Aluminum is extensively utilized in the manufacturing, cookware, construction, and transport sectors due to its inherent light weight and corrosion-resistant characteristics.
Nonetheless, certain applications demand an additional layer of protection.
Manufacturers and surface finishing providers use various aluminum finishing techniques, including Alodining, anodizing, polishing, and powder coating.
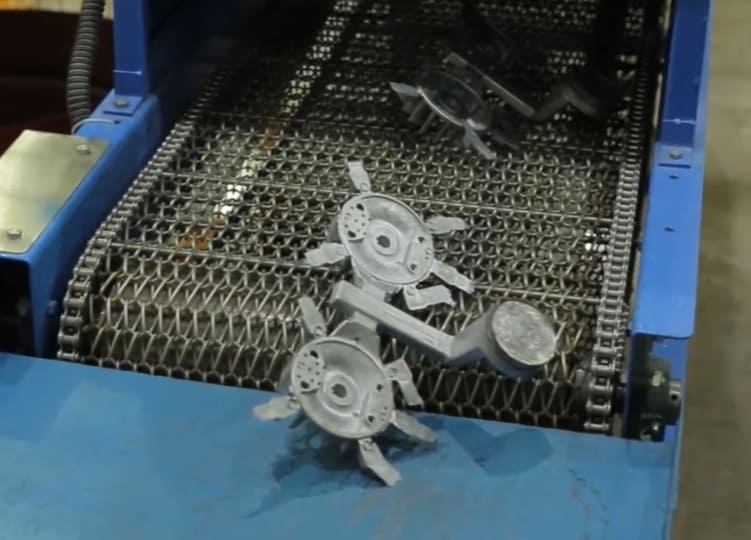
YongZhu Casting Supply Better Solution for You.
Alodine, being a passivation process, is ideal for internal components of aluminum projects, whereas anodizing provides the necessary durability and protection for external parts.
What is Alodining?
Alodining is a chemical process that forms a protective layer on aluminum.
The aluminum part is immersed in an Alodine solution at room temperature, creating a coating that adheres to the surface and remains effective for many years without needing reapplication.
This chemical film requires minimal technical expertise and is cost-effective.
It allows aluminum to retain its thermal and electrical conductivity, making it ideal for parts that need to be electrically grounded.
Aspect | Details |
---|---|
Process Temperature | Conducted at room temperature |
Technical Expertise | Requires minimal technical expertise |
Cost | More cost-effective compared to other coating processes |
Durability | Provides a long-lasting protective layer without the need for reapplication |
Conductivity | Maintains aluminum’s thermal and electrical conductivity |
Applications | Suitable for parts requiring electrical grounding |
Advantages of Alodine
- Cost-Effective: Relatively lower-cost process.
- Corrosion and Scratch Protection: Offers improved protection.
- Conductivity: Maintains good electrical and thermal conductivity.
- Paint-Friendly: Allows painting without a primer.
- Minimal Cleanup: Cleanup is unnecessary after application.
- Dimensional Stability: Does not alter the dimensions of the parts.
- Low Skill Requirement: Requires minimal technical expertise.
Disadvantages of Alodine
- Durability Issues: The coating can be removed easily and may have micro-defects.
- Environmental Concerns: Disposal of spent tank contents is not environmentally friendly.
- Health Risks: Contact with Alodine can cause itching or rashes.



What is Anodizing?
Anodizing is an electrolytic process that forms a protective, corrosion-resistant layer on aluminum by following the principles of electrochemistry.
The aluminum part is immersed in an electrolyte solution, and electricity is applied.
Aluminum serves as the anode, and the acid releases oxygen ions, transforming the aluminum surface into aluminum oxide. This coating has enhanced durability and corrosion resistance properties.
Anodized aluminum has many applications in cookware, medical, automotive, aviation, and military industries. It is also used in manufacturing pharmaceutical and medical equipment, such as sterilizers.
Aspect | Details |
---|---|
Electrolyte Solution | Typically involves sulfuric acid, chromic acid, or phosphoric acid solutions. |
Color Options | Anodized aluminum can be dyed in various colors, enhancing customization. |
Surface Properties | The anodizing process can increase surface hardness and wear resistance. |
Environmental Impact | Anodizing is generally more environmentally friendly compared to other coating processes, producing fewer hazardous by-products. |
Maintenance | Anodized surfaces require minimal maintenance and are easy to clean. |
Cost Efficiency | Though the initial process may be more costly, the longevity and durability of anodized parts can lead to cost savings over time. |
Advantages and Disadvantages of Anodizing
Advantages | Disadvantages |
---|---|
Increased Durability: Creates a tough, protective layer resistant to dents, wear, corrosion, and scratches. | Cost: More expensive than bare aluminum due to the labor-intensive and time-consuming process. |
Enhanced Aesthetics: Available in various colors with a uniform, smooth finish that resists discoloration and fading. | Limited Thickness: The oxide layer’s thickness is limited, making it less resistant to certain forms of damage. |
Corrosion Resistance: Naturally resistant to air and water, ideal for moisture-exposed applications. | Welding Challenges: Anodized aluminum is more challenging to weld due to its non-conductive oxide layer. |
Alodine vs. Anodizing – What is the Difference?
Both Alodining and anodizing enhance aluminum’s corrosion-resistant properties.
If your primary goal is to protect aluminum parts from corrosion without any technical requirements or budget constraints, either method can be chosen.
Key Differences and Design Considerations: Alodining vs. Anodizing
Aspect | Alodining | Anodizing |
---|---|---|
Cost | Relatively inexpensive, allows aluminum to be painted. | Requires specialized equipment and skilled labor, making it more expensive. |
Durability | Offers a thinner protective film. | Provides a uniform coat with enhanced durability and corrosion resistance. |
Application | Serves as a primer for paint. | Preferred for applications requiring a strong, wear-resistant surface. |
Safety | Requires advanced safety measures due to chemicals. | Requires advanced safety measures due to electricity and chemicals. |
Production Volume | Suitable for small-sized orders or cheaper components. | Ideal for large-scale manufacturing. |
Film Thickness | Creates a thinner film, impacting designs requiring tight tolerances. | Creates a thicker oxide layer. |
Mechanical Damage | Less protection against mechanical damage. | Provides better protection against mechanical damage. |
Aesthetics | Available only in brown or clear. | Can be dyed in various colors. |
Sustainability | Similar environmental impacts; powder coating may be more sustainable. | Similar environmental impacts; powder coating may be more sustainable. |
Conductivity | Maintains good electrical and thermal conductivity. | Has ceramic-like properties, making it a poorer conductor of heat and electricity. |
Conclusion
Alodine and anodizing are essential aluminum finishing techniques, each offering unique benefits and applications.
Alodine is cost-effective and suitable for internal parts requiring conductivity and paintability.
In contrast, anodizing provides a durable, corrosion-resistant surface ideal for exterior parts exposed to harsh conditions.
Choosing the right method depends on the specific requirements of the project, including budget, durability, aesthetics, and environmental considerations.
Contact us today to discuss your project needs and receive a quote, you can trust us to deliver exceptional castings that meet your requirements.