Aluminum die-casting molds are a critical component in the industrial sector, known for their role in producing high-quality aluminum parts used across various industries, including automotive, electronics, and aerospace.
As an aluminum casting manufacturer, it is essential to ensure the mold’s longevity, durability, and precision.
This article provides an in-depth look at the material selection and process involved in creating molds, focusing on the methods to enhance mold quality, sustainability, and efficiency.
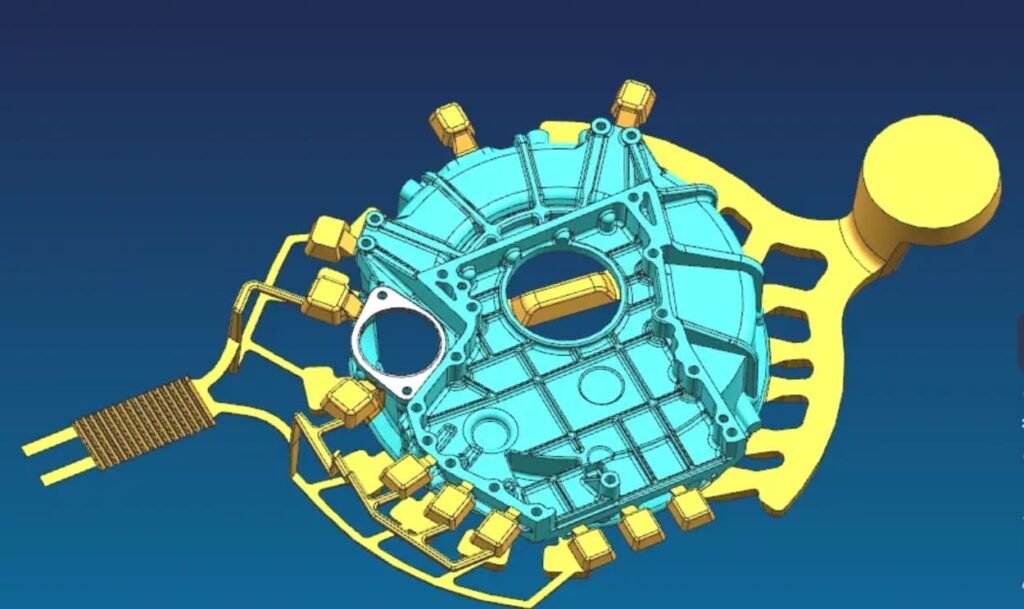
Material Selection for Aluminum Casting Molds
Choosing the right materials for cast aluminum molds impacts not only the quality but also the longevity and production efficiency of the final products.
Mold defects, for instance, can result in costly quality control issues. Below are the common types of reusable molds and their associated materials.
Types of Reusable Molds:
- Sand Casting Molds
- Ceramic Molds
- Permanent Molds
- Die Casting Molds
- Shell Molds
- Plaster Molds
- Graphite Molds
Common Materials for Aluminum Casting Molds
For reliable molds, materials should be chosen carefully to meet production requirements. Typical materials include:
- Steel – Durable and commonly used in permanent molds.
- Cast Iron – Known for strength and heat retention.
- Ceramic – Ideal for intricate designs in high-temperature environments.
- Graphite – Suited for high-precision parts.
Searching for High-Quality for Cast Aluminum Parts?
You’ve come to the right place! Yongzhu Casting is a certified die casting manufacturer with over 20 years of expertise in the industry.
We have successfully completed numerous die casting projects for Aluminum casting parts, particularly in your industry.

Zhejiang Yongzhu Casting Technology Co., Ltd.
Location: Zhejiang, Shaoxing
Company type: Manufacturing
Year Founded: 2004
Main Products: Aluminium die casting, Mold Making, Die Casting, Sand Casting, Gravity Casting
Leading Chinese producer Yongzhu Casting is formerly known as Hangzhou Higer Metal Products Co., Ltd., was established in 2004.
With 20 years of experience in the industry, we are a specialized manufacturer in Aluminum casting and Machining.
Our products are widely used in various applications such as Automotive, Energy, Lighting, Medical, Home Furnishings, Machinery & Equipment etc. Below is one of our products.
It’s worth mentioning that the evolution of rapid logistics has transformed how industries approach purchasing. Aluminum casting orders can now be sourced from overseas suppliers efficiently.
For instance, working with YONGZHU CASTING, you can inquire, order, and even find better value than your local options—all while maintaining assured quality.
Design Review & DFM Support
Our professionals will evaluate your designs and provide suggestions for cost savings. Additionally, we offer Design for Manufacturing (DFM) assistance and conduct mold flow analyses to facilitate efficient production.
State-of-the-Art Manufacturing Equipment
Our facility is equipped with advanced hot-chamber and cold-chamber die casting machinery for aluminum and zinc production.
We also utilize high-precision CNC machines in a temperature-controlled workshop, featuring 3-Axis, 4-Axis and 5-Axis setups to manage any project you have.
Rigorous Quality Control Measures
Our dedicated quality control team ensures that all parts meet the highest standards of quality and consistency. We employ high-accuracy measurement instruments, including CMM, spectrometers, and X-ray detectors.
Comprehensive Surface Treatment Options
We provide a variety of surface finishing techniques for your precision die casting components. Our in-house services include cleaning, polishing, anodizing, shot blasting, and painting.
Flexible Project Acceptance
While larger manufacturers often shy away from low-volume projects, and smaller ones may struggle with quality, Yongzhu Casting stands apart. We prioritize customer satisfaction and willingly accept high-mix, low-volume projects like yours.

Key Factors in Material Selection for Molds
- Material Properties
High machinability, thermal conductivity, and strength are crucial. The material must withstand high pressure and temperature while maintaining dimensional stability. - Manufacturing Requirements
The mold should meet the production volume, complexity, and specific manufacturing conditions needed for your parts. - Cost Considerations
While higher-quality materials may be more expensive, they yield more durable and reliable molds, offsetting costs in the long term. - Durability and Lifespan
Molds for high-pressure aluminum casting need to withstand the harsh casting environment, which ensures consistent quality and reduces downtime.
Steps to Make Permanent Molds for Aluminum Casting
Permanent molds offer high efficiency and reusability, making them ideal for high-volume manufacturing. Below are the typical steps involved in making a reusable mold:
- Custom Mold Design
Precision machining ensures parts fit perfectly, with gates for molten material entry. - Mold Preparation
Preheating the mold to 300-500°F reduces potential defects and extends the mold’s life by preventing thermal shock. - Mold Assembly
Permanent molds often consist of two sections and may include cores for complex details. Every component must be securely sealed before casting. - Pouring Process
Molten aluminum flows through a gated sprue, filling the mold cavity. - Cooling and Mold Release
The mold cools gradually before being opened to avoid shrinkage-induced cracks or deformations. - Finishing
Any excess metal is removed, resulting in a smooth, precise casting ready for finishing treatments.
Using 3D Printing in Aluminum Casting Mold Production
3D printing has modernized mold-making, enabling rapid production of complex designs with intricate geometries that traditional methods struggle to achieve. CAD software and advanced printing technologies like SLA create highly detailed patterns and molds with minimal material waste.
Advantages and Limitations of 3D-Printed Molds
- Advantages
- Speed and cost-effectiveness for prototyping and limited production runs.
- Ability to produce complex shapes and intricate multi-core designs.
- Reduced waste and fewer production steps.
- Limitations
- Requires CAD software expertise.
- Limited to smaller mold sizes due to machine constraints.
Maintenance and Storage for Aluminum Casting Molds
Ensuring molds remain in peak condition is critical for consistent casting quality and cost efficiency. Here’s how to manage and maintain mold longevity:
- Regular Cleaning
Prevent buildup of dirt or residues that could impair surface quality and mold function. - Routine Inspections
Look for signs of wear, such as cracks or warping, which might indicate the need for repairs or adjustments. - Safe Handling and Storage
Store molds in a dry, clean area free from dust and impacts, ensuring they remain in optimal condition between uses.
FAQs on Mold-Making for Aluminum Casting
- What materials are best for high-durability casting molds?
Steel and cast iron are preferred for their strength, while graphite suits high-precision applications. - What factors influence mold material choice?
Properties like machinability, thermal conductivity, durability, and cost. - How does mold preheating benefit the casting process?
Preheating prevents thermal shock, reduces defect rates, and enhances mold lifespan. - Is 3D printing viable for high-volume mold production?
3D printing is ideal for prototyping or low-volume production but may not be cost-effective for large runs. - What makes permanent molds suitable for aluminum casting?
Reusability, high strength, and excellent surface finish make permanent molds ideal. - How can I prevent mold defects?
Regular maintenance, cleaning, and proper storage ensure mold quality and prevent defects. - Why is durability important in mold materials?
High-durability materials reduce the need for replacements, saving costs over time. - What finishing processes are compatible with cast aluminum molds?
Shot blasting, polishing, and anodizing are common for aluminum to enhance surface quality. - How often should mold testing be performed?
After each production cycle, inspect for wear and other signs of degradation. - What is the role of simulation in mold design?
Simulation tools optimize mold design, reduce defects, and ensure quality castings.
Conclusion
Aluminum casting molds, when crafted with the right materials and maintained properly, offer significant advantages in durability, efficiency, and cost savings.
Using advanced processes such as 3D printing and careful selection of materials ensures high-quality outputs suited to various industrial applications.
Regular testing and maintenance extend mold life, making reusable aluminum casting molds a preferred choice across industries for sustainable and economical production.