Introduction to A356 Die Casting
A356 die casting is a widely used manufacturing process known for producing high-quality aluminum alloy components.
This method is integral to various industries, including automotive, aerospace, and consumer electronics, due to its ability to create complex shapes with excellent mechanical properties and high surface quality.
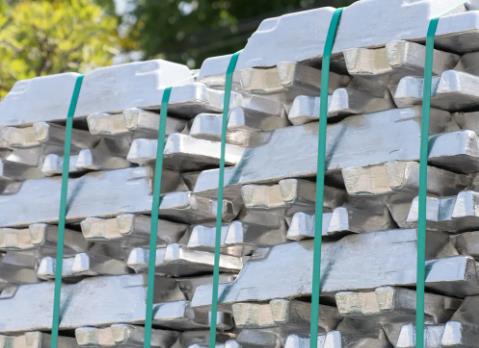
Understanding A356 Alloy
A356 is an aluminum alloy characterized by its excellent castability, corrosion resistance, and mechanical strength. The primary constituents of A356 alloy include:
- Aluminum (Al): Base metal providing overall structure.
- Silicon (Si): Enhances fluidity and reduces shrinkage during solidification.
- Magnesium (Mg): Improves strength and heat treatment response.
- Iron (Fe): Maintained at low levels to avoid brittleness.
- Copper (Cu) and Zinc (Zn): Controlled to ensure optimal mechanical properties.
Step-by-Step A356 Die Casting Process
Mold Design and Preparation
These molds are precision-engineered to define the final shape of the cast component. Key considerations in mold design include:
- Cavity Design: Ensuring proper flow and filling of molten metal.
- Cooling Channels: Facilitating rapid cooling and solidification.
- Ejection Mechanism: Allowing easy removal of the solidified part.



Melting and Alloying
This process requires careful control of temperature and composition to maintain the alloy’s properties. The steps include:
- Melting: Heating aluminum ingots and alloying elements to a liquid state.
- Degassing: Removing hydrogen and other impurities to prevent porosity.
- Fluxing: Adding fluxes to cleanse the molten metal and enhance quality.
Injection and Filling
Once the alloy reaches the desired molten state, it is injected into the prepared mold under high pressure. This stage is critical for achieving precise and consistent shapes.
- Injection: Using a hydraulic system to force molten metal into the mold.
- Filling Time: Optimizing to prevent defects like cold shuts and misruns.
- Venting: Ensuring proper air evacuation from the mold cavity.

Cooling and Solidification
After filling, the molten metal rapidly cools and solidifies within the mold. Proper cooling is essential to achieve desired mechanical properties and dimensional accuracy.
- Cooling Channels: Embedded in the mold to regulate temperature.
- Solidification Time: Controlled to minimize internal stresses and shrinkage.
- Ejector Pins: Activating to release the solidified part from the mold.
Trimming and Finishing
The solidified part, now referred to as a casting, undergoes trimming and finishing processes to remove excess material and achieve the final product specifications. These steps involve:
- Trimming: Removing flash and excess material using mechanical or manual methods.
- Surface Treatment: Enhancing surface quality through processes like sandblasting, grinding, or polishing.
- Heat Treatment: Applying heat treatment processes such as T6 to improve mechanical properties.
Quality Control and Inspection
Quality control is vital to ensure that the die-cast components meet industry standards and customer requirements. The inspection process includes:
- Dimensional Inspection: Using precision instruments to verify dimensions.
- Non-Destructive Testing (NDT): Techniques like X-ray and ultrasonic testing to detect internal defects.
- Mechanical Testing: Assessing properties such as tensile strength and hardness.
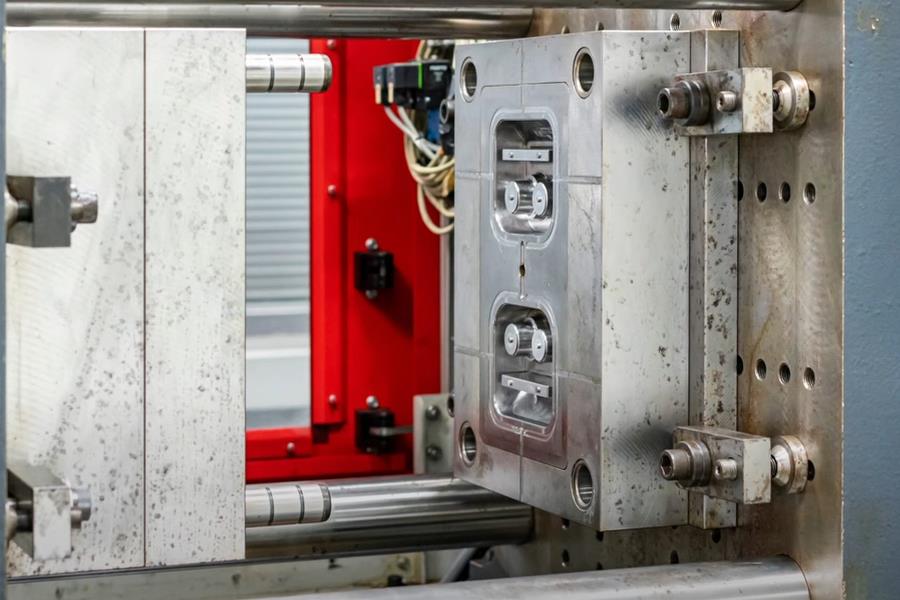
Advantages of A356 Die Casting
A356 die casting offers several advantages, making it a preferred method in various applications:
- High Precision: Achieves complex geometries with tight tolerances.
- Excellent Mechanical Properties: Combines strength, ductility, and corrosion resistance.
- Cost-Effectiveness: Suitable for high-volume production with minimal material wastage.
- Surface Quality: Produces parts with smooth surfaces, reducing the need for extensive finishing.
Applications of A356 Die Cast Components
A356 die cast components are used across a broad range of industries due to their versatility and performance. Key applications include:
- Automotive Industry: Engine blocks, transmission cases, and suspension components.
- Aerospace Sector: Aircraft frames, control surfaces, and structural parts.
- Consumer Electronics: Housings, heat sinks, and connectors.
- Industrial Equipment: Pump housings, valve bodies, and machinery components.
By understanding each step, from mold design to quality control, manufacturers can optimize production efficiency and product performance.
For further information on A356 die casting and to explore its full potential, feel free to reach out to our expert team.