Aluminum is widely used in various industries due to its lightweight nature, corrosion resistance, and ease of fabrication.
However, for applications requiring enhanced durability, aesthetics, and further corrosion protection, chrome plating is often applied to aluminum surfaces.
This process offers a range of benefits, from improved wear resistance to an attractive, polished finish, making it a popular choice in industries such as automotive, aerospace, and manufacturing.
In this guide, we’ll explore the key reasons to choose chrome plating for aluminum, the benefits it offers, and the most common applications where this surface treatment is used.
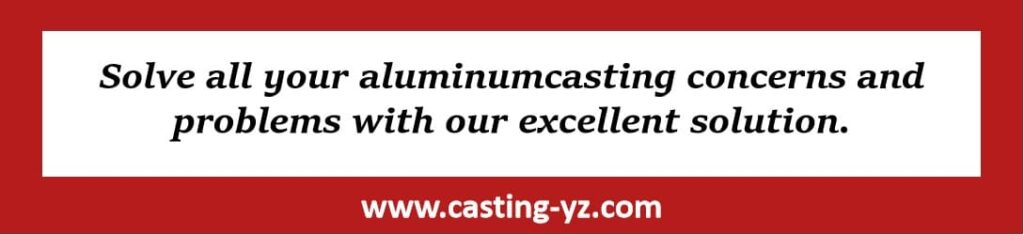
What is Chrome Plating?
Chrome plating, or chromium electroplating, is a process where a thin layer of chromium is applied to a metal surface through an electrochemical process.
In the case of aluminum, the surface is first prepared and coated with an intermediate layer (often nickel) before the chrome is applied.
This extra step ensures strong adhesion, as aluminum does not naturally bond well with chromium.
Key Steps in the Chrome Plating Process for Aluminum
- Surface Preparation: The aluminum surface is cleaned and pre-treated to remove any contaminants or oxidation.
- Intermediate Coating: A layer of nickel or copper is applied to the aluminum to improve adhesion.
- Chrome Plating: A thin layer of chrome (typically 0.0002 to 0.0005 inches thick) is electroplated onto the prepared surface.
- Polishing and Finishing: The chrome-plated surface is polished for a smooth, reflective finish.
Step | Description | Importance |
---|---|---|
Surface Preparation | Cleaning and removing oxidation from the aluminum surface. | Ensures proper adhesion and prevents defects in the plating. |
Intermediate Coating | Application of nickel or copper before chrome plating. | Improves the bond between aluminum and the chrome layer. |
Chrome Plating | Electroplating the chromium layer onto the aluminum. | Adds durability, corrosion resistance, and aesthetic appeal. |
Polishing and Finishing | Final polishing for a high-gloss, reflective surface. | Enhances appearance and smoothness of the plating. |
Searching for High-Quality for Cast Aluminum Parts?
You’ve come to the right place! Yongzhu Casting is a certified die casting manufacturer with over 20 years of expertise in the industry.
We have successfully completed numerous die casting projects for Aluminum casting parts, particularly in your industry.
Design Review & DFM Support
Our professionals will evaluate your designs and provide suggestions for cost savings.
Additionally, we offer Design for Manufacturing (DFM) assistance and conduct mold flow analyses to facilitate efficient production.
State-of-the-Art Manufacturing Equipment
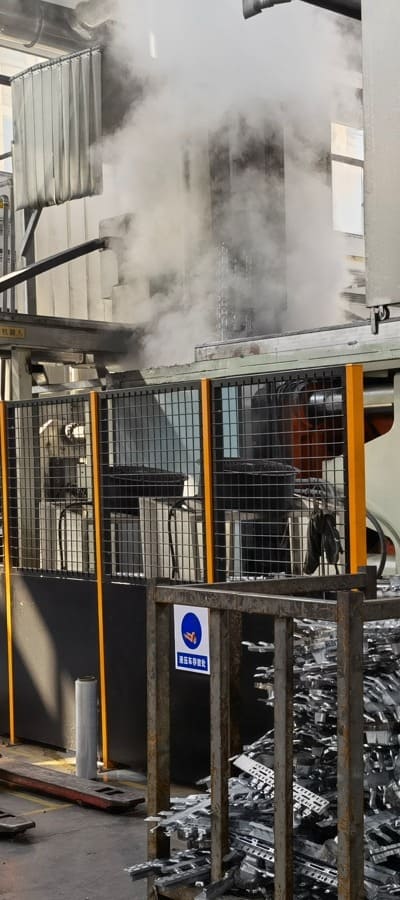
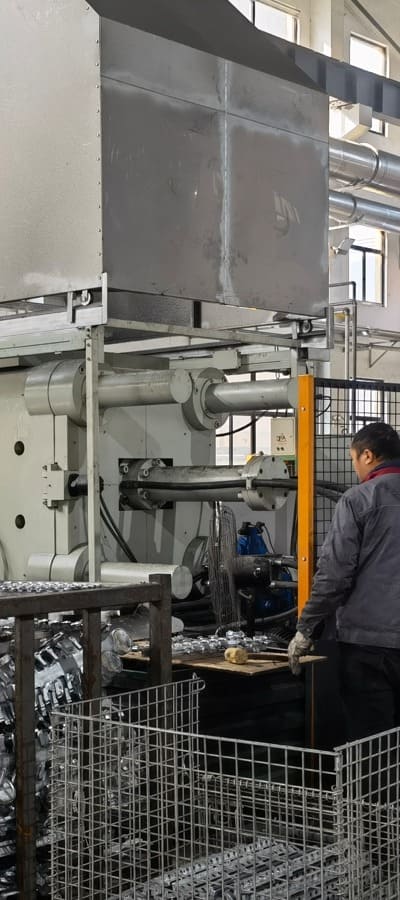
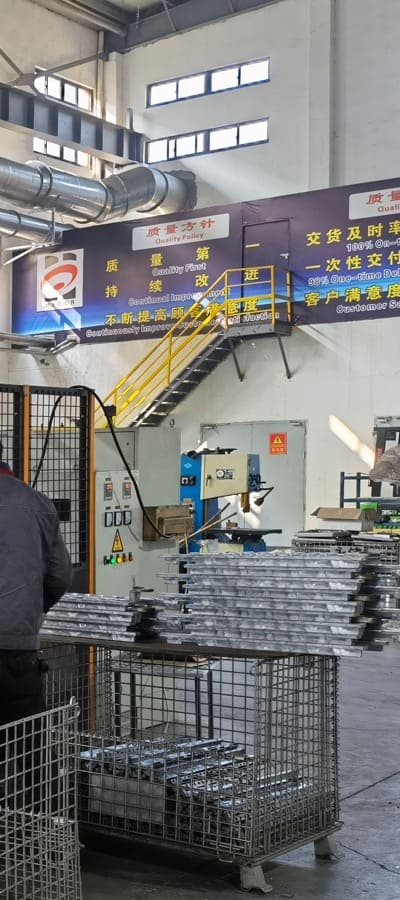
Our facility is equipped with advanced hot-chamber and cold-chamber die casting machinery for aluminum and zinc production.
We also utilize high-precision CNC machines in a temperature-controlled workshop, featuring 3-Axis, 4-Axis, 5-Axis, and 7-Axis setups to manage any project you have.
Rigorous Quality Control Measures
Our dedicated quality control team ensures that all parts meet the highest standards of quality and consistency.
We employ high-accuracy measurement instruments, including CMM, spectrometers, and X-ray detectors.
Comprehensive Surface Treatment Options
We provide a variety of surface finishing techniques for your precision die casting components. Our in-house services include cleaning, polishing, anodizing, shot blasting, and painting.
Flexible Project Acceptance
While larger manufacturers often shy away from low-volume projects, and smaller ones may struggle with quality, Yongzhu Casting stands apart.
We prioritize customer satisfaction and willingly accept high-mix, low-volume projects like yours.
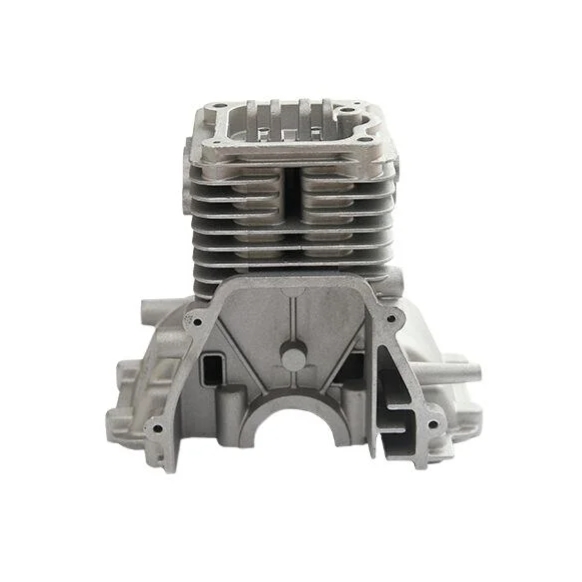

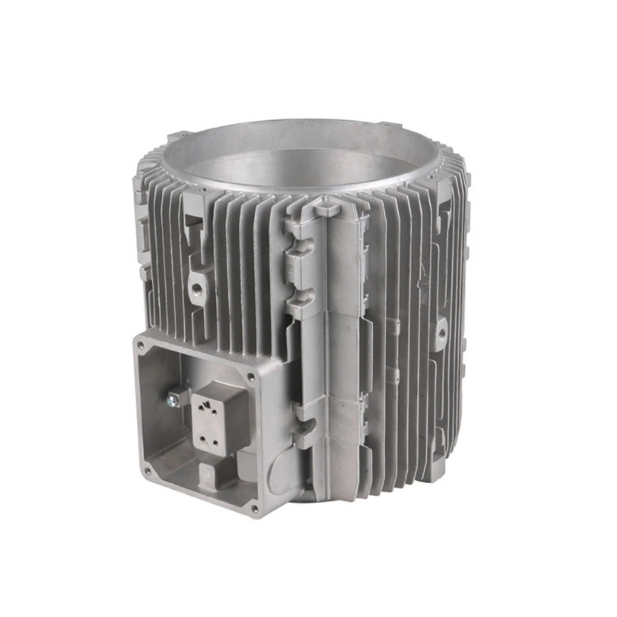
Benefits of Chrome Plating on Aluminum
1. Enhanced Corrosion Resistance
One of the primary reasons to choose chrome plating for aluminum is to improve its corrosion resistance.
While aluminum naturally forms a protective oxide layer, chrome plating provides an additional barrier against environmental factors like moisture, chemicals, and salt, which can cause corrosion over time.
This makes chrome-plated aluminum ideal for outdoor or high-moisture environments.
2. Improved Wear Resistance
Chrome-plated surfaces are known for their exceptional hardness, which enhances wear resistance.
The chromium layer helps protect the underlying aluminum from mechanical wear, scratches, and abrasion, increasing the lifespan of the part in high-use applications.
3. Aesthetic Appeal
Chrome plating gives aluminum a bright, mirror-like finish that is highly valued in industries like automotive and consumer goods.
The reflective surface not only improves the appearance but also increases the perceived value of the product.
4. Ease of Maintenance
Chrome-plated surfaces are easy to clean and maintain due to their smooth, non-porous finish.
Dirt, grime, and other contaminants can be easily wiped away, keeping the aluminum part looking polished for longer periods.
Benefit | How It Works | Impact on Performance/Appearance |
---|---|---|
Corrosion Resistance | Chrome adds an extra protective layer against corrosion. | Ideal for outdoor or high-moisture applications. |
Wear Resistance | The hard chrome surface reduces scratches and wear. | Extends the lifespan of high-use parts. |
Aesthetic Appeal | Chrome provides a shiny, mirror-like finish. | Enhances the look and value of the product. |
Ease of Maintenance | The non-porous finish is easy to clean and maintain. | Keeps parts looking polished for longer. |
Common Applications of Chrome-Plated Aluminum
1. Automotive Industry
Chrome plating is widely used in the automotive industry, where both appearance and performance are important.
Aluminum parts such as wheels, trim, and engine components are often chrome-plated to enhance durability and add a premium look to the vehicle.
2. Aerospace
In the aerospace industry, lightweight and durable materials are essential.
Chrome-plated aluminum components are used in high-stress areas that require both corrosion resistance and wear resistance, such as landing gear and engine parts.
3. Manufacturing Equipment
In manufacturing environments, equipment and machinery are often subject to harsh conditions, including exposure to chemicals, high wear, and extreme temperatures.
Chrome plating aluminum components helps to protect these parts from wear and corrosion, extending their service life.
4. Consumer Goods
Chrome-plated aluminum is also popular in consumer products such as bicycles, kitchen appliances, and electronics.
The combination of durability, ease of cleaning, and aesthetic appeal makes chrome-plated parts ideal for high-end consumer goods.
Industry | Key Applications | Benefits of Chrome Plating |
---|---|---|
Automotive | Wheels, trim, engine components. | Improved durability and premium appearance. |
Aerospace | Landing gear, engine parts. | Corrosion resistance and wear resistance. |
Manufacturing | Machinery, equipment components. | Enhanced protection from wear and harsh conditions. |
Consumer Goods | Bicycles, kitchen appliances, electronics. | Durability, easy cleaning, and aesthetic enhancement. |
Challenges of Chrome Plating on Aluminum
While chrome plating offers many benefits, there are some challenges to consider:
- Cost: Chrome plating can be more expensive than other surface treatments due to the additional processes involved, including the application of an intermediate coating.
- Environmental Impact: Chrome plating involves the use of chemicals that require careful handling and disposal to avoid environmental damage. Some regulations govern the use of certain plating processes due to their environmental impact.
- Adhesion Issues: Without proper preparation and the use of an intermediate coating, chrome plating can have adhesion issues on aluminum, leading to peeling or flaking over time.
Conclusion
Chrome plating for aluminum offers numerous advantages, from enhanced durability and corrosion resistance to improved aesthetics and ease of maintenance.
It is a popular choice in industries ranging from automotive to aerospace and consumer goods.
However, understanding the plating process and addressing challenges like adhesion and cost ensures the long-term success of chrome-plated aluminum components.
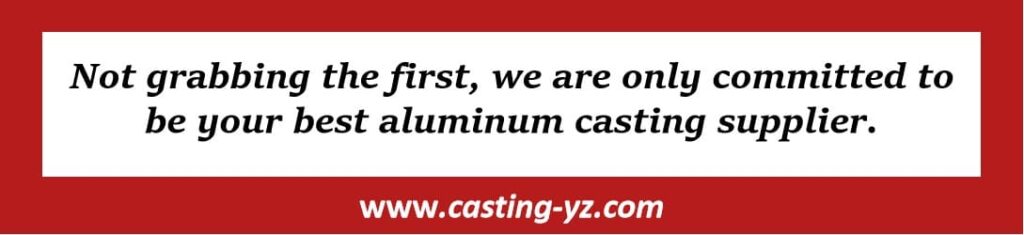