Zinc die casting is a widely-used method for creating strong, durable parts that are lightweight, cost-effective, and highly precise.
At Yongzhu Casting, we specialize in producing zinc die-cast parts for industries such as automotive, electronics, appliances, and hardware.
In this article, I’ll walk you through the ins and outs of zinc die casting, explaining why it’s the go-to method for many manufacturers and how it can help your business thrive.
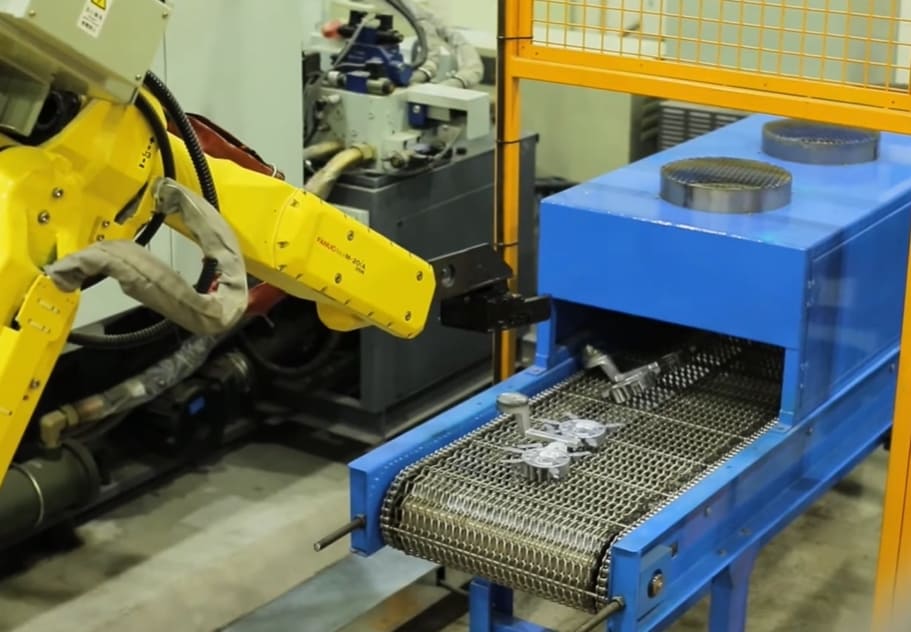
What is Zinc Die Casting?
Zinc die casting involves injecting molten zinc alloy into a steel mold under high pressure. The process creates complex shapes with tight tolerances and excellent surface finishes.
It is particularly known for its efficiency in producing parts at high volumes with minimal variation between each piece.
This makes zinc die casting an ideal choice for products requiring consistency, such as automotive components, electronic housings, and consumer hardware.
Key Benefits of Zinc Die Casting:
- Cost-Effective: Zinc has a low melting point, which reduces energy consumption and tooling wear.
- Precision: The process allows for tight tolerances, often within ±0.001 inches, making it ideal for intricate designs.
- Durability: Zinc die-cast parts have high strength and excellent wear resistance, suitable for high-stress applications.
- Superior Surface Finishes: Zinc parts often require little to no post-production machining or polishing, reducing finishing costs.
Benefit | Description | Best Application Examples |
---|---|---|
Cost-Effective | Reduces energy consumption and tooling wear. | Automotive parts, appliance hardware. |
High Precision | Offers tight tolerances, often ±0.001 inches. | Intricate components like electronic enclosures. |
Durability | Excellent wear resistance and strength for heavy-duty use. | Automotive gears, locks, and levers. |
Superior Surface Finishes | Minimal need for post-production finishing or machining. | Consumer electronics, appliance parts. |
The Zinc Die Casting Process at Yongzhu Casting
At Yongzhu Casting, we follow a well-defined zinc die casting process to ensure the best results. Here’s a breakdown:
- Melting and Injection: Zinc is melted in a furnace and injected into the mold at high pressure, filling every cavity with precision. This high-pressure technique ensures that the material fills all intricate parts of the mold.
- Cooling and Solidification: After the molten zinc is injected, it cools rapidly, solidifying into the desired shape. The rapid cooling process also contributes to the material’s strength.
- Ejection: Once solidified, the part is ejected from the mold, leaving behind a precise component that often requires little to no finishing.
- Finishing and Inspection: Any minor imperfections are addressed through finishing processes like deburring, and the part undergoes thorough inspection for quality assurance.
Step | Description | Importance |
---|---|---|
Melting and Injection | Molten zinc is injected into the mold at high pressure. | Ensures the precision of complex, high-tolerance parts. |
Cooling and Solidification | The molten metal cools quickly, solidifying into the shape. | Fast cooling helps retain strength and durability. |
Ejection | The solidified part is ejected from the mold. | Allows for consistent high-volume production. |
Finishing and Inspection | Parts are inspected and minor imperfections removed. | Guarantees the quality and finish of the final product. |
10 Professional and Common FAQs
- What is zinc die casting, and how does it work?
Zinc die casting is a high-pressure casting process where molten zinc is injected into a steel mold, known as a die. The process allows for the creation of complex shapes with tight tolerances, usually within ±0.001 inches. At Yongzhu Casting, we specialize in producing high-precision zinc parts for automotive, electronics, and appliance industries. - What are the advantages of zinc die casting over other casting methods?
Zinc die casting offers several advantages, including low tooling costs, faster production cycles, and superior surface finishes. Zinc’s low melting point means the process consumes less energy, and the material itself has excellent strength and wear resistance. This makes zinc die casting ideal for high-volume production runs where cost-effectiveness and precision are critical. - How durable are zinc die-cast parts?
Zinc die-cast parts are extremely durable, with high tensile strength and excellent wear resistance. They perform exceptionally well in high-stress environments such as automotive components, where they need to withstand continuous mechanical use. Zinc’s durability also makes it suitable for locks, gears, and appliance components that require long-term reliability. - What industries commonly use zinc die casting?
Zinc die casting is used across many industries, with common applications in automotive, consumer electronics, appliances, and hardware. For instance, automotive manufacturers use zinc die casting for parts like door handles, brackets, and lock mechanisms due to its high strength-to-weight ratio and precision. - What is the typical lead time for zinc die casting at Yongzhu Casting?
Lead times can vary depending on the complexity and volume of the project. Generally, we can deliver zinc die-cast parts within 4 to 6 weeks after mold creation, though high-volume production runs can be completed faster due to the efficiency of the process. We pride ourselves on meeting client deadlines without compromising on quality. - How does zinc die casting compare to aluminum die casting?
Zinc has a lower melting point than aluminum, making the die casting process more energy-efficient. Zinc also offers better dimensional stability and tighter tolerances compared to aluminum, which is ideal for small, intricate parts. However, aluminum is better for high-temperature applications and lighter components, such as those used in aerospace. - What are the typical tolerances achieved in zinc die casting?
Zinc die casting allows for exceptionally tight tolerances, often as tight as ±0.001 inches. This level of precision is one of the reasons zinc die casting is favored for producing complex, high-precision parts, such as gears and electronics housings, which require minimal post-casting machining. - Is zinc die casting environmentally friendly?
Yes, zinc die casting is considered environmentally friendly due to zinc’s high recyclability. Up to 95% of zinc die-cast parts can be made from recycled materials. At Yongzhu Casting, we are committed to sustainable manufacturing practices, ensuring that our production process minimizes waste and energy consumption. - Can zinc die casting be used for both small and large parts?
Zinc die casting is highly versatile and can be used to create both small, intricate parts like gears and locks, as well as larger components such as automotive brackets. The process is scalable, making it an ideal choice for a wide range of part sizes and production volumes. - How does zinc die casting help reduce production costs?
Zinc’s low melting point reduces energy consumption, and its excellent fluidity allows for faster cycle times, enabling high-volume production with fewer defects. Zinc’s ability to create precise parts with minimal post-production machining also cuts down on finishing costs, making it a cost-effective solution for mass production.