Die casting is a versatile and efficient metal casting process widely used in various industries to produce complex and high-precision metal parts.
The process can be categorized into three main types based on the pressure applied during casting: Low Pressure Die Casting (LPDC), Medium Pressure Die Casting (MPDC), and High Pressure Die Casting (HPDC).
Each method has its unique advantages, applications, and limitations. This article provides an in-depth comparison of these three die casting techniques.
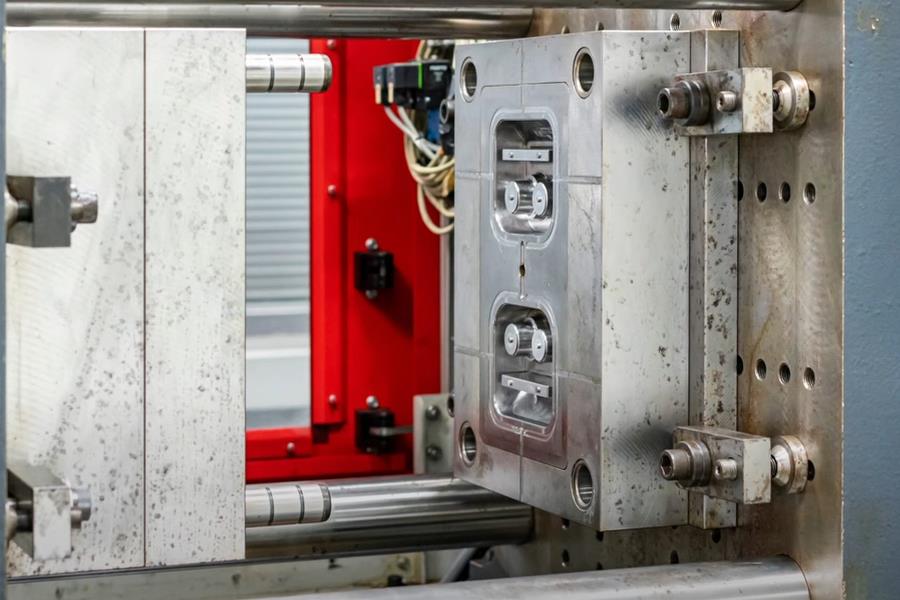
What is Low Pressure Die Casting (LPDC)?
Low Pressure Die Casting (LPDC) involves using a low-pressure environment to fill a mold with molten metal. This method is highly effective for producing intricate and high-quality components with excellent surface finishes.
Low Pressure Die Casting: Process, Advantages, Disadvantages, and Applications
Aspect | Details |
---|---|
Process | Mold Preparation: A permanent steel mold is preheated and coated with a release agent. Molten Metal Introduction: The mold is sealed, and low pressure (typically 1-2 bars) is applied to move the molten metal into the mold cavity. Solidification: The metal cools and solidifies within the mold. Casting Removal: The casting is removed, and any excess material is trimmed. |
Advantages | High-Quality Parts: Produces components with minimal porosity and excellent surface finishes. Precision and Consistency: Ensures accurate dimensional control. Cost-Efficiency: Lower scrap rates and minimal need for secondary operations. Eco-Friendly: Generates less waste and fewer emissions. |
Disadvantages | Material Limitations: Best suited for aluminum, magnesium, and zinc alloys. High Initial Costs: Significant upfront investment in tooling. Slower Production Speed: Compared to HPDC. |
Applications | Automotive: Engine parts, transmission components. Aerospace: Structural elements, turbine blades. Electronics: Heat sinks, precision components. |
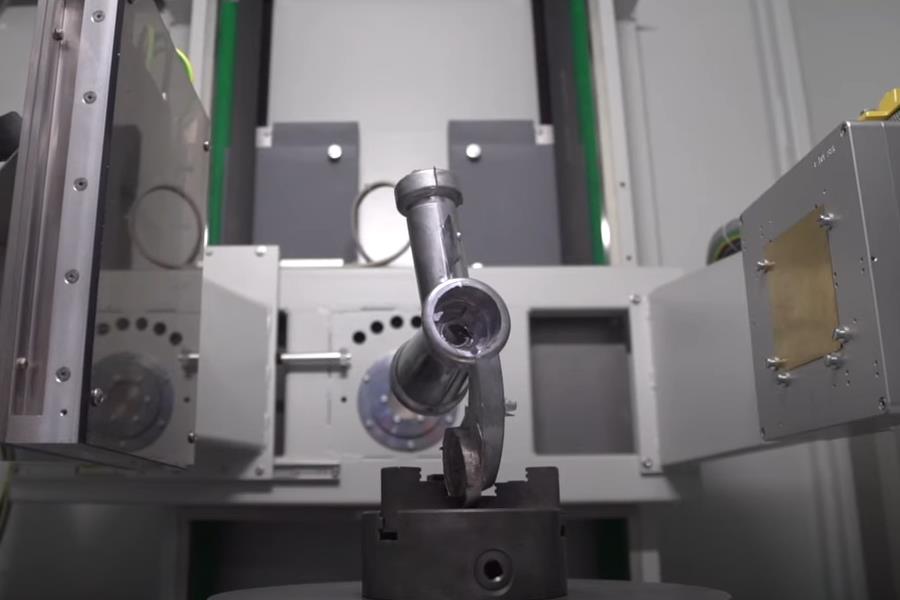
What is Medium Pressure Die Casting (MPDC)?
Medium Pressure Die Casting (MPDC) operates at pressures between those used in LPDC and HPDC, typically ranging from 3 to 100 MPa. This method is ideal for creating complex parts with high precision and durability.
Medium Pressure Die Casting: Process, Advantages, Disadvantages, and Applications
Aspect | Details |
---|---|
Process | Mold Designing: A steel mold is designed with detailed geometries. Molten Metal Injection: Molten metal is injected into the mold at medium pressure. Cooling and Solidification: The metal cools and solidifies within the mold. Ejection and Finishing: The casting is ejected, and excess material is trimmed. |
Advantages | High Precision: Excellent dimensional accuracy and repeatability. Improved Surface Finish: Smooth finishes with reduced porosity. Cost-Effective: Balances cost and production speed. Design Flexibility: Capable of producing lightweight designs with thin walls. |
Disadvantages | Material Selection: Primarily for non-ferrous metals like aluminum and zinc. Moderate Speed: Slower than HPDC but faster than LPDC. |
Applications | Automotive: Engine components, structural parts. Aerospace: Aircraft components, turbine blades. Consumer Goods: Cookware, electronic housings. |
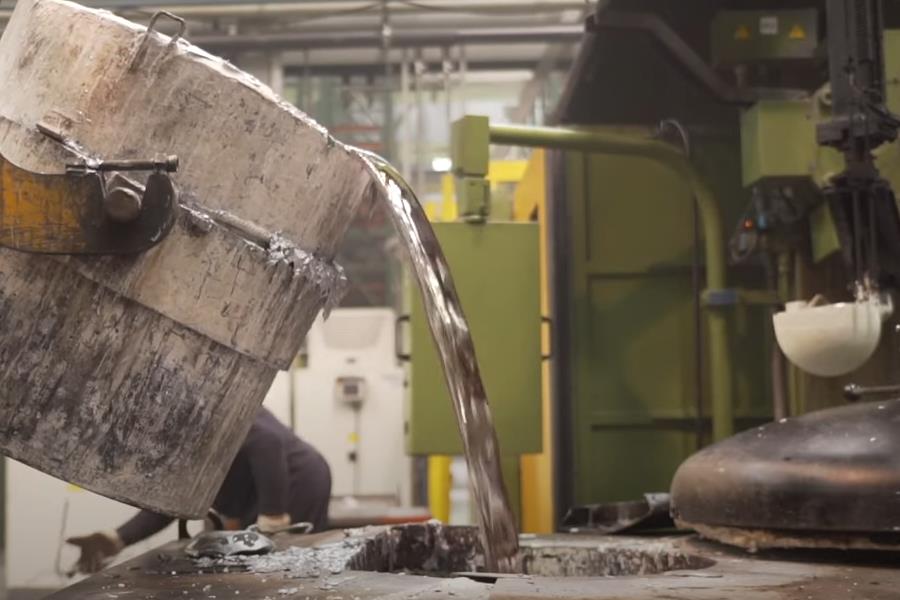
What is High Pressure Die Casting (HPDC)?
High Pressure Die Casting (HPDC) uses high pressure, typically up to 700 MPa, to inject molten metal into a mold. This method is renowned for its speed and ability to produce large volumes of parts.
High Pressure Die Casting: Process, Advantages, Disadvantages, and Applications
Aspect | Details |
---|---|
Process | Mold Preparation: A detailed mold is created and prepped. Molten Metal Injection: Molten metal is injected into the mold at high pressure. Rapid Solidification: The metal quickly cools and solidifies. Casting Ejection: The casting is removed, and any excess material is trimmed. |
Advantages | High Production Speed: Suitable for large-scale manufacturing. Wide Material Compatibility: Can be used with a variety of metals, including aluminum, zinc, and magnesium. Cost Efficiency for High Volumes: Economical for large production runs. |
Disadvantages | Surface Finish: May require more post-processing compared to LPDC and MPDC. High Operational Costs: Due to the need for robust equipment and maintenance. Complex Tooling: Requires detailed and expensive tooling. |
Applications | Automotive: Engine blocks, transmission housings. Industrial Machinery: Components for heavy machinery. Consumer Electronics: Housings and structural components. |
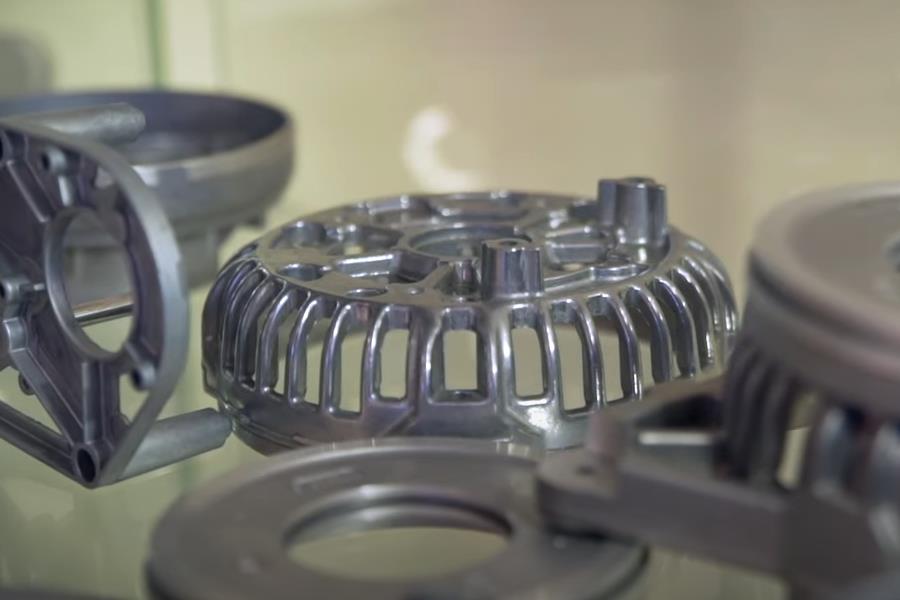
Comparison of LPDC, MPDC, and HPDC
Aspect | LPDC | MPDC | HPDC |
---|---|---|---|
Precision and Quality | Offers the highest quality with minimal porosity and excellent surface finishes. | Provides high precision and good surface finishes, suitable for intricate designs. | Best for high-speed production, but may require more post-processing. |
Production Speed | Slowest of the three, suitable for detailed and high-quality parts. | Moderate speed, balancing precision and production efficiency. | Fastest, ideal for high-volume production. |
Cost Considerations | Higher initial tooling costs, but cost-efficient in the long run due to low scrap rates. | Cost-effective with balanced tooling and operational costs. | Lower initial tooling costs for large volumes, but higher operational costs. |
Material Compatibility | Best for lightweight alloys (aluminum, magnesium, zinc). | Suitable for non-ferrous metals. | Compatible with a wide range of metals, including heavier alloys. |
Conclusion
Each die casting method—Low Pressure Die Casting (LPDC), Medium Pressure Die Casting (MPDC), and High Pressure Die Casting (HPDC)—offers unique benefits and is suited to different applications based on the required precision, production speed, and material compatibility.
LPDC excels in quality and precision, MPDC provides a balance of cost and performance, while HPDC is ideal for high-volume manufacturing.
Contact us today to discuss your project needs and receive a quote, you can trust us to deliver exceptional castings that meet your requirements.