How Aluminum Street Lights Adapt to the Environment?
Aluminum alloy has become a preferred material for streetlights due to its strength, corrosion resistance, and lightweight properties.
What’s more impressive is its ability to withstand extreme weather conditions such as high winds, heavy snow, and corrosive coastal air.
This article explores how aluminum alloy streetlight poles, brackets, and housings perform in these harsh environments and highlights the technological advances that ensure their durability and reliability.
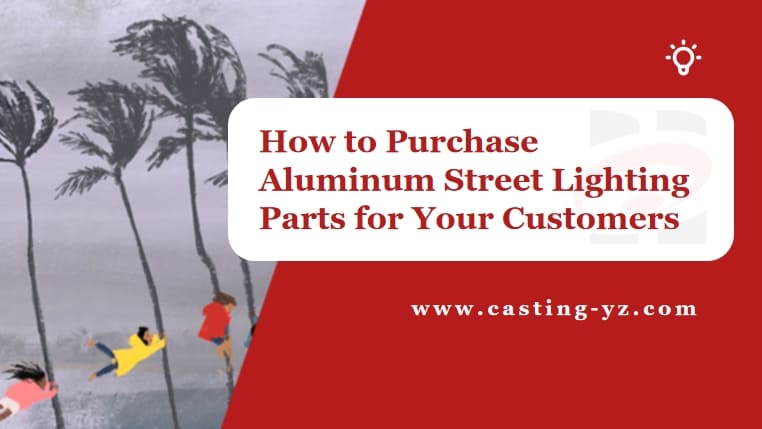
How do aluminum street light poles perform in extreme weather?
Streetlights are essential infrastructure, but their performance can be compromised when exposed to extreme weather conditions.
Areas prone to typhoons, hurricanes, or heavy snow must rely on materials that can withstand these challenges.
In terms of wind resistance, aluminum alloy streetlights perform well due to their light weight combined with strength.
Aluminum poles and brackets are designed to endure wind speeds of up to 150 mph, which is common in regions affected by typhoons and hurricanes.
- Windy Weather Conditions: Typhoons, Hurricanes, and Extreme Storms
- Aluminum alloy streetlight poles are built to withstand the impact of high winds. Their lightweight construction helps prevent the bending or breaking of poles under intense storm conditions.
- By reinforcing the joints and using aerodynamic designs, manufacturers ensure the poles are resistant to wind-induced stress.
- Additionally, aluminum alloys have a high strength-to-weight ratio, which makes them ideal for such conditions.
- Safety Standards for Different Wind Conditions
- Different regions have unique safety standards depending on their exposure to extreme weather.
- For instance, cities in coastal regions or areas prone to hurricanes, such as Japan or the Philippines, require streetlights that can endure higher wind speeds.
- These locations implement stricter regulations, ensuring the materials and structures used are capable of withstanding powerful storms.
What design considerations are needed for coastal and wet environments?
Coastal areas face unique challenges due to salty air, which can lead to rapid corrosion if the materials are not appropriately treated.
This is where aluminum alloys shine—they naturally offer resistance to corrosion, making them a suitable choice for coastal regions.
However, additional surface treatments like anodizing and powder coating are commonly used to enhance their durability further.
- Corrosion Resistance in Coastal Areas
- For example, anodizing increases aluminum’s natural oxide layer, providing an additional barrier against corrosion. For more extreme cases, powder coating and electrophoretic coatings are applied to give aluminum alloy components a protective finish.
- Special Needs for Humid Environments
- Coatings like polyurethane are used to further enhance the durability of the streetlight poles, ensuring that they maintain their integrity over time despite the harsh environmental conditions.
How Aluminum Alloys withstand High and Low Temperatures?
Streetlights are exposed to a wide range of temperatures, from scorching heat in desert areas to freezing cold in northern climates.
The ability of aluminum alloy to handle these extremes is a significant advantage, but how does the material perform in these conditions?
- Handling High Temperatures
- Aluminum alloy’s ability to withstand heat is another reason for its widespread use. In hot climates, such as the Middle East or southern parts of the U.S., streetlights are subjected to extreme temperatures.
- Aluminum alloys, particularly those with specific alloying elements, can maintain their strength and performance at temperatures that exceed 100°C (212°F) without risk of structural failure. This makes them perfect for areas where the sun beats down relentlessly.
- Adapting to Cold Climates
- In cold regions, such as parts of Russia, Canada, or northern Europe, aluminum alloys perform equally well. The material’s low coefficient of expansion means that it doesn’t contract or expand too dramatically in freezing temperatures.
- However, to ensure optimal performance in these regions, the aluminum alloy formulation may be adjusted to improve its impact resistance, reducing the risk of cracking under freezing conditions.
How to improve the durability of streetlights?
One of the key reasons aluminum alloy streetlights are able to stand up to the challenges posed by extreme weather is their surface treatment.
Beyond just providing an aesthetic finish, these treatments play a crucial role in ensuring long-lasting performance.
- Anodizing, Electrocoating, and Powder Coating
- Anodizing: Anodizing is a process that creates a thick, protective oxide layer on the surface of aluminum. This process enhances the material’s natural corrosion resistance and also allows for a variety of color options. The anodized layer is durable and ensures the longevity of the streetlight in challenging environments.
- Electrophoretic Coating (e-coating): This method provides a smooth, uniform coating that further protects aluminum alloys from environmental wear and corrosion. It is particularly effective in coastal areas where the air contains high levels of salt.
- Powder Coating: Powder coating involves applying a dry powder to the surface of aluminum components and then curing them under heat. This coating not only provides a strong, corrosion-resistant finish but also adds a protective barrier against UV damage and environmental contaminants.
These surface treatments are crucial for the longevity and performance of aluminum alloy streetlights, ensuring that they can withstand harsh weather conditions without deteriorating over time.
What are the different standards and needs for street lighting?
Different countries have their own standards when it comes to the design, durability, and safety of streetlights.
Understanding these regional differences is essential for manufacturers who wish to supply streetlight components to various markets.
- Standards in Different Regions
- China: Streetlight regulations in China emphasize energy efficiency and environmental sustainability. Aluminum alloy components must meet strict corrosion resistance requirements, especially in coastal cities.
- United States: In the U.S., streetlight manufacturers follow the American National Standards Institute (ANSI) guidelines. These standards focus on strength, durability, and ease of maintenance, with additional attention paid to ensuring compliance with the Americans with Disabilities Act (ADA).
- European Union: Europe’s standards, regulated by the European Union, prioritize energy efficiency, long lifespan, and low maintenance. In coastal areas, streetlights must meet high corrosion resistance specifications.
- Australia: Australia’s standards focus on the ability of streetlights to withstand high UV radiation and extreme temperature fluctuations, common in the Australian outback.
- India: In India, streetlight regulations are focused on energy conservation and cost-efficiency, especially in rural and semi-urban areas.
- Middle East: Countries like the UAE require streetlights that can withstand high temperatures and the corrosive effects of sand and dust storms.
Searching for High-Quality for Cast Aluminum Parts?
You’ve come to the right place! Yongzhu Casting is a certified die casting manufacturer with over 20 years of expertise in the industry.
We have successfully completed numerous die casting projects for Aluminum casting parts, particularly in your industry.

Zhejiang Yongzhu Casting Technology Co., Ltd.
Location: Zhejiang, China
Company type: Manufacturers, Producers, Wholesalers
Year Founded: 2004
Main Products: Aluminium die casting, Mold Making, Die Casting, Sand Casting, Gravity Casting
Leading Chinese producer Yongzhu Casting is formerly known as Hangzhou Higer Metal Products Co., Ltd., was established in 2004.
With 20 years of experience in the industry, we are a specialized manufacturer in Aluminum casting and Machining.
Our products are widely used in various applications such as Automotive, Energy, Lighting, Medical, Home Furnishings, Machinery & Equipment etc. Below are our advantages:
1. Design Review & DFM Support
Our professionals will evaluate your designs and provide suggestions for cost savings. Additionally, we offer Design for Manufacturing (DFM) assistance and conduct mold flow analyses to facilitate efficient production.
2. State-of-the-Art Manufacturing Equipment
Our facility is equipped with advanced hot-chamber and cold-chamber die casting machinery for aluminum and zinc production.
We also utilize high-precision CNC machines in a temperature-controlled workshop, featuring 3-Axis, 4-Axis and 5-Axis setups to manage any project you have.
3. Rigorous Quality Control Measures
Our dedicated quality control team ensures that all parts meet the highest standards of quality and consistency. We employ high-accuracy measurement instruments, including CMM, spectrometers, and X-ray detectors.
4. Comprehensive Surface Treatment Options
We provide a variety of surface finishing techniques for your precision die casting components. Our in-house services include cleaning, polishing, anodizing, shot blasting, and painting.
5. Flexible Project Acceptance
While larger manufacturers often shy away from low-volume projects, and smaller ones may struggle with quality, Yongzhu Casting stands apart. We prioritize customer satisfaction and willingly accept high-mix, low-volume projects like yours.
