Aluminum die casting is widely used in numerous industries, offering precision, strength, and lightweight properties ideal for high-volume manufacturing.
It requires careful process management to ensure quality and minimize costs.
In this article, we’ll explore essential safety guidelines, machine considerations, industry applications, common casting defects, and, importantly, 10 proven strategies to optimize costs without sacrificing quality.
Helping you and your vendors have better solutions
Safety in Aluminum Die Casting
Die casting processes involve high temperatures, pressurized metal, and complex machinery. Therefore, maintaining rigorous safety protocols is essential.
- Implement Comprehensive Safety Measures: Establish safety and health education programs and create thorough inspection standards. This reduces risk and prepares workers for unexpected issues.
- Use Advanced Safety Features: Equip die-casting machines with safety interlocks, lockouts, and emergency stop functions. When operators enter the protected area, automatic interlocks prevent machine startup, safeguarding against accidents.
- Proper Safety Gear: Equip workers with personal protective equipment (PPE) such as heat-resistant gloves, face shields, and aluminized aprons. Regular inspection of safety equipment is also vital to worker protection.
- Routine Inspection of Machinery: Regular checks on die-casting machines help identify potential malfunctions or leaks, preventing accidents before they occur. Ensure machinery is up-to-date and functional.
By following these protocols, manufacturers can maintain a safe environment, reduce the risk of workplace injuries, and boost productivity.
Aluminum Die Casting Machines
Die casting is generally performed using hot and cold chamber machines, each suited to specific metals and project requirements.
Selecting the correct machine and optimizing its use is critical for cost control and production efficiency.
- Hot Chamber Die Casting: Ideal for low-melting-point alloys, this machine type uses an internal molten metal reservoir, reducing cycle times and improving efficiency. Its quick cycles are suitable for zinc or magnesium but not aluminum.
- Cold Chamber Die Casting: This type is commonly used for aluminum due to its higher melting point. It has an external furnace, increasing cycle time but maintaining material integrity. Though initially more costly, cold chamber machines optimize output for aluminum products.
- Low-Pressure Casting Equipment: These machines use compressed air to feed molten metal into molds, minimizing oxidation. Though suited for specific types of aluminum castings, low-pressure equipment offers precise control over molten flow, reducing defects.
Optimizing machine parameters, such as injection speed and cooling time, further enhances casting quality and minimizes energy consumption.
Applications of Aluminum Die Casting Across Industries
The versatility of die-casting makes it invaluable across numerous sectors. Some primary applications include:
- Automotive Industry: Lightweight aluminum castings are crucial for components like engine brackets, heat sinks, and gearbox housings, enhancing fuel efficiency.
- Electronics Industry: Die-cast aluminum frames and heat sinks offer durability and thermal conductivity, essential for electronics.
- Aerospace Industry: Aluminum castings provide strength and temperature resistance for aviation components, including engine parts and structural supports.
- Construction and Furniture Industries: Durable, lightweight castings are used in building frames, furniture brackets, and knobs, benefiting from aluminum’s corrosion resistance.
- Medical Equipment: Complex and lightweight aluminum parts support equipment such as dialysis machines and surgical tools, meeting stringent hygiene and quality standards.
Understanding these applications helps highlight the benefits of optimizing aluminum die-casting processes, especially for industries where high strength and intricate designs are essential.
Searching for High-Quality for Cast Aluminum Parts?
You’ve come to the right place! Yongzhu Casting is a certified die casting manufacturer with over 20 years of expertise in the industry.
We have successfully completed numerous die casting projects for Aluminum casting parts, particularly in your industry.
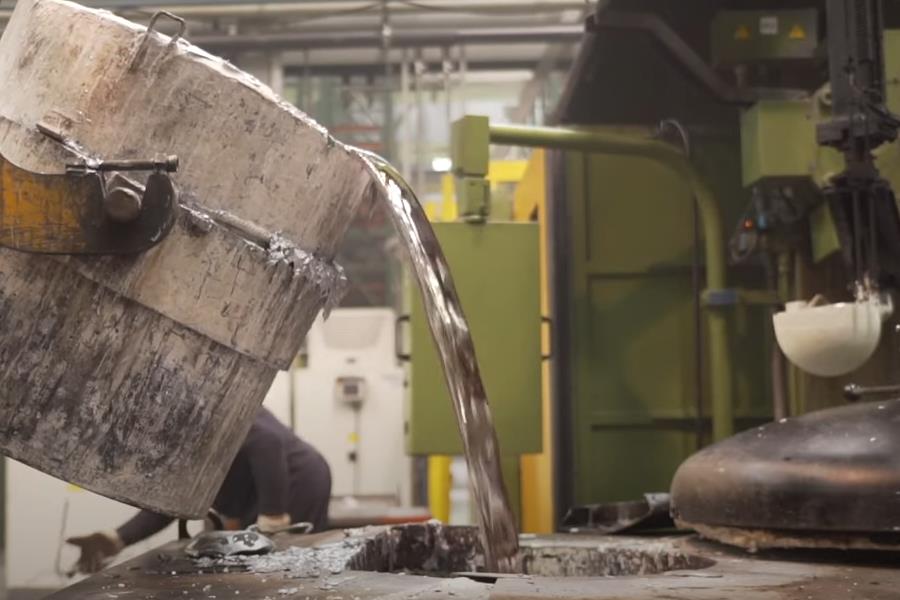
Zhejiang Yongzhu Casting Technology Co., Ltd.
Location: Zhejiang, Shaoxing
Company type: Manufacturing
Year Founded: 2004
Main Products: Aluminium die casting, Mold Making, Die Casting, Sand Casting, Gravity Casting
Leading Chinese producer Yongzhu Casting is formerly known as Hangzhou Higer Metal Products Co., Ltd., was established in 2004.
With 20 years of experience in the industry, we are a specialized manufacturer in Aluminum casting and Machining.
Our products are widely used in various applications such as Automotive, Energy, Lighting, Medical, Home Furnishings, Machinery & Equipment etc. Below is one of our products.
It’s worth mentioning that the evolution of rapid logistics has transformed how industries approach purchasing. Aluminum casting orders can now be sourced from overseas suppliers efficiently.
For instance, working with YONGZHU CASTING, you can inquire, order, and even find better value than your local options—all while maintaining assured quality.
Design Review & DFM Support
Our professionals will evaluate your designs and provide suggestions for cost savings. Additionally, we offer Design for Manufacturing (DFM) assistance and conduct mold flow analyses to facilitate efficient production.
State-of-the-Art Manufacturing Equipment
Our facility is equipped with advanced hot-chamber and cold-chamber die casting machinery for aluminum and zinc production.
We also utilize high-precision CNC machines in a temperature-controlled workshop, featuring 3-Axis, 4-Axis and 5-Axis setups to manage any project you have.
Rigorous Quality Control Measures
Our dedicated quality control team ensures that all parts meet the highest standards of quality and consistency. We employ high-accuracy measurement instruments, including CMM, spectrometers, and X-ray detectors.
Comprehensive Surface Treatment Options
We provide a variety of surface finishing techniques for your precision die casting components. Our in-house services include cleaning, polishing, anodizing, shot blasting, and painting.
Flexible Project Acceptance
While larger manufacturers often shy away from low-volume projects, and smaller ones may struggle with quality, Yongzhu Casting stands apart. We prioritize customer satisfaction and willingly accept high-mix, low-volume projects like yours.

Common Aluminum Die Casting Defects and How to Prevent Them
Quality control in die casting is essential to avoid defects that compromise structural integrity and performance. Here are common defects and prevention techniques:
- Shrinkage Defects: Occur when molten aluminum shrinks during solidification, creating internal voids.
- Prevention: Use risers for consistent molten metal flow, modify mold geometry, or adjust machine settings to cool hotspots.
- Gas Porosity: Small gas bubbles trapped in the casting weaken the structure.
- Prevention: Improve mold ventilation, reduce gas content in molten metal, and optimize injection speed.
- Mold Material Defects: Issues like fusion, swells, and cracks can arise from improper mold handling or inadequate materials.
- Prevention: Use high-refractoriness molds, adjust pouring temperatures, and apply coatings for added mold protection.
- Metallurgical Defects: High temperatures can weaken the casting, causing cracks.
- Prevention: Optimize mold design and apply cooling mechanisms to prevent hot tears or cracks.
- Pouring Defects: Misruns, flashes, and warping often occur due to incorrect pouring speed or temperature.
- Prevention: Maintain optimal pouring temperatures and improve mold design to allow even molten flow.
These preventive measures ensure high-quality casting with minimal rejects, reducing rework and material waste.
Ten Cost-Saving Strategies for Aluminum Die Casting
Ensuring quality while reducing costs is possible with these 10 strategies, which cover material, tooling, production, and post-casting processes.
- Optimize Material Usage: Select materials based on project requirements to minimize waste. For instance, using thinner walls in low-stress areas reduces the total volume needed.
- Reduce Tooling Costs: Use reusable molds and modular mold designs for similar products, reducing the need for new tooling.
- Choose the Right Machine for Each Job: Cold chamber machines are best for high-melting-point metals like aluminum, while hot chamber machines are more economical for low-melting alloys.
- Invest in Mold Flow Analysis: CAD simulations help identify and resolve potential design flaws early, saving costs in trial runs.
- Incorporate Risers and Chills: Control shrinkage defects by using risers and internal chills, ensuring complete filling and cooling, which prevents rework.
- Reduce Cycle Time: Optimize machine parameters to shorten injection, cooling, and resetting times, reducing production costs.
- Standardize Part Design: Uniform designs lower manufacturing complexity and setup time, especially useful for high-volume orders.
- Adopt Multi-Cavity Molds: Producing multiple parts per cycle reduces cycle times and maximizes machine output, essential for large orders.
- Leverage Core and Cavity Modifications: Minor changes to mold cores can produce variant designs, saving time and tooling costs.
- Improve Maintenance and Machine Efficiency: Regular machine maintenance reduces downtime and ensures consistent output quality.
These techniques are proven methods for manufacturers to cut costs without sacrificing quality, making die casting a more efficient process for large and small projects alike.
Conclusion
In this comprehensive guide, we’ve examined key aspects of aluminum die casting, including safety rules, machinery choices, industry applications, and defect prevention.
These insights are essential for ensuring high-quality production and maximizing profitability. By implementing the 10 cost-saving strategies outlined above, manufacturers can reduce waste, increase efficiency, and deliver better outcomes across various industries that rely on die-cast parts.
This knowledge empowers manufacturers to optimize their processes, ensuring the reliability and economic viability of aluminum die casting.
Aluminum casting orders can now be sourced internationally with ease, especially from YONGZHU CASTING, where you can inquire and place orders confidently—often at a better value than local suppliers, with quality equally assured.