
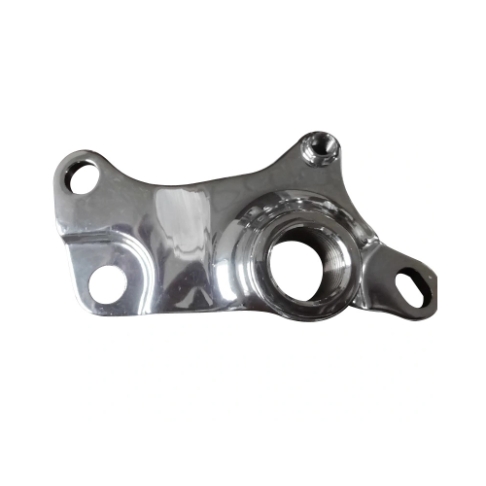

Surface finishing is a critical process in the manufacturing of die-cast aluminum components. It not only enhances the aesthetic appeal but also significantly improves the functional performance of the parts.
This guide covers advanced techniques for surface finishing, focusing on optimizing quality, durability, and appearance.
Surface Finishing in Die-Cast Aluminum
The most common goals include improving corrosion resistance, enhancing appearance, and preparing the surface for additional coatings or treatments.
Importance of Surface Finishing
Surface finishing is essential for extending the lifespan of aluminum components. It helps in minimizing wear, reducing friction, and preventing corrosion.
A well-finished surface also ensures better adhesion for coatings, which can further protect the material from environmental factors.

Key Surface Finishing Techniques
Mechanical Finishing
Mechanical finishing involves physically altering the surface of the aluminum component to remove imperfections and create a uniform texture.
- Polishing: Polishing uses abrasive materials to smooth out surface irregularities, giving the component a reflective finish. It is ideal for parts that require high aesthetic appeal.
- Buffing: Buffing is similar to polishing but uses softer abrasives for a higher level of smoothness and gloss.
- Grinding: This process removes material from the surface to eliminate defects such as burrs or rough spots.
Chemical Finishing
Chemical treatments are used to clean, etch, or passivate the aluminum surface, preparing it for further processes.
- Anodizing: Anodizing enhances corrosion resistance and can be used to add color to the aluminum surface. The process involves creating a protective oxide layer through an electrolytic reaction.
- Etching: Etching is used to create a matte finish or prepare the surface for painting or coating by using acids or alkalis to remove a thin layer of material.
- Chemical Polishing: This technique smooths the surface by dissolving microscopic peaks and valleys, leading to a highly reflective finish.
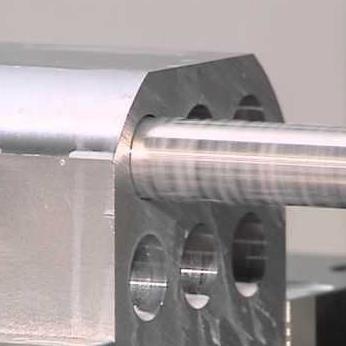
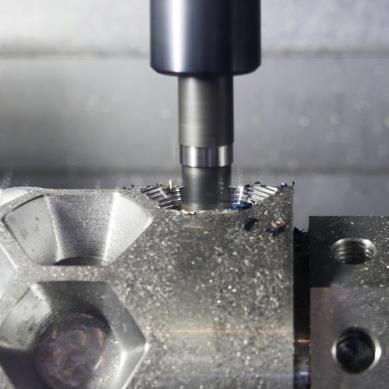

Electroplating
Electroplating deposits a thin layer of metal onto the aluminum surface, enhancing its properties.
- Nickel Plating: Nickel provides a hard, wear-resistant surface that is also aesthetically pleasing.
- Chrome Plating: Chrome offers excellent corrosion resistance and a bright, reflective finish, making it ideal for decorative applications.
Powder Coating
Powder coating applies a dry powder to the surface of the aluminum component, which is then cured under heat to form a hard, durable finish. It is available in a wide range of colors and textures, providing both aesthetic and protective benefits.
Painting
Painting is a versatile surface finishing method that allows for various colors and finishes. Special primers are often used to ensure strong adhesion between the paint and the aluminum surface.
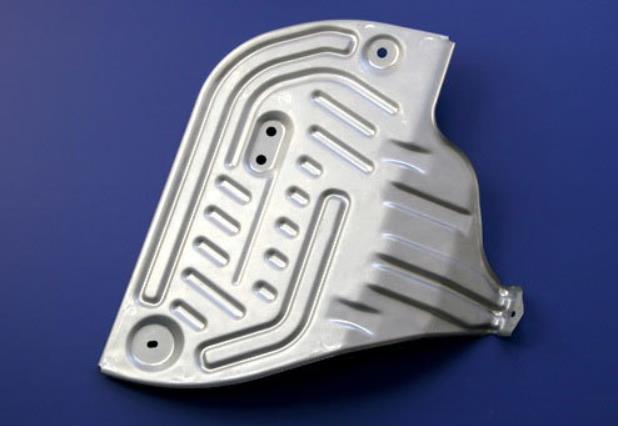
Advanced Surface Finishing Techniques
Laser Texturing
Laser texturing is a precise method of creating patterns or textures on the surface of aluminum components. This technique allows for intricate designs and can improve the adhesion of coatings.
Plasma Electrolytic Oxidation (PEO)
PEO is an advanced anodizing process that creates a ceramic-like coating on the aluminum surface, offering superior hardness, wear resistance, and corrosion protection.
Vapor Deposition Coatings
Vapor deposition techniques, such as Physical Vapor Deposition (PVD) and Chemical Vapor Deposition (CVD), apply thin films to the aluminum surface. These coatings are highly durable and can offer enhanced resistance to wear, corrosion, and heat.

Best Practices for Achieving Optimal Surface Finish
Surface Preparation
Proper surface preparation is crucial for achieving a high-quality finish. This may involve cleaning, degreasing, or pre-treatment processes to ensure the surface is free from contaminants.
Process Control
Maintaining consistent process parameters, such as temperature, pressure, and chemical concentration, is essential for achieving repeatable results.
Inspection and Quality Control
Regular inspection and testing of the finished components ensure that they meet the required standards. Techniques such as visual inspection, thickness measurement, and adhesion testing are commonly used.
Conclusion
Mastering the art of surface finishing for die-cast aluminum components is vital for producing high-quality, durable, and aesthetically pleasing parts.
By utilizing advanced techniques and adhering to best practices, manufacturers can significantly enhance the performance and lifespan of their products.