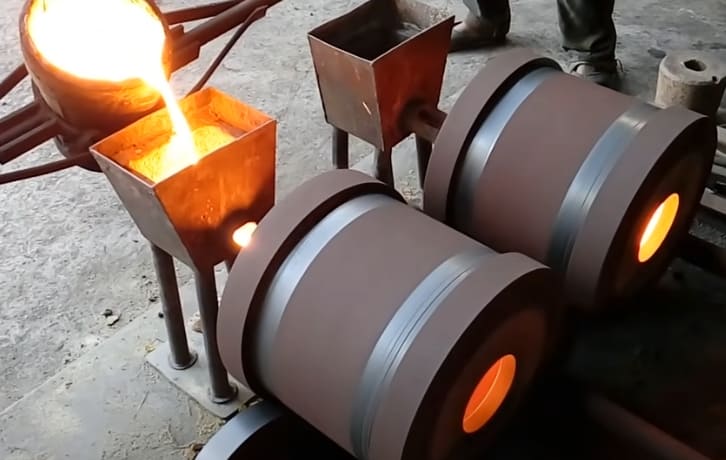
Centrifugal Casting
Centrifugal casting utilizes a rotating mold, where molten aluminum is poured. The centrifugal force distributes the metal along the mold’s walls.
Advantages | Disadvantages |
Quality: Produces parts with high density and minimal defects. Strength: Ideal for cylindrical parts with superior mechanical properties. Efficiency: Efficient for certain shapes, reducing material waste. | Shape Limitation: Best suited for symmetrical, tubular designs. Tooling Costs: Can be high for complex molds. |
Comparison of Methods
Method | Production Volume | Surface Finish | Tolerance | Cost | Complexity |
---|---|---|---|---|---|
Sand Casting | Low to Medium | Rough | Low | Low | High |
Die Casting | High | Smooth | High | High | Medium |
Investment Casting | Low to Medium | Very Smooth | High | High | Very High |
Permanent Mold Casting | Medium | Smooth | Medium | Medium | Low |
Centrifugal Casting | Medium | Smooth | High | Medium | Medium |
Choosing the Right Method
Selecting the appropriate aluminum casting method depends on several factors:
- Volume Requirements: High-volume production favors die casting, while lower volumes may be more cost-effective with sand or investment casting.
- Design Complexity: Investment casting is ideal for intricate parts, while permanent mold casting suits simpler designs.
- Budget Constraints: Initial tooling costs vary significantly, with sand casting being the most economical for low production runs.
Conclusion
Understanding the strengths and limitations of each aluminum casting method allows manufacturers to optimize their processes, ensuring the best balance of cost, quality, and efficiency.
Whether you are producing high-precision components or simple, robust parts, the right casting method can significantly impact your production success.