Surface Treatment Techniques
Surface treatment techniques for automotive aluminum alloy parts play a crucial role in enhancing durability, aesthetics, and performance.
At YONGZHU, we specialize in employing advanced surface treatment methodologies that meet the rigorous standards of the automotive industry.

Anodizing: Enhancing Corrosion Resistance
Anodizing is a pivotal surface treatment technique utilized to improve the corrosion resistance of aluminum alloy parts.
Through an electrolytic process, an oxide layer is formed on the surface, providing a protective barrier against environmental factors such as moisture and chemicals.
Chromate Conversion Coating: Ensuring Adhesion and Paintability
Chromate conversion coating is another essential technique used in the surface treatment of aluminum alloy parts.
This process involves the chemical conversion of the metal surface, forming a chromate layer that enhances adhesion and facilitates subsequent painting processes.
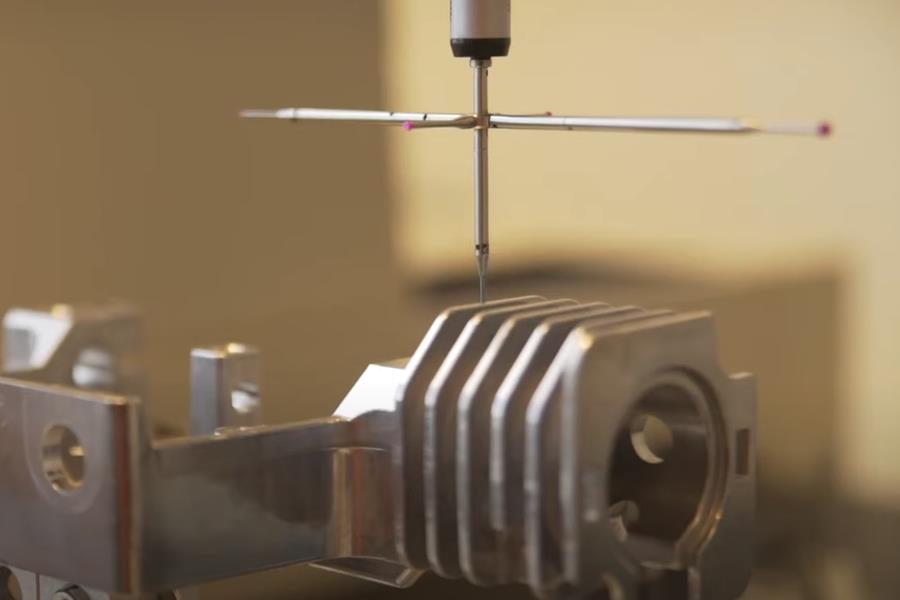
Electroplating: Enhancing Surface Hardness and Wear Resistance
Electroplating is employed to enhance the surface hardness and wear resistance of aluminum alloy parts.
By depositing a layer of metal, such as chromium or nickel, onto the substrate through an electrolytic process, the part’s durability is significantly improved.
Powder Coating: Durable and Environmentally Friendly Finishes
Powder coating offers a durable and environmentally friendly alternative for surface treatment of aluminum alloy parts.
This method involves applying a dry powder to the substrate, which is then cured under heat to form a tough, protective layer.
Powder coatings not only provide excellent corrosion resistance but also offer a wide range of color options and textures, making them ideal for automotive applications requiring both aesthetic appeal and functional durability.
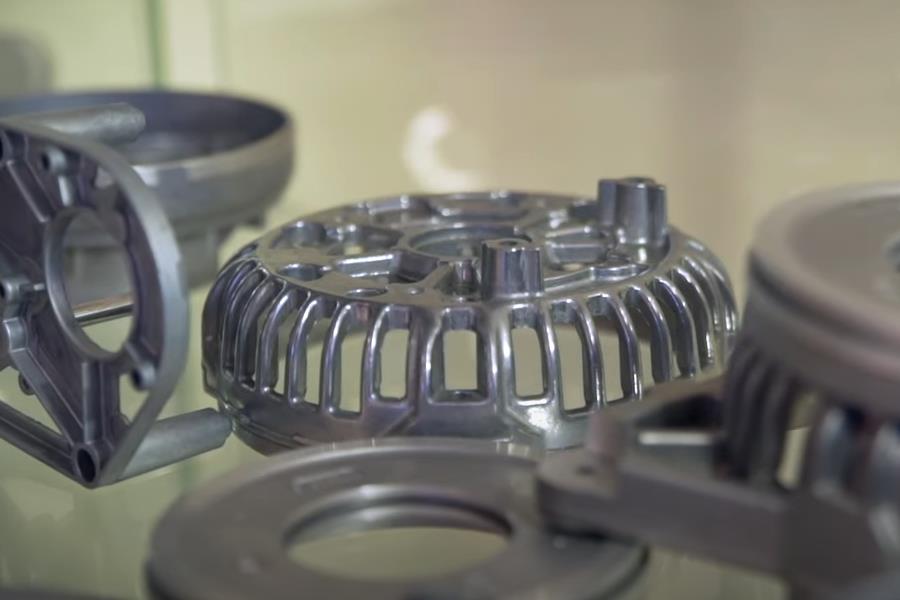
Shot Peening: Improving Fatigue Resistance
Shot peening is a mechanical surface treatment technique used to enhance the fatigue resistance of aluminum alloy parts.
By bombarding the surface with spherical particles, residual compressive stresses are induced, effectively preventing crack initiation and propagation.
This process is crucial for automotive components exposed to cyclic loading conditions, ensuring structural integrity and longevity under operational stresses.
Quick Preview
Surface Treatment Technique | Description | Benefits |
---|---|---|
Anodizing | Electrolytic process forming an oxide layer on the aluminum surface. | Enhanced corrosion resistance Aesthetic customization through dyeing |
Chromate Conversion Coating | Chemical conversion forming a chromate layer on the aluminum surface. | Enhanced adhesion Facilitates painting processes |
Electroplating | Electrolytic deposition of a metal layer (e.g., chromium or nickel) on the aluminum surface. | Enhanced surface hardness Increased wear resistance |
Powder Coating | Application of dry powder to the aluminum surface, cured under heat to form a protective layer. | Excellent corrosion resistance Wide range of colors and textures |
Shot Peening | Mechanical treatment where the surface is bombarded with spherical particles to induce compressive stresses. | Improved fatigue resistance Prevents crack initiation and propagation |
At YONGZHU, we leverage advanced methodologies such as anodizing, chromate conversion coating, electroplating, powder coating, and shot peening to meet the stringent requirements of the automotive industry.
Contact us today to learn more about how our comprehensive surface treatment solutions can elevate the quality and performance of your automotive components.