Nickel plating aluminum is a common surface treatment that enhances the corrosion resistance, durability, and aesthetics of aluminum parts.
This electroplating process involves coating aluminum with a layer of nickel to provide a harder surface and improve wear resistance.
Nickel-plated aluminum is used across industries, including automotive, aerospace, electronics, and manufacturing, where components are exposed to harsh environments and require extra protection.
In this article, we’ll dive into the benefits of nickel plating aluminum, explore the plating process, and outline its common applications.
Why Choose Nickel Plating for Aluminum?
Nickel plating aluminum offers a range of benefits, from increased corrosion resistance to enhanced wear protection.
Aluminum, while naturally corrosion-resistant, can benefit from an additional nickel layer for applications in marine, automotive, or high-humidity environments.
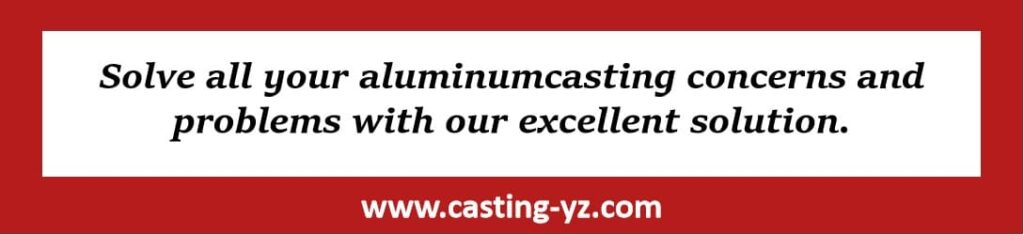
Key Benefits of Nickel Plating Aluminum
- Corrosion Resistance: Nickel provides a protective barrier against moisture, chemicals, and salt, extending the lifespan of aluminum parts in corrosive environments.
- Wear Resistance: Nickel plating significantly increases the surface hardness of aluminum, making it more resistant to scratches, wear, and mechanical damage.
- Aesthetic Improvement: Nickel gives aluminum a shiny, polished finish, making it an excellent choice for decorative parts in consumer electronics or automotive trim.
- Conductivity: Nickel plating improves the electrical conductivity of aluminum, which is crucial for applications in the electronics and telecommunications industries.
Benefit | How It Helps | Key Applications |
---|---|---|
Corrosion Resistance | Provides a barrier against moisture and chemicals. | Marine, automotive, outdoor structures. |
Wear Resistance | Increases surface hardness and prevents mechanical wear. | Manufacturing tools, mechanical parts, electronics. |
Aesthetic Improvement | Adds a shiny, polished look to the aluminum surface. | Automotive trim, consumer electronics. |
Improved Conductivity | Enhances electrical conductivity for electronic components. | Telecommunications, electronics. |
Searching for High-Quality for Cast Aluminum Parts?
You’ve come to the right place! Yongzhu Casting is a certified die casting manufacturer with over 20 years of expertise in the industry.
We have successfully completed numerous die casting projects for Aluminum casting parts, particularly in your industry.
Design Review & DFM Support
Our professionals will evaluate your designs and provide suggestions for cost savings.
Additionally, we offer Design for Manufacturing (DFM) assistance and conduct mold flow analyses to facilitate efficient production.
State-of-the-Art Manufacturing Equipment
Our facility is equipped with advanced hot-chamber and cold-chamber die casting machinery for aluminum and zinc production.
We also utilize high-precision CNC machines in a temperature-controlled workshop, featuring 3-Axis, 4-Axis, 5-Axis, and 7-Axis setups to manage any project you have.
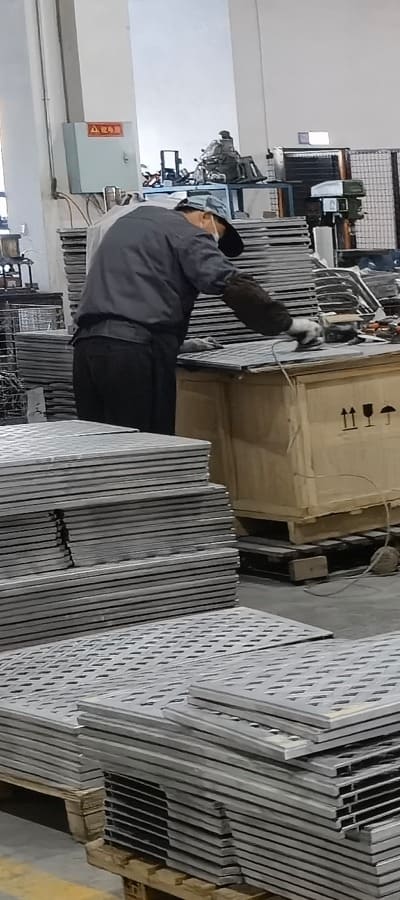
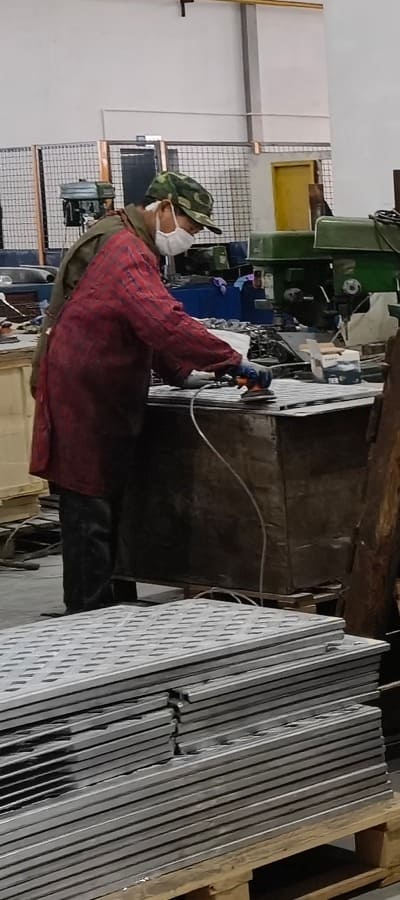
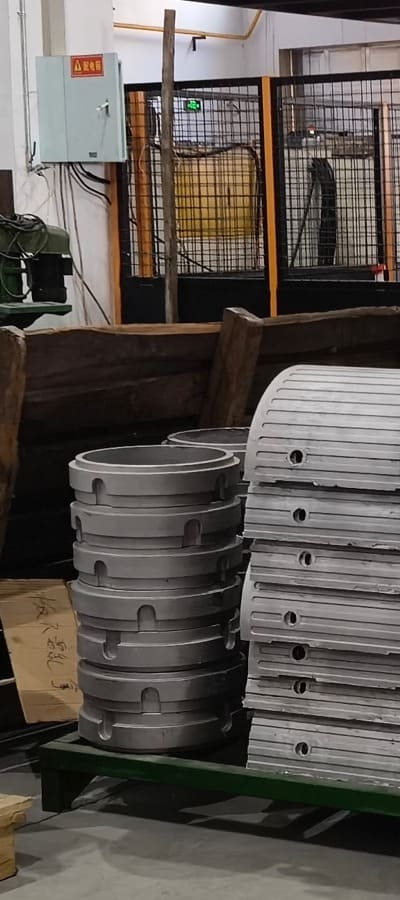
Rigorous Quality Control Measures
Our dedicated quality control team ensures that all parts meet the highest standards of quality and consistency.
We employ high-accuracy measurement instruments, including CMM, spectrometers, and X-ray detectors.
Comprehensive Surface Treatment Options
We provide a variety of surface finishing techniques for your precision die casting components. Our in-house services include cleaning, polishing, anodizing, shot blasting, and painting.
Flexible Project Acceptance
While larger manufacturers often shy away from low-volume projects, and smaller ones may struggle with quality, Yongzhu Casting stands apart.
We prioritize customer satisfaction and willingly accept high-mix, low-volume projects like yours.
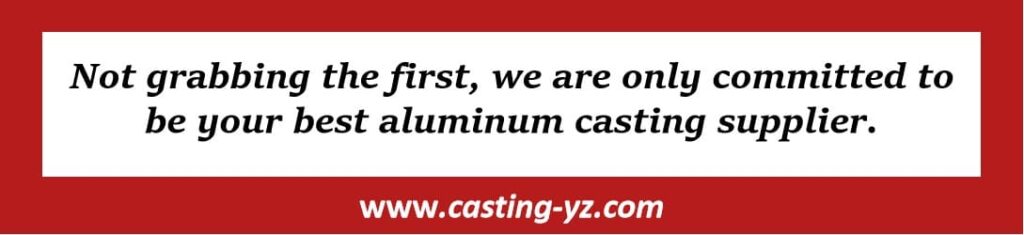
Nickel Plating Process for Aluminum
Nickel plating on aluminum involves several key steps to ensure proper adhesion and optimal results. The process can be broken down into surface preparation, pre-plating, and the actual nickel electroplating.
1. Surface Preparation
Before the nickel can be applied, the aluminum surface must be cleaned and etched to remove any contaminants, dirt, or oxides.
This is usually done through a series of degreasing, acid etching, and rinsing processes to prepare the surface for electroplating.
2. Zincate Treatment (Pre-Plating)
Aluminum does not naturally bond well with nickel, so a zincate process is used to create an intermediate layer that improves adhesion.
During the zincate treatment, a thin layer of zinc is deposited onto the aluminum surface to provide a base for the nickel to adhere to.
3. Nickel Electroplating
Once the zinc layer is applied, the part is immersed in a nickel bath. Direct current (DC) is used to deposit the nickel layer onto the aluminum surface.
The thickness of the nickel plating can be controlled based on the intended use, typically ranging from 0.0005 to 0.001 inches.
4. Finishing
After electroplating, the part is rinsed and polished to achieve the desired finish.
Depending on the application, additional treatments such as buffing or coating may be applied to further enhance the appearance or durability.
Step | Description | Purpose |
---|---|---|
Surface Preparation | Cleaning, degreasing, and etching the aluminum surface. | Removes impurities and promotes better adhesion. |
Zincate Treatment | A zinc layer is applied to improve nickel adhesion. | Ensures strong bonding between aluminum and nickel. |
Nickel Electroplating | Nickel is deposited using electrochemical methods. | Creates a durable, corrosion-resistant surface. |
Finishing | Final steps include polishing and buffing. | Enhances the appearance and smoothness of the part. |
Common Applications of Nickel-Plated Aluminum
Nickel-plated aluminum is widely used in industries where corrosion resistance, durability, and appearance are critical. Some of the key applications include:
1. Automotive
Nickel-plated aluminum parts are commonly used in automotive trim, wheels, and engine components to provide a polished look and protect against corrosion from road salts and moisture.
2. Aerospace
In the aerospace sector, nickel plating is applied to aircraft parts and structural components that are exposed to extreme conditions.
The nickel layer enhances the material’s wear resistance and increases the longevity of critical parts.
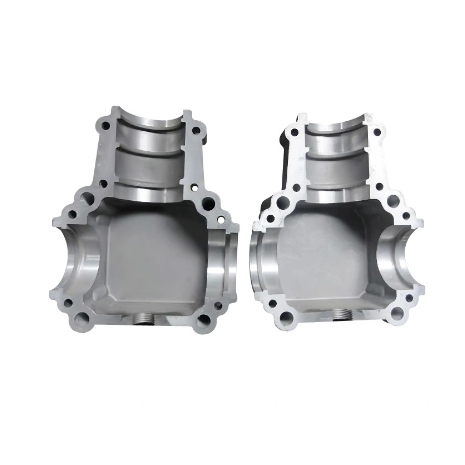

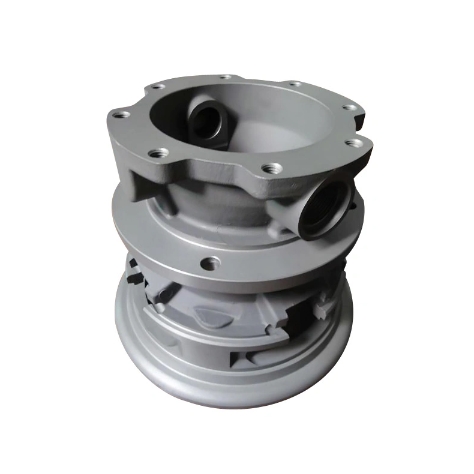
3. Consumer Electronics
Nickel-plated aluminum is frequently used in the consumer electronics industry, especially in components like smartphone casings, laptop bodies, and connectors, where aesthetics and electrical conductivity are important.
4. Manufacturing Tools
In manufacturing, nickel-plated aluminum tools are prized for their wear resistance and ability to withstand harsh conditions.
This is especially true in molds, dies, and cutting tools, where both durability and corrosion resistance are essential.
Industry | Nickel-Plated Aluminum Applications | Benefits |
---|---|---|
Automotive | Trim, wheels, engine components. | Corrosion resistance, polished aesthetic. |
Aerospace | Structural parts, engine components. | Wear resistance, durability in harsh environments. |
Consumer Electronics | Smartphone casings, connectors, laptop bodies. | Aesthetic appeal, enhanced conductivity. |
Manufacturing | Molds, dies, cutting tools. | High wear resistance, durability. |
Conclusion
Nickel plating aluminum offers several advantages, from improved corrosion resistance and enhanced durability to a polished finish that makes parts more visually appealing.
The process is widely used across industries like automotive, aerospace, electronics, and manufacturing, where long-lasting protection and aesthetics are critical.
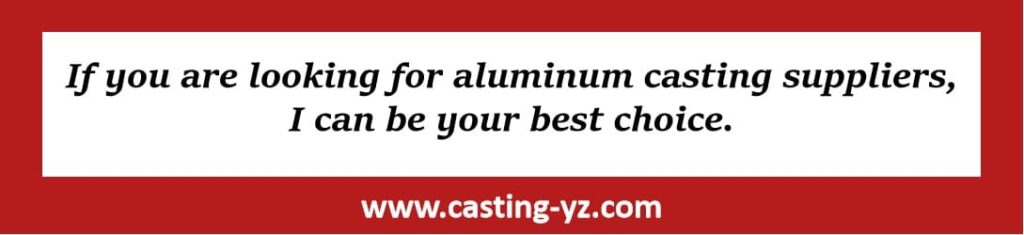