Flash occurs when liquid alloy or metal unexpectedly flows into unauthorized areas of the die, such as beneath slides, along parting lines, or around ejector pins.
These areas are not intended to receive molten metal, yet flash occurs when the metal infiltrates them.
Excessive metal extrudes from the mold during casting, settling on the final product as flash. The scorching hot liquid metal, with its fluid properties, displaces some of the molten metal from internal sections, leading to flash formation.
The occurrence of flash in high-pressure die-casting processes presents significant challenges for manufacturers. This article briefly explores its causes, impacts, and preventive measures.

Causes of Flash:
- Inadequate Die Sealing: Uneven heating during different casting phases can cause irregular expansion, compromising the seal of the die. This increased internal pressure forces molten metal to escape, resulting in flash.
- Improper Temperature Control: Operating temperatures exceeding recommended ranges are a significant cause of flash. Failure to adjust casting design factors alongside excessive temperatures often leads to this defect.
- Elevated Metal Pressure: Exceeding the recommended maximum static pressure can exacerbate shrink porosity, increasing internal pressure and forcing molten metal to flow out, causing flash on casting surfaces.
- Incorrect Machine Setup: Imbalanced adjustments in machine setup can lead to mechanical distortions. Subsequent inaccuracies in processing, such as misalignment of tie bars, platens shoes, and toggle links, contribute to flash formation.
Effects of Flash:
- Safety Concerns: Accumulation of flash at breach points in the die can lead to safety hazards, especially in large-scale manufacturing processes where flash expulsion can cause burns to skin and damage to machinery.
- Dimensional Problems: Flash buildup under slides can prevent proper seating, resulting in dimensional distortions that affect the desired size of the final product.
- Component Damage: Flash formation can cause damage to metal/alloy components in the final product. Parts such as horn pins, slide carriers, keyways, and cores may experience ruptures or other forms of damage.
- Increased Contamination: The accumulation of flash and debris under the dies can lead to contamination with other impurities, rendering the material unsuitable for remelting or reuse.
- Reduced Productivity: Over time, flash accumulation can significantly decrease productivity and product quality. Restarting operations becomes more time-consuming and labor-intensive as extensive flash buildup requires additional effort to address.
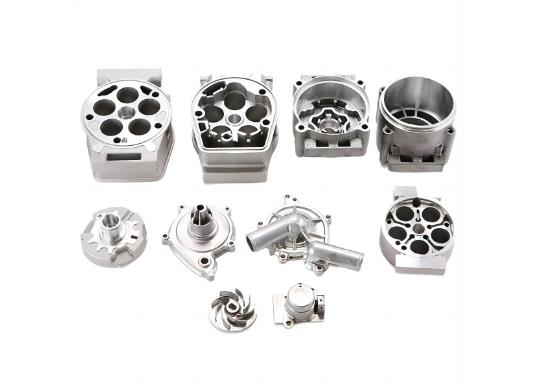
Prevention of Die Cast Flash:
- Optimal Temperature Control: Maintaining the recommended operating temperature range is critical to preventing flash formation. For aluminum and magnesium, the range is (1200°F – 1250°F) ± 10°F or (650°C – 675°C) ± 6°C, while for zinc it’s 800°F ± 5°F or 426°C ± 3°C. Deviations from these ranges should only occur after adjusting dependent parameters, but the key challenge lies in ensuring stable temperature conditions.
- Precise Machine Setup: Proper machine configuration is essential for controlling processing defects, including flash. Balancing tie bar strain based on applied load helps achieve accurate adjustments. Any deformities, roughness, wear, loose connections, or excessive tear must be avoided to optimize casting molds.
- Controlled Metal Pressure: Keeping static metal pressure at a minimum helps reduce flash formation. Recommended limits vary, such as 3000psi – 5500psi for aluminum, 3000psi – 4000psi for magnesium, and 2000psi – 4000psi for zinc. However, pressure adjustments may differ between machines, necessitating a thorough review to determine the appropriate setting.
- Efficient Cooling System Design: Accurate thermal analysis and proper placement of cooling systems prevent die expansion and ensure even temperature distribution across the casting. Detailed mold sizing considerations are necessary for a proper fit. Regular maintenance also helps minimize flash occurrence.
- Slag Bag Exhaust Integration: Advanced design concepts incorporate slag bag exhaust integration to increase sealing surface area for low-temperature and low-pressure casting. This reduces the occurrence of flying flash during the process and also reduces energy consumption, leading to cost savings without compromising quality.
Yongzhu Metal has discovered through extensive die-casting experience that typically only 20% of the accumulated flash is recoverable. Drop me an email with your ideas, and I’ll get back to you swiftly!