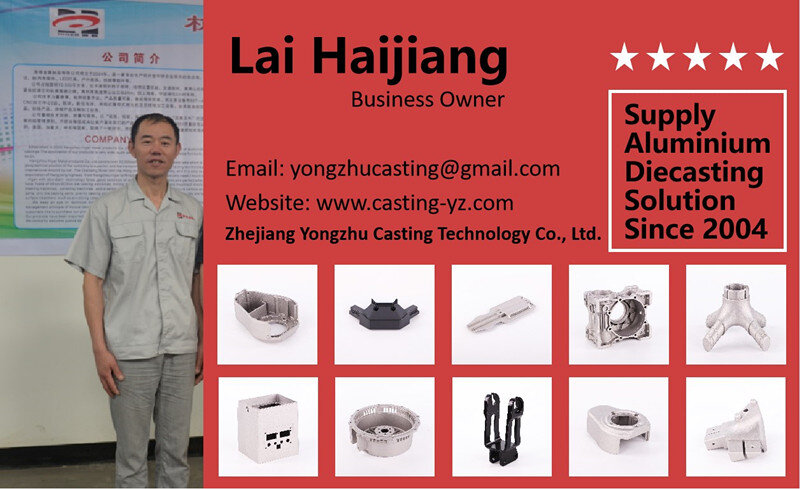
Hi, I’m Lai Haijiang, owner of Yongzhu Die Casting since 2004. Passionate about aluminum die-casting? Let’s chat! We craft custom aluminum parts for various industries and offer both manufacturing and wholesale services. Interested in being our overseas agent? Drop me an email with your ideas, and I’ll get back to you swiftly!
Introduction to Aluminum Casting
Aluminum casting is an intricate and sophisticated method of forming aluminum into a wide array of products. This guide provides an in-depth exploration of the aluminum casting process, ensuring a comprehensive understanding for both beginners and experts in the field.
Understanding the Basics of Aluminum Casting
Aluminum Casting Process: The process of aluminum casting involves pouring molten aluminum into a mold to create a desired shape. This technique is favored for its versatility, efficiency, and the superior properties of the end product.
Types of Aluminum Casting:
- Die Casting: A high-pressure method suitable for mass production.
- Permanent Mold Casting: Reuses molds for multiple castings.
- Sand Casting: Utilizes sand molds for complex geometries.



Step-by-Step Guide to Aluminum Casting
1. Preparing the Aluminum: Select high-quality aluminum alloys for casting. Preheat the aluminum to its melting point, typically between 660.3°C (1220.5°F) and 760°C (1400°F).
2. Creating the Mold: Design the mold based on the final product’s specifications. For intricate designs, consider using cores to create internal cavities.
3. Melting and Pouring: Melt the aluminum in a crucible and pour it into the mold. Ensure a controlled pour to minimize air entrapment and defects.
4. Cooling and Solidification: Allow the aluminum to cool and solidify in the mold. The cooling rate can impact the microstructure and properties of the casting.
5. Removal and Finishing: Once cooled, remove the casting from the mold. Perform finishing processes like sanding, grinding, or machining to achieve the desired surface finish and dimensions.
Advanced Techniques in Aluminum Casting
A. Vacuum Casting: Reduces defects by casting in a vacuum environment.
B. Low-Pressure Casting: Ideal for producing high-quality castings with improved mechanical properties.



Quality Control in Aluminum Casting
Implement rigorous quality control measures at each stage of the casting process. This includes inspecting the raw materials, monitoring the melting and pouring temperatures, and conducting post-casting inspections for defects.
Environmental Considerations and Sustainability
Strive for sustainability in aluminum casting by optimizing energy consumption, recycling aluminum scrap, and employing eco-friendly manufacturing practices.
Aluminum Casting Applications
Aluminum castings are extensively used in various industries, including automotive, aerospace, and consumer electronics, due to their lightweight, durability, and corrosion resistance.
Conclusion
This comprehensive guide to aluminum casting covers every aspect of the process, from the basics to advanced techniques. By adhering to best practices and focusing on quality and sustainability, we can achieve superior aluminum castings for a wide range of applications.