Introduction
Die casting is a precise and efficient manufacturing process where molten metal is forced into molds under high pressure to create intricate, high-quality parts.
As an aluminum die-casting factory, we understand that knowing the type of die casting—hot or cold chamber—can make a big difference for procurement teams seeking reliable components.
This article explores these two processes, their applications, and their advantages, helping you make informed purchasing decisions.
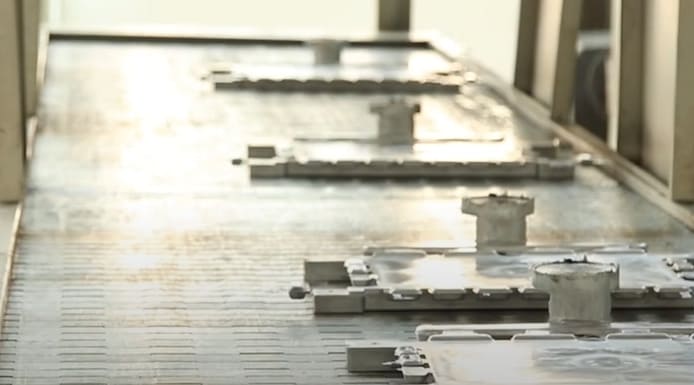
What is Die Casting?
Die casting uses high pressure to mold molten metal into reusable steel dies, delivering exceptional precision and surface finish.
Commonly used in automotive, electronics, and industrial applications, it is celebrated for its versatility, speed, and cost-effectiveness.
Searching for High-Quality for Cast Aluminum Parts?
You’ve come to the right place! Yongzhu Casting is a certified die casting manufacturer with over 20 years of expertise in the industry.
We have successfully completed numerous die casting projects for Aluminum casting parts, particularly in your industry.

Zhejiang Yongzhu Casting Technology Co., Ltd.
Location: Zhejiang, Shaoxing
Company type: Manufacturing
Year Founded: 2004
Main Products: Aluminium die casting, Mold Making, Die Casting, Sand Casting, Gravity Casting
Leading Chinese producer Yongzhu Casting is formerly known as Hangzhou Higer Metal Products Co., Ltd., was established in 2004.
With 20 years of experience in the industry, we are a specialized manufacturer in Aluminum casting and Machining.
Our products are widely used in various applications such as Automotive, Energy, Lighting, Medical, Home Furnishings, Machinery & Equipment etc. Below is one of our products.
It’s worth mentioning that the evolution of rapid logistics has transformed how industries approach purchasing. Aluminum casting orders can now be sourced from overseas suppliers efficiently.
For instance, working with YONGZHU CASTING, you can inquire, order, and even find better value than your local options—all while maintaining assured quality.
Design Review & DFM Support
Our professionals will evaluate your designs and provide suggestions for cost savings. Additionally, we offer Design for Manufacturing (DFM) assistance and conduct mold flow analyses to facilitate efficient production.
State-of-the-Art Manufacturing Equipment
Our facility is equipped with advanced hot-chamber and cold-chamber die casting machinery for aluminum and zinc production.
We also utilize high-precision CNC machines in a temperature-controlled workshop, featuring 3-Axis, 4-Axis and 5-Axis setups to manage any project you have.
Rigorous Quality Control Measures
Our dedicated quality control team ensures that all parts meet the highest standards of quality and consistency. We employ high-accuracy measurement instruments, including CMM, spectrometers, and X-ray detectors.
Comprehensive Surface Treatment Options
We provide a variety of surface finishing techniques for your precision die casting components. Our in-house services include cleaning, polishing, anodizing, shot blasting, and painting.
Flexible Project Acceptance
While larger manufacturers often shy away from low-volume projects, and smaller ones may struggle with quality, Yongzhu Casting stands apart. We prioritize customer satisfaction and willingly accept high-mix, low-volume projects like yours.

Types of Die Casting: Hot and Cold Chamber
Hot Chamber Die Casting
Hot chamber die casting, also known as gooseneck casting, is ideal for low-melting-point metals like zinc, magnesium, and lead.
Process:
- Metal is melted in a furnace connected to the machine.
- The molten metal is injected into the die using a piston.
Advantages:
- High production speed.
- Consistent surface quality.
- Suitable for intricate designs and thin walls.
Disadvantages:
- Limited to low-melting-point metals.
- Best for smaller components under 4.5 kg.
Cold Chamber Die Casting
Cold chamber die casting is used for metals with higher melting points, such as aluminum and copper.
Process:
- The metal is melted in an external furnace.
- The molten metal is manually ladled into the shot chamber before injection.
Advantages:
- Suitable for high-melting-point metals.
- Allows for larger and heavier components (up to 20 kg).
- Produces complex geometries with precision.
Disadvantages:
- Slower production cycles compared to hot chamber casting.
- Requires additional steps for metal transfer.
Vacuum Die Casting
Vacuum die casting removes air from the mold cavity for enhanced part quality and reduced surface defects.
Advantages:
- Superior surface finish and dimensional accuracy.
- Eliminates porosity in the final product.
Disadvantages:
- High operational costs.
Steps in the Die Casting Process
- Die Preparation: Lubricate the die for smooth release.
- Clamping: Secure the die halves with appropriate pressure.
- Injection: Fill the die with molten metal under high pressure.
- Cooling: Allow the metal to solidify within the mold.
- Ejection: Remove the solidified part.
- Trimming: Eliminate excess metal from the part.
Key Metals in Die Casting
- Aluminum: Lightweight, thermally efficient, corrosion-resistant.
- Zinc: Durable, great for precision components.
- Magnesium: Lightweight with high strength-to-weight ratio.
- Copper: High conductivity, ideal for electrical parts.
Advantages of Die Casting
- High Precision: Produces dimensionally accurate parts.
- Cost-Effective: Suitable for high-volume production with low labor costs.
- Versatility: Handles complex shapes and sizes with ease.
- Durability: Creates strong, long-lasting components.
Conclusion
Understanding the distinctions between hot and cold chamber die casting processes is crucial for selecting the right manufacturing method. At Yongzhu Casting, we specialize in delivering high-quality aluminum die-cast components tailored to your needs. Whether you require precision or durability, our advanced technology and expertise ensure optimal results.
FAQs About Die Casting Molds
- What materials are used for die-casting molds?
Common materials include steel, cast iron, and copper alloys for durability and precision. - How does hot chamber die casting differ from cold chamber?
Hot chamber integrates the furnace into the machine, while cold chamber uses an external furnace for high-melting-point metals. - What industries use die-casting the most?
Automotive, electronics, aerospace, and industrial manufacturing are major users. - Can vacuum die casting improve part quality?
Yes, vacuum casting reduces porosity and enhances surface finish. - How do you maintain die-casting molds?
Regular cleaning, lubrication, and monitoring for wear ensure longevity. - What is the typical weight limit for hot chamber casting?
It is best for components under 4.5 kg due to its design limitations. - Is aluminum suitable for high-precision casting?
Yes, aluminum’s lightweight and machinability make it ideal for intricate designs. - How are defects in die casting minimized?
By optimizing mold design, cooling rates, and using high-quality materials. - What is the cycle time for hot chamber casting?
Shorter than cold chamber casting due to integrated metal melting. - Why choose Yongzhu Casting for die-casting needs?
Our expertise, advanced machinery, and commitment to quality make us a trusted partner for high-performance die-cast components.