Introduction
In the realm of manufacturing, the die casting process stands as a cornerstone for producing intricate structural components with precision and efficiency.
At Yongzhu, we specialize in mastering the die casting manufacturing process for structural components. In this comprehensive guide, we delve into the intricacies of die casting, offering invaluable insights and expert strategies to empower you in your manufacturing endeavors.
Understanding Die Casting
Die casting is a versatile manufacturing process that involves injecting molten metal into a steel mold cavity under high pressure.
This process enables the production of complex geometric shapes with tight tolerances and excellent surface finishes. It finds widespread applications across various industries, including automotive, aerospace, electronics, and more.
The Die Casting Process: A Step-by-Step Overview
1. Mold Preparation
- Die Design: The process begins with the design and fabrication of precision steel molds, also known as dies, tailored to the specific geometry of the desired component.
- Die Preparation: The dies are meticulously cleaned, lubricated, and assembled to ensure smooth operation during the casting process.
2. Melting and Injection
- Metal Melting: The selected metal alloy, typically aluminum or zinc, is melted in a furnace to the desired temperature.
- Injection: The molten metal is injected into the die cavity at high pressure, filling the mold and taking the shape of the component.
3. Cooling and Solidification
- Cooling Phase: After injection, the molten metal rapidly cools and solidifies within the die cavity.
- Ejection: Once solidified, the newly formed part is ejected from the die cavity using ejector pins or mechanisms.
4. Finishing Operations
- Trimming: Excess material, such as flash or runners, is removed from the cast part using trimming or deburring operations.
- Surface Treatment: Optional surface treatments, including shot blasting, machining, or coating, are applied to achieve the desired finish and properties.
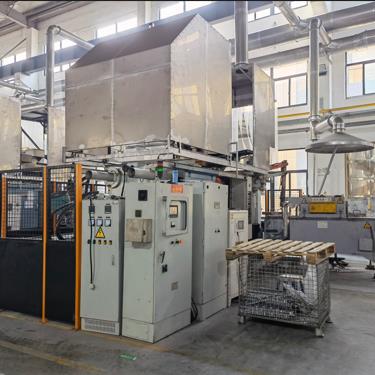

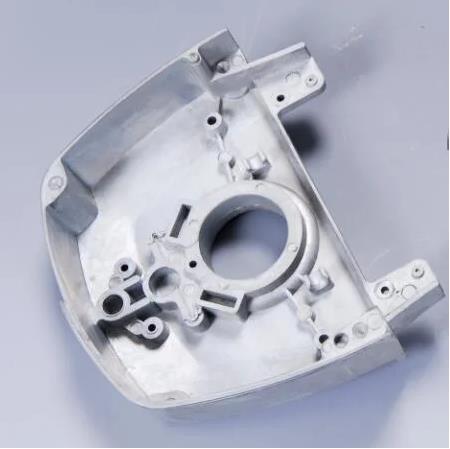
Key Considerations for Successful Die Casting
1. Material Selection
- Choose the appropriate metal alloy based on the application requirements, considering factors such as mechanical properties, corrosion resistance, and cost-effectiveness.
- Optimize alloy composition and purity to ensure consistent casting quality and performance.
2. Design Optimization
- Collaborate closely with design engineers to optimize component geometry for die casting, considering draft angles, fillets, and parting lines to facilitate mold filling and ejection.
- Leverage advanced simulation tools to analyze and validate designs, predicting potential defects and optimizing part quality.
3. Process Control
- Implement stringent process controls and monitoring systems to maintain consistent casting parameters, including metal temperature, injection pressure, and cooling rates.
- Conduct regular maintenance and inspection of dies to prevent wear and ensure dimensional accuracy and repeatability.
Advantages of Die Casting for Structural Components
- High Precision: Die casting offers tight tolerances and excellent dimensional stability, ensuring consistent part-to-part quality.
- Cost Efficiency: The high production rates and minimal post-processing requirements of die casting result in cost-effective manufacturing solutions.
- Complex Geometry: Die casting enables the production of intricate and complex geometric shapes with minimal machining or assembly requirements.
- Material Versatility: A wide range of metal alloys can be utilized in die casting, providing versatility in material selection to meet diverse application needs.
Conclusion
Mastering the die casting manufacturing process is essential for producing high-quality structural components with precision and efficiency.
By understanding the intricacies of die casting and implementing expert strategies for material selection, design optimization, and process control, Yongzhu empowers you to achieve superior results in your manufacturing endeavors.
Partner with us to unlock the full potential of die casting for your structural component needs.
Drop me an email with your ideas, and I’ll get back to you swiftly!