Low Pressure Die Casting (LPDC) is an advanced metal casting technique that leverages controlled low-pressure environments to mold and shape molten metal into complex, precise components.
The LPDC Process Explained
The LPDC process begins with a preheated permanent steel mold, which is coated with a release agent to prevent the molten metal from adhering. The mold is sealed, and the furnace containing the alloy is pressurized.
The molten metal is transferred to a shot chamber and introduced into the mold cavity under controlled low pressure, typically between 1 and 2 bars.
This method minimizes turbulence and prevents gas entrapment, ensuring a high-quality cast. Once the metal has solidified, the casting is removed, and any excess material is trimmed.
This reduces porosity and minimizes the need for additional finishing processes, resulting in parts with excellent surface finishes and structural integrity.
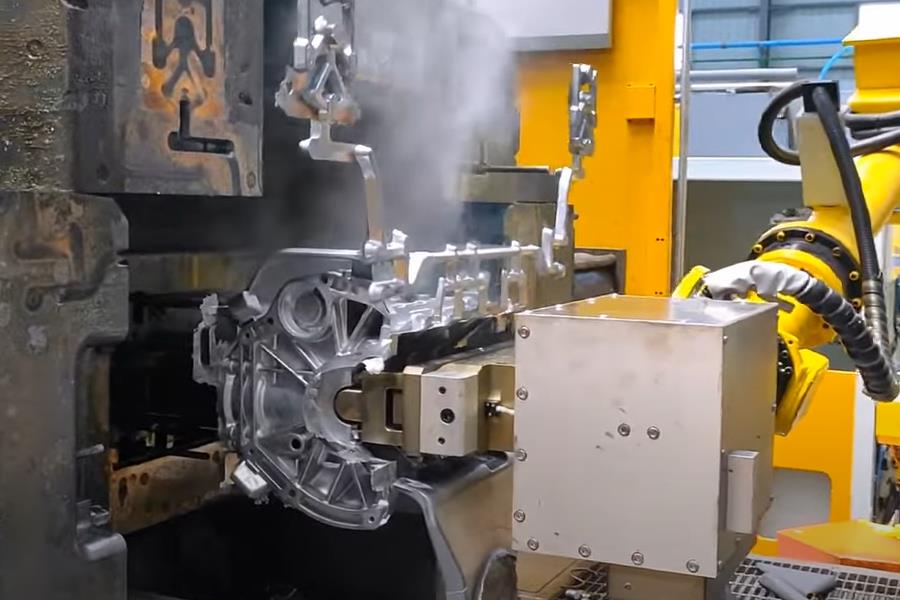
Benefits and Drawbacks of LPDC
Advantages of LPDC
- High-Quality Outputs: LPDC produces parts with minimal porosity and high density, leading to excellent surface finishes that often eliminate the need for secondary operations.
- Precision and Consistency: The low-pressure environment ensures accurate dimensional control and repeatability, making it ideal for producing high-precision components.
- Cost Efficiency: Reduced scrap rates and minimal post-processing translate to significant cost savings.
- Eco-Friendly: LPDC generates less waste and fewer emissions compared to other casting methods.
Disadvantages of LPDC
- Material Limitations: LPDC is best suited for aluminum, magnesium, and zinc alloys, which limits its applicability for some projects.
- High Initial Tooling Costs: The upfront investment in tooling can be substantial, making it less economical for small production runs.
- Slower Production Speed: LPDC processes are generally slower than high-pressure die casting (HPDC), which can affect production timelines.
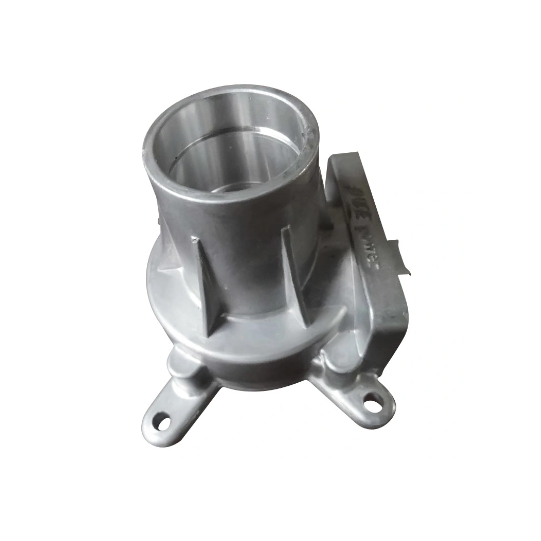
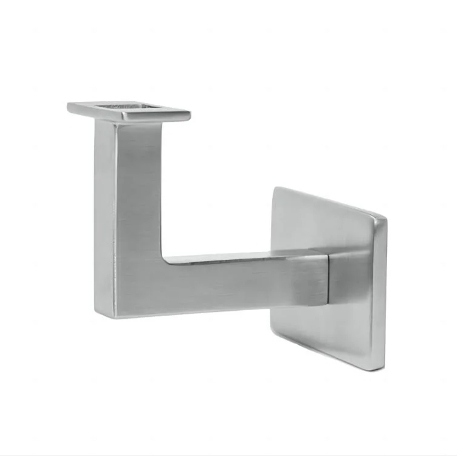
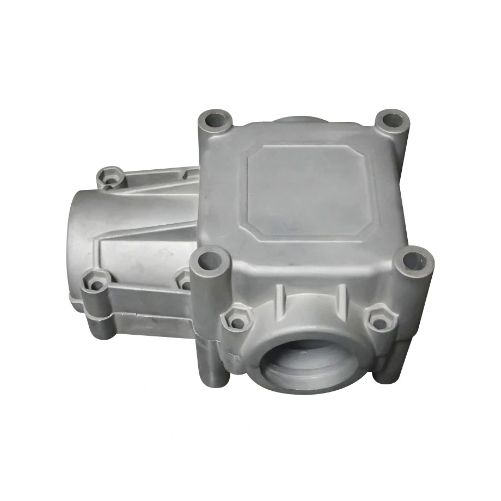
Comparing LPDC and HPDC
Aspect | LPDC (Low Pressure Die Casting) | HPDC (High Pressure Die Casting) |
---|---|---|
Pressure Application | Utilizes low pressure (1-2 bars) for high precision and excellent surface finishes. | Employs high pressure (up to 700 bars) for faster production, often requiring more post-processing. |
Material Compatibility | Ideal for lightweight alloys such as aluminum and magnesium. | Can accommodate a broader range of materials, including heavier metals. |
Cost Considerations | Higher initial tooling costs but long-term cost efficiency due to lower scrap rates and reduced secondary processing. | Lower initial tooling costs but higher operational expenses due to more extensive post-processing requirements. |
When to Avoid LPDC
LPDC may not be suitable for projects that:
- Require Extremely Fast Production Cycles: LPDC is slower compared to other methods like HPDC.
- Involve Materials Not Compatible with LPDC: If the project requires materials such as steel or certain exotic alloys, alternative casting methods should be considered.
- Are Highly Cost-Sensitive:
other casting processes like sand casting might be more cost-effective if precision is not critical.
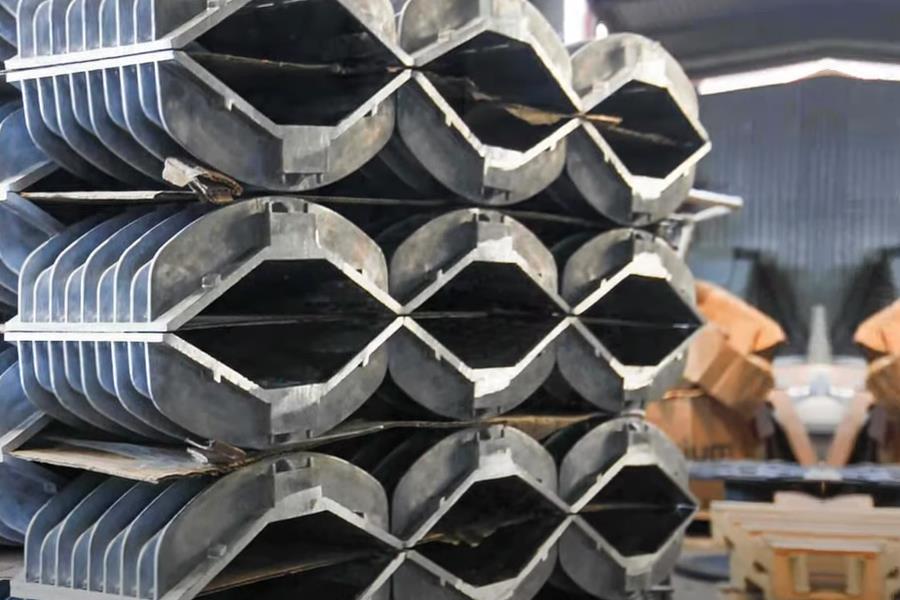
Applications of Low Pressure Die Casting
Industry | Applications |
---|---|
Automotive Industry | Engine components such as cylinder heads and transmission parts, enhancing performance and durability. |
Aerospace Industry | Lightweight, robust structural elements that contribute to fuel efficiency and safety in aircraft design. |
Electronics Industry | Manufacturing heat sinks and precision components for devices, ensuring efficient heat dissipation and long-lasting performance. |
Other Industries | Industrial machinery, lighting fixtures, renewable energy systems, medical devices, and marine components, valued for precision and adaptability. |
Contact us today to discuss your project needs and receive a quote, you can trust us to deliver exceptional castings that meet your requirements.