As an aluminum die casting manufacturer, I can assure you that producing high-quality aluminum castings is a meticulous process.
From creating a robust mold to the final finishing touches, each step is essential to ensure we deliver a product that meets industry standards and customer expectations.
Here, I’ll walk you through the step-by-step process of how we create aluminum die castings.

Mold Preparation
The first step in making aluminum die-cast parts is mold preparation, also known as tooling. The mold’s design dictates the dimensions, shape, and quality of the final casting.
Using high-strength materials for the mold is crucial, as they must withstand repeated exposure to molten aluminum at high temperatures.
For accuracy, we rely on 3D CAD/CAM systems to design the mold, optimizing it for precise production. Each mold has two halves: the stationary half, mounted on the fixed plate, and the ejector half, fixed to a movable plate.
These halves are separated by a parting line, carefully positioned to prevent material from seeping out, which could cause defects.
Gating System Creation
The gating system is the channel through which molten aluminum flows into the mold cavity.
It includes components like the sprue, runner, and ingate, all designed to control the flow, minimize heat loss, and reduce turbulence.
Proper gating design ensures a smooth, uniform flow of metal, directly impacting the casting’s quality.
Lubricating the Mold Surface
Before casting, the mold surface must be lubricated to prevent the aluminum from sticking.
The lubricant acts as a release agent, allowing the casting to separate smoothly and reducing wear on the mold itself.
Too much lubricant, however, can result in porosity and poor surface finish, so we use just the right amount for optimal results.
Clamping the Mold in the Die Casting Machine
Next, we securely clamp the mold halves in the die casting machine.
During the casting process, the machine applies enough pressure to keep the mold tightly closed, preventing any leaks or misalignment that could affect the casting’s integrity.
Die casting machines vary in clamping force, ranging from 25 to 3,000 tons, depending on the size of the casting.
Injecting the Molten Aluminum
Molten aluminum is injected into the mold, which can be done through two methods: hot chamber or cold chamber die casting.
- Hot Chamber Die Casting: In this method, the machine uses a gooseneck system, where molten aluminum is drawn directly into the chamber and injected into the mold at high pressure. This technique is ideal for low melting point alloys.
- Cold Chamber Die Casting: Here, molten aluminum is ladled into a cold chamber before being forced into the mold cavity. This method works well with high melting point metals like aluminum.
Solidifying the Casting
Once the mold cavity is filled, we let the aluminum cool and solidify inside the mold. Proper cooling is essential to prevent warping and ensure the casting’s strength and accuracy.
Removing the Casting
After solidification, the die-cast part is removed from the mold.
At this point, we apply lubricant to prepare the mold for the next casting cycle, ensuring consistency and efficiency for high-volume production.
Trimming Excess Metal
Once the casting has cooled, we remove any excess metal, including sharp edges and seams. Trimming ensures that the casting meets precise specifications and has a smooth, polished appearance.
Machining for Precision
Machining is a critical step for achieving intricate details or tighter tolerances that aren’t possible with casting alone.
Using CNC machines, we can create complex geometries, adding precision and refinement to each part. This step is particularly vital for customized or complex applications.
Finishing Touches
The finishing stage enhances the durability and appearance of the casting. Some common finishing options include:
- Powder Coating: Applied as a dry powder and heated, providing a flexible, durable finish.
- Chemical Film: A chromate coating applied to protect aluminum surfaces, often used to prevent corrosion.
- Anodizing: This electrochemical process creates a corrosion-resistant oxide layer on the aluminum, making it more durable and aesthetically pleasing.
Searching for High-Quality for Cast Aluminum Parts?
You’ve come to the right place! Yongzhu Casting is a certified die casting manufacturer with over 20 years of expertise in the industry. We have successfully completed numerous die casting projects for Aluminum casting parts, particularly in your industry.
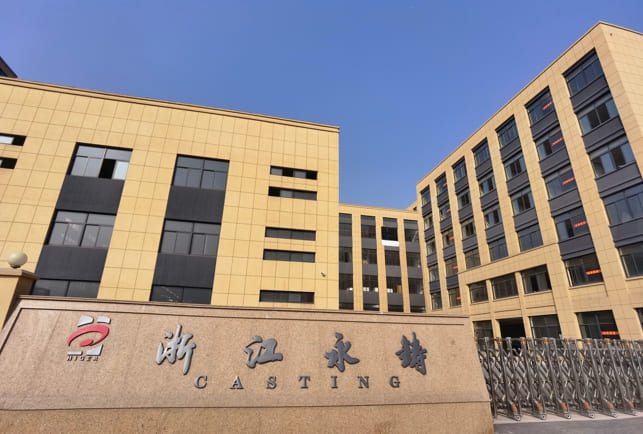
Zhejiang Yongzhu Casting Technology Co., Ltd.
Main Products: Aluminium die casting, Mold Making, Die Casting, Sand Casting, Gravity Casting
Leading Chinese producer Yongzhu Casting is formerly known as Hangzhou Higer Metal Products Co., Ltd., was established in 2004.
With 20 years of experience in the industry, we are a specialized manufacturer in Aluminum casting and Machining. Our products are widely used in various applications such as Automotive, Energy, Lighting, Medical, Home Furnishings, Machinery & Equipment etc. Below is one of our products.
Design Review & DFM Support
Our professionals will evaluate your designs and provide suggestions for cost savings. Additionally, we offer Design for Manufacturing (DFM) assistance and conduct mold flow analyses to facilitate efficient production.
State-of-the-Art Manufacturing Equipment
Our facility is equipped with advanced hot-chamber and cold-chamber die casting machinery for aluminum and zinc production.
We also utilize high-precision CNC machines in a temperature-controlled workshop, featuring 3-Axis, 4-Axis and 5-Axis setups to manage any project you have.
Rigorous Quality Control Measures
Our dedicated quality control team ensures that all parts meet the highest standards of quality and consistency. We employ high-accuracy measurement instruments, including CMM, spectrometers, and X-ray detectors.
Comprehensive Surface Treatment Options
We provide a variety of surface finishing techniques for your precision die casting components. Our in-house services include cleaning, polishing, anodizing, shot blasting, and painting.
Flexible Project Acceptance
While larger manufacturers often shy away from low-volume projects, and smaller ones may struggle with quality, Yongzhu Casting stands apart. We prioritize customer satisfaction and willingly accept high-mix, low-volume projects like yours.

Conclusion
We’ve just explored each phase of the aluminum die casting process, from mold preparation to final finishing.
While this process may seem intricate, it’s actually a seamless, efficient way to produce high-quality aluminum parts on a large scale.
With the right tools, materials, and expertise, aluminum die casting can yield outstanding results tailored to the unique needs of every industry.