In the realm of manufacturing, two prominent techniques stand out: die casting and injection molding. Each method has its own set of advantages and applications, making them suitable for different types of production needs.
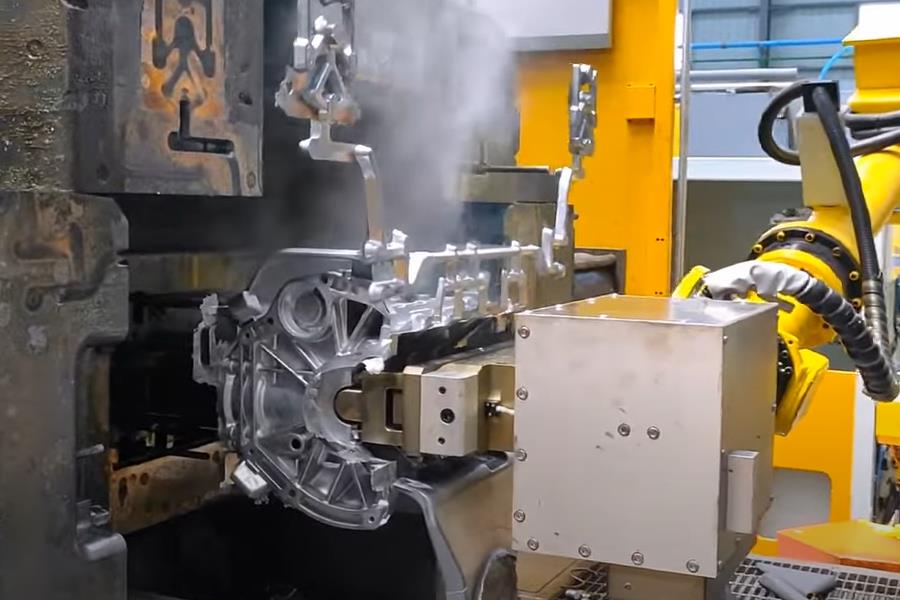
Understanding Die Casting
Die casting is a versatile manufacturing process used to produce geometrically complex metal parts. It involves injecting molten metal into a mold cavity under high pressure.
The process can be divided into two main types: hot-chamber die casting and cold-chamber die casting.
Hot-Chamber Die Casting
Hot-chamber die casting, also known as gooseneck casting, is typically used for metals with low melting points such as zinc, magnesium, and lead.
In this process, the metal is melted in a furnace and then drawn into the gooseneck for injection into the die.
This method is characterized by its high-speed production capability and cost-effectiveness for small to medium-sized parts.
Cold-Chamber Die Casting
Cold-chamber die casting is used for metals with high melting points like aluminum and copper. In this process, the molten metal is ladled into the injection chamber, from where it is forced into the die.
Cold-chamber die casting is preferred for producing larger parts with higher density and superior mechanical properties.

Exploring Injection Molding
Injection molding is predominantly used for manufacturing plastic parts. This process involves injecting molten plastic into a mold where it cools and solidifies into the final product.
Injection molding is renowned for its ability to produce high volumes of parts with excellent repeatability and precision.
Types of Injection Molding
- Thermoplastic Injection Molding: Utilizes thermoplastic polymers that can be melted and re-melted without altering their chemical structure.
- Thermoset Injection Molding: Uses thermosetting polymers which solidify into a permanent shape upon heating.
- Liquid Silicone Rubber (LSR) Injection Molding: Involves injecting liquid silicone rubber into a mold, suitable for producing flexible and durable parts.
Key Differences Between Die Casting and Injection Molding
Aspect | Die Casting | Injection Molding |
---|---|---|
Material Usage | Metals (aluminum, zinc, magnesium, copper) | Plastics (thermoplastics, thermosets, elastomers) |
Process Temperature | High temperatures to melt metals | Lower temperatures to melt plastics |
Mold Design and Complexity | Robust molds for high pressures and temperatures | Molds from various materials, less expensive |
Production Volume and Speed | High-speed production for large volumes | Efficient for large quantities of plastic parts |



Applications of Die Casting and Injection Molding
Application Area | Die Casting | Injection Molding |
---|---|---|
Automotive Industry | Engine components, transmission parts, structural components | Dashboard components, interior trims, under-the-hood parts |
Consumer Electronics | Housings for electronic devices, connectors, heat sinks | Household items, toys, packaging |
Aerospace | Aircraft components requiring high strength and precision | – |
Medical Devices | – | Syringes, surgical instruments, diagnostic equipment |
Advantages and Disadvantages
Aspect | Die Casting | Injection Molding |
---|---|---|
Advantages | – High production efficiency and speed – Excellent dimensional accuracy and surface finish – Suitable for large-scale production | – High repeatability and precision – Versatile for a wide range of plastics – Lower tooling costs compared to die casting |
Disadvantages | – High initial tooling costs – Limited to high-melting-point metals – Potential for porosity in cast parts | – Limited to plastic materials – Longer cooling times for thick-walled parts – Potential for warping and shrinkage |
Conclusion
Both die casting and injection molding are invaluable manufacturing techniques with distinct advantages and specific applications.
The choice between the two depends on factors such as material requirements, production volume, part complexity, and cost considerations.
Contact us today to discuss your project needs and receive a quote, you can trust us to deliver exceptional castings that meet your requirements.