


Introduction
By implementing advanced strategies that minimize waste and boost productivity, manufacturers can achieve superior results, lower costs, and enhance sustainability.
This article explores key practices that can optimize aluminum die casting operations.
Aluminum Die Casting Efficiency
Efficiency in aluminum die casting is defined by the ability to produce high-quality parts with minimal waste, reduced cycle times, and lower operational costs.
Achieving this involves a combination of precise process control, material optimization, and technological advancements.
Key Strategies for Decreasing Waste
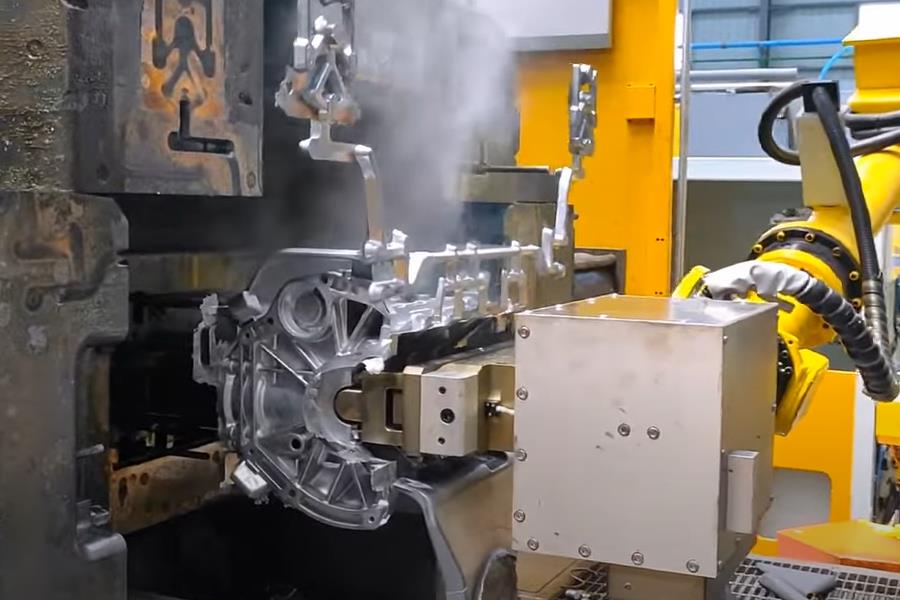
Optimizing Mold Design
- Importance of Precision: A well-designed mold is critical to minimizing waste. Accurate mold designs reduce material usage and prevent defects such as porosity and flash.
- CAD/CAM Integration: Leveraging Computer-Aided Design (CAD) and Computer-Aided Manufacturing (CAM) ensures precise mold development, leading to consistent part quality and minimal scrap.
Material Utilization and Recycling
- Material Selection: Choosing the right aluminum alloy based on part requirements minimizes excess usage and ensures recyclability.
- Scrap Recycling: Implementing a robust recycling program for aluminum scrap not only reduces waste but also lowers material costs and environmental impact.
Process Control and Monitoring
- Automated Systems: Advanced automation in die casting processes enables real-time monitoring and adjustments, reducing human error and material wastage.
- Quality Control: Implementing stringent quality checks throughout the production process ensures early detection of defects, minimizing the need for rework.
Boosting Productivity in Aluminum Die Casting
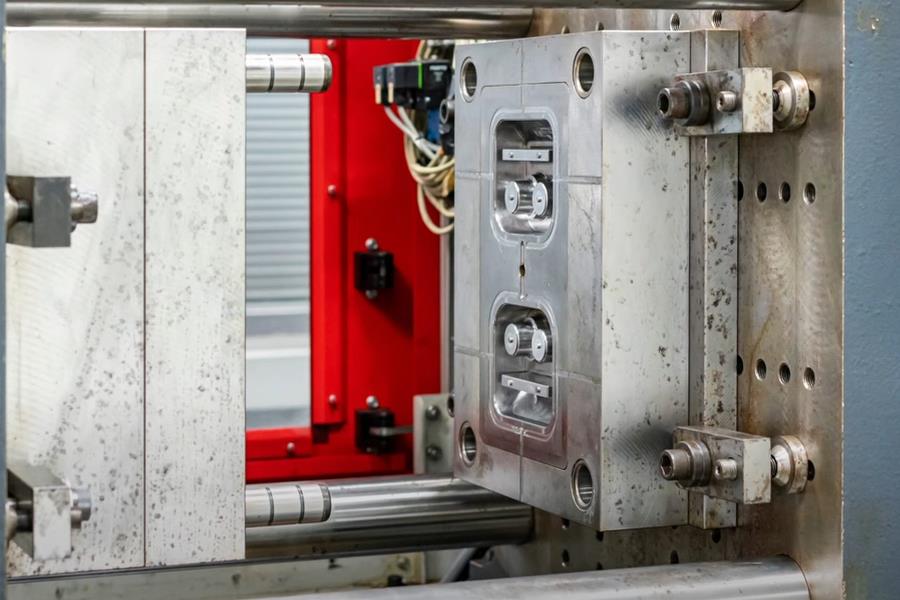
Cycle Time Reduction
- Optimized Cooling Systems: Efficient cooling systems reduce cycle times by quickly solidifying the molten aluminum, enabling faster mold ejection.
- High-Pressure Die Casting (HPDC): Utilizing HPDC techniques accelerates the production process, improving throughput without compromising quality.
Enhanced Workforce Training
- Skill Development: Regular training programs for operators ensure that they are proficient in the latest die casting technologies and best practices.
- Safety Protocols: Emphasizing workplace safety not only protects employees but also reduces downtime due to accidents.
Implementing Lean Manufacturing
- Value Stream Mapping (VSM): Applying VSM identifies bottlenecks and inefficiencies in the die casting process, allowing for targeted improvements.
- 5S Methodology: Adopting the 5S principles—Sort, Set in order, Shine, Standardize, Sustain—enhances workplace organization and efficiency.
Future Trends in Aluminum Die Casting

Industry 4.0 Integration
- Smart Factories: The adoption of Industry 4.0 technologies, including IoT devices and data analytics, enhances process transparency and decision-making.
- Predictive Maintenance: Utilizing machine learning algorithms for predictive maintenance reduces downtime and extends equipment lifespan.
Sustainable Practices
- Energy Efficiency: Investing in energy-efficient machinery and practices reduces the carbon footprint of die casting operations.
- Eco-Friendly Materials: The development of eco-friendly aluminum alloys and coatings supports sustainability goals while maintaining product performance.
Conclusion
By adopting these strategies, manufacturers can significantly reduce waste, enhance productivity, and position themselves as leaders in the competitive die casting industry.