Hermetic scroll compressors are a key component in modern HVAC systems and refrigeration applications, known for their efficiency, durability, and quiet operation.
These compressors rely on the innovative scroll mechanism to compress refrigerants, offering a more efficient solution compared to traditional reciprocating compressors.
One critical factor that contributes to the performance and reliability of hermetic scroll compressors is the use of aluminum die castings in their design and construction.
In this article, we will explain what a hermetic scroll compressor is, how it works, and the significant role aluminum cast parts play in its structure and performance.
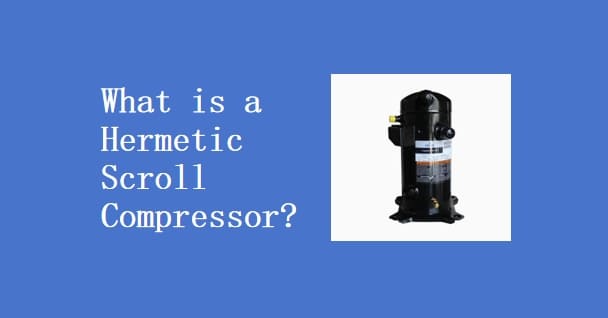
What is a Hermetic Scroll Compressor?
A hermetic scroll compressor is a type of positive displacement compressor that uses two interleaving scrolls (one fixed and one orbiting) to compress refrigerants within a sealed, hermetic housing.
The term “hermetic” refers to the sealed nature of the compressor, meaning the motor and the compressor are housed in a single, airtight unit.
This prevents leakage of refrigerant, making the compressor highly efficient and reliable for applications like air conditioning, refrigeration, and heat pumps.
Key Features of Hermetic Scroll Compressors
- Energy Efficiency: Scroll compressors offer 10-15% higher efficiency than reciprocating compressors due to their continuous compression process, reducing energy consumption in HVAC systems.
- Durability and Reliability: With fewer moving parts, scroll compressors experience less wear and tear, resulting in a longer operational life.
- Quiet Operation: The smooth, continuous motion of the scroll design leads to quieter operation compared to traditional compressors.
Searching for High-Quality for Cast Aluminum Parts?
You’ve come to the right place! Yongzhu Casting is a certified die casting manufacturer with over 20 years of expertise in the industry.
We have successfully completed numerous die casting projects for Aluminum casting parts, particularly in your industry.
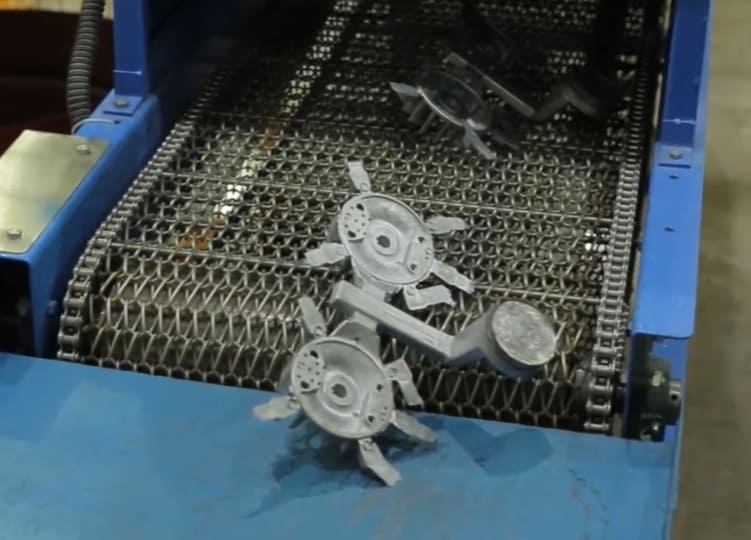

Design Review & DFM Support
Our professionals will evaluate your designs and provide suggestions for cost savings. Additionally, we offer Design for Manufacturing (DFM) assistance and conduct mold flow analyses to facilitate efficient production.
State-of-the-Art Manufacturing Equipment
Our facility is equipped with advanced hot-chamber and cold-chamber die casting machinery for aluminum and zinc production.
We also utilize high-precision CNC machines in a temperature-controlled workshop, featuring 3-Axis, 4-Axis, 5-Axis, and 7-Axis setups to manage any project you have.
Rigorous Quality Control Measures
Our dedicated quality control team ensures that all parts meet the highest standards of quality and consistency. We employ high-accuracy measurement instruments, including CMM, spectrometers, and X-ray detectors.
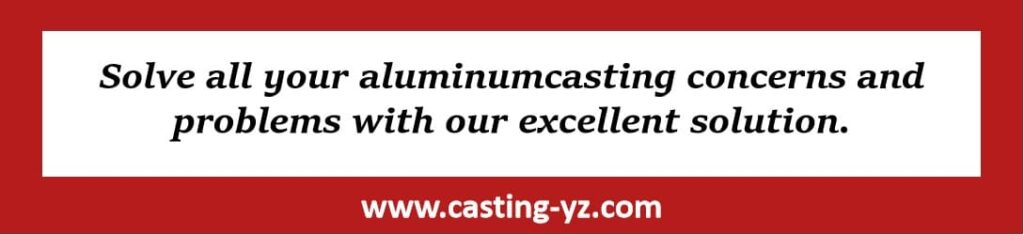
Comprehensive Surface Treatment Options
We provide a variety of surface finishing techniques for your precision die casting components. Our in-house services include cleaning, polishing, anodizing, shot blasting, and painting.
Flexible Project Acceptance
While larger manufacturers often shy away from low-volume projects, and smaller ones may struggle with quality, Yongzhu Casting stands apart.
We prioritize customer satisfaction and willingly accept high-mix, low-volume projects like yours.
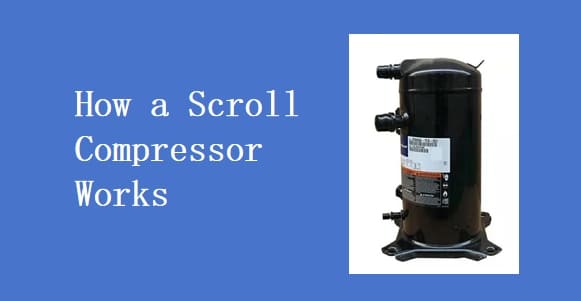
How a Scroll Compressor Works
In a scroll compressor, two spiral scrolls are nested together. One scroll remains stationary, while the other orbits around it, creating small pockets of refrigerant that are compressed as they move towards the center of the scrolls.
This design provides continuous, smooth compression without the back-and-forth motion seen in reciprocating compressors, resulting in less noise and vibration.
Feature | Description | Benefit |
---|---|---|
Continuous Compression | Compression occurs as refrigerant is trapped and compressed between scrolls. | Improved efficiency and lower energy consumption. |
Fewer Moving Parts | The scroll design minimizes the number of parts subject to wear. | Increased durability and reduced maintenance. |
Sealed Design | The hermetic seal prevents refrigerant leakage. | Enhanced reliability and longer compressor lifespan. |
The Role of Aluminum Die Castings in Hermetic Scroll Compressors
One of the reasons hermetic scroll compressors are so efficient and reliable is the use of aluminum die cast parts in their construction.
Aluminum, with its lightweight, corrosion resistance, and excellent thermal conductivity, is an ideal material for many of the compressor’s internal components.
The use of precision die-cast aluminum parts contributes to the overall performance, energy efficiency, and durability of these compressors.
Key Aluminum Components in Hermetic Scroll Compressors
- Compressor Housing: The housing, which encases the scroll mechanism and motor, is often made from aluminum die casting due to its ability to withstand high pressures while being lightweight. The reduced weight helps in minimizing overall system weight, which is critical for HVAC systems.
- Scroll Plates: Some scroll compressors use aluminum scroll plates, which benefit from aluminum’s high thermal conductivity. This allows the compressor to dissipate heat more effectively, preventing overheating and improving operational efficiency.
- Motor Components: Aluminum die-cast motor housings are used to reduce weight and provide better cooling to the motor, which is critical for maintaining the hermetic seal and ensuring long-term reliability.
- Valves and Covers: Various internal valve covers and end caps within the compressor are made from aluminum die castings, taking advantage of the material’s ability to be cast into complex shapes with tight tolerances, essential for ensuring proper sealing and mechanical function.
Aluminum Component | Function | Benefit to Compressor Performance |
---|---|---|
Compressor Housing | Protects internal components and maintains a sealed system. | Lightweight, high strength, and corrosion resistance. |
Scroll Plates | Compress refrigerant through orbital motion. | Improved heat dissipation and reduced overheating. |
Motor Components | Enclose and protect the compressor motor. | Weight reduction and efficient cooling of motor. |
Valves and Covers | Seal and regulate internal refrigerant flow. | Precision casting ensures tight seals and durability. |
Advantages of Using Aluminum in Scroll Compressors
1. Lightweight Construction
Aluminum’s low density (about 2.7 g/cm³) means it is much lighter than steel, reducing the overall weight of the compressor unit.
This is particularly important in HVAC systems and refrigeration units, where weight savings translate to easier installation and lower transportation costs.
2. Thermal Conductivity
Aluminum has high thermal conductivity (about 205 W/m·K), making it ideal for components like scroll plates and motor housings that need to dissipate heat quickly.
Improved heat management extends the life of the compressor and maintains efficiency during long operational periods.
3. Corrosion Resistance
Aluminum naturally forms a protective oxide layer, giving it excellent resistance to corrosion. This is particularly valuable in hermetic compressors, which operate in high-moisture environments such as refrigeration systems and air conditioners.
4. Complex Part Geometry
Aluminum die casting allows for intricate and precise designs, making it possible to produce complex components like scroll plates and housings with tight tolerances.
This precision ensures the efficient operation of the compressor and minimizes energy losses due to mechanical inefficiencies.
Advantage | Description | Application in Compressors |
---|---|---|
Lightweight Construction | Reduces overall system weight and installation costs. | Easier to transport and install in HVAC systems. |
Thermal Conductivity | Improves heat dissipation in critical components. | Prevents overheating in scroll plates and motor housing. |
Corrosion Resistance | Protects against environmental wear and moisture. | Ensures long life in refrigeration and outdoor systems. |
Complex Part Geometry | Allows precision manufacturing of internal components. | Ensures tight tolerances for better energy efficiency. |
Common Applications of Hermetic Scroll Compressors
Hermetic scroll compressors are widely used in industries where efficiency, durability, and reliability are key. Some common applications include:
- HVAC Systems: Used in both residential and commercial air conditioning systems, where energy efficiency is critical.
- Refrigeration: Employed in industrial refrigeration units, including supermarket freezers and cold storage facilities, where consistent cooling and reliable performance are essential.
- Heat Pumps: Hermetic scroll compressors are used in heat pumps, which are an energy-efficient solution for both heating and cooling buildings.
- Automotive Air Conditioning: Increasingly used in electric vehicles (EVs) and hybrid vehicles for their compact size, lightweight design, and energy-efficient operation.
