High pressure die casting (HPDC) is a manufacturing process known for its efficiency and precision in producing high-quality metal components.
From automotive parts to intricate electronics, HPDC plays a crucial role in various industries.
In this comprehensive guide, we’ll delve into the nuances of high pressure die casting, exploring its benefits, applications, and much more.

What is High Pressure Die Casting?
High pressure die casting is a versatile and widely used manufacturing process where molten metal is injected into a mold cavity under high pressure.
The pressure ensures the metal fills the mold completely and rapidly, producing parts with fine detail and excellent surface finish.
This method is ideal for high-volume production of complex and precise components.
The HPDC Process: Step-by-Step
Step | Description |
---|---|
Mold Preparation | Preparing the steel mold with two halves: the fixed die half and the moving die half. |
Melting the Metal | Melting the selected metal (often aluminum or magnesium) in a furnace to the required temperature. |
Injection | Injecting the molten metal into the mold cavity at high speed and pressure to form the desired shape. |
Cooling and Solidification | Allowing the metal to cool and solidify, forming the final shape and mechanical properties. |
Ejection | Opening the moving die half and ejecting the cast part from the mold using ejector pins. |
Trimming and Finishing | Trimming excess material (flash) and applying additional finishing processes like machining or surface treatment. |
Materials Used in HPDC
Several metals can be used in high pressure die casting, with the most common being:
- Aluminum: Lightweight, strong, and corrosion-resistant, making it ideal for automotive and aerospace applications.
- Magnesium: The lightest structural metal, known for its excellent strength-to-weight ratio.
- Zinc: Offers high ductility and impact strength, commonly used in small, intricate components.
- Copper: Provides superior electrical conductivity, suitable for electrical components.
Advantages of High Pressure Die Casting
Key Points | Description |
---|---|
Precision and Accuracy | HPDC produces parts with tight tolerances and fine details, reducing the need for secondary machining. |
High Production Rate | Rapid cycle times make HPDC an efficient choice for mass production. |
Material Efficiency | The process generates minimal waste, and excess material can often be recycled. |
Strength and Durability | Parts made with HPDC exhibit high mechanical properties, suitable for demanding applications. |
Applications of HPDC
High pressure die casting is employed across various industries, including:
- Automotive: Engine components, transmission cases, and structural parts.
- Electronics: Housings for devices, connectors, and heat sinks.
- Aerospace: Lightweight structural components and complex shapes.
- Consumer Goods: Appliance parts, hardware, and tools.
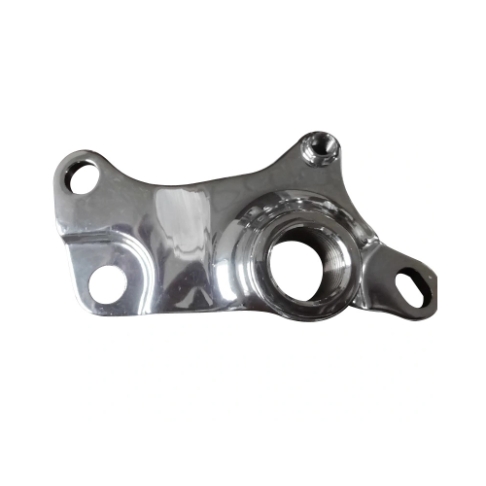
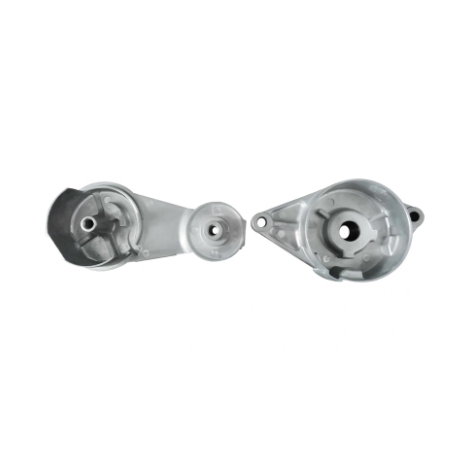
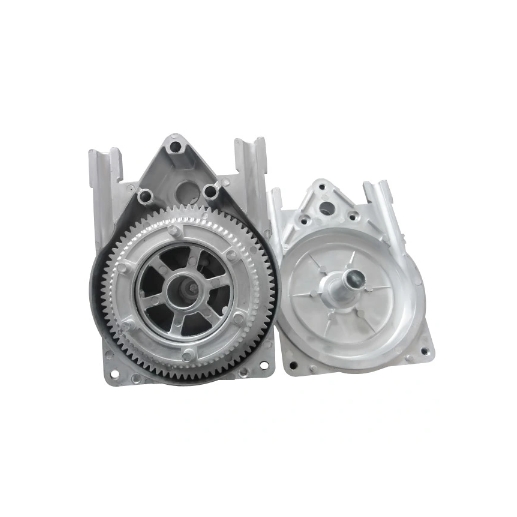
High Pressure Die Casting vs. Other Casting Methods
HPDC vs. Gravity Die Casting
HPDC uses high pressure to inject molten metal, resulting in finer details and thinner walls compared to gravity die casting, which relies on gravity to fill the mold.
HPDC vs. Sand Casting
While sand casting is versatile and cost-effective for low-volume production, HPDC is more suitable for high-volume runs due to its faster cycle times and superior surface finish.
HPDC vs. Investment Casting
Investment casting can produce highly detailed parts with excellent surface finishes, but HPDC is faster and more cost-effective for large production volumes.
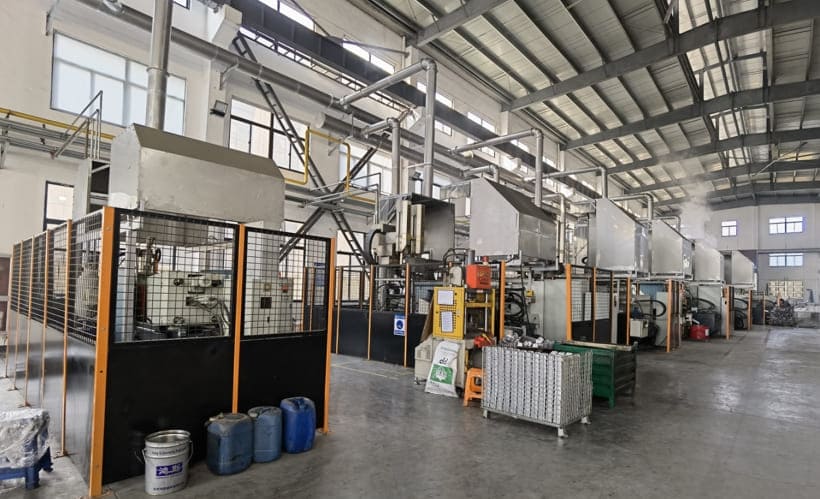
Design Considerations in HPDC
When designing parts for high pressure die casting, several factors must be considered to ensure manufacturability and performance:
- Wall Thickness: Uniform wall thickness prevents defects and ensures consistent cooling.
- Draft Angles: Including draft angles facilitates the ejection of the part from the mold.
- Ribs and Bosses: Adding ribs and bosses can enhance strength and rigidity without significantly increasing weight.
- Fillets and Radii: Smooth transitions reduce stress concentrations and improve flow during casting.
Quality Control in HPDC
Maintaining high quality in HPDC involves several inspection and testing methods:
- Dimensional Inspection: Ensuring parts meet specified dimensions using precise measurement tools.
- X-ray Inspection: Detecting internal defects like porosity and voids.
- Surface Testing: Checking for surface defects and ensuring a smooth finish.
- Mechanical Testing: Verifying mechanical properties such as tensile strength and hardness.
Challenges in High Pressure Die Casting
Issue | Description |
---|---|
Porosity | Trapped air or gas leads to weak spots in the cast part. Proper mold design and process control can mitigate this issue. |
Thermal Fatigue | Repeated heating and cooling cycles cause cracks and reduce mold life. High-quality mold materials and proper cooling techniques can extend mold life. |
Metal Flow and Filling | Ensuring complete and consistent mold filling is crucial. Poor metal flow can result in defects and incomplete parts. Optimizing injection parameters and mold design helps achieve proper flow. |
Innovations in HPDC Technology
The HPDC industry continuously evolves with technological advancements:
- Vacuum Die Casting: Reduces porosity by evacuating air from the mold cavity before injection.
- Squeeze Casting: Combines HPDC and forging techniques to produce parts with superior mechanical properties.
- Simulation Software: Helps design and optimize molds, predicting potential defects and improving process parameters.
Environmental Impact of HPDC
Aspect | Description |
---|---|
Energy Consumption | HPDC is energy-intensive, especially during the metal melting stage. Using energy-efficient furnaces and optimizing production processes can reduce energy consumption. |
Recycling | The process generates minimal waste, and scrap material can often be recycled, contributing to sustainability. |
Emissions | Proper management and use of eco-friendly materials can minimize emissions and environmental impact. |
Future Trends in High Pressure Die Casting
Here is the optimized table with the key points and details:
Aspect | Description |
---|---|
Lightweight Materials | The demand for lightweight materials, particularly in the automotive and aerospace sectors, drives the development of new alloys and HPDC techniques. |
Automation | Automation enhances production efficiency, reduces labor costs, and improves quality consistency in HPDC. |
Sustainability | Focus on sustainable practices, such as recycling and energy efficiency, will continue to grow, making HPDC more environmentally friendly. |
Choosing the Right HPDC Service Provider
Selecting a reliable HPDC service provider is crucial for quality and efficiency:
- Experience: Look for providers with extensive experience and a proven track record in your industry.
- Technology: Ensure they use state-of-the-art equipment and technologies.
- Quality Assurance: Check their quality control processes and certifications.
- Customer Support: Reliable customer support and communication are essential for successful collaboration.


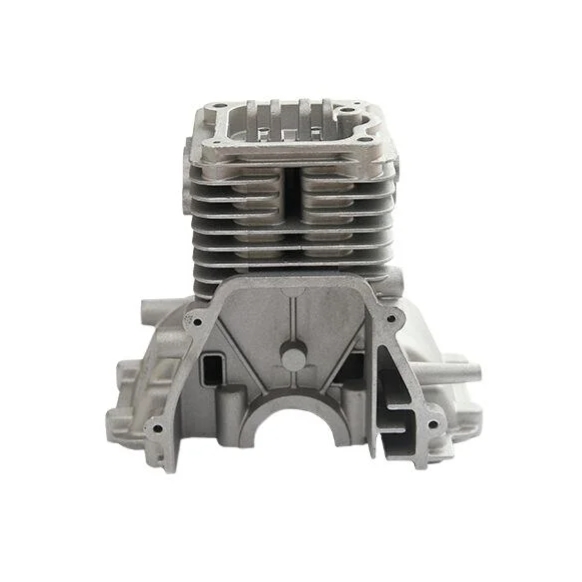
Cost Considerations in HPDC
The cost of high pressure die casting can be influenced by several factors:
- Material Costs: The type of metal used can significantly impact costs.
- Mold Costs: High-quality, durable molds are essential but can be expensive to manufacture.
- Production Volume: Higher production volumes typically reduce the cost per unit.
- Finishing Processes: Additional machining and surface treatments add to the overall cost.
Conclusion
High pressure die casting is a powerful manufacturing process capable of producing high-quality, complex metal parts efficiently.
Its applications span across numerous industries, driven by its precision, durability, and cost-effectiveness.
As technology advances, HPDC continues to evolve, offering even greater potential for innovation and sustainability.
Contact us today to discuss your project needs and receive a quote, you can trust us to deliver exceptional castings that meet your requirements.
FAQs
What is the lifespan of a die in HPDC?
The lifespan of a die in HPDC can vary depending on factors like material, design, and usage. High-quality dies can last for thousands of cycles.
Can HPDC produce large parts?
Yes, HPDC can produce large parts, but the size is limited by the capacity of the die casting machine and mold.
How does HPDC compare to 3D printing?
While 3D printing is versatile for prototyping and low-volume production, HPDC is more efficient for high-volume manufacturing due to its speed and cost-effectiveness.
What surface finishes can be achieved with HPDC?
HPDC can produce parts with smooth, high-quality surface finishes, often eliminating the need for additional machining.
Is HPDC suitable for producing structural components?
Yes, HPDC is ideal for producing strong, durable structural components used in industries like automotive and aerospace.