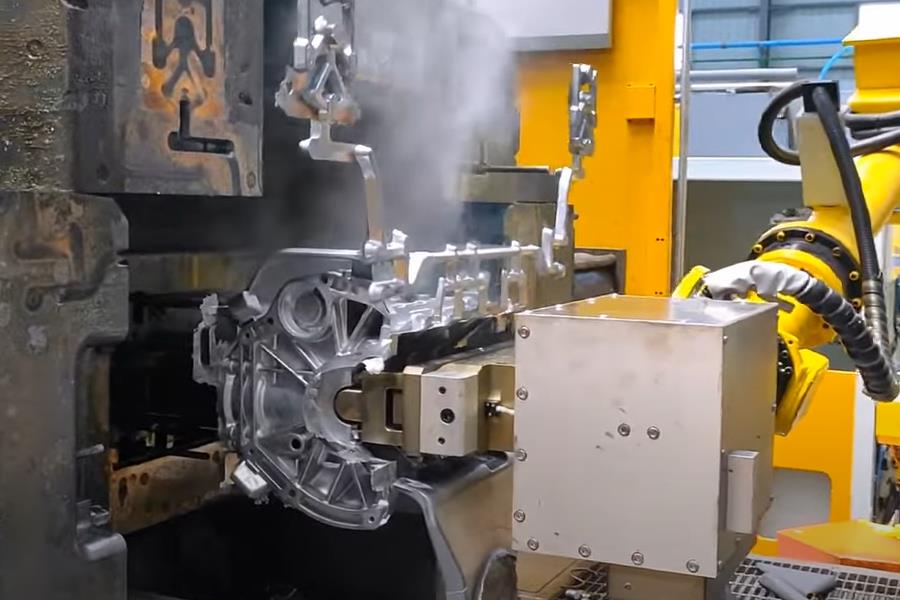
Aluminum die casting is a popular manufacturing process due to its efficiency and the excellent properties of the resulting parts.
But aluminum parts can be prone to corrosion, especially in harsh environments.
Enhancing corrosion resistance in aluminum die casting parts is crucial for extending their lifespan and maintaining their performance.
Understanding Corrosion in Aluminum
Causes of Corrosion
Corrosion in aluminum is primarily caused by environmental factors that lead to the formation of aluminum oxide.
Key factors include:
- Exposure to Moisture: Water, especially when containing salts, can accelerate the corrosion process.
- Acidic or Alkaline Environments: Extreme pH levels can enhance the rate of aluminum degradation.
- Electrolytic Reactions: Contact with different metals can lead to galvanic corrosion.



Types of Corrosion
Aluminum can experience various types of corrosion:
Pitting Corrosion | Galvanic Corrosion | Crevice Corrosion |
Localized corrosion that leads to small pits on the surface. | Occurs when aluminum is in contact with a more noble metal. | Develops in confined spaces where stagnant solution can exist. |
Techniques to Improve Corrosion Resistance
Surface Treatments
Surface treatments are effective methods to protect aluminum die casting parts from corrosion:
- Anodizing: This electrochemical process increases the thickness of the natural oxide layer, enhancing corrosion resistance.
- Powder Coating: Provides a protective barrier that prevents moisture and chemicals from reaching the aluminum surface.
- Electrophoretic Deposition (EPD): A method of applying a coating through electrical means, providing uniform coverage and protection.
Material Selection
Selecting the right aluminum alloy can significantly impact corrosion resistance:
- High-Purity Aluminum: Contains fewer impurities that can act as sites for corrosion initiation.
- Aluminum Alloys with Protective Elements: Elements such as magnesium, silicon, and zinc can improve corrosion resistance.
Design Considerations
Design plays a crucial role in preventing corrosion:
Avoiding Crevices | Ensuring Proper Drainage | Using Compatible Materials |
Designing parts with fewer crevices reduces areas where moisture can accumulate. | Allowing water to drain away from the surface prevents prolonged exposure to moisture. | Avoiding direct contact with metals that can cause galvanic corrosion. |
Maintenance Practices
Regular maintenance is essential for extending the lifespan of aluminum die casting parts:
- Cleaning: Regularly cleaning parts to remove contaminants that can accelerate corrosion.
- Inspection: Periodic inspections to identify and address early signs of corrosion.
- Protective Coatings: Reapplying protective coatings as necessary to maintain protection.
Conclusion
By understanding the causes and types of corrosion, employing effective surface treatments, selecting appropriate materials, considering design factors, and implementing regular maintenance practices.
Yongzhu can significantly enhance the lifespan of aluminum parts in various applications.