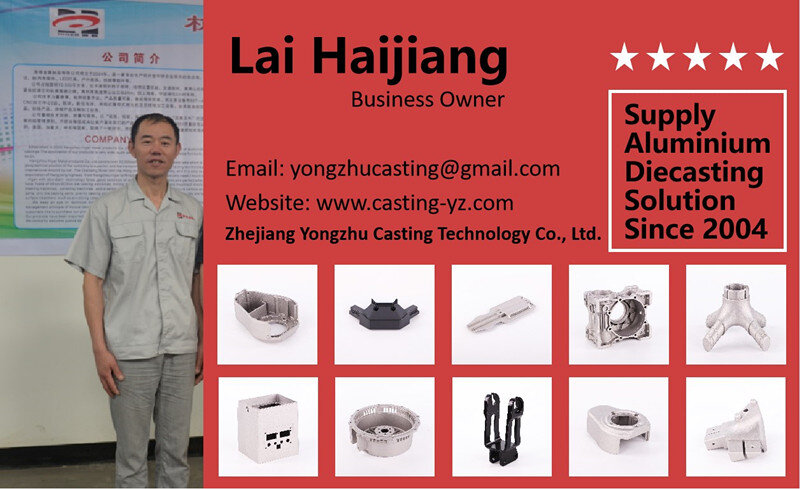
Pad printing is a versatile printing technique that transfers a 2D image onto a 3D object. This method is particularly useful for printing on irregular surfaces, making it a favored choice across various industries, including medical, automotive, electronics, and promotional items.
Our in-depth guide covers the essential aspects of pad printing, ensuring a solid understanding of its applications, techniques, and best practices for achieving optimal results.
Understanding Pad Printing
Pad printing involves transferring ink from a flat plate onto a substrate using a silicone pad. This process allows for the precise application of intricate designs on uneven or complex surfaces.
Key Components of Pad Printing
- Plate (Cliché): The image carrier, typically made of steel or photopolymer, where the artwork is etched.
- Ink Cup: Holds the ink and moves over the plate, filling the etched image.
- Pad: A soft silicone stamp that picks up the inked image from the plate and transfers it to the object.
- Substrate: The object or material being printed on.
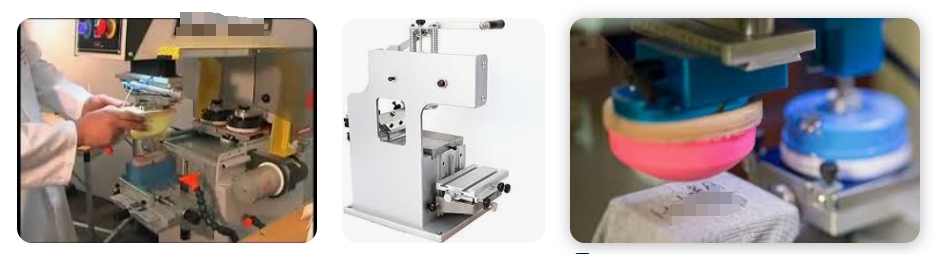
The Printing Process
- Artwork Preparation: The design is created and etched onto the printing plate.
- Inking: The ink cup slides over the plate, filling the etched areas with ink.
- Pad Compression: The silicone pad presses down onto the plate, picking up the ink.
- Ink Transfer: The pad moves to the substrate and compresses, transferring the ink onto the surface.
Applications of Pad Printing
Pad printing’s adaptability makes it suitable for a wide range of applications:
- Electronics: Printing on buttons, panels, and casings for phones, computers, and other gadgets.
- Medical Devices: Applying user-friendly interfaces on irregularly shaped medical equipment.
- Automotive Components: Marking dials, buttons, and instrument panels.
- Promotional Items: Customizing pens, keychains, and other promotional products.
Advantages of Pad Printing
- Versatility: Can print on almost any surface, shape, or material.
- High Precision: Capable of reproducing complex images with fine detail.
- Cost-Effective: Suitable for both small custom jobs and large-scale production.
Best Practices for Pad Printing
- Proper Plate Selection: Choose the right type of plate based on the complexity of the image and the production volume.
- Ink Management: Use ink formulated for the substrate to ensure adhesion and durability.
- Pad Selection: Pick a pad that complements the shape of the substrate for a clean transfer.
- Process Control: Maintain consistent machine settings and environmental conditions to ensure repeatable quality.
Enhancing Pad Printing with Technology
Incorporating advanced technologies like laser etching for plates and computerized color matching can significantly improve the efficiency and quality of pad printing operations.

Pad Printing Vs Screen Printing – Selecting the Appropriate Method
The decision between pad printing and screen printing hinges on the specific demands of your project rather than the superiority of one technique over the other. It necessitates a thorough assessment of your products and the desired outcomes.
For die-cast parts that boast intricate patterns, delicate details, or non-uniform surfaces, pad printing is the go-to option for its adaptability and fine resolution capabilities.
Conversely, if your components are flat or slightly curved and you’re looking at higher production quantities, screen printing could offer a more economical solution.
The choice ultimately rests on the particular needs of your project, your budgetary constraints, and the unique aspects of your die-cast parts. For additional guidance, feel free to reach out to Yongzhu Casting for more personalized advice.
Conclusion
Pad printing is a highly efficient, versatile, and precise printing method suitable for a myriad of applications across various industries. By understanding the fundamentals, applications, and best practices outlined in this guide, businesses can leverage pad printing to enhance their product offerings, ensuring high-quality prints on even the most challenging substrates.
Drop me an email with your ideas, and I’ll get back to you swiftly!